3D Printing Industry Review of the Year July 2019
Liquid magnets made possible by Berkley lab 3D printing
Berkeley researchers 3D print all-liquid device for batteries and drug formulations
Lawrence Berkeley National Laboratory: Researchers Use Liquid-in-Liquid Printing to Create 3D Fluidic Devices
The mixing of oil and water is generally something most of us have no use for, with the two known to be immiscible liquids—meaning they do not combine together and eventually separate into layers. Researchers at Lawrence Berkeley National Laboratory are currently studying how these types of mixtures could be helpful in a variety of different scientific applications though. Their findings are discussed in a recently published paper, ‘Harnessing liquid-in-liquid printing and micropatterned substrates to fabricate 3-dimensional all-liquid fluidic devices,’ authored by Wenqian Feng, Yu Chai, Joe Forth, Paul D. Ashby, Thomas P. Russell, and Brett A. Helms.
In harnessing liquid structures to create 3D fluidic devices, the researchers explained that such an exercise is an ‘emerging design paradigm’ for chemists today interested in manipulating soft matter and figuring out ways to produce them on demand.
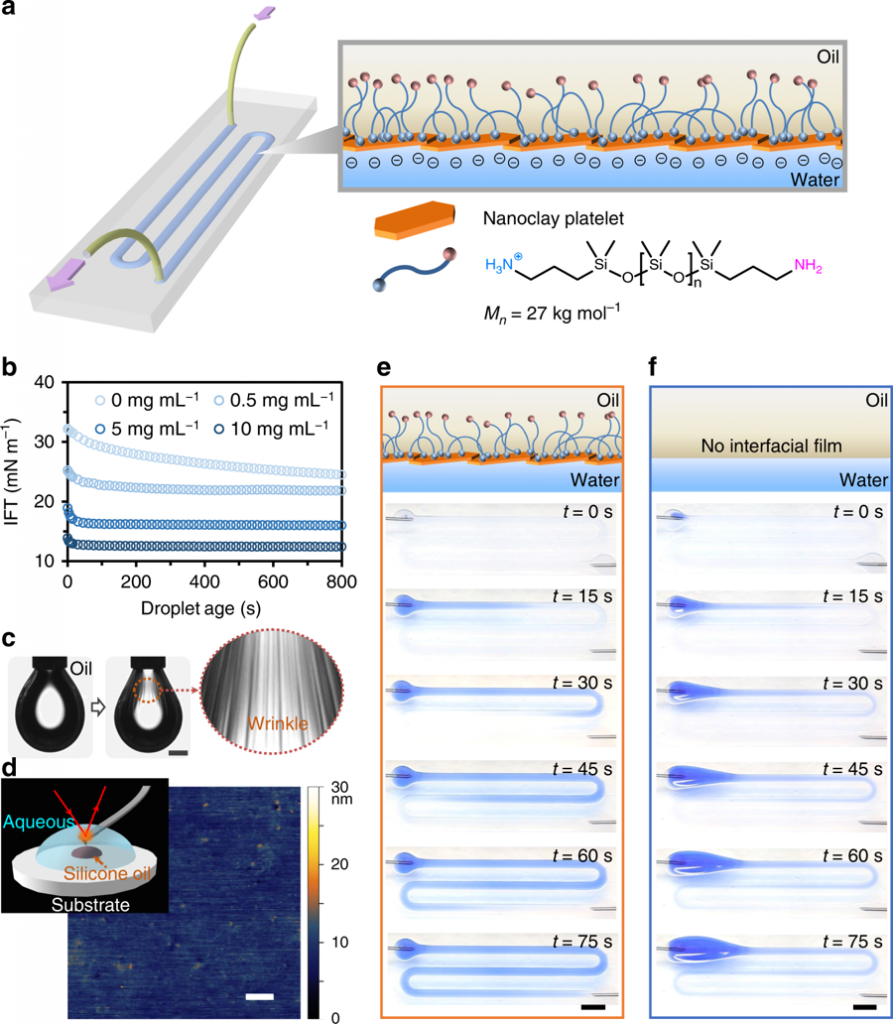
All-liquid fluidic devices stabilized by NPS membranes. a Schematic of an all-liquid fluidic device comprised of immiscible liquid phases confined in space using superhydrophobic−superhydrophilic micropatterned substrates. Nanoclay–polymer surfactants (NPSs) self-assemble at the liquid–liquid interface, forming an elastic wall that allows the all-liquid architecture to maintain integrity while fluid is pumped through the channel. b Temporal evolution of interfacial tension (IFT) of aqueous nanoclay dispersions (0.5, 5, and 10 mg mL−1, pH 7.0) introduced to solutions of H2N-PDMS-NH2 in toluene (10% w/w), illustrating control over the rate of NPS assembly at the interface. c Buckling behavior observed when retracting a droplet cladded with the interfacial NPS film. Scale bar, 1 mm. d In-situ AFM image of the NPS film. The inset shows the schematic diagram of the experimental setup for AFM measurements. Scale bar, 100 nm. e, f Time-lapse images of a solution of blue-colored dye being pumped (10 mL h−1) through the channel in the presence (e) and in the absence (f) of the NPS film. Scale bars, 5 mm. AFM atomic force microscopy
“Still nascent in their development, structured liquids presently lack clear design rules for controlling their 2D or 3D architectures, spatially directing functional components within each liquid phase, and coupling physiochemical processes across the liquid−liquid interface so as to create autonomous chemical systems capable of performing useful work, processing information, or executing logical functions,” state the scientists.
