Big Push in Germany to Enable 3D Printing in Automotive Industry
3D printing and additive manufacturing have become a matter of national importance in Germany, and to the automotive industry overall. Several organizations—along with the ongoing support of the Fraunhofer Institute for Laser Technology ILT and the Chair for Digital Additive Production DAP of RWTH Aachen University—are eager to see the Industrialization and Digitization of Additive Manufacturing for Automotive Series Processes (IDAM) lead the way for furthering the use of AM processes in the auto industry. Project partners for IDAM include a variety of small to medium enterprises (SMEs) and research institutions, all dedicated to the progress of metallic 3D printing for the manufacturing of vehicles.
BMW Group is behind much of this push, and their dedication to additive manufacturing for almost 30 years has not gone unnoticed. From an investment in a new AM facility in Munich to specialized projects like restoring Elvis’ long-lost BMW 507 from 1958, their work in 3D printing has been so prolific that by last year they had fabricated over one million parts, harnessing the untold power of this progressive technology. Currently, 3D printing and AM processes with metal are in force at BMW’s facility in Munich, along with GKN Powder Metallurgy’s factory in Bonn.
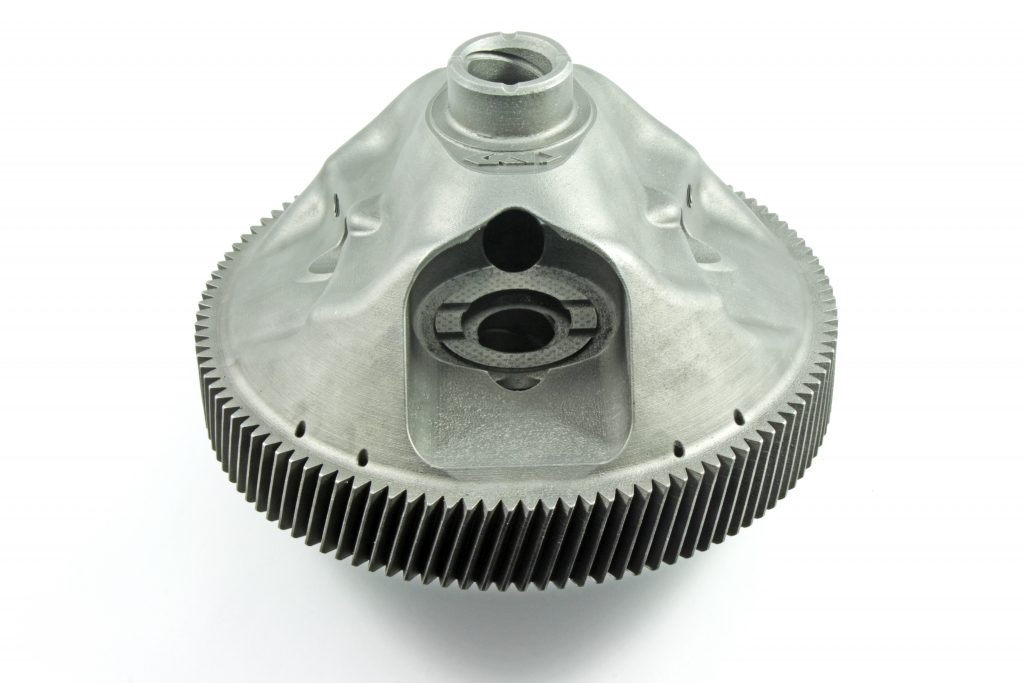
This structural optimized differential housing, jointly developed by GKN Powder Metallurgy and Porsche Engineering, is one of the growing new e-drive powertrain applications for Metal AM (Photo: GKN Powder Metallurgy)
There are 12 partners total working within the ongoing project via IDAM, and as Fraunhofer Institute for Laser Technology ILT points out in their latest press release, the use of metallic 3D printing should ‘sustainably strengthen Germany’s technological pioneering role and the country itself as a manufacturing location.’ Everyone involved is obviously envisioning making use of all of 3D printing’s most famed benefits, beginning with greater affordability. Along with that comes exponential reduction of turnaround time in manufacturing, and the ability to offer a wide range of customization options for clientele.
The IDAM team is present at both facilities, qualifying the technology for production of metal parts, with projections for manufacturing at least 50,000 3D printed parts annually. They also expect over 10,000 individual and spare parts to be created. This is a far cry from the initial use of 3D printing for low-batch production of customized parts. Even with plans for mass production, the partners expect high-performance parts to be created ‘under extreme cost pressure.’
Project partners include:
- Aconity GmbH, Herzogenrath
- Concept Reply GmbH, Munich
- Fraunhofer Institute for Laser Technology ILT, Aachen
- GKN Powder Metallurgy, Radevormwald
- Myrenne GmbH, Roetgen
- Intec GmbH – Ingenieurbüro für Automatisierungstechnik, Bad Neuenahr-Ahrweiler
- Kinexon Industries GmbH, Munich
- Chair for Digital Additive Production DAP, RWTH Aachen, Aachen
- Technical University of Munich, Chair of Metal Forming and Casting, Munich
- Schmitz Spezialmaschinenbau GmbH, Rheinbreitbach
- Volkmann GmbH, Soest
This activity truly marks the beginning of metal AM taking a prioritized role within Germany’s industrial dynamic, with two modular production lines being installed (one in Munich; one in Bonn). Customization is key here too, as modules can be changed to fit production needs.
