Purdue students design award-winning 3D printed heat sink
Report from European Patent Office shows 3D printing patent numbers increasing
COVID-19 Doesn’t Shake Reinforced Optimism of 3D Printing Businesses
Recent announcements regarding earnings and financial performance through the first quarter of 2020, have given some insight into the impact COVID-19 has had on major 3D Printing businesses worldwide.
While ensuring employee safety and business continuity remained paramount, public companies were simultaneously challenged by a sudden decline in consumer demand, a continuing halt or reduction in onsite activities, and global supply chain issues, which began in China shortly before impacting Europe and the Americas.
Revenues for Stratasys and 3D Systems declined by 14% and 11% respectively, whereas strong order backlogs from 2019 led to significantly higher revenues realized for SLM and ExOne. SLM had the best first quarter performance in the company’s history with a 143% increase compared to 2019.
3D Systems saw revenues decline across segments, except materials, which stayed flat. The company faced a drop in consumer demand in automotive, aerospace, healthcare and dental, as well as disruptions in production facilities and on-site services. Despite sustained cost reduction measures and improving operating expenses by 13%, its shares depreciated 5% with 0.04 loss per share for 2020, compared to 0.09 loss per share for 2019.
In addition to the decline in Q1, Stratasys expects a sequential decline in Q2 of 5-10%. Yet the company believes its balance sheet with $325M in cash, coupled with its ability to generate cash and control costs, will help it manage the short-term hit in revenues, and strongly expects margins to recover.
Across businesses, revenue decline has primarily been attributed to short-term impact of reduced manufacturing activity and industrial production due to COVID-19, resulting in a fall in consumer demand across segments. In addition, a pause and postponement of investment has seen lower capex spend across key industries such as automotive, aerospace, healthcare and oil & gas. Demand for new hardware and software licenses has declined, partly offset by recurring revenues from materials, consumables, or after-sales services. In some sectors, such as dental, material consumption has slowed as elective procedures are delayed or cancelled. In general, machine and software segment revenues have seen a decline, but recurring revenues from the installed base of 3D printers has seen revenues from the materials segment increase or stay flat. For instance, Prodways saw a decrease of 6.3% in machines and software, but a 25% increase in materials revenues.
This change in demand is seen as more of a ‘pushing-out’ of capex spend, than a cancellation. Order intakes stayed flat or reduced overall, as customers in key industries postponed capital expenditure and investment due to COVID-19 uncertainty and impact.
The impact in operations differed, as businesses with localized supply chains were less impacted—such as SLM who also kept safety stocks for high-risk and long-lead time items—as compared to 3D Systems or HP, who faced production and capacity disruptions in their global supply chains.
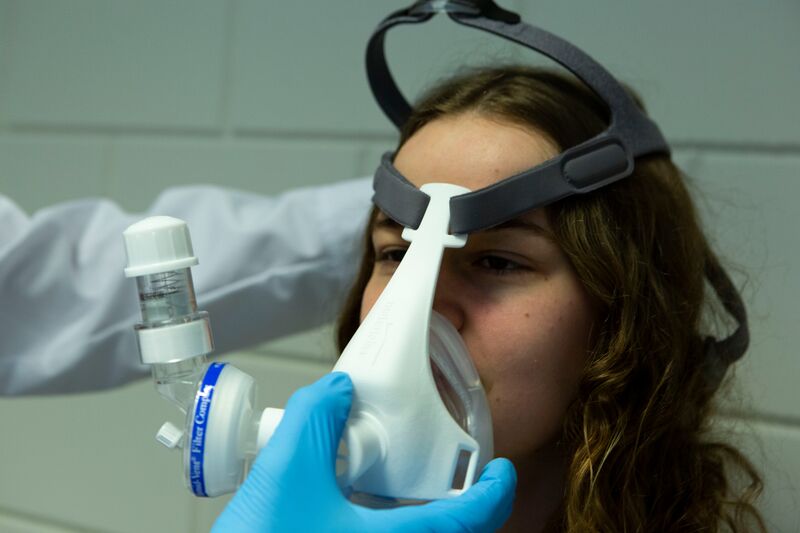
The NIP mask, developed by Materialise to help treat COVID-19 patients. Image courtesy of Materialise.
Materialise saw a slight revenue decrease of 1.8% with gross profits decreasing 3.7% compared to last year’s quarter. Though their software and medical segments grew, there was a steeper decline in their manufacturing segment revenues, which account for 45% of total revenue. The company delivered higher than expected revenues this quarter with a gross profit of $109M, and despite varied market performance recently, has seen its shares up 25.4% year to date.
ExOne, sold 14 of its metal and sand binder jetting machines in the quarter, with a 40% increase in revenues and a 19% improvement in net loss with $3.6M in Q1 2020, resulting in a $0.22 loss per share for 2020 compared to $0.28 in 2019.
