Wear resistance in 3D printed materials is critical for many users, with few research studies so far delving into such details for ABS or PC-ABS blends. Much of the concern is centered around anisotropic mechanical properties too, all in relation to ‘friction direction,’ with their findings outlined in ‘Preliminary Characterization of Novel LDPE-Based Wear-Resistant Composite Suitable for FDM 3D Printing.’
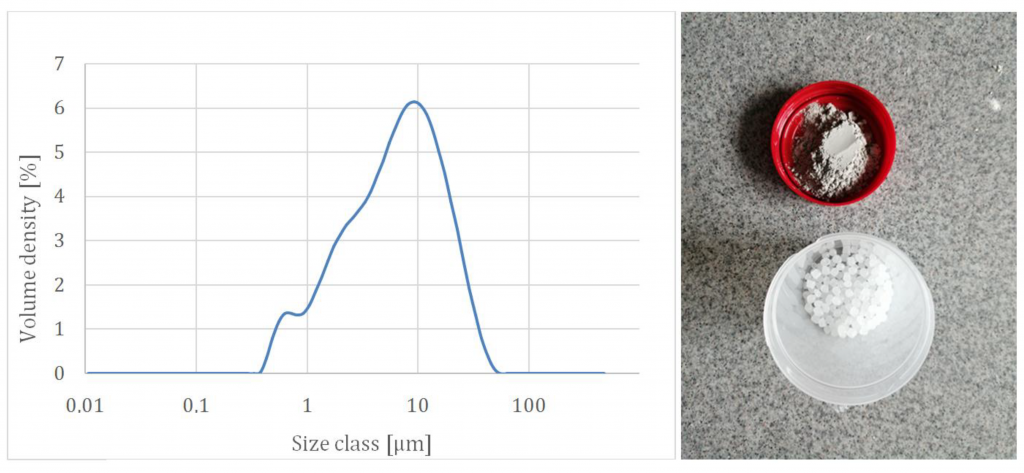
The particle size distribution of the obtained glass powder (left) and the powder with low-density polyethylene (LDPE) granules (right).
Low-density polyethylene (LDPE) is a polymer used in many different types of packaging, and the authors point out that it is responsible for a substantial amount of waste—which optimally, should be recycled in FDM 3D printing. And while this is certainly not a novel idea, with the exercise of recycling plastic that has been discarded and grinding it into pellet or powder form for re-use being completely feasible, it is not a habit that has become widespread with users yet.
In exploring LDPE, the authors point out that it not only has inferior strength and stiffness but is also responsible for adhesion issues and high shrinkage—all qualities pointing to the need for a composite material with the potential for adding ceramic or metal.
“As mentioned before, adding ceramic or metal powders to LDPE can improve its storage modulus, reduce shrinkage, and increase its mechanical properties. Currently, LDPE composites with a mold flow index (MFI) of 10 g/10 min were successfully printed, so it is possible to manufacture an LDPE composite filament for FDM printing made from waste materials,” stated the researchers.
LDPE as a friction material offers potential, and especially when wear resistance is a critical issue; for example, the soles of shoes also require hardness, plasticity, elasticity, and more. LDPE can also be used as a near-surface filler or in creating products like sliding pads (commonly used with furniture).
The team created a composite, recycling even further with glass waste—obtained from shredded car windshields—refining both technological and wear-resistance properties and testing their results.
Composites exhibited suitable layer adhesion, devoid of cracks or voids. The research team employed a mathematical model for feed rate and printing speed—discovering in this study that the higher modulus allowed for more rapid printing, but also offered greater potential in defects due to the speed. Higher crystallinity was also found, but only slightly and ‘close to the error limit.’ The addition of the recycled glass was a suitable ‘reinforcement’ according to the researchers, who found that it did strengthen wear resistance further.
“An evident effect of the friction direction vs. the printed path direction on the wear appeared, which was probably related to differences in the removal of friction products from the friction area for different print-path layouts against the friction direction,” concluded the researchers.
“The LDPE composite with auto-screen glass particles is a promising material and should be studied further.”
Composites have become not only an interesting area of focus for 3D printing users but also a useful one as researchers and developers strengthen materials with wire composites, reinforced carbon fiber, and PLA. What do you think of this news? Let us know your thoughts! Join the discussion of this and other 3D printing topics at 3DPrintBoard.com.
[Source / Images: ‘Preliminary Characterization of Novel LDPE-Based Wear-Resistant Composite Suitable for FDM 3D Printing’]
The post Testing Low-Density Polyethylene Glass Composites in FDM 3D Printing appeared first on 3DPrint.com | The Voice of 3D Printing / Additive Manufacturing.