3D Printing and COVID-19, April 3, 2020 Update
Companies, organizations and individuals continue to attempt to lend support to the COVID-19 pandemic supply effort. We will be providing regular updates about these initiatives where necessary in an attempt to ensure that the 3D printing community is aware of what is being done, what can be done and what shouldn’t be done to provide coronavirus aid.
Anesthesiology residents from Massachusetts General Hospital in Boston are now hosting the CoVent-19 Challenge on GrabCAD, where the community can submit designs for rapidly deployable ventilator systems. The challenge will last two months starting April 1, with finalists chosen to work with Stratasys to realize their designs as functional prototypes for testing. After four weeks, 20 finalists will be chosen before another four weeks are dedicated to developing and testing functional prototypes with the help of private and public sector representatives knowledgeable about the regulatory measures and safety testing associated with these medical devices. Three top finalists will win $10,000 in credits Stratasys Direct Manufacturing.
Now that Medtronic has opened up the design files for its PB560 system, there may be a possibility that these designs will be functional and safe. Unfortunately, two months is a long time for people currently in dire need of ventilators, so hopefully alternatives to the CoVent-19 Challenge can be found instead. Perhaps most logically and importantly would be the increase in production of ventilators by manufacturers, possibly in response to government mandate.
In the Czech Republic—the site of a major theft of 680,000 face masks shipping from China to Italy, possibly with state involvement—auto manufacturer ŠKODA is using its Multi Jet Fusion (MJF) systems to 3D print respirators for medical staff. The devices were designed by the Czech Institute of Informatics, Robotics and Cybernetics (CIIRC) at the Czech Technical University and certified according to EN 140:1999 standards for use within a week.
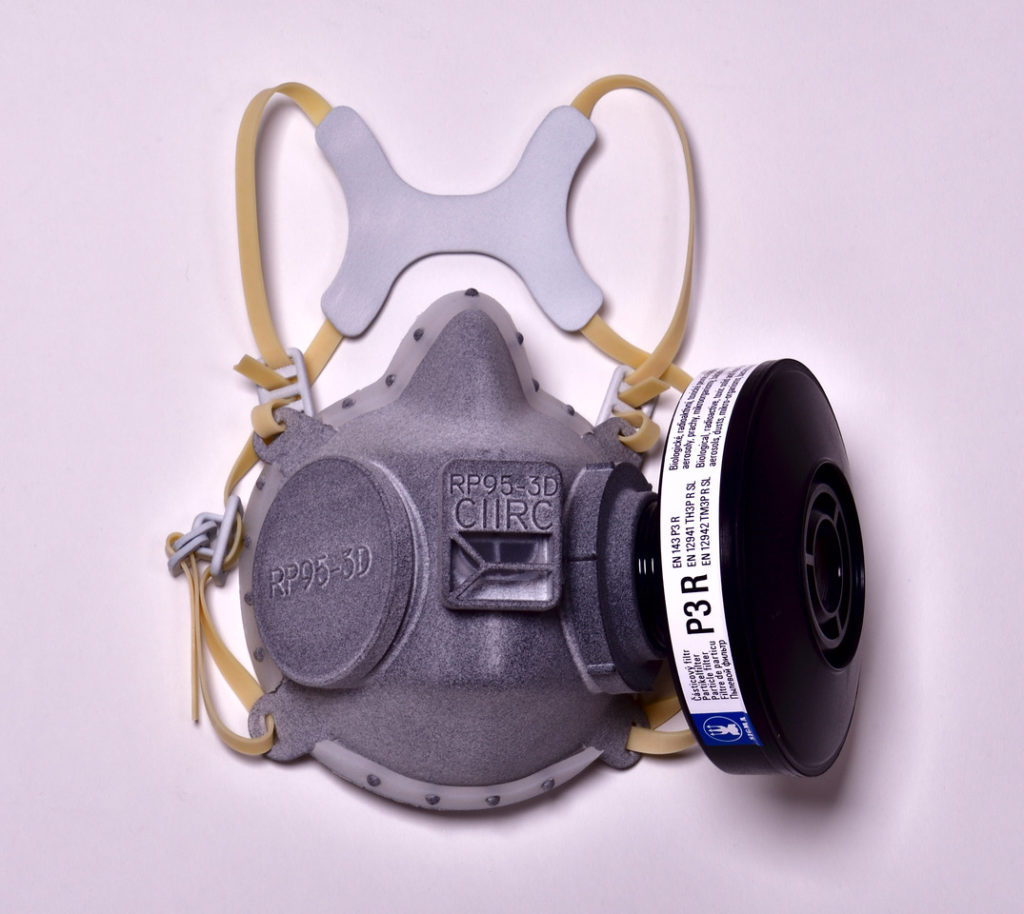
Respirator masks printed by ŠKODA and certified according to EN 140:1999 standards. Image courtesy of ŠKODA.