Revenues at GE Group fell 8% to $20.5B, with is power and aviation division significantly impacted by its exposure to the decline in the commercial aerospace sector. However, GE’s Healthcare and Lifesciences segment saw demand surge 6% due to COVID-19. Yet the company has seen its shares lose more than 40% of their value this year and expects the second quarter results to decline sequentially, showing the first full quarter impact from COVID-19.
HP Inc has reported second quarter results with net revenues were down 11.2% to $12.5B compared to 2019, with personal systems declining 7% and printing 19%. In Printing, the company has set long term margin targets of 16-18%. In 3D Printing, HP has recently partnered with New Balance and Superfeet to grow its end-user solutions in scanning and printing, and is counting on key verticals such as healthcare for continued growth. The company is continuing its focus on structural cost optimization and productivity gains, hoping to generate over $2B in savings. It has also provided guidance of $2.33-2.43 per share for 2020 and $3.25-3.65 per share for 2022.
Voxeljet’s share price has reduced dramatically over the last five years, despite steadily growing revenues. It has until December, 29, 2020 to regain compliance with NYSE after its average closing share price had fallen below $1.00 standard and the $50M market capitalization standard. Yet the company has reported Q4 2019 revenues with an 11.4% increase over 2018, and a record order backlog. While it does expect disruptions in operations and supply chain due to COVID-19, it anticipates demand for its large-scale printers to continue, expecting annual revenue for 2020 to be between €25-30M.
Companies have also been proactive within their organization to manage the impact of the crisis to their employees, customer base and business operations. From introducing remote working, reduced work week or shifts, and other employee-facing policies, to implementing safety and health protocols, freezing non-essential hiring and travel, and short-term optimization measures to ensure business continuity and avoid large-scale layoffs. For instance, salaries for all Stratasys employees and executives was reduced by 20%. Executives and board members at 3D Systems took a 10% pay cut with a majority of employees on limited furloughs, and partial activity measures were introduced for almost 50% of Prodways employees worldwide. Businesses have also taken measures to optimize operational costs, revaluate their supply chain and production costs, and increase focus and spend in digital, particularly in sales and marketing, for the long-term.
Overall, while Q1 earnings do show some signs of business impact, businesses are pointing towards Q2 as to where the full impact will be seen, since the pandemic peaked largely in the latter half of the first quarter, through March and April. In this regard, businesses have trended toward withdrawing guidance for the rest of the year, as uncertainties due to COVID-19 continue, while stating that second quarter results are expected to show a more considerable impact. Although there is a near-term focus on cost reduction, optimization and ensuring liquidity, 3D printing businesses are positive in their long-term outlook. Key industries are expected to remain structurally unaffected, with markets returning to the new normal in the second half of this year, and AM’s increased relevance has reinforced optimism in the industry’s long-term growth. No major shifts in long-term strategy or investment have been made yet due to COVID-19, with investments in on-going R&D continuing.
With their real-time response and contribution during COVID-19, 3D Printing businesses have led the way and impacted the front-line pandemic response, providing rapid, direct support for personnel safety and in essential medical devices and equipment. The response also proved AM’s capability in high-volume and bridge production, its potential in localizing and distributing manufacturing, flexibly and at speed, whether to retool or expand existing production, or to develop new, improved products faster, especially in healthcare. If anything, the pandemic response has only underlined the critical and long-term value of AM in addressing real-world gaps and needs, in ways that traditional manufacturing and supply chains just cannot.
The post COVID-19 Doesn’t Shake Reinforced Optimism of 3D Printing Businesses appeared first on 3DPrint.com | The Voice of 3D Printing / Additive Manufacturing.
3D Printing and COVID-19, May 2, 2020 Update
Companies, organizations and individuals continue to attempt to lend support to the COVID-19 pandemic supply effort. We will be providing regular updates about these initiatives where necessary in an attempt to ensure that the 3D printing community is aware of what is being done, what can be done and what shouldn’t be done to provide coronavirus aid.
Swiss creative agency Atoll, in partnership with Pragma Engineering and 3D printing company Rapid Manufacturing, has designed a device that can be used to remove protective gloves in a way that is less likely to spread contamination. According to one study, almost 50 percent of people contaminate their skin with germs when removing protective clothing.
Atoll’s device is made up of a curved piece of plastic that can be mounted on walls or metal bars over a garbage can using a modular fastening system. Glove wearers are meant to slide the tip of the device between their palms and the cuffs of their gloves. As they pull upward, the gloves fall off and into the bin below. The 3D printable file is located at the Atoll website here.
Members of the AM business community are publishing their quarterly financial results, which include the impacts of the economic slowdown on their finances. Materialise announced its first quarter results, ending March 31, 2020. Renveues dropped 1.8 percent to €46.2 million, from €47.1 million in Q1 2019. Revenue growth continued in its Software (+5 percent, to €9.8 million) and Medical (+15.3 percent to €15.6 million) segments, which was offset by a decrease in its Materialise Manufacturing (-13.9 percent to €20.8 million) segment decreased compared to the same period last year. Executive Chairman Peter Leys commented:
“Fiscal 2020 began with unexpected challenges for businesses worldwide as a result of the COVID-19 virus. Materialise still performed relatively well during the first quarter as sales began to be negatively impacted only towards the end of the quarter. With the subsequent spread of the COVID-19 crisis and the increased disruption to the global economy and normal business operations, we expect the pandemic’s impact to be much more pronounced during at least the second quarter of 2020.”
