After becoming one of the fastest-growing 3D printing startups, Desktop Metal announced plans to go public following a reverse merger deal with blank check company Trine Acquisitions. The Boston-based metal 3D printing systems manufacturer revealed that the combined companies will be listed on the New York Stock Exchange (NYSE) under the ticker symbol “DM” and are expected to have an estimated post-transaction equity value of up to $2.5 billion.
2020 has seen a surge of company’s opting to go public through special purpose acquisition company (SPAC) merger deals. During the first half of the year, there have been 79 SPAC IPOs that have raised gross proceeds of $32 billion, according to SPACInsider, a sharp increase from last year’s 59 SPAC IPO’s and gross proceeds of $13.6 billion. In fact, Desktop Metal follows in the steps of space tourism startup Virgin Galactic and electric car maker Nikola Corp, drawn to SPAC listings to go public without the risk and complexity of a traditional IPO.
Since coming out of stealth mode in 2017, Desktop Metal has managed to raise over $438 million in funding, becoming one of the fastest companies in US history to achieve unicorn status. Claiming to reinvent the way design and manufacturing teams 3D print metal and continuous carbon fiber parts, the company aims to create the world’s fastest metal 3D printers. Its broad product portfolio already includes an office-friendly metal 3D printing system for low volume production, as well as new mid-volume manufacturing and continuous fiber composite printers, both of which are expected to ship in the fourth quarter of 2020.
With a valuation of $1.5 billion, Desktop Metal is the first major Massachusetts-based 3D printing company to go public. Locally, Desktop Metal competitors include fellow 3D printing technology unicorn Formlabs in Somerville and continuous carbon fiber manufacturing company Markforged in Watertown.
“We are at a major inflection point in the adoption of additive manufacturing, and Desktop Metal is leading the way in this transformation,” said Ric Fulop, Co-founder, Chairman, and CEO of Desktop Metal. “Our solutions are designed for both massive throughput and ease of use, enabling organizations of all sizes to make parts faster, more cost effectively, and with higher levels of complexity and sustainability than ever before. We are energized to make our debut as a publicly traded company and begin our partnership with Trine, which will provide the resources to accelerate our go-to-market efforts and enhance our relentless efforts in R&D.”

Desktop Metal’s Shop System, an additive manufacturing solution targeted at the machine shop market and designed for mid-volume production of customer-ready metal parts. (Image courtesy of Business Wire)
According to Desktop Metal, the deal will generate up to $575 million in gross proceeds, comprised of Trine’s $300 million of cash held in trust, and $275 million from fully committed common stock PIPE (private investment in public equity) at $10.00 per share. The move is expected to provide, what the company considers, an opportunity to build the “first $10 billion additive 2.0 company,” part of an emerging wave of next-generation additive manufacturing (AM) technologies expected to unlock throughput, repeatability and competitive part costs. With solutions featuring key innovations across printers, materials, and software, Desktop Metal anticipates this new trend to pull AM into direct competition with conventional processes used to manufacture $12 trillion in goods every year.
When consulted, 3DPrint.com’s own Executive Editor and Vice President of Consulting at SmarTech Analysis, Joris Peels, considered the deal to be an aggressive valuation when outlined against the current capabilities, technologies, growth and installed base of the firm. Peels explained that at present, he does not think that the transaction is commensurate with revenues or the perceived quality of its offering.
The expert further suggested that “the firm has consistently overstated capabilities. It has also had significant issues with deploying its technology in the field. Competition from firms such as Markforged, HP, and GE will expand the binder jet market considerably, but also offer alternatives to Desktop Metal. New startups such as One Click Metal, Laser Melting Innovations, Aconity3D and ValCUN can also provide alternative solutions. The low-cost metal market is set for rapid growth. These are the types of systems that we could expect in many a machine shop and factory in the years to come. The opportunity is for over 750,000 deployments worldwide, dwarfing the current market. The battle for dominance in this exciting space will yet see more market entrants arrive and we are in the initial stages of a very exciting time.”
