A few years ago I started to think of 3D printing as a triangle where you had to control for each part of the delta: software, machines, and materials. I’ve now come to realize that it is more complex still. In order to get true repeatability, reliability and throughput in high-quality parts we have to from concept to customer consider the most significant influences on 3D printing. We have to each of us, whether we be users, OEMs, manufacturers have to look at 3D printing holistically, and take into account how our inputs affect all others. Only by controlling for all sides of the 3D Printing Octagon can we ultimately succeed in 3D printing parts reliably and repeatably at scale.
People have been trying to reduce the influence of variables on 3D printed parts since the technology began. But, initially, it was one OEM who made the machine, sold the materials and made the software (or at least influenced these things). Companies like Stratasys and 3D Systems could coordinate all of the settings and variables to come up with coherent 3D prints. Their level of control meant that parts came out the right way every time. The current 3D printing landscape consists of this Closed way of doing things but also an Open Ecosystem. And let’s be frank guys, the Open Ecosystem is currently a mess. Everyone is just winging it. People are building systems willy-nilly without much a thought to the importance of software. A lot of OEMs have very little understanding of firmware and the effects of that on prints. Materials companies just throw stuff over the hedge with settings such as between 200 and 230 C? You’re joking right, would that work if I were baking a cake? Part of that problem is due to run to run differences on machines. Often machines can be found to have temperature differences at the nozzle of 10 to 15 degrees. So the temperature that you’re printing at is probably not the temperature you’re actually printing at. A knock on effect of this is that a lot of 3D printing research is junk because it doesn’t correct for these temperature differences. There is variability also in the torque of the mostly totally crappy stepper motors we use as well. Open printers have huge influences from airflow, ambient temperature, and humidity. Often there are considerable temperature fluctuations in a build chamber during a build. We all just random walkaly try to solve the bed adhesion issues as if it were second grade and we’re playing with glue-sticks. There are inconsistencies in procedures as well. Settings on the printer are dealt with if they’re some kind of dadaist art form with everyone semi-randomly changing retraction, speeds and extrusion power. Gcode and the way the nozzle actually builds up a part has effects which are not addressed. Design for 3D printing is something that is being made up as we go along but is hampered because we make up new terms for everything. We can’t even agree to all use Material Extrusion, FDM, FFF or whatever to describe the different technologies. We don’t have a universal accuracy measurement or a way to test 3D printer performance. Most dogbones are printed in vain due to inconsistencies in testing methodology. Kids, it’s time to put down the screwdrivers for a moment and work together.

1. Standardization & Testing. We need to adopt the same terminology, procedures, tests, and standards if we are to advance. I know this is boring, but it is also essential. If we don’t do this, then there is no way through which we can collectively advance the industry. Furthermore, a lot of inefficiencies will be created while everyone tries to build their platform. We can opt for, or a “chaotic everyone do their own thing industry” if we want, but we would get to better parts quicker by working together. You see, you may think you’re competing against one another, but this is not true. What we’re competing with is injection molding, clay, welding or any other manufacturing technology. We have to make 3D printing more viable for more things. That way we all profit. The more things we can make reliably; the more valuable and desirable our machines, materials, and software will be. I’ve said this before but you are not Boeing, and the other guy is not Airbus. There are 7 billion people on this planet that do not use 3D printing, the ones that do for business or at home are essentially a rounding error. We can perhaps now make only around 2% of all the things in the world. It is by activating more people on 3D printing and by making more prints possible that we all advance. Meanwhile a lot of you hawkeyed look at the other guy like we’re some mature no-growth industry. Stop with this nonsense, but rather help us make us the answer to all the things that do not exist yet.

After we, hopefully, standardize our nomenclature and testing we should come to grips with the other sides of the 3D Printing octagon. If we want to produce parts reliably, we will need to realize that there are seven sides to this problem and that they all have to be understood and controlled for 3D printing to work well. If we industrialize, we will have to control for and master the entire octagon. Lack of understanding of one or more elements of the octagon means that we will screw up at one point. This is all well and dandy for your Yoda head but not for my 3D printed heart. This is the future guys, and the future sucks because it will have a lot of statistics in it, graphs and clipboards.
2. Machine & Slicer Settings The machine settings influence how quickly a part is printed at what speed the head moves and at what temperature the nozzle extrudes. Settings have direct effects on wall slip, pressure and the voxel as it is being built. Individual settings such as retraction work in concert with and have significant feedback loops with other parameters such as speed, feeder setting, feeder speed, etc. These settings also cannot be universally applied and do not have consistent effects. E.g., differences in filament roundness can interfere with consistent extrusion and mask optimal extrusion speeds or differences in filament surface finish can cause different optimal feeder settings. Settings are often user tweaked in isolation, and the user often feels as if they are “learning how to 3D print” whereas in actuality they are continually compensating for other misunderstood differences in environment, material or design. Incorrect and inconsistent use of settings leads to many print failures and is the chief reason why 3D printing is advancing slower than it should on the desktop. It’s as if we’re all trying to bake cakes, but no one ever writes down a recipe or even defines what boiling or icing means. In this case, I’ve lumped together slicer and machine settings because they work in concert and are both open to user input often to that user’s detriment.