“In addition, their process steps can be controlled and utilized flexibly,” states Fraunhofer Institute for Laser Technology ILT in their press release. “By taking an integrated view of the automotive production line into account, the project partners plan on reducing the manual share of activities along the process chain from currently around 35 percent to less than 5 percent. In addition, the unit costs of 3D printed metal components should be more than halved.”
The IDAM partners are currently using their experience and expertise in designing modules for the mass production line, to include automated processes for powder handling, monitoring, post-processing, and more.
“Since large industrial companies are involved, these linked modules can be used in the AM production lines under real conditions and on a large scale,” explains the Fraunhofer Institute for Laser Technology ILT release. “In addition, industrial standards can be set, and industry-relevant quality characteristics elaborated. Only through this interdisciplinary cooperation does the IDAM project make it possible to holistically examine metallic 3D printing for automotive series processes and to establish it sustainably in production.”
What do you think of this news? Let us know your thoughts! Join the discussion of this and other 3D printing topics at 3DPrintBoard.com.
Metal 3D Printing Material Scalmalloy Could be the Aircraft Material of the Future
Aviation is one of the many industries around the world that’s increasing its adoption of 3D printing, which can be used to create the lightweight components and complex parts that are necessary for an airplane. The technology makes these parts with repeatable characteristics and consistently high quality, and can also decrease the amount of time, money, and materials needed to produce them, making the overall supply chain more efficient.
Speaking of these materials, we most often hear about components being made with strong thermoplastics and metals, such as titanium. But there’s another metal out there – a lightweight, corrosion-resistant aluminium alloy nearly as strong as titanium – that could be the hero we all need for the future of aircraft. I am of course referring to Scalmalloy, an aluminum-magnesium-scandium alloy developed and patented specifically for metal 3D printing by APWorks.
Scalmalloy is a highly ductile material that works on all existing powder bed SLM 3D printers. With a stable microstructure at temperatures of up to 250ºC, it’s highly weldable and can easily be machined for use in industries like aviation and automotive. Additionally, the material was developed specifically to use the lowest buy-to-fly ratio when compared to parts designed and manufactured using conventional methods.
Recently, a collaborative group of researchers from the Nanjing University of Aeronautics and Astronautics (NUAA) and the Fraunhofer Institute for Laser Technology (ILT) published a paper about another scandium-reinforced aluminum alloy, titled “Selective laser melting of rare earth element Sc modified aluminum alloy: Thermodynamics of precipitation behavior and its influence on mechanical properties,” in the Additive Manufacturing journal.
The abstract reads, “The interest of selective laser melting (SLM) Al-based alloys for lightweight applications, especially the rare earth element Sc modified Al-Mg alloy, is increasing. In this work, high-performance Al-Mg-Sc-Zr alloy was successfully fabricated by SLM. The phase identification, densification behavior, precipitate distribution and mechnical properties of the as-fabricated parts at a wide range of processing parameters were carefully characterized. Meanwhile, the evolution of nanoprecipitation behavior under various scan speeds is revealed and TEM analysis of precipitates shows that a small amount of spherical nanoprecipitates Al3(Sc,Zr) were embedded at the bottom of the molten pool using a low scan speed. While no precipitates were found in the matrix using a relatively high scan speed due to the combined effects of the variation of Marangoni convection vector, ultrashort lifetime of liquid and the rapid cooling rate. An increased hardness and a reduced wear rate of 94 HV0.2 and 1.74 × 10-4 mm3N-1 m-1 were resultantly obtained respectively as a much lower scan speed was applied. A relationship between the processing parameters, the surface tension, the convection flow, the precipitation distribution and the resultant mechanical properties has been well established, demonstrating that the high-performance of SLM-processed Al-Mg-Sc-Zr alloy could be tailored by controlling the distribution of nanoprecipitates.”
The researchers fabricated Sc- and Zr-modified AI-Mg alloy using SLM 3D printing, and were then able to provide clarification on the relationships between the convection flow, precipitate distribution, mechanical properties, and scan speed. SEM and TEM characterize the various precipitation behavior between different scan speeds, and a relatively low scan speed helped to evaluate and explain how significantly the material’s hardness had improved.
Authors of the paper are Han Zhang, Dongdong Gu, Jiankai Yang, and Donghua Dai from NUAA, and Tong Zhao, Chen Hong, Andres Gasser, and Reinhart Poprawe from Fraunhofer ILT.
Discuss this materials research and other 3D printing topics at 3DPrintBoard.com or share your thoughts in the Facebook comments below.
[Images: APWorks unless otherwise noted]