Monitoring and quality control systems are becoming more widespread in additive manufacturing as a means of ensuring repeatability and aiming for first-time-right parts. A greater need for quality control are now trickling down to items that are more commonly made by the average consumer using FFF 3D printers, as detailed in “Open Source Computer Vision-based Layer-wise 3D Printing Analysis,” by Aliaksei L. Petsiuk and Joshua M. Pearce.
Dr. Joshua Pearce, an associate professor of materials science & engineering, and electrical & computer engineering at Michigan Technical University has performed extensive research into 3D printing, recyclability, and open-source platforms, along with protocrystallinity, photovoltaic technology, nanotechnology, and more.
As a proponent of 3D printing household items rather than purchasing them, Pearce foresees that the technology will infiltrate the mainstream and the average household much more deeply in the future. While there are many skeptics, this thinking is in line with many other tech visionaries who see great potential for 3D printing on all levels.
In a press release sent to 3DPrint.com, Pearce explains that quality control continues to be an issue at the household level—leading him to create a visual servoing platform for analysis in multi-stage image segmentation, preventing failure during AM, and tracking of errors both inside and out. In referring to previous research and development of quality control methods for “more mature areas of AM,” the authors realized that generally there is no “on-the-fly algorithm for compensating, correcting or eliminating manufacturing failures.
Analysis in Pearce’s program begins with side-view height validation, measuring both the external and internal structure. The approach is centered around repair-based actions, allowing users to enjoy all the benefits of 3D printing (speed, affordability, the ability to create and manufacture without a middleman, and more) without the headaches of wasted time and materials due to errors that could have been caught ahead of time. The overall goal is to “increase resiliency and quality” in FFF 3D printing.
“The developed framework analyzes both global (deformation of overall dimensions) and local (deformation of filling) deviations of print modes, it restores the level of scale and displacement of the deformed layer and introduces a potential opportunity of repairing internal defects in printed layers,” explain Petsiuk and Pearce in their paper.
Parameters such as the following can be controlled:
- Temperature
- Feed rate
- Extruder speed
- Height of layers
- Line thickness
While in most cases it may be impossible to compensate for mechanical or design errors, a suitable algorithm can cut down on the number of print failures significantly. In this study, the authors used a Michigan Tech Open Sustainability Technology (MOST) Delta RepRap FFF-based 3D printer for testing on a fixed surface improving synchronization between the printer and camera, based on a 1/2.9 inch Sony IMX322 CMOS Image Sensor and capturing 1280×720 pixel frames at a frequency of 30 Hz.
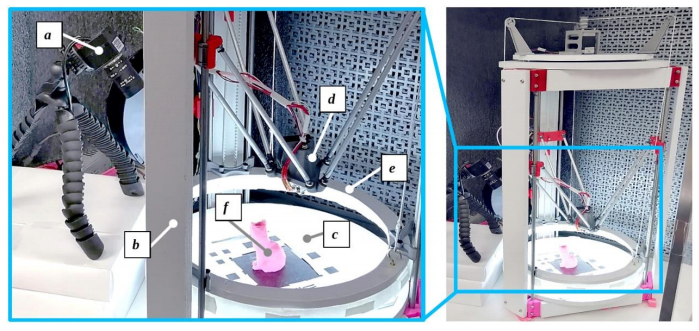
Visual Servoing Platform: working area (left), printer assembly (right): a – camera; b – 3-D printer frame; c – visual marker plate on top of the printing bed; d – extruder; e – movable lighting frame; f – printed part.

Projective transformation of the G-Code and STL model applied to the source image frame: a – camera position relative to the STL model; b– G-Code trajectories projected on the source image frame. This and the following slides illustrate the printing analysis for a low polygonal fox model [63].
The algorithm monitors for printing errors with the one camera situated at an angle, watching layers being printed—along with viewing the model from the side:
“Thus, one source frame can be divided into a virtual top view from above and a pseudo-view from the side.”
Currently, the study serves as a tool for optimizing efficiency in production via savings of time and material but should not be considered as a “full failure correction algorithm.”
Interested in finding out more about how to use this open-source analysis program? Click here.
[Source / Images: “Open Source Computer Vision-based Layer-wise 3D Printing Analysis”]
The post Michigan Tech Develops Open Source Smart Vision for 3D Printing Quality Control appeared first on 3DPrint.com | The Voice of 3D Printing / Additive Manufacturing.