3. Machine & Environment By machine we mean here the actual positioning, movement, and print process that the machine parts are doing at any one time. In this sense lack of calibration, calibration procedure or run to run differences inhibit precision. Through machine, we also mean the internal surfaces in the machine, especially where melt occurs. The pressure in the nozzle, as well as the surfaces of these critical pathways, are little understood. We will need to grasp these effects much more precisely. Understanding settings are also in and of themselves useless if the machine inconsistently acts upon these settings.
We must control the machine in order for it to build parts. We must also manage the environment. At one point, hopefully, all printers will be closed, and we’ll breathe in fewer fumes and get better print results. We have to control airflows, laminar flow, heat, ambient temperature and humidity if we are to print consistently. Right now people are spoiling their datasets by printing near windows or with heat changes in their buildings. We need to bring down the excessive number of variables and their effects significantly.
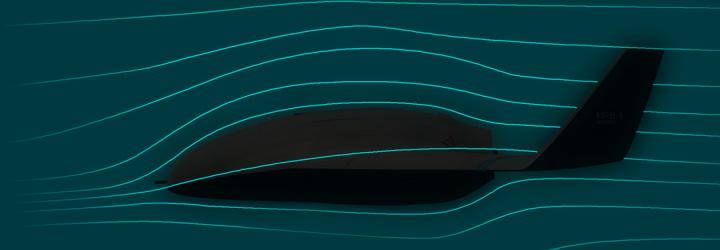
4. Material Material roundness and diameter has significant effects on nozzle pressures and misprints. The temperature that materials have to be extruded at to get optimal layer adhesion is often also not precisely understood or communicated. There are also many material dependent settings and differences. Some materials require fans to be at 100% some print better when they are off. The interplay between materials and settings with the complex feedback loops occurring there are not understood by industry. Often much instruction and expounding on optimal settings are not much better than guesswork. The correct applications of the right material for the correct part is also not communicated. Polymer companies toss resin pellets at extrusion companies that gleefully catch this manna from heaven before extruding it, rolling it up and frisbeeing that at an OEM. OEM’s copy paste some info and pass it on to users. No one speaks the same language, and no one understands each other. Additives, grades, and polymers themselves can have massive effects. Many users are not even aware that colorants mean that different PLA’s from the same vendor print best at different nozzle temperatures.
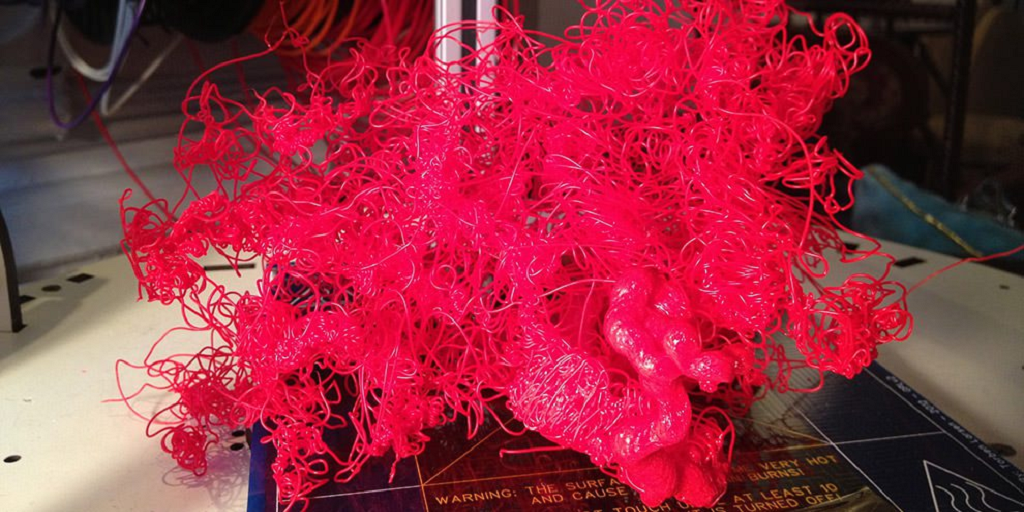
Through this five hundred million dollar whispering word game, the user is left with some marketing slogans and imprecise guidance on when to use a material and how to print it. OEMs and retailers want better printability, and by putting them in the driving seat, we’ve set the “spreadability” of butter as the main priority rather than its taste. Printability is when a machine manufacturer asks you to cover up their machine’s failings through polymer chemistry or additives. Printability is a lie. A 3D printer manufacturer telling us what materials to print and how is like an arsonist advising the fire department. I do not in the slightest doubt that there is real affinity and interest, but in the final analysis, our shared goal does diverge. You want a thing that makes your machine look good, and I want a thing that gives me the best parts and best properties.