The CIIRC RP95-3D is made up of a mask, seal caps, an adapter for a P3 filter cartridge attachment and exhalation covers. It is designed to be reused and sterilized in a steam sterilizer, as well as disinfected with a spray solution made of 85 percent ethanol. The filter is meant to last up to a week. MJF was used to ensure minimal porosity and layer lines in order to maximize disinfection.
After first testing the printing of five masks and certifying the production of the device, ŠKODA is now able to produce 60 respirators per day, with 16 hours to print and 16 hours to cool. Once made by the auto company, Czech print shop 3Dees is assembling them and sending them to the Ministry of Health, which will distribute them. Whereas injection molding will ultimately be used for production, 3D printing is a stopgap while molds are developed and made. In the interim, companies with Jet Fusion 4200 and 5200 series systems are invited to access the CIIRC web portal.
The certification of the device is key. The fact that the CIIRC RP95-3D respirator is said to offer the same degree of protection as an FFP3 class respirator or higher, as certified according to specific medical device standards, means that this could be a valid replacement for traditionally made respirators.
The same cannot be said of some well-meaning filter systems being developed by individuals in Hong Kong. Makers in the region have developed 3D printable filter adapters for use on standard 3M half masks. Teacher Carlos Tchiang, for instance, has developed several iterations of an adapter to attach aerosol droplet filters to 3M HF52, 6200 and 7502 masks. Similarly, Neo Chan, the director of a video production team called Mirai Productions, has redesigned his own 3D printable filter adapter shown in the video below.
That isn’t to say that Makers don’t have their role to play in creating items in response to the pandemic, but that there are safer ways of participating. Devices for medical staff should be made in conjunction with medical professionals, possibly through existing initiatives, such as #GetUsPPE in the U.S. Those devices should either be certified by regulatory bodies or of the variety that don’t require as strict safety standards, such as face shields and distancing devices. One example is a face shield that has been approved by the National Institute of Health in the U.S.
Otherwise, Makers and businesses that don’t want to get into risky medical device production can work on items for the general public. Anisoprint, which manufactures fiber reinforcement 3D printing technology, is instead lending its hand to manufacturers impacted by the supply chain disruption resulting from the pandemic. The Russian-Luxembourg company will 3D print composite or plastic parts for businesses facing supply chain issues for free by emailing them at info@anisoprint.com.
The post 3D Printing and COVID-19, April 3, 2020 Update appeared first on 3DPrint.com | The Voice of 3D Printing / Additive Manufacturing.
3D Printing for COVID-19, Part Four: Corporate Partners
As small 3D printing businesses and individual users jump at a chance to support efforts to manufacture critically needed medical supplies, larger corporations also see opportunities to lend aid. Among the names involved are HP, Airbus, and Ford.
Emergency Bagger and Splitter
A consortium of Spanish companies has developed an emergency bag valve mask featuring 3D-printed components. Called the Leitat 1, the device is meant to be both simple and robust. Unlike a ventilator, the Leitat 1 is designed more for immediate emergency usage and not long-term use. The design was created by Leitat Technological Center, a private technical institute, and validated by the director of innovation at Hospital Parc Taulí. Airbus, Navantia and HP aim to aid in the production of the device, with manufacturing of 50 to 100 units sought to be established by next week.
Leitat has since gone on to develop a 3D printable splitter (similar to the part discussed in our previous post) that allows multiple patients to use a single respirator. started yesterday the production of a 3D printed splitter that will allow multiple patients affected by the Coronavirus syndrome COIVD-19 to access a single respirator. The company is relying on HP’s multi jet fusion technology with the idea that it might be possible to 3D print 17 parts in a single print job. A number of companies have already begun producing the parts.