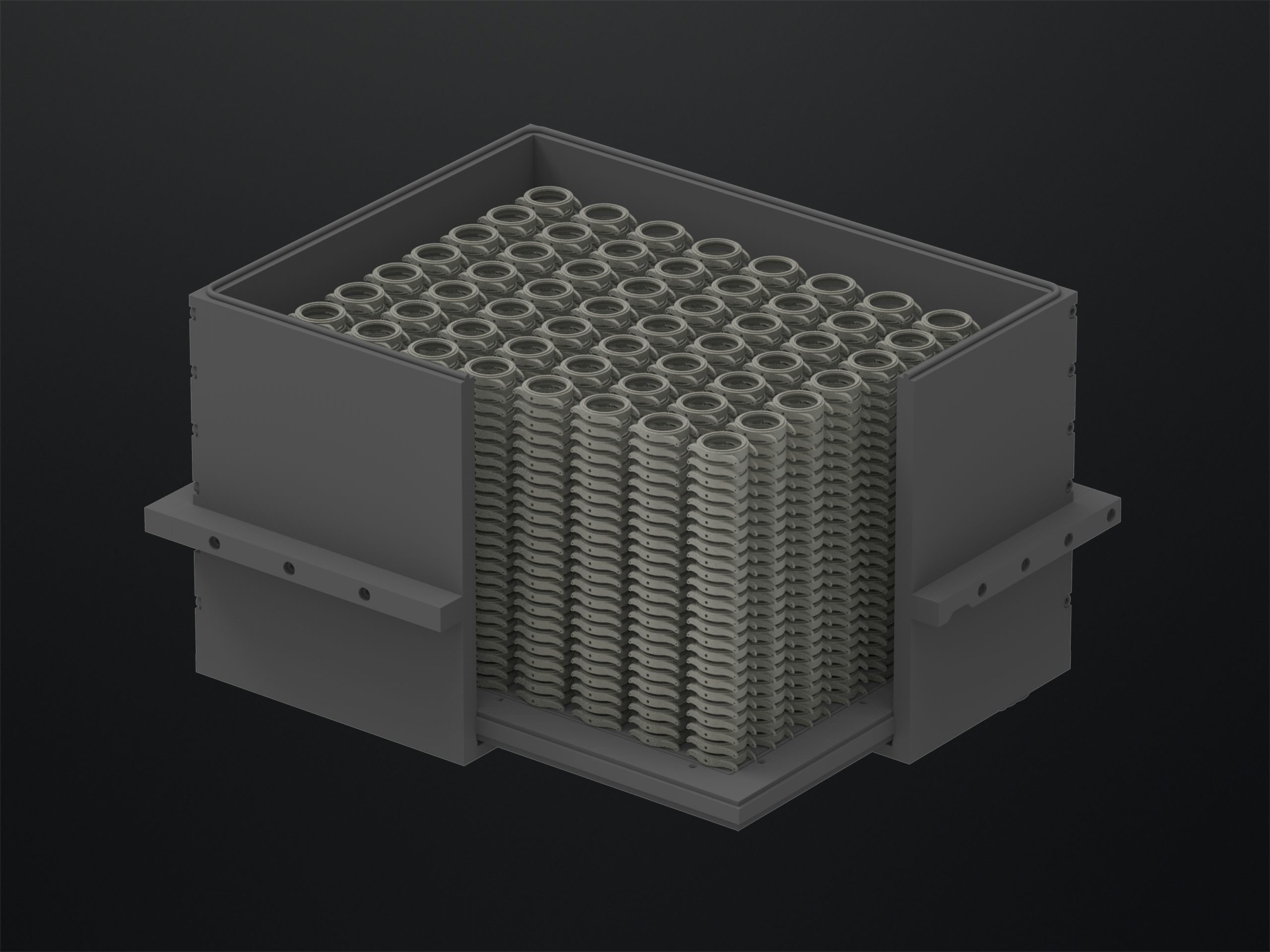
Desktop Metal’s Production System is designed to be the fastest way to 3D print metal parts at scale. (Image courtesy of Business Wire)
During a conference call on August 26, 2020 – just after news of Desktop Metal’s SPAC transaction were revealed – legendary technology investor and operator Leo Hindery, Jr., Chairman and CEO of Trine Acquisitions, said that Desktop Metal will be the “only pure-play opportunity available to public market investors in the additive manufacturing 2.0 space.”
Emphasizing his belief that the company is in the process of revolutionizing the industry, and developing a technology that will be a significant step in replacing mass manufacturing base, which has become antiquated, Hindery said this deal will become pivotal to transforming the products and industries that will drive the economy into the 21st century, including electric vehicles, 5G communications, digital supply chains, and space flight.
Both company CEOs suggested that the AM industry is slated to realize explosive growth over the next decade, reaching over ten times the 2019 market size, estimated to surge from $12 billion to $146 billion by 2030 as it shifts from prototyping to mass production.
To better understand the future of the AM metal industry, 3DPrint.com turned to Scott Dunham, SmarTech’s Vice President of Research, who reported on the market conditions today, stating that nothing changes in business without significant pain first.
“The metal additive manufacturing market in 2020 is feeling a combination of ongoing growing pains with difficulties in the sales environment now intensified due to economic effects from COVID-19. General manufacturing companies facing similar challenges, however, and now are faced with the choice of continuing on with the status quo in light of the pandemic exposing weaknesses in their supply chains, or making serious changes to address those weaknesses in the future. Both choices are fraught with risks,” Dunham suggests. “Metal additive manufacturing market stakeholders are hopeful this scenario may catalyze the industry back to strong growth as companies arrive at a decision to invest in new technologies and further develop their capabilities in concert with AM leaders to arrive better prepared for future challenges.”
