Oral cancer is on the rise around the world, and it’s especially bad in developing countries, such as Pakistan, Sri Lanka, and India, which don’t have the necessary medical infrastructure for early detection and treatment. A team of researchers from Boston and India explained in their paper, “Platform for ergonomic intraoral photodynamic therapy using low-cost, modular 3D-printed components: Design, comfort and clinical evaluation,” that there is “critical demand for an effective treatment modality that can be transparently adapted to low-resource settings.”
“The high expense and logistical barriers to obtaining treatment with surgery, radiotherapy and chemotherapy often result in progression to unmanageable late stage disease with high morbidity. Even when curative, these approaches can be cosmetically and functionally disfiguring with extensive side effects. An alternate effective therapy for oral cancer is a light based spatially-targeted cytotoxic therapy called photodynamic therapy (PDT),” the researchers wrote.
PDT uses a photosensitizer molecule accumulated in the tumor, and once it interacts with a specific light wavelength, it can cause targeted damage. It has few side effects, doesn’t cause disfigurement or loss of sensation, and has shown some good clinical results in terms of good post-treatment healing and epithelial necrosis. For regions with fewer medical resources, it would be very helpful to translate PDT therapy so it can be completed in an outpatient visit, and 3D printed oral applicators would be a great help on this journey.
“Despite excellent healing of the oral mucosa in PDT, a lack of robust enabling technology for intraoral light delivery has limited its broader implementation,” the team continued in their paper.
“Leveraging advances in 3D printing, we have developed an intraoral light delivery system consisting of modular 3D printed light applicators with pre-calibrated dosimetry and mouth props that can be utilized to perform PDT in conscious subjects without the need of extensive infrastructure or manual positioning of an optical fiber.”
The team’s goal in this study was to evaluate the clinical utility and ergonomics of their 3D printed oral PDT applicators, which were designed to comfortably, and stably, deliver light to patients’ oral lesions.
“Here, the natural structure of the patients’ oral cavity, teeth and jaw provided the support and stability to hold the fiber in place, avoiding any use of posts, holders, reflectors or light pipes,” the researchers explained.

3D Schematics of the applicators for three different regions in the mouth. The photos showcase the integrated unit with the applicator (1), the bite wing (2) and the endoscope (3) utilized in the ergonomics clinical study.
The 3D printed intraoral applicators, which attach to the optical fiber, have two parts – bite blocks and applicators. The blocks position the angle of the applicator, which then delivers the suitable beam spot, along with pre-calibrated dosimetry, to a certain lesion size. The team used Autodesk Fusion 360 to design the light applicators, and they were printed on a Stratasys Objet Pro system out of VeroBlue and VeroBlack filament.
In order to determine how stable and comfortable the applicators were, the researchers performed a study, approved by the Massachusetts General Hospital Partners Institution Review Board, on ten subjects.
A physician placed three fiducial ink marks on each subject’s inner cheek, and tested the anterior and posterior buccal cheek and retromolar positions for ten minutes, one after the other. The light delivery fiber was replaced with an endoscope of similar size, with a 5.5 mm diameter camera and 6 LEDs, in order to record motion at these three spots.
The researchers explained, “Subjects were asked to rate comfort and fatigue on a numerical scale of 1 to 5 where 1 was no discomfort due to the applicator and 5 was intolerable discomfort due to the applicator.”
Each subject was asked three questions:
- Was there any physical discomfort during the ten minutes?
- Rate the fatigue or numbness in your mouth.
- Would you be comfortable immediately repeating another ten-minute interval at the same site?
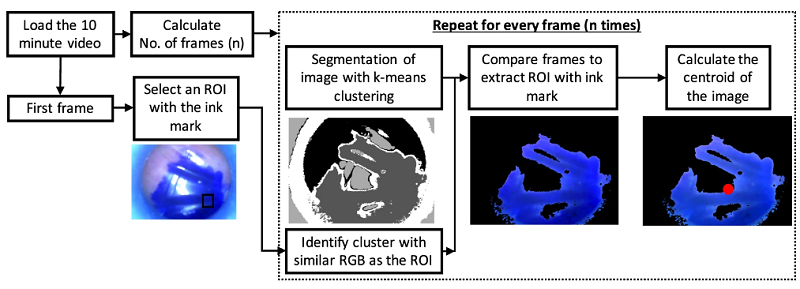
Flow chart of video and image processing method to calculate centroid of the fiducial ink mark mimicking the anterior buccal cheek, posterior buccal cheek or retromolar position imaged with a USB Endoscope fitted to the oral applicators.
Additionally, the endoscope actually recorded the movement of the ink marks during testing in order to evaluate the applicators’ stability. Custom-designed algorithms in MATLAB were used to process the videos. They determined that the applicators were indeed stable, and capable of “delivering light precisely to the target location in ten healthy volunteers.” Additionally, the ten subjects rated the devices overall as comfortable, though one did report “no tolerance” to the applicator in the posterior buccal cheek position.
Five of the subjects had confirmed T1N0M0 oral cancer lesions with no lymph node involvement, and several months after PDT treatment, demonstrated no cancerous lesions, fibrosis, or scarring. This showed that the 3D printed applicators, paired with an inexpensive fiber and LED-based light source, “served as a complete platform for intraoral light delivery achieving complete tumor response with no residual disease at initial histopathology follow up in these patients.”
“While we used a set of applicators with pre-determined sizes that were comfortable for various subjects, mouth and jaw dimensions and genders, it is reasonable to envision extension of this approach to customized patient treatment. Specifically, personalized applicators can be rapidly printed at the time of procedure due to advances in image-based 3D printing and the increasing availability of low-cost, high-quality 3D printers in clinical settings,” the researchers concluded.
“The ergonomic design of 3D printable light applicators has significant practical benefit in enabling longer irradiation duration and improved accuracy of light delivery necessary for curative PDT. With costs of healthcare and cancer incidences increasing worldwide, particularly in developing countries, we report an affordable methodology for delivering light stably and ergonomically in the oral cavity which can be used in conjunction with a low-cost, portable, battery-powered fiber-coupled LED based light source.”
This is just one more good example of 3D printing successfully being used for cancer therapy.
Co-authors of the paper are Srivalleesha Mallidi, Amjad P. Khan, Hui Liu, Liam Daly, Grant Rudd, Paola Leon, Shakir Khan, Bilal M. A. Hussain, Syed A. Hasan, Shahid A. Siddique, Kafil Akhtar, Meredith August, Maria Troulis, Filip Cuckov, Jonathan P. Celli, and Tayyaba Hasan.
Discuss this and other 3D printing topics at 3DPrintBoard.com or share your thoughts below.
The post Researchers Evaluate Comfort and Stability of 3D Printed Applicators for Oral Cancer Therapy appeared first on 3DPrint.com | The Voice of 3D Printing / Additive Manufacturing.