Leys attributed the shrinkage of the company’s manufacturing division to the impact of the virus outbreak on its ACTech subsidiary, a full-service manufacturer of complex metal parts. Leys said that ACTech is over 80 percent exposed to the automotive industry, compared to its broader manufacturing division which Leys performed “very well, and even in spite of our traditional business also being hit by the COVID crisis towards the end of March actually did better than the first quarter of 2019.”
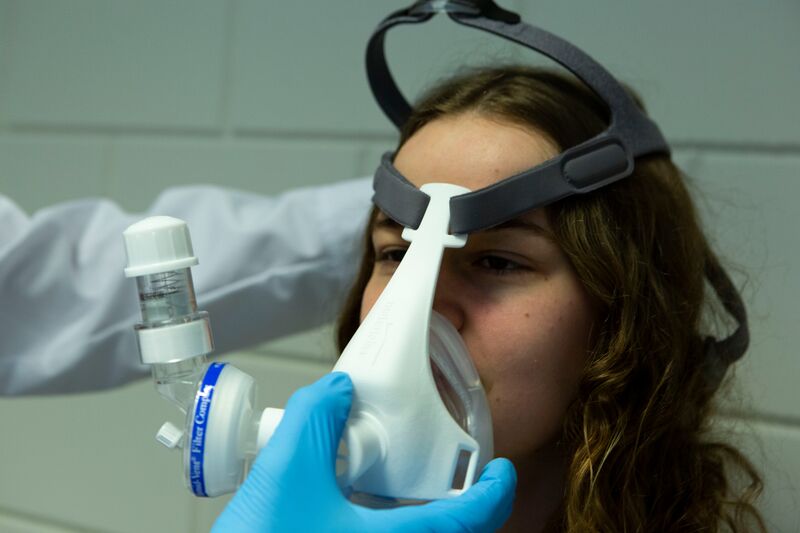
The NIP mask, developed by Materialise to help treat COVID-19 patients. Image courtesy of Materialise.
Materialise Fried Vancraen noted: “While we do not expect our industry to grow exponentially during this crisis, or shortly thereafter, we are picking up many signals that this crisis, however devastating it may be for those who are personally affected is putting industry 4.0 initiatives in general, and in particular, higher on the agendas.”
Prodways Group of France also reported its financial earnings for the first quarter of 2020, which included an 11 percent decrease in total revenue from Q1 2019 €15.5 million. Revenue generated from design and manufacturing dropped 19.6 percent to €5.6 million from Q1 2019. Software, 3D printers, and related materials and services were down 6.3 percent to €9.8 million.
GE Group revenues dropped 8 percent to $20.5 billion, with total orders decreasing by 5 percent to $19.5 billion. Revenues fell 13 percent in its power and aviation division, which the company naturally associated with the dramatic decline in commercial aerospace caused by the spread of the virus. In turn, CEO Larry Culp, said that the company will be cutting costs:
“We are targeting more than $2 billion in operational cost out and $3 billion of cash preservation to mitigate the financial impact, and we executed a series of actions to de-risk and de-lever our balance sheet amid a challenging environment.”
voxeljet AG received a notice of noncompliance from the New York Stock Exchange due to the fact its average closing price fell below $1.00 per share over 30 consecutive trading days. Due to the pandemic, voxeljet was given an extension to comply with NYSE requirements and has until December 29, 2020, and May 4, 2021, to regain compliance with the $1.00 minimum share price standard and the $50 million market capitalization standard, respectively.
HP Inc.’s net revenue was down 0.6 percent to $14.6 billion compared to last year, according to its earnings report published in February. Protolabs’ revenue actually increased 1.46 percent to $115,108,000. Stratasys has scheduled its Q1 earnings call for May 14. 3D Systems’ call will take place on May 6. SLM Solutions has scheduled its report for May 7.
Meanwhile, Volkswagen Passenger Cars has returned to production, building Golf, Tiguan, Touran and SEAT Tarraco vehicles at the company’s Wolfsburg plant, where VW’s 3D printing center is located. 8,000 employees will work one-shift at a time with reduced contact between one another. About 2,600 suppliers, most of which are in Germany, are also operating to make parts for Volkswagen’s main plant. Roughly 1,400 vehicles are expected to be completed by the end of the first week of resumed production before quantities are increased to over 6,000 in the coming weeks (or about 40 percent of pre-COVID production levels), as multiple shifts are reintroduced.
In order to return to work, the company is instituting a 100-point plan that includes rules related to distancing and hygiene, including home temperature-taking for workers and performing a daily health checklist. Where distances of 1.5 meters are not possible, workers must wear mouth and nose protection. Mobile plexiglass partitions and more handwashing sites have been setup throughout buildings, while conference rooms are converted into office spaces.
