In the recently published ‘Antioxidant PLA Composites Containing Lignin for 3D Printing Applications: A Potential Material for Healthcare Applications,’ Belfast researchers experiment with new 3D printing materials. Due to its strength as a biopolymer and an antioxidant, the research team combined lignin with poly(lactic acid) in FDM 3D printing.
Coating PLA pellets with LIG powder and castor oil, which is biocompatible, they extruded the material at 200 °C. The researchers reported LIG loadings that ranged from 0% to 3% (w/w). With the goal of providing additional, beneficial features to PLA, the research team tried varied strategies, to include incorporating molecules with antioxidant properties to PLA.
“The unrestrained production of free radicals and reactive oxygen species is linked with the onset of diseases such as rheumatoid arthritis, atherosclerosis or cancer,” stated the researchers. “Accordingly, the development of antioxidant compounds/materials can contribute to reduce the concentration of these compounds. Moreover, it has been shown that the excess of reactive oxygen species prevents wound healing. Accordingly, antioxidants have been proposed to control oxidative stress in wounds to accelerate their healing.
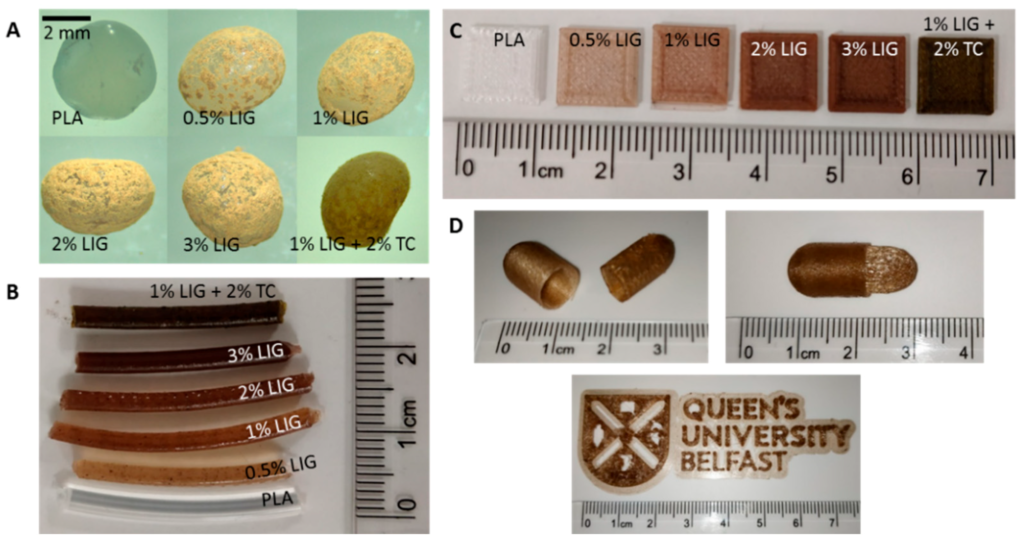
Photographs of: PLA and PLA coated pellets (A); LIG and TC containing PLA filaments (B); LIG and TC containing 1 cm × 1 cm squares prepared using 3D printing (C); and different shapes printed using the filament containing 2% (w/w) LIG (D).
Previously, SLA 3D printing was used to fabricate antioxidant vascular stents with bioresorbable abilities, while SLS 3D printing was used to create materials with antioxidants to promote cell growth. While the actual compound was not disclosed, the researchers reported that they used UV-stable polyamide 12 material with antioxidant properties. LIG is known to possess both antioxidants and antimicrobes and incidentally, is also the second most abundant polymer on our planet—with researchers still having plenty of studying to do—especially for biomedical applications.
As the researchers combined LIG with PLA here, the intent was to develop a composite for healthcare as the materials were combined through extrusion, characterized, and then actually used in FDM 3D printing. It is expected that these composites can be used for wound dressings due to the potential for localized antibacterial qualities. Here, the researchers used tetracycline (TC) as the antibacterial agent.
Used in wound dressings, the composite made up of LIG and PLA would allow for customization of size and shape—and not only that, PLA offers a biodegradable form.
“The present work showed that PLA and LIG can be combined easily by coating PLA pellets with LIG. Other alternatives to prepare PLA/LIG composites have been explored but they require organic solvents or more complex equipment such as twin screws extruders,” concluded the researchers.
“Antioxidant packaging can be used to improve the condition and increase the shelf-life of packaged food. Due to the enhanced cell proliferation on antioxidant materials, these materials can be used for tissue culture applications or even for regenerative medicine. Due to the versatility of FFF, complex geometries can be prepared such as scaffolds. However, before this type of material can be implanted into humans, the safety of lignin-based materials should be evaluated. It has been reported before that LIG-based materials are biocompatible, but more studies should be performed.”
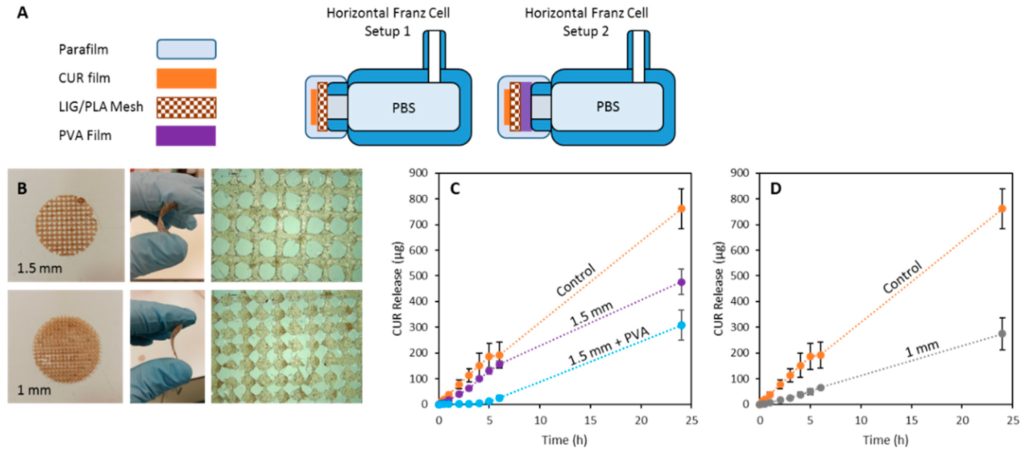
Experimental setup used to measure drug diffusion trough the 3D printed meshes (A); photographs of the 3D printed meshes made of PLA and 2% (w/w) LIG (B); and CUR release through 1.5 mm (C) and 1 mm (D) 3D printed meshes (n = 3).
As the range of 3D printing materials continues to expand, so does research and development of composites, from thermoset composites for aerospace to glass composites, nanocomposites, and more.
What do you think of this news? Let us know your thoughts! Join the discussion of this and other 3D printing topics at 3DPrintBoard.com.
[Source / Images: ‘Antioxidant PLA Composites Containing Lignin for 3D Printing Applications: A Potential Material for Healthcare Applications’]
The post Belfast: 3D Printing with Antioxidant PLA Composites Shows Potential in Medical Applications appeared first on 3DPrint.com | The Voice of 3D Printing / Additive Manufacturing.