Hospital de la Vall d´Hebron and the Consorci Sanitari de Terrassa in Spain are in the process of validating the splitter and ensuring an effective protocol is in place for their implementation. A first round of 200 devices is in the process of being delivered and 1,000 pieces are expected to be produced by next week.
Protective Gear 3D Printed by Ford
Ford Motor Company has partnered with 3M and GE Healthcare in an attempt to scale up its production capabilities for medical equipment and supplies using its in-house AM systems at its Advanced Manufacturing Center in Michigan. The company hopes to manufacture and assemble 100,000 face shields per week, which can complement N95 masks for further protection of medical staff. The first 1,000 shields are being tested this week at Detroit Mercy, Henry Ford Health Systems and Detroit Medical Center Sinai-Grace hospitals.
With 3M, Ford is adapting its existing off-the-shelf components, such as fans from its F-150 vehicle, to work with 3M HEPA filters in order to improve airflow and filter airborne droplets for 3M’s powered air-purifying respirators (PAPRs). The car company is also looking at how to manufacture these PAPR designs at its facilities in Michigan. GE Healthcare is working with Ford to produce simplified versions of GE’s ventilators, potentially manufacturing them at Ford’s own facilities and at a GE site.
Protective Gear 3D Printed by HP
HP has claimed that it is 3D printing critical parts for medical staff, including respirator parts, face masks and shields, mask adjusters, nasal swabs and hands-free door openers. The initial applications are in the validation stages and are now being finalized for mass production; however, HP has already produced over 1,000 parts to hospitals from its research centers in Spain, Oregon, California and Washington. The company is currently discussing with governments, health agencies and industry to determine the possibilities of working together to get these items to medical staff.
Devices being finalized for manufacturing include a hands-free door opener that has been designed by HP partner Materialise, which makes it possible for people to open doors without touching possibly contaminated handles; a mask adjuster that allows staff to improve the comfort of their masks; and brackets for attaching plastic face shields.
Other items that are in the testing face include the Leitat bag valve mask described above and FFP3 face masks. The files will be made available for download and production. Requests and suggestions can also be made directly to HP.
Specialty Test Swabs and Masks from Carbon and Alphabet (Google)
According to the company, Carbon has redirected all of its business operations in California to addressing the COVID-19 outbreak. Working with Verily, the Alphabet-owned company developing the COVID-19 online screening software Project Baseline, the startup has developed a face shield that is already being tested at Stanford Hospital and with Kaiser Permanente.
Carbon also claims to be discussing the use of its technology to 3D print test swabs with adidas, Mayo Clinic and ASU. The test swabs would feature a lattice structure to increase their testing capacity. This project is being performed alongside Stanford Medical Center, Harvard Medical School/Beth Israel Deaconess Medical Center, Desktop Metal’s Ric Fulop, Chan Zuckerberg BioHub and University of North Carolina at Chapel Hill.
In response to interruptions to business operations during the outbreak, Carbon is also allowing for a payment extension for its customers with fewer than 250 employees.
As helpful as any of these parties may wish to be, it is difficult to determine the line between marketing exploit and genuinely altruistic endeavor. Though it feels like there’s no need for elaboration on this point, it’s necessary to underscore the fact that we regularly witness large corporations take advantage of genuine public concerns and health crises to portray those businesses as good samaritans. The sheer number of businesses “stepping up” might reflect that there is some marketing at work here, in spite of any good attentions. We may even be hitting a point at which nearly all 3D printing companies feel pressured or obligated to participate in COVID-19 efforts based on the general zeitgeist of the industry.
Regardless of the intent behind such efforts, it is worth noting that larger institutions have the ability and resources to potentially contribute and actually meet the regulatory requirements of the medical system. Carbon, HP, and Materialise, for instance, have already been working with medical companies to produce sterile parts. The general clout that big businesses have will also get their efforts placed in front of the proper government agencies and regulatory bodies to ensure the safety of their printed devices, whereas small firms may not have the same advantages.
As a doctor pointed out in our last post, it may be necessary for anyone who can contribute to the pandemic to do so, regardless of a company’s motivation. With that in mind, as long as 3D-printed parts are safe and effectively deployed, their efforts may be desirable in this time of need.
The post 3D Printing for COVID-19, Part Four: Corporate Partners appeared first on 3DPrint.com | The Voice of 3D Printing / Additive Manufacturing.
