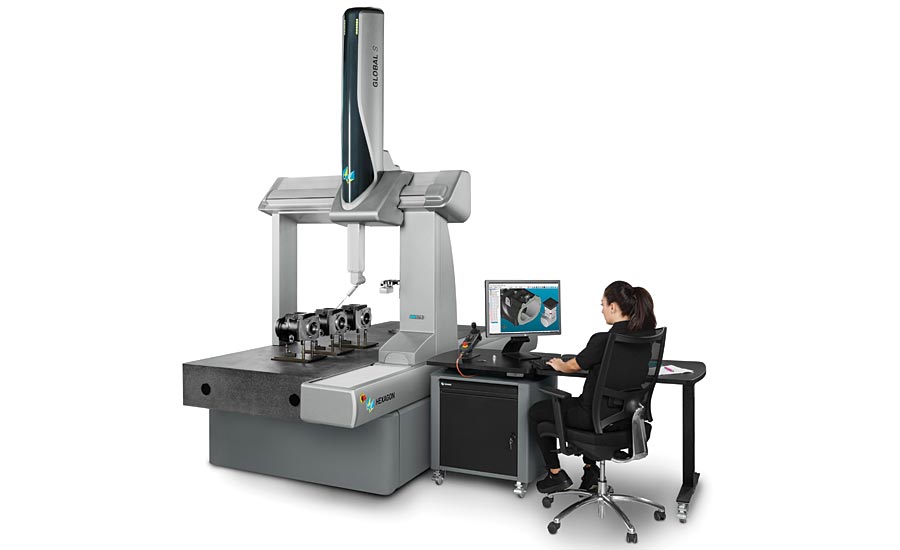
CMM
A CMM is a widely used machine used to measure objects. A CMM is a coordinate measuring machine. This refers to any machine that measures the geometry of physical objects by sensing discrete points on the surface of the object with a probe. This is the essence of many a metrology system. The precision of a CMM is vital for determining the geometry of objects. This then leads to more precision in the manufacturing and replication of objects.
Probes are the engine of a CMM. They sense objects through their surfaces. There are various types of probes as well. The types of probes used in CMMs include mechanical, optical, laser, and white light. Mechanical probes typically have a ball and rod looking setup attached to them, or have a nozzle setup. These physically touch the surface of a material that is in need of measuring. Optical probes typically refer to spectral analysis and measuring through these means. One can think of a fiber optic probe in particular. These type of probes are usually used in Raman spectroscopy, and diffuse reflection applications. Raman spectroscopy is a spectroscopic technique based on inelastic scattering of monochromatic light, usually from a laser source. Inelastic scattering means that the frequency of photons in monochromatic light changes upon interaction with a sample. The scattering of the photons within a monochromatic light source allows for a device to detect if an object is within the path of monochromatic light. This thus leads to measuring capabilities that are important in terms of a CMM as well. Diffuse reflection is similar to Raman Spectroscopy aside from the optical source is typically infrared. When an IR beam passes through a physical object, it can be reflected off the surface of a particle or be transmitted through a particle. The IR energy reflecting off the surface is typically lost. This transmission‐reflectance event can occur many times in the object, which increases the pathlength. This pathlength is vital for measuring. Finally, the scattered IR energy is collected by a spherical mirror that is focused onto the detector. The detected IR light is partially absorbed by particles of the object, collating the object information.

Typical Raman Spectroscopy Setup
A CMM is heavily reliant on a built-in coordinate system of, typically, three axes. This is similar to the coordinate systems we are aware of within a 3D build environment. This is a Cartesian Coordinate system. The main structure of which includes three axes of motion. The material used to construct the moving frame has varied over the years. Granite and steel were used in the early CMM ‘s. Today the major CMM manufacturers tend to build frames from aluminium alloy or some derivative and also use ceramic to increase the stiffness of the Z axis for scanning applications. CMM axises need to be stiff because there should be minimal outside inference with forces that may misalign the device during measurement. Any misalignment will cause higher error ranges for measurement.

Cartesian Coordinate System
Scanning techniques are becoming more reliant on data collection and compilation. These methods use either laser beams or white light that are projected against the surface of a part. Thousands of points can then be taken and used not only to check size and position but also to create a 3D image of the part also. This “point-cloud data” can then be transferred to CAD software to create a working 3D model of the part. The ability to hold various point cloud data from these methods is essential for the future development of the field. Big data is something of interest most definitely for this field.
CMM’s are very interesting and are the basis of most metrology methods. It is important to understand how in-depth and fascinating this field is. It is a very vital one as well for the future in terms of 3D printing and manufacturing. Stay tuned for the next installment where we take a look into different subfields within Metrology as well.
The post What is Metrology Part 2: CMM appeared first on 3DPrint.com | The Voice of 3D Printing / Additive Manufacturing.