Despite the current impasse, Dunham insists that the additive industry will ultimately benefit from a renewed push for cost savings, supply chain independence and agility, and a desire for faster manufacturing. Suggesting that not all will make it through the next two years in metal AM, but those which do will likely build the future of manufacturing that experts have anticipated for some time.
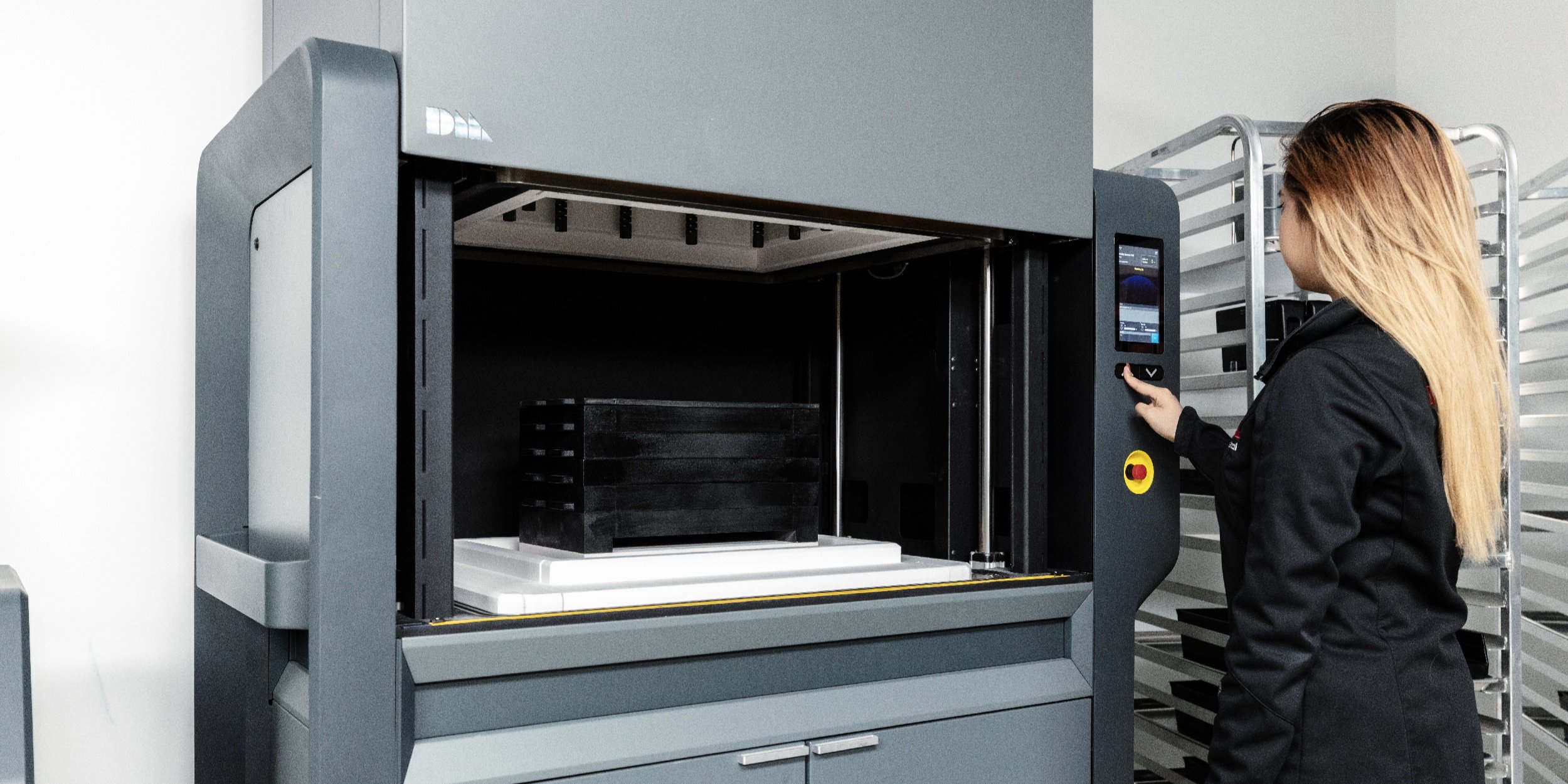
Desktop Metal’s innovative 3D printing metal systems used from prototyping through mass production. (Image courtesy of Desktop Metal)
In a quest to speed up technology development Desktop Metal is moving fast. The proposed business combination is expected to be completed by November 2020 and has already been approved by the boards of directors of the two companies. Once finalized, Desktop Metal will have post-deal cash on hand that will enable accelerated growth and product development efforts, especially as a large portion of the $575 million in gross proceeds from the deal will be dedicated to continuous product innovation and to pursue targeted acquisition opportunities.
The post 3D Printing Unicorn Desktop Metal to Go Public After Reverse Merger Deal appeared first on 3DPrint.com | The Voice of 3D Printing / Additive Manufacturing.