As illustrated, businesses globally are being impacted by economic shutdowns. In turn, there may be some potentially positive effects on our ecosystem in the near-term, with the International Energy Agency predicting an 8 percent decrease from last year in global carbon dioxide emissions, the largest recorded drop since the global financial crisis of 2008.
However, IEA Executive Director Dr. Fatih Birol warned that this reduction in CO2 should not be celebrated for a variety of reasons, not the least of which is the dramatic loss of life and increase in suffering that has resulted from the COVID-19 outbreak. Birol told The New York Times:
“This historic decline in emissions is happening for all the wrong reasons. People are dying and countries are suffering enormous economic trauma right now. The only way to sustainably reduce emissions is not through painful lockdowns, but by putting the right energy and climate policies in place.”
There have been nearly a quarter-of-a-million deaths from COVID-19, including nearly 64,000 in the U.S. alone. Over 26.5 million people in the U.S. applied for unemployment within a medical system of appalling inequality, with potentially 8.9 to 13.9 million locked out of unemployment aid altogether. The toll that the virus and economic hardship has had on individuals highlights the fact that economic degrowth cannot come at the expense of human suffering.
Additionally, such dips in emissions as occurred during the 2008 financial crisis are typically followed by emission booms, as economic activity restarts. Moreover, nations such as the U.S. are using the crisis to relax environmental regulations, which can result in greater emissions and other ecological hazards. Therefore, it’s important to be mindful of the human response to the crisis from a global, institutional and individual perspective.
While VW may be able to return to production, we have to wonder about the cost, for instance, on individual workers. Despite the myriad protections in place, what are the assembly line operators exposed to working on the line that the executive class of the corporate group are not exposed to working from home? As manufacturing is ramped up, what does the roll out of new vehicles mean for the larger ecosystem already experiencing collapse?
As the pandemic continues to grip the world, we will continue to provide regular updates about what the 3D printing community is doing in response. As always, it is important to keep safety in mind, remain critical about the potential marketing and financial interests behind seemingly good humanitarian efforts from businesses, and to do no harm.
The post 3D Printing and COVID-19, May 2, 2020 Update appeared first on 3DPrint.com | The Voice of 3D Printing / Additive Manufacturing.
AMS 2020: Keynote Presentations on 3D Printing in Metal and Medical Industries
For the second year running, and its third year total, 3DPrint.com and SmarTech Analysis have brought the Additive Manufacturing Strategies summit to Boston. With a theme of “The Business of 3D Printing,” the event continues its established coverage of 3D printing in the medical and dental industries, but adds a new metals track this year.
Lawrence Gasman, the President of SmarTech, welcomed everyone to the event, and then we jumped right into the thick of things, as Dr. Banu Gemici-Ozkan, Senior Market Intelligence Leader for GE Additive, presented her keynote, entitled “Metal Additive Strategies Enabling Next Generation of Adopters.”
Dr. Gemici-Ozkan explained that she’s been working with additive manufacturing for about four years, and her role is to oversee global operations, as well as support business in the metal AM space with the right applications.
“I’m in marketing, so I have to start with numbers,” she said, pulling up a slide of the “world of opportunities” for metal AM.
She explained that conventional manufacturing happens in many stages – you have to extract the metal, process it in chemical plants, assemble it into the final products, and several others that I’m definitely leaving out. Additive manufacturing can accomplish all of this in less steps, which is why it’s so attractive.
An example of an engine turbine came up, and at the bottom was a statement about how metal AM is competing with $570 billion worth of core conventional metal manufacturing processes. But, system redesign is what makes it competitive to this traditional methods – AM offers a simpler supply chain and leaner operations.
“It’s really exciting to see the potential of additive manufacturing,” Dr. Gemici-Ozkan said. “But where are we in this vision today?”
A timeline showed that the number of metal AM system installations in the first stage of the “diffusion of innovation,” in the 1990s, was less than 50…only the true innovators will put in the work of debugging these first systems and working out the kinks. The early adoption visionaries come in later, excited to invest in the technology.
“The customers are who drive the change,” she said. “So far, we’ve only seen innovators and visionaries.”
She explained that the next generation of the market will consist of the bigger players, or pragmatists, jumping on board. These adopters are cost-conscious, and will be looking for full solutions.
Then, she walked us through what she called the four “critical industries” in metal additive manufacturing. I’m sure you can guess them: medical, dental, aerospace, and automotive. When asked if they were there with the medical field, nearly half the hands in the room were raised, making Dr. Gemici-Ozkan’s point that this sector is a “great space to be in from a metal AM perspective.” The adoption drivers in this industry are cost and performance, with major applications in porous, biocompatible structures with fine features. Here, accuracy, repeatability, and traceability become really important.