Airbus Subsidiary Uses Full-Color Multi Jet Fusion for Maintenance Tooling
Among the most exciting aspects of HP’s Multi Jet Fusion (MJF) technology when initially unveiled was the ability to 3D print functional objects in a full range of color. Though it took a couple of years for it to happen, that capability finally hit the market in 2018 with the release of the HP Jet Fusion 300/500 Color 3D Printer range. Now we are beginning to see the applications that a broad spectrum of hues has in practice. Airbus services company Satair used the technology to 3D print a series of tools for its maintenance operations.
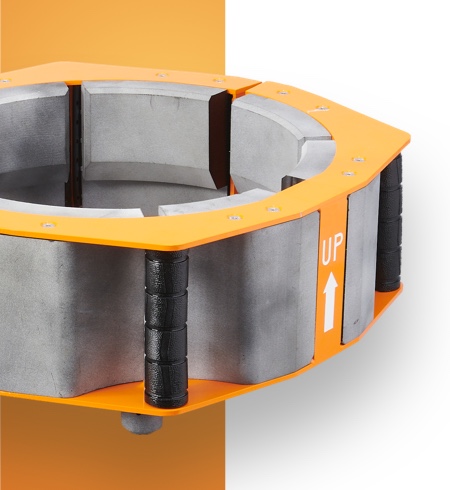
Used to gag the main landing gears on the A380, the GAGS tool pads were redesigned to improve the strength-to-weight ratio, resulting in 60 percent mass reduction. Image courtesy of HP.
Satair turned to service bureau Fast Radius with the ultimate goal of to speed up aircraft repair with the use of 3D printed tools. As a member of HP’s Digital Manufacturing Network, Fast Radius leveraged MJF to print tools for the company. In particular, the color printing capabilities of the Jet Fusion 580 Color system were utilized to 3D print bright red and orange tools in order to improve job safety and ensure that tools were not misplaced after use. The tools were also optimized to reduce total part count, enhance robustness and integrate new functions.
One particularly unique feature about the company is the fact it has a production hub on-site at the UPS Worldport facility in Louisville, Kentucky, allowing it to potentially ship parts at greater speeds than other service providers.
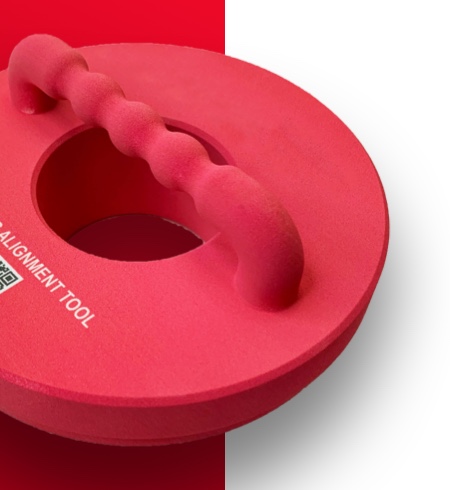
This pintle bearing alignment tool is used to bear in the rear spar prior to installing it during the installation of the main landing gear installation. Assembly was reduced from four parts to two. Image courtesy of HP.
Three new tools were redesigned and printed by HP and Fast Radius for Satair: GAGS tool pads, pintle bearing alignment tools, and flap zero locking tools. MJF was chosen in part for the ability to 3D print durable parts with the mechanical properties necessary for harsh aircraft repair environments. Specifically, HP 3D High Reusability PA 12 was chosen due to its chemical resistance to oils, grease, aliphatic hydrocarbons and alkalies.
3D printing the parts also sped up design time, as multiple iterations could be produced at once within a single build. The use of color also allowed for the communication of information in unique ways, such as 3D printing part numbers, serial numbers and scannable QR codes directly onto the tool.
Whereas Satair previously waited weeks for new tools to be manufactured, this project saw Fast Radius print, inspect, package and ship two tools in less than 48 hours. This was enabled in part by Fast Radius’s logistics partnership with UPS, with which it sent the items from Chicago to Hamburg, Germany.