5. Operator & Process Touched on above, the operator is mostly a creature of random habit. Part artist part scientist excelling at neither we blunder through misprint after misprint. Look I also thoroughly enjoyed the exploration and astronaut feeling of 3D printing initially. But, could we now make it humdrum and predictable? And Astronauts become astronauts through learning and stay alive through a process. We need the best processes, and we need these mapped and explained well.
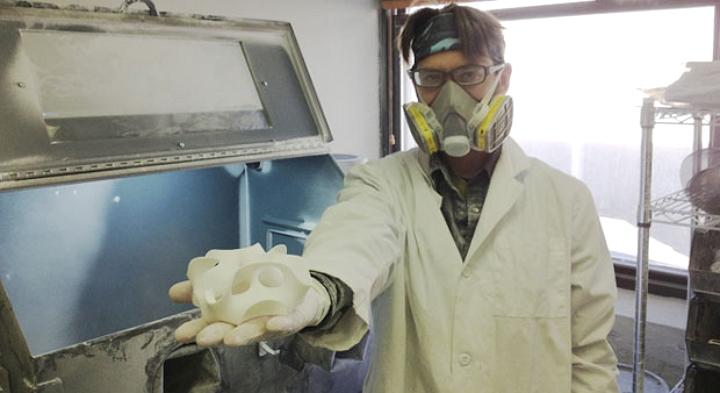
One of the most prominent failure modes in desktop 3D printing is layer adhesion issues with your first layer. Often the cause of this is greasy fingers on the build platform. Clean the platform, and many first layer issues disappear. 3D printing would be much better if we all knew the best way to do certain things. Many misprints are also due to incorrect storage of PLA and moisture on it. There have to be processes for these kinds of seemingly ancillary but crucial things as well. The rote concentration and effort of processes correctly implemented by a knowledgeable operator working systematically will be tedious but will reduce failure rates for all of us.
6. FIle The STL needs to die in a fire, this much is certain. We need to have one good file type that can describe densities, colors, patterns and every bit of information in the voxel at every location. We also have to find ways of going from CAD directly to movement on the machine while also finding better ways to describe circles, triangles, and parts. A lot of CAD software changes the way your file works and a lot of information that we want in the file such as where it is from and how it can become parametric and what materials work how is absent. I’ve previously been a proponent of sDNA which essentially is an idea whereby an XML file format contains not only a description of the thing but the thing in all of its permutations in all of the available materials with the relevant settings and attribution and use information. We will need this eventually, and the sooner we get it, the better.
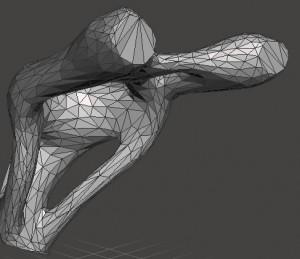
7. Toolpath, Melt Pool & Infill Toolpaths are not intelligent and can be optimized. Much more efficient ways to draw objects can be found. More research needs to be done as to how the nozzle moves and how this coupled with extrusion speed, wall slip effects, and nozzle diameter makes your print. If the laser would build a part with a different spot size or melt pool, then the consequences are enormous on the part. We need to be able to control where crystallization occurs (when and if it is intended to happen) and we need more control over the actual placement/melting in place of material. Once we can do that, then we can genuinely consider each print a unique material made for one application and can control for and optimize the qualities of that part at every voxel. Then we can also dynamically optimize infill patterns, shapes and make them dynamic as well. We could then design the sand, shape the mortar and use both to build a house by letting us determine the right properties at each voxel, also at each 3D infill space and also of the part as a whole through the modification of these three in concert.
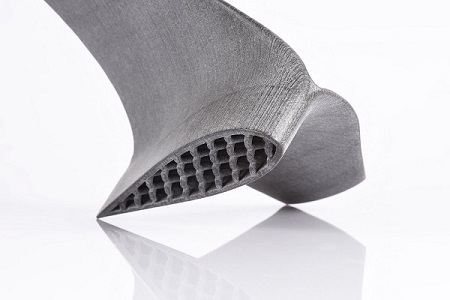
8. Design Stuck in our Voronoi ways we’ll hopefully look back at this as a quaint time of salt of the earth people. Like how we now look at times when only truckers wore trucker hats and New York didn’t look like a German U-Boot crashed off of Greenpoint. Form follows function is such a universally held truism in design that few actually practice it. But, by starting from the utility of a thing, how long it needs to exist and what it needs to do we can then go to a functional shape. Using FEA and other techniques more designers and engineers will start to make objects that are made for a purpose. We will need to get our heads around optimal weight saving techniques, how to integrate multiple functionalities in one object, how to reduce part count, how to iterate and test designs. We will have to look again at textures, topology optimization and how this works in conjunction with the possible and desirable. Design and engineering from 3D printing will be many iterations, many failures agile engineering affair. If this is done in conjunction with those above to control for the 3D Printer Octagon then we will have a 3D printed world. Have at it.