Dental is the most mature industry for metal AM, a point that I heard multiple times throughout the day in different presentations. She explained that adoption drivers are lead time and customization; in this and the medical industry, the turnover time with metal 3D printed parts is roughly 24 hours, which you just can’t beat. Additionally, technology providers are focused on meeting customer needs.
In the aerospace industry, industrial production is the main focus. The materials are more versatile, and applications are in large parts and complex geometries with fine features.
“I could talk for hours about this industry,” she said.
“The potential is huge…this space offers a great potential from the industrial production perspective.”
She brought up the GE9X jet engine, which has 304 3D printed components and offers GE Aviation fuel savings of 10% when compared to its predecessor, the GE90, which only featured one 3D printed part.
The automotive industry is already automated, so its needs are focused on cost-conscious systems. Dr. Gemici-Ozkan said that AM technology providers “need to consider integrating their systems to the factory solutions.” The technology will have greater potential in this sector as material costs continue to come down, and she noted that binder jetting will be important in this space.
“Additive manufacturing is not a one-size-fits-all solution – it offers different solutions for different industries and applications,” Dr. Gemici-Ozkan said in summary. “It sounds like it’s all versatile, but these are the building blocks of mainstream technology.”
Then it was time for the next keynote presentation, “Medical 3D Printing: Building the Infrastructure for Innovation,” by Lauralyn McDaniel, Industry Manager, Analysis, for the American Society of Mechanical Engineers (ASME). Part of ASME’s mission is to improve people’s lives through engineering, which is definitely what 3D printing is working towards in the medical field.
McDaniel also started with numbers, with a slide stating that over one million patients had been directly impacted by AM, and that number increases to over two million when you take into account indirect impacts.
“Understanding the history of additive manufacturing in the medical industry can give us clues as to where we go from here,” McDaniel said, before launching into a brief timeline that began with the first 3D printed model from a medical image in 1988.
She explained that some of the factors leading to growth of the technology in the medical field include improved software, more material choices, precision medicine, faster and more precise processes, and the fact that more people share their resources and experience.
“You need published studies to generate the evidence that doctors need,” McDaniel explained.
Challenges include process bottlenecks, verification and validation processes, standards and regulations, and the workforce development.
Then, she cleared up something that many don’t always understand – most materials that people say are FDA-cleared are not, they have just been used in FDA-cleared devices. For example, titanium is often used in orthopedic implants, but the material itself is not cleared by the FDA, it’s just been cleared for use in the implant.
Continuing on to the regulatory process, McDaniel explained that there’s a “big difference” between a new product, and a new way to make the same product.
“The dental industry has a whole infrastructure set up to match patients with devices and implants, 3D printing just gives them a new, more efficient way to do it,” she said. “But anatomical models is a whole new product category.”
McDaniel said that ASME is supporting a series of discussions about the FDA’s concept framework for 3D printing at the point-of-care, and has worked with the agency to create validation and verification standards, including those for 3D printed medical devices. Just over half of the medical devices that have been cleared by the FDA are metal, so never fear, polymers are still significant in this space.
On the clinical side of things, standards aren’t quite as common, but she mentioned that the RSNA Special Interest Group is working to develop guidelines to help others with their own processes.
Some of the development highlights that McDaniel touched on include 3D printing-enabled tissue fabrication, clear dental aligners, which “exploded a bit because some of the patents expired,” tissue fabrication in outer space, and the fact that nearly 150 3D printed medical devices have been cleared by the FDA overall; at least three of these were patient-specific.
Moving forward with medical 3D printing, McDaniel said we need more collaboration and sharing of our experiences and resources, along with continuing materials development, improved software and AI, increased standards development, and more regulatory clarification, especially in hospitals.
Stay tuned to 3DPrint.com as we continue to bring you the news from our third annual AMS Summit.
Discuss this and other 3D printing topics at 3DPrintBoard.com or share your thoughts below.
[Photos: Sarah Saunders]
The post AMS 2020: Keynote Presentations on 3D Printing in Metal and Medical Industries appeared first on 3DPrint.com | The Voice of 3D Printing / Additive Manufacturing.
The State of 3D Printing in Industrial Goods, Part Two
In the last part of this series, we discussed a variety of general industrial product manufacturers that have begun to adopt 3D printing along the road from prototyping to end part manufacturing. Now, we’ll begin to look at service bureaus that 3D print general industrial goods for their customers. Because there are a number of service bureaus capable of producing parts for industrial product makers, we’ll limit our exploration to just those who market themselves for industrial goods specifically, or are otherwise aligned in such a way that they are already close to the industrial sector.
Kennametal is a tooling and materials supplier that has found a position in the AM space as a metal powders and AM services provider. The company makes powders for metal powder bed fusion (PBF), directed energy deposition (DED) and bound metal 3D printing (think Markforged and Desktop Metal’s desktop metal systems). These materials include gas-atomized cobalt, nickel and iron alloy powders (Stellite, Nistelle and Delcrome).