To make such devices, glass supports were coated with superhydrophobic polymers. Next, the researchers used photo-patterning with superhydrophilic channel architectures, also accompanied by an aqueous dispersion of anionic 2D nanoclays.

Semi-permeability of 2D NPS interfacial films. a Schematic showing selective mass transfer across the water–oil interface through the NPS film. b Stacked UV–Vis spectra of a neutral dye (1) at 5-min time-intervals, monitoring dye transfer from water to toluene across the NPS membrane film in a masked cuvette. The inset shows the chemical structure of dye 1 engaged in mass transfer. c LSCM images of the fluidic channel after infusing dye 1 solution in the preformed liquid channel covered by toluene. d A fluidic device depicting the flow of a mixed solution of dye 1 and resazurin sodium (2) for chemical separation. [1] = 1.4 mg mL−1, [2] = 1 mg mL−1. Photographs of the diluted inlet, outlet, and overlay of toluene solutions collected in cuvettes show the dye separation after infusing the mixed solution at a flow rate of 0.2 mL h−1 for 1 h. Scale bar, 5 mm. e UV–Vis spectra of the diluted inlet and outlet solutions used to quantify the efficiency of dye 1 partitioning from the aqueous phase to the toluene phase. NPS nanoparticle−polymer surfactant, LSCM laser scanning confocal microscopy
“Interfacial forces are effective in pinning and confining the aqueous phase in arbitrarily complex geometries and a wide range of channel widths,” stated the research team.
The manipulated systems are able to reach the desired steady state quickly, and nanoparticle−polymer surfactants (NPS) topography was presented after the researchers employed atomic force microscopy. They reported that their data demonstrated ‘well-packed nanoclays’ at the interface with no structural problems. The researchers also noted that only microchannels with NPS walls could guide flow at the desired rate. Without them, the aqueous phase proceeded to build up at the channel entrance. The team also noted that maximum flow is completely reliant on the channel’s cross-section and overall architecture.
The team also went on to investigate membrane permeability, functionalization, and further chemical transformations regarding the fluidic devices with the requisite NPS walls. With the use of NPS films, they found that added microchannels were ‘straightforward to introduce’ direct-write methods.
“To contextualize this advance, without the aid of micropatterned substrates and NPS films, constructing channel-like aqueous threads in oil is not typically possible, as the thermodynamic driving force required to reduce interfacial area breaks up aqueous threads into droplets,” stated the researchers.

a Schematic of fabricating 3D microchannels stabilized by nanoclay-surfactant interfacial assembly to connect the separated microchannels by printing of water in oil. Disconnecting these microchannels is also possible by cutting these “bridges” off. b Adjacent channels on a patterned substrate connected by a 3D printed overpass. Na-fluorescein (0.1 mg mL−1) has been added to the clay dispersion to clarify features of the constructs. Scale bar: 2 mm. c Fabrication of a 3D bridge linking separate channels (middle panel) and clipping the bridge (right panel). Scale bar: 500 µm.
The fabricated microchannels offered such a stable structure during research and evaluation that the researchers found they could use them as bridges either connecting separate regions on the substrate, or in connecting the device to an exogeneous entity.
“Our studies uncover a latent learning ability in such devices, in that physiochemical sensing or detection of channel properties and contents can be used to direct the architecture of the device to achieve a specific outcome. Maturation of the design concept led to devices that can execute complex tasks in a logical manner by reversible compartmentalization of function and direction of chemo-energetic flows that operate far from equilibrium conditions,” concluded the researchers.
“The potential for this system to exhibit autonomous learning is evident. Such devices may also be arrayed to generate deep or dark data for machine learning, e.g., from all-liquid (bio)chemical transformations and screens, to build knowledge and understanding from chemical logic.”