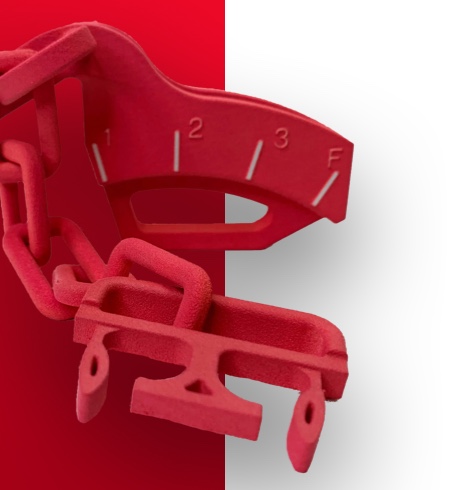
This flap zero locking tool is used to lock flaps in the A320 cockpit. The assembly was reduced from six parts to two and resulted in a lead time reduction of 50 percent. Image courtesy of HP.
The use of 3D printing by Satair is just another notch in Airbus’s belt, as the aerospace giant deploys AM all across its business to the point that it is probably not necessary to recount all of the ways it is being used, but we can highlight the myriad parts printed for the A350 XWB, as well as the work of Premium AEROTEC and APWorks.
As for Fast Radius, this is another interesting customer from the service bureau, which is fond of emerging AM technologies. For instance, the company also used Carbon’s Digital Light Synthesis to print parts for Steelcase’s office chair. Outside of 3D printing, Fast Radius offers a number of other manufacturing services, including CNC machining and injection molding. With the Fast Radius Virtual Warehouse, the company is hoping to implement the concept of digital inventory, in which digital files replace physical stock, with goods manufactured on-demand.
As with 3D printing itself, it will take some time for designers and engineers to fully grasp the potential of producing parts in full color. The ability to use bright pigments for safety purposes and to embed QR codes is just the beginning. HP previously demonstrated the use of colors to exhibit the level of wear on a part, so that, as it is worn down, it shows new colors that can be more easily quantified. Augmented reality applications could also be developed based on embedded symbols in a part. In the near future, we may see even more interesting uses of full color printing of end parts.
The post Airbus Subsidiary Uses Full-Color Multi Jet Fusion for Maintenance Tooling appeared first on 3DPrint.com | The Voice of 3D Printing / Additive Manufacturing.
HP’s MJF Shaves Seconds off CUPRA’s Leon Competición Racer
Given its unique ability to produce small numbers of specialty components quickly and cost-effectively, it’s no surprise that 3D printing is being increasingly applied to the world of motorsports. The latest user is CUPRA Racing, the motorsports division of Volkswagen Group’s Spanish subsidiary, SEAT. To design, test and produce parts for its new Leon Competición, CUPRA relied on the Jet Fusion 5200 from HP.
To speed up the development of the CUPRA Leon Competición, the racer version of the new 2020 SEAT Leon, the design team turned to 3D printing. This made it possible to rapidly iterate and test new features, which was particularly important as the development of the racer and its production equivalent occur simultaneously. Therefore, any changes that were made during the design of the production Leon could be implemented in the Competición version. Parts printed by the team included the steering wheel’s center control module, the bonnet air vents, door mirrors and the brake and water-cooling inlets.
Racers have a variety of specifications that differ from traditional street vehicles. In the case of the TCR International Series of races, however, the door mirror actually must have the same shape as the production version of the car. The CUPRA team maintained the shape of the structure but added great functionality by incorporating an air intake that had the benefit of cooling the driver.

A component for the Leon Competición 3D printed using HP’s Multi Jet Fusion technology. Image courtesy of CUPRA.
Within the wind tunnel, the 3D printed parts were verified to ensure that they would perform with the same effectiveness as traditionally manufactured components. Testing was then carried to the track before the official release of the car on February 20, 2020, which coincides with the inauguration of the CUPRA Garage, the new headquarters of the racing brand.
The Leon Competición will hit the racing circuit on the Portimao track in Portugal, where the true quality of the 3D printed parts will be put to the test. Meanwhile, customers interested in purchasing the racer can be pre-booked, a first for touring race cars (heavily modified road cars). A batch of 10 units has been made available for pre-order and will be delivered at the CUPRA Garage in Barcelona, Spain in April 2020.
While 3D printing may be new to CUPRA, AM has been a standard feature of motorsports for some time. Other instances include McLaren’s use of Stratasys technology for track-side printing, Nissan’s implementation of 3D printing for prototypes and end parts, and Team Penske’s use of Stratasys’ new carbon fiber filament 3D printer for producing jigs, fixtures and prototypes. A long series of Formula 1 teams rely on AM, such as Ferrari, Alfa Romeo, and Sauber. Numerous student teams have relied on 3D printing for their own motorsports projects, as well.