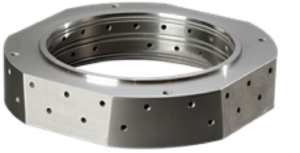
A 3D-printed valve cage made from Kennametal’s Stellite 6-AM-K powder. Image courtesy of Kennametal.
Kennametal has been 3D printing prototypes and cutting tools for some time, but took things a step further in fall of 2019 with the establishment of a Kennametal Additive Manufacturing business unit. The AM division will help customers through the entire process of securing materials, designing parts for 3D printing, and provide series production relying on binder jetting and PBF. An example component described on the unit’s website is a valve cage 3D printed for IMI Critical Engineering, which supplies flow control systems for industrial processes.
Aidro is an Italian company that makes hydraulic valves and systems for a variety of industries. The firm uses metal PBF to 3D print end-use parts that are up to 85 percent lighter than traditionally made counterparts. Other capabilities developed by Aidro include the ability to combine subcomponents into one single printed unit, improve performance over traditionally made parts, and take up less space than conventionally fabricated components.
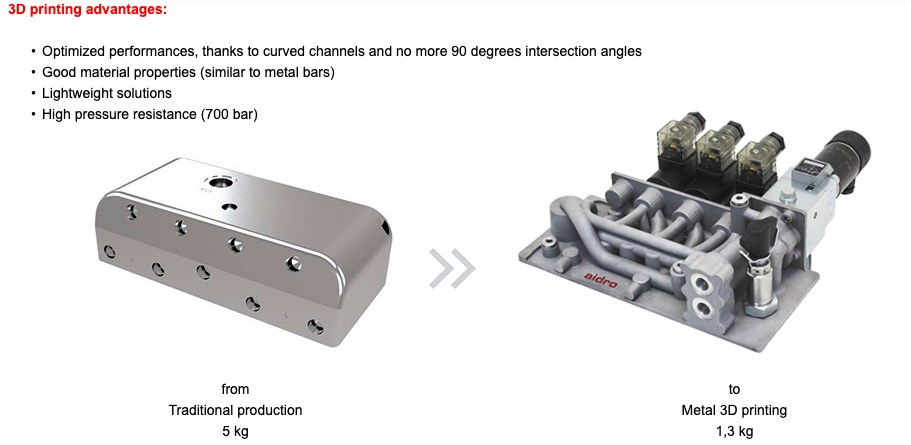
A comparison between a traditionally made hydraulic manifold and one redesigned for 3D printing. Image courtesy of Aidro.
HP’s partners GKN Additive and Parmatech will likely play increasingly important roles in AM for the industrial sector through the use of HP’s MetalJet 3D printers. Parmatech is a metal injection molding provider, which focuses on the medical and industrial sectors. Though GKN Additive is somewhat focused on aerospace and automotive parts, given the specialties of its parent company, GKN, it manufactures metal powders for AM and provides 3D printing services more broadly, augmented by its more recent acquisition of Forecast3D.
In particular, the company is tackling copper induction coils, which are used in the automotive and industrial sectors for tempering metal components to make them harder. In addition to allowing for the production of complex, custom copper inductor coils, 3D printing is actually a more repeatable and reliable process for fabricating these parts because the heat treatment phase is built into the production step.
GKN is not alone in this space, however. As niche as the application is, PROTIQ, a subsidiary of German industrial manufacturer Phoenix Contact, has an online configurator for customized copper induction coils, which it can 3D print as a part of is its larger 3D printing services. Additionally, the company offers optimized tooling for injection molding. 3D Inductors is another business that is entirely dedicated to 3D printing copper induction coils.
Though it does not offer its services through an online marketplace, NXCMFG is a service provider that focuses specifically on 3D-printed tooling. Using design and weight optimization, the company is able to 3D print metal molds and inserts with conformal cooling channels that reduce injection molding cycle times between 20 and 80 percent.
In addition to its metal powder production, Swiss engineering conglomerate Oerlikon’s AM division provides 3D printing services. While it can lean on its expertise across a number of verticals, Oerlikon AM boasts 20 years of experience in toolmaking and general industrial products. Examples on its website range from injection molding tools to a heating sleeve and a heating plate with built-in cooling channels and reduced part count.
DM3D is a manufacturer of directed energy deposition (DED) machines that also provides 3D printing services. Like many DED companies, DM3D markets its technology for both part fabrication and repair. This includes pumps for the agricultural industry, hardfacing cutting implements, and high productivity tooling. DED is capable of 3D printing with multiple metals, with which DM3D uses to produce tooling.
Carpenter Technology Corporation (CarTech) is metals company that has been increasing its stake in 3D printing, first by purchasing titanium powder company Puris, then by acquiring an electron beam melting service provider, CalRAM. Along with Proto Labs and Burloak Technologies, an engineering and manufacturing company, the two service providers have become part of the GE Additive’s Manufacturing Partner Network. All three companies perform AM of industrial goods and have expertise related to all forms of manufacturing. This, along with GE’s close ties to the industrial sector, will likely make the entire network an important component in production of industrial parts.