Fabrications methods used in 3D design and 3D printing today span many different industries and intricate applications, but you may be surprised to explore further into the science of materials, hardware, and software, and realize how many chemists are using the technology from use in continuous flow systems to studies centered around miniaturization and complex designs in microfluidics. Learn more about current processes in liquid-in-liquid printing here.
What do you think of this news? Let us know your thoughts! Join the discussion of this and other 3D printing topics at 3DPrintBoard.com.
[Source / Images: Harnessing liquid-in-liquid printing and micropatterned substrates to fabricate 3-dimensional all-liquid fluidic devices]
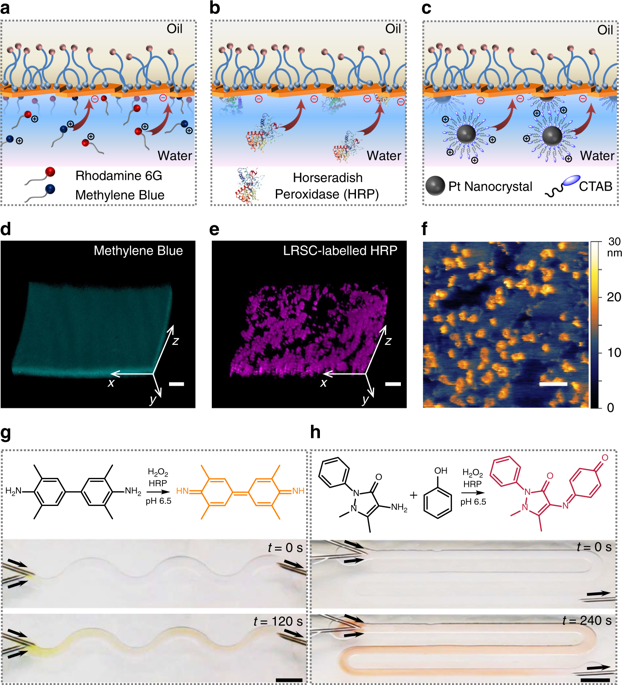
All-liquid microreactors. a–c Schematic of the anchoring of cationic molecules (a), enzymes (b), and nanocrystals (c) to the anionic NPS film lining the microchannels. d, e 3D reconstitution of confocal images of methylene blue (d) and LRSC-labeled HRP (e) to determine the adhesion of cationic species to the NPS wall of the microchannel. Scale bars, 100 µm. f In-situ AFM image of the NPS film immobilized with CTAB-coated Pt nanocrystals at the water−silicone oil interface. Scale bar, 100 nm. g, h Oxidation of TMB (g) and 4-AAP/phenol (h) substrates catalyzed by immobilized HRP in the channels, which generate products with distinctive colors under flow. Scale bars, 5 mm. NPS nanoparticle−polymer surfactant, LRSC lissamine rhodamine B sulfonyl chloride, HRP Horseradish peroxidase, TMB 3,3′,5,5′-tetramethylbenzidine, 4-AAP 4-aminoantipyri
New Research Could Lead to DNA 3D Printer
Technology is capable of amazing things, but it doesn’t mean those things are easy. It’s incredible that scientists can produce DNA in a lab, but the process is difficult, lengthy and requires toxic chemicals. Imagine, however, if they could simply print it, the way that you would 3D print anything else. That could be the future, after scientists at UC Berkeley and Lawrence Berkeley National Laboratory developed a new way to synthesize DNA. The method could lead to DNA printers, similar to ordinary 3D printers, that could produce DNA strands that are more accurate and 10 times longer than the strands produced with today’s methods – more quickly and easily, and without the use of toxic chemicals.
“If you’re a mechanical engineer, it’s really nice to have a 3D printer in your shop that can print out a part overnight so you can test it the next morning,” said UC Berkeley graduate student Dan Arlow. “If you’re a researcher or bioengineer and you have an instrument that streamlines DNA synthesis, a ‘DNA printer,’ you can test your ideas faster and try out more new ideas. I think it will lead to a lot of innovation.”
The research was led by Arlow and PhD student Sebastian Palluk, a doctoral student at the Technische Universität Darmstadt in Germany and a visiting student at Berkeley Lab. It is published in a paper entitled “De novo DNA synthesis using polymerase-nucleotide conjugates,” which you can access here. The research was conducted at the Department of Energy’s Joint BioEnergy Institute (JBEI).
“I personally think Dan and Sebastian’s new method could revolutionize how we make DNA,” said Jay Keasling, a UC Berkeley professor of chemical and biomolecular engineering, senior faculty scientist at Berkeley Lab and Chief Executive Officer of JBEI.
Keasling and JBEI scientists specialize specialize in adding genes to microbes, typically yeast and bacteria, to sustainably produce useful products. Palluk came from Germany specifically to work with Arlow in Keasling’s lab.
