A small gland (about the size of a small bean) located at the base of the skull, the pituitary secretes hormones and regulates the other major organs. Also known as the master gland, it is vital to good health, and can be seriously affected by over-production of hormones—or the opposite. When something goes wrong, surgery can be necessary, but tricky; for instance, endoscopic endonasal transsphenoidal pituitary surgery presents numerous challenges and risks as a procedure.
Seeking better solutions for surgeons, researchers came together to perform a recent study, detailing the results in ‘The manufacturing procedure of 3D printed models for endoscopic endonasal transsphenoidal pituitary surgery.’ Honing in on the need to provide better training—especially as cadavers can be hard to come by for both medical students and surgeons to practice on—the researchers examined the further potential of 3D printed models for improved planning.
In removing pituitary tumors, surgeons must work through the nose and sphenoid sinus, using tools to enter the nasal cavity and then actually break the bone until the sphenoid sinus is visible. This is considered to be challenging due to the complex anatomy of the nose, as well as in terms of how the sinus is situated, with the endoscope method most commonly used for surgical removal.
For this study, the authors not only propose that surgeons should be able to 3D print and customize skull models themselves but also use them ‘directly for simulation of the surgery.’ Along with that, their goal was to use a multi-tiered software system to offer better precision in creating the models from CT data.
“The limited accuracy of CT scanning and threshold segmentation may cause missing features and unexpected holes in the digital model,” explained the authors, moving forward to refine the process with new software.
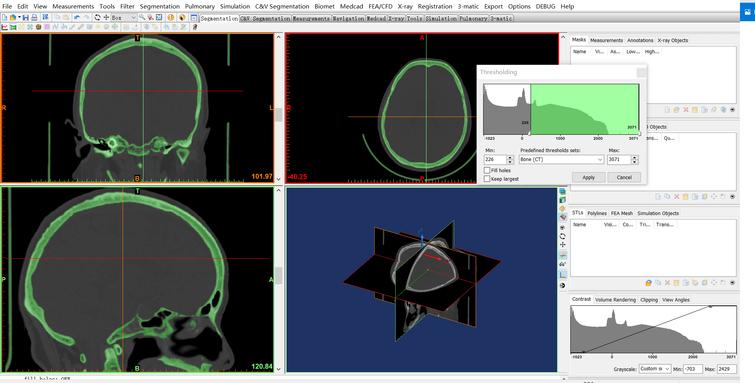
Set the thresholding value for Bone (CT). We select Menu bar > Segmentation > Thresholding, and set the minimum value as 226 (Bone (CT)) to get the required part of the skull model in this case. The thresholding result is saved as a new mask automatically.
Using Materialise Interactive Medical Image Control System (Mimics), they were able to improve the CT scan by fixing the holes at the base, along with using Geomagic to optimize and repair the skull base and surgical area. Segmentation consisted of extracting the nasal cavity and sellar region.
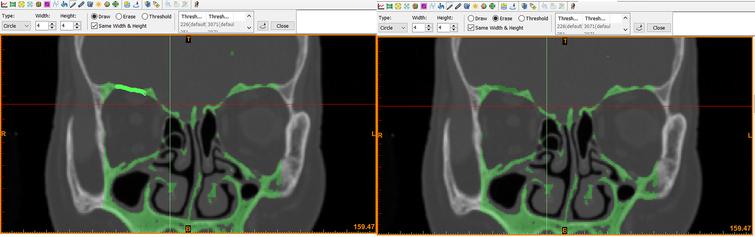
Fix the hole by drawing slice by slice. We use Menu bar > Segmentation > Edit Masks and select ‘Circle’ with reasonable size and select ‘Draw’ to connect the part.
3ds Max was used for segmentation and production of molds, correcting the surgical area and base into a polygon shape.
An Ultimaker 2 was used for 3D printing the base and molds, printing with PLA; however, for the surgical area, the researchers switched to binder jetting, using a 3D Systems ProJet 660 Pro with plaster.
“For the practice, the surgical area should be printed by the breakable and low-cost material (like plaster), as the sellar region will be broken during the real surgery,” explained the researchers.
Molds were used for fabrication of the soft tissue due to the expense in 3D printing the material directly. The researchers mixed pigment and silica gel to represent the following:
- Face
- Pituitary
- Optic nerves
- Internal carotid arteries
To imitate the pituitary tumor properly, the researchers set the model tumor underneath the optic nerve, using an adhesive for proper placement.
“With the assistance of 3D printed medical models, the surgery can be practiced repeatedly,” concluded the researchers. “The surgical safety can be improved, and the risk of death and morbidity can be reduced. In addition, the 3D printed medical model can be a good tool for the patient or their family members to learn about the disease, the condition and the risk of the surgery, which can promote the communication between the patients and neurosurgeons.”
“The outcomes demonstrate that the 3D printed skull model is able to improve the structure recognition learning. This case proves that the 3D printed anatomical model is worthy of use. Obviously, the model for specific surgery is able to improve the understanding of students or neurosurgeons on the specific or special situations.”
3D printed models are helpful today in a wide array of applications, but within the medical realm they are being used for diagnosing health conditions like tumors, as well as allowing for more streamlined treatment. Even better, such models allow more detailed explanations for patients and their families about ensuing treatments and possible surgical procedures.
Medical students are able to train with 3D printed models, surgeons can prepare for rare procedures—or those which have never been performed before—and such models may also be used as extremely helpful guides in the operating room too. Discuss this article and other 3D printing topics at 3DPrintBoard.com.
[Source / Images: ‘The manufacturing procedure of 3D printed models for endoscopic endonasal transsphenoidal pituitary surgery’]
The post 3D-Printed Models for Training & Planning of Endoscopic Pituitary Surgery appeared first on 3DPrint.com | The Voice of 3D Printing / Additive Manufacturing.