With headquarters in Austria, voestalpine in an important player in the industrial goods sector, providing AM services as a part of its international steel products manufacturing. In addition to developing metal powders for AM, the company has opened a new AM research institute in Taiwan, a production plant in Canada, and an AM center in Singapore. Aside from making products for just about every sector, voestalpine also manufactures molding and tools, highlighting the ability to 3D print molds with built-in conformal cooling.
Through a majority acquisition in AM service provider Materials Solutions, Siemens is now a 3D printing bureau. With a number of EOS metal PBF systems, the company has an established history in metal 3D printing dating back to 2006. Among the sectors it serves, Materials Solutions highlights the 3D printing of tooling from high-temperature super alloys and featuring conformal cooling.
U.K. engineering company Renishaw has its own line of metal PBF 3D printers, as well as Global Solutions Centres in which customers can begin their journey of AM adoption. As a part of this journey, clients can lease Renishaw machines or have parts printed as a service. Along with its expertise across a number of verticals, Renishaw offers 3D printing for industrial tooling and end parts. As we mentioned in our previous installment, Renishaw 3D printed screw-in milling cutters for KOMET Group in Germany.
SMS Group, which recently partnered with Additive Industries for the development of its serial production 3D printers, developers metal powders for AM and offers 3D printing services. Among the parts it has 3D printed for the industrial space are an SIS injector for electric arc furnaces, a PSM roll cooling ring for metalworking, and a 3D-printed multi-nozzle spray head for die maintenance.
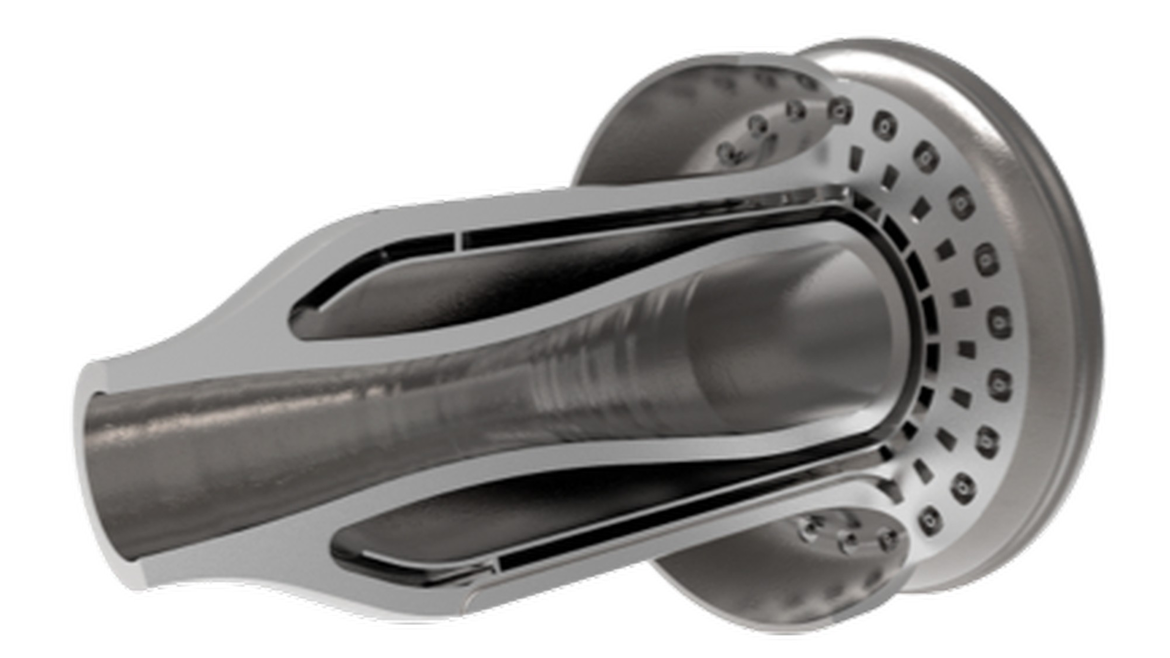
Previously welded from 18 different parts, this SIS injector is now made up of a single 3D-printed part and takes up 50 percent less space. Image courtesy of SMS Group.
Jabil is another service provider worth mentioning, given its size and the fact that it is an early adopter of HP’s Multi Jet Fusion (MJF) technology for mass production. After using Ultimaker printer farms in-house for printing jigs and fixtures on its assembly line, the contract manufacturer began using MJF, with HP itself as an early customer. The company 3D prints 50 polymer parts for HP’s printers.
In addition to the companies described here, there are a number of large AM service bureaus that you may already be familiar with that are involved in 3D printing tooling for the industrial sector. These include Stratasys Direct Manufacturing, Protolabs, Xometry, Materialise, Digital Metal, FIT AG and 3D Systems.
In the next installment in this series, we will take a look at some of the 3D printer manufacturers already providing systems for manufacturing industrial goods or primed to take advantage of that sector as it evolves.
The post The State of 3D Printing in Industrial Goods, Part Two appeared first on 3DPrint.com | The Voice of 3D Printing / Additive Manufacturing.