Perhaps one of the more interesting examples is BMW’s use of metal 3D printing to water pump wheels for its German Touring Car Masters (DTM) vehicles. BMW began 3D printing this part using laser powder bed fusion back in 2010, replacing a multi-piece plastic assembly with a single-unit metal unit. As of 2015, BMW had 3D printed 500 water pump wheels for its DTM race cars and Z4 GT3 customer vehicles.
In fact, for a company as new to AM as HP, motorsports aren’t even all that new. An Aussie race team called Triple Eight announced its use of Multi Jet Fusion earlier this month.
The application of AM in racing is a natural one, given the high cost these high-performance parts would generate if made using conventional manufacturing methods. And, as the CUPRA team learned, 3D printing is capable of the rapid iteration necessary for designs in which every minor improvement could shave milliseconds off of the finish time. So, when it comes to motorsports, the question isn’t who is using 3D printing. It’s who isn’t?
The post HP’s MJF Shaves Seconds off CUPRA’s Leon Competición Racer appeared first on 3DPrint.com | The Voice of 3D Printing / Additive Manufacturing.
Triple Eight Race Engineering customizes race wheel with HP MJF 3D printing
Q&A: Cheryl MacLeod, Global Head of 3D Fusion Science and Materials Expansion at HP
Top Questions Answered: Multi Jet Fusion Plastic PA12
As part of our month-long feature on Multi Jet Fusion Plastic PA12, we’ve asked you, our readers, to submit your questions about this material. Here are the top questions and answers to help you better understand the properties and applications of MJF PA12.
Top Questions Asked
Q. Is PA12 certified non-allergenic?
A. Yes, here is a certification for biocompatability for skin-contact applications, such as jewelry.
Q. Do you have any colored MFJ materials available?
A. Colors for MJF is not in our near-term roadmap, but we will consider this for the future.
Q. I’m curious about the price of printing in this material.
A. Please upload a model through our model upload page, select Multi Jet Fusion Plastic and your desired color and finishing to see the price for your model; or reach out to our sales team and we would be happy to help!
Q. What type of glue is recommended for use with this material?
A. An off-the-shelf epoxy material will work well.
Q. My product has a moveable part. Is PA12 a good material that can withstand constant bending of this moveable part without breakage?
A. PA12 is a good option. PA11 also has great elasticity and may have slightly better long-term wear properties.
More from the Material of the Month Series: PA12
Part One: Material Overview
Part Two: Material Comparison: Nylon Plastics
Part Three: Business Example: PA12 used in the virtual reality industry
Part Four: Tutorial: Post processing PA12
The post Top Questions Answered: Multi Jet Fusion Plastic PA12 appeared first on Shapeways Magazine.
How to Paint 3D Printed Eyeglass Frames Your Favorite Color
If you want to learn how to add finishing touches to your products post-production before shipping to your customers or transform your own 3D printed designs to a more vivacious color you can do so by following a few simple steps. In this tutorial, Steven and Jeremy Gonzalez of The Super Maker Bros demonstrate how to paint eyeglass frames printed in Multi Jet Fusion Plastic PA12 in multiple colors, a process that can be applied to many other projects of the same 3D printed material.