“We believe that increased access to DNA constructs will speed up the development of new cures for diseases and simplify the production of new medicines,” Palluk said.
The synthesis of DNA is a growing business; companies are ordering custom-made genes so that they can produce chemicals, biologic drugs or industrial enzymes. Researchers purchase synthetic genes to engineer plants and animals or try out new CRISPR-based disease therapies. Some scientists have even researched storing information in DNA, but that would require much larger quantities of DNA than are currently synthesized. All of these applications require that synthesis produce the desired sequence of nucleotides or bases, the building blocks of DNA, in each of millions or billions of copies of DNA molecules.
Current DNA synthesis is limited to producing oligonucleotides about 200 bases long, because errors in the process lead to a low yield of correct sequences as the length increases. To assemble even a small gene, scientists have to stitch together segments of about 200 bases long. The turnaround time for a small gene of 1,500 bases long can be two weeks at a cost of $300, limiting the experiments that scientists can do. Synthetic biologists like Arlow, Palluk and Keasling often insert a dozen different genes at once into a microbe to get it to produce a chemical, and each gene presents its own synthesis problems.
“As a student in Germany, I was part of an international synthetic biology competition, iGEM, where we tried to get E. coli bacteria to degrade plastic waste,” said Palluk. “But I soon realized that most of the research time was spent just getting all the DNA together, not doing the experiments to see if the engineered cells could break down the plastic. This really motivated me to look into the DNA synthesis process.”
The technology developed by Palluk, Arlow, Keasling and their team relies on a DNA-synthesizing enzyme found in cells of the immune system that has the natural ability to add nucleotides to an existing DNA molecule in water, where DNA is most stable. The technology results in increased precision, allowing synthesis of DNA strands several thousand bases long – a medium-sized gene.
“We have come up with a novel way to synthesize DNA that harnesses the machinery that nature itself uses to make DNA,” Palluk said. “This approach is promising because enzymes have evolved for millions of years to perform this exact chemistry.”
Cells create DNA by copying it with the help of several different polymerase enzymes that build on DNA already in the cell. But in the 1960s, scientists discovered a polymerase that doesn’t rely on an existing DNA template but instead randomly adds nucleotides to genes that make antibodies for the immune system. The enzyme, called terminal deoxynucleotidyl transferase (TdT), creates random variation in these genes, resulting in antibody proteins that are better able to attack new types of invaders.
TdT is fast and does not have side-reactions that could affect the resulting molecule. Scientists over the years have tried to use the enzyme to synthesize DNA sequences, but it was hard to control. The key is to find a way to get the enzyme to add one nucleotide and then stop, so that the sequence can be synthesized one base at a time. Previous approaches tried to obtain that control by using modified nucleotides with a special blocking group that prevents multiple additions at once. After the DNA molecules have been extended by a blocked nucleotide, the blocking groups are removed to allow the next addition.
TdT, however, cannot accommodate a blocking group on the nucleotide being added. But Arlow came up with the idea to tether an unblocked nucleotide to TdT, so that after the nucleotide is added, the enzyme remains attached and prevents further additions. After the molecule has been extended, the tether is cut, releasing the enzyme and re-exposing the end for the next addition.
In the first trials, the researchers demonstrated that this technique is not only faster and simpler, but nearly as accurate as other techniques in each step of the synthesis.
“When we analyzed the products using NGS, we were able to determine that about 80 percent of the molecules had the desired 10-base sequence,” Arlow said. “That means, on average, the yield of each step was around 98 percent, which is not too bad for a first go at this 50-plus-year-old problem. We want to get to 99.9 percent in order to make gene-length DNA.”
Once they can reach 99.9 percent fidelity, they can synthesize a 1,000-base-long molecule with a yield of more than 35 percent, which is currently impossible with existing techniques.
“By directly synthesizing longer DNA molecules, the need to stitch oligonucleotides together and the limitations arising from this tedious process could be reduced,” said Palluk. “Our dream is to directly synthesize gene-length sequences and get them to researchers within few days.”
“Our hope is that the technology will make it easier for bioengineers to more quickly figure out how to biomanufacture useful products, which could lead to more sustainable processes for producing the things that we all depend on in the world, including clothing, fuel and food, in a way that requires less petroleum,” said Arlow.
He added, “Our dream is to make a gene overnight. For companies trying to sustainably biomanufacture useful products, new pharmaceuticals, or tools for more environmentally friendly agriculture, and for JBEI and DOE, where we’re trying to produce fuels and chemicals from biomass, DNA synthesis is a key step. If you speed that up, it could drastically accelerate the whole process of discovery.”
Discuss this and other 3D printing topics at 3DPrintBoard.com or share your thoughts below.
[Source: UC Berkeley / Images: Marilyn Chung, Berkeley Lab]