GE, ORNL, PARC receive $1.3 million to accelerate energy products with additive manufacturing
Optomec reaches milestone of 500 3D printers installed worldwide
Tuskegee University Selected by NASA to Advance Additive Manufacturing in Aerospace
The aerospace industry is a trendsetter when it comes to manufacturing. It is a major industry that evolved its expertise into lighter material, efficient engines and overall safer machines. Leveraging high technologies and reducing time-to-market is essential for the field to move forward, especially with a close future in the commercial development of low Earth orbit (LEO) and beyond. NASA is now accelerating manufacturing needs in the US space sector by selecting three minority-serving institutions to advance aerospace manufacturing. The space agency announced last week that Tuskegee University, in Alabama, will be one of three universities awarded grants through its Minority University Research and Education Project (MUREP). Part of NASA’s Office of STEM Engagement, MUREP partnered with the agency’s Aeronautics Research Mission Directorate to provide the students with the education and experience needed to help address manufacturing needs. Tuskegee will be looking into the impact of additive manufacturing on aerospace high-volume manufacturing and supply chain management.
“In recent years, the U.S. aerospace industry has struggled to meet the growing global demand for aircraft and parts, resulting in all-time-high order backlogs, unsustainable spare parts inventories, and lost opportunities for growth,” explained Firas Akasheh, an associate professor of mechanical engineering at Tuskegee University and leader of the project as its principal investigator.
Through the project, entitled Impact of Additive Manufacturing on Aerospace High-Volume Manufacturing and Supply Chain Management: Workforce Alignment through Research and Training, faculty researchers and students at Tuskegee will collaborate with the Bell Helicopter team, an American aerospace manufacturer headquartered in Fort Worth, Texas. Together, they will analyze current manufacturing and supply chain practices and develop executable 3D manufacturing plans for both helicopter and drone applications. In the drone track, university researchers will incorporate 3D printing into the design, build and test phases to improve the functionality and performance of these aircraft. The work will be conducted in increments to allow for continuous assessment of the quality performance of 3D printed parts.
Akasheh will lead a multidisciplinary research team that includes co-principal investigators Vascar Harris, a professor of aerospace science engineering; Mohammad Hossain, an associate professor of mechanical engineering; and Mandoye Ndoye, an assistant professor of electrical and computer engineering.
During the next two years, the project will provide students with innovative opportunities to learn about designing and building aerospace parts using high-volume manufacturing practices, as well as supply chain management. It will also help Tuskegee’s College of Engineering expand its existing additive manufacturing facilities and capabilities for the benefit of future academic and research efforts.
“3D printing offers an incredible advantage to current manufacturing shortfalls that risk the nation’s aerospace industry maintaining its competitive edge and meeting its strategic requirements,” Akasheh continued.
Indeed, Akasheh is on the right track: a 2019 Ernst and Young report suggests that aerospace and defense players are also increasingly adopting digital and advanced manufacturing technologies in the design and production of their products. Advanced manufacturing technologies, such as 3D printing, help them reduce supply chain lead time, improve reliability and productivity, and simplify designs. For example, to further enhance its advanced manufacturing capabilities, GE announced the acquisitions of Europe-based Arcam AB and Concept Lasers and is establishing a “GE Additive Customer Experience Center” in Germany. Among original equipment manufacturers (OEMs), Boeing has about 50,000 3D printed parts flying on its commercial, space, and military products. Airbus, on the other hand, is focusing on using AM for not only prototyping and parts manufacturing for a wide range of aircraft, but also for spare parts solutions. Simplifying engineering by using can improve time-to-market, quality, product reuse, significantly cut costs, and supply chain complexity.
Other minority-serving institutions funded through this NASA cooperative include the University of Texas at El Paso that proposed a southwest alliance for aerospace and defense manufacturing and talent development, and Virginia State University, in Petersburg, that will create a pilot program to advance all fronts of manufacturing in the sector.
The MUREP Aerospace High-Volume Manufacturing and Supply Chain Management Cooperative will provide almost $1.5 million to fund curriculum-based learning, research, training, internships, and apprenticeships at all three institutions to meet the growing demand for expertise and techniques in high-volume aerospace manufacturing.
For more than a decade, MUREP investments have enhanced the academic, research and technological capabilities of minority-serving institutions through multiyear grants. These institutions recruit and retain underrepresented and underserved students — including women, girls, veterans, and persons with disabilities — into STEM fields. Out of the total 3,289 enrolled students at Tuskegee, 62% are women, while 80% are Black. Encouragement and incentives are a great way to get people interested in the field of study. Additionally, if the gender gap in STEM careers will close sometime in the next 50 years, it will be with initiatives like MUREP that help us do it.
[Image credits: NASA and Tuskegee University]
The post Tuskegee University Selected by NASA to Advance Additive Manufacturing in Aerospace appeared first on 3DPrint.com | The Voice of 3D Printing / Additive Manufacturing.