Previously Danish startup Addifab had announced that it was working with its investor Mitsubishi Chemical to develop and offer more materials for its Free Form Injection Molding process, which combines injection molding with 3D printing. Now, Mitsubishi Chemical will be offering FIM as a service.
With Addifab’s process, molds are 3D printed out of photopolymer resin and then cured. This mold is then filled and later dissolved similar to lost wax casting. Because it uses molding, Addifab makes it possible to perform short-run manufacturing with many more materials than are possible with just 3D printing. Start-up costs are lower than actual molding and the lead times are faster, as well. Especially if you work with materials in conventional molding that you just can’t get in 3D printing, Addifab would be a boon. At higher volumes, conventional molding would be more advantageous, of course, and 3D printing would be possible in a lot of geometries where Addifab would not be. Like other technologies such as RIM (reaction injection molding), Thermoforming, thermoplastic injection, and cast Urethane, Addifab provides an alternative for runs between 1 and 10,000 parts.
Mistubishi Chemical will begin by offering FIM services at three locations worldwide: Mesa, Arizona; Tielt, Belgium; and in Tokyo, Japan. The Japanese chemicals giant will offer FIM as a service in Arizona in early Q3 and somewhere toward the end of the year at the other locations.
Randy White, Chief Innovations Officer, Mitsubishi Chemical Advanced Materials, said of the partnership:
“Mitsubishi Chemical Advanced Materials is leading the field of metal replacement polymers. We quickly realized that Freeform Injection Molding would allow us to offer entirely new levels of light-weighting, and we have been working with AddiFab to bring our KyronMAX materials onto the FIM platform. When we were able to drive an 8,000-pound pick-up truck onto a KyronMAX lattice weighing only 70 grams, we knew we were onto something”.
AddiFab CEO Lasse Staal noted:
“We have brought 3D-printing lead-times and start-up costs to the injection molding industry, without compromising on the choice of materials”.

An Addifab mold and the resulting ABS part.
The company is primarily targeting this replacement service at the capital goods industry. It seems to have identified a need and market for machine tool makers, process equipment vendors, and the machinery industry for just the types of parts that Addifab can make. Spare parts have always been a huge imagined opportunity in 3D printing, much funded by the EU in particular.
It is very nice to see a company target this market commercially. Consumables and spare parts are a huge market in the industrial sector. The replacement parts market is not transparent or indeed really global. Often logistics or warehousing unpopular parts is a huge cost element and the combination of Addifab and Mitsubishi Chemical Advanced Materials could bring real change to such a market. Spare parts, consumables, and replacement materials on demand could be a very interesting business model. For now, in certain geographies for certain parts, it could make sense.
If designers and engineers take replacement through Addifab into account during the design stages, then things could really get interesting. Firms would have less of an outlay in certain parts initially. Less upfront investment in part development may improve cashflow in some cases or at some times. Firms would still have to make sure that they wouldn’t overpay in parts, however. An entirely or partially outsourced, or flexible, replacement parts service would be a considerable advantage to many firms. Companies would have much less capital tied up in spare parts. It would also be easier for them to develop specialized and niche versions of existing products, while still being able to support them.
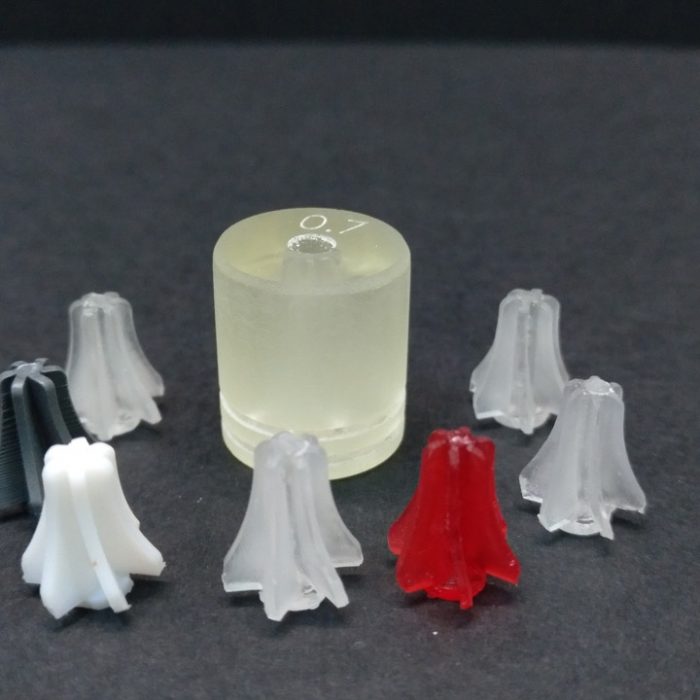
PMMA, PBT and ABS Addifab parts.
Will the new service only work with OEMs? That could be the case, but if it does not, then we may see other firms get into the spare parts business. By making it relatively straightforward to make spares and by democratizing molded parts, it could be easier for service companies, for example, to get into the spares business. If I already service trucks in Indonesia, I could now offer less expensive spare parts for those trucks to my existing customers. Likewise, someone could offer much less expensive spares in the Chilean bus market or for the industrial machinery of one particular company. Capital goods and industrial B2B markets are considerable in revenue and value, but do not often experience the glare of the media or of new disruptive technologies. Overall, this seems to be a particularly timely and well-chosen market entry into a high volume opportunity of many parts.
Generally, we can see chemical and polymer companies increasingly toy with the idea of moving from selling chemicals and polymers to parts. Victrex, for example, has moved towards a service model whereby, for some medical parts, it sells the components themselves and not resin. While still staying in the PEEK business, Victrex’s Invibio unit moves up the food chain and is now helping people develop and get approval for medical devices made out of PEEK.
Is this a similar move by Mitsubishi? In some ways it is, but, rather than carve out a niche that it won’t let others into, the Japanese company has extended its offering into more parts as a service. Such an approach would seem to make a lot of sense. There are much higher margins to be found in parts and one can work more on developing a, by its very nature more strategic, relationship with customers. By moving away from bulk and even specialty chemicals toward parts, polymer and chemical companies could be doing their bottom lines a whole world of good.
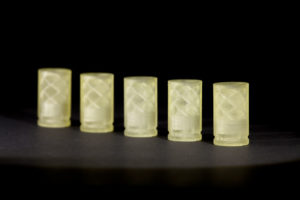
The Addifab Printed Molds
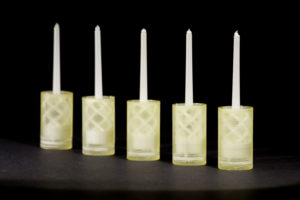
Molds Being injected.
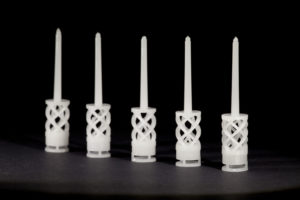
Finished Parts.
There is risk: perhaps existing customers could feel alienated because their supplier now competes with them? This has happened before in 3D printing, for example, with OEMs who have started services. If their existing business was adjacent, then such a move could lead to a decline in some revenues that hopefully would be compensated by parts revenue. If Mitsubishi has been careful to avoid that issue, then their move of helping a company it has invested in with entering the global service business through making parts out of Mitsubishi polymers seems like a very solid play aimed at a more end product oriented future.
The post Freeform Injection Molding Service by Mitsubishi Chemical Advanced Materials appeared first on 3DPrint.com | The Voice of 3D Printing / Additive Manufacturing.