3D printed eyeglass frames in MJF PA12, 220/400/600 grit sandpaper (Photo by The Super Maker Bros)
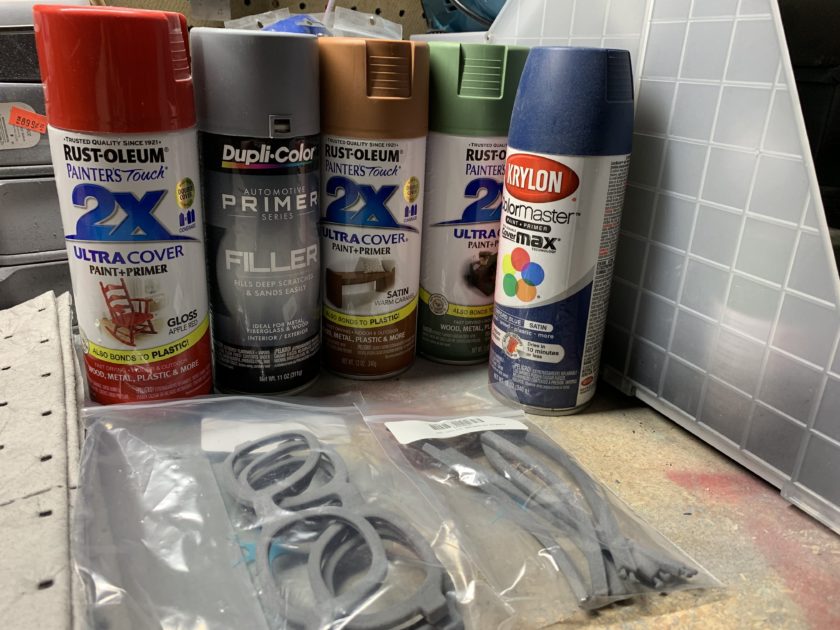
Primers and paints (Photo by The Super Maker Bros)
Here is what you will need:
- 3D model printed in Multi Jet Fusion Plastic PA12 (also applicable for Versatile Plastic)
- 220 grit, 400 grit and 600 grit sandpaper
- Spray paint primer
- Spray paint in your desired color(s)
- Clear coat matte or gloss spray paint
- Reusable drop cloths or newspaper to protect your work area from paint
- Highly Recommended: A respirator with replaceable filters will not only protect you from spray paint fumes but will last you through many more future paint projects.
Once you have these materials you are ready to get started. Follow the steps below and check out this video to see each step in action.
Step 1:
Prepare your workspace by placing newspaper or a drop cloth over the area to cover any furniture or floor space in range of your spray painting pattern. Protect enough space to spray from different angles.
Step 2:
Put on your respirator. Spray paint fumes are toxic and sanding generates dust particles that are dangerous to inhale, so make sure you sand and spray in a well ventilated area and wear your respirator.
Step 3:
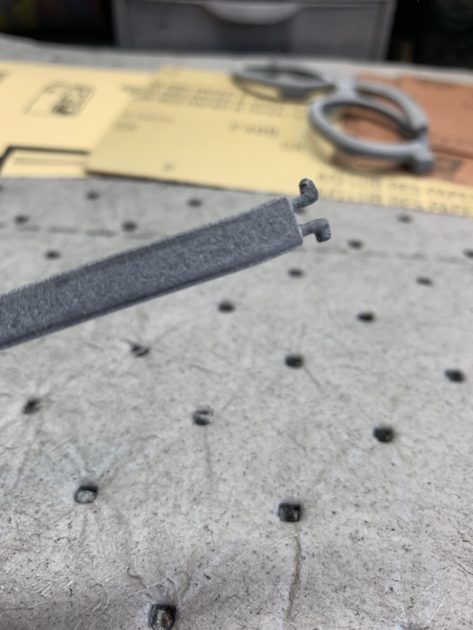
3D printed eyeglass frames, sanded (Photo by The Super Maker Bros)
Start by sanding the glasses pieces to smooth out their surfaces. This will also help the paint adhere to the plastic. Makerbro Tip: The best sandpaper to use is wet/dry or waterproof paper because getting the paper wet helps cool the plastic while sanding as well as keeps small dislodged plastic particles under control. Waterproof sandpaper is black instead of tan or beige.
Begin with a rougher, 220 grit sandpaper to remove any bulky texture and then move on to 400 grit and 600 grit to buff the surface smooth. The lower the number, the rougher the paper is. Be sure to rinse and dry the pieces to remove loose particles.
Makerbro Tip: To give your sandpaper more longevity, apply spray adhesive to the back of your quarter sandpaper sheet and fold it over to make an extra thick one-eighth sheet. This will give you the ability to use more pressure without tearing a hole in the paper.
Step 4:
Prime the frames using a spray primer like the Dupli color filler primer. Spray the glasses using a sweeping motion, keeping the spray can at a distance of about 6 to 12 inches. Spraying too closely will coat the object in too much paint and cause dripping or even cause the coat to crack when dry. Make sure all visible surface area is covered and let the pieces dry before spraying the other side.
Makerbro Tip: Spray paint takes about 30 minutes to dry to touch but wait between 1 to 2 hours to handle it. It will be fully dry after 24 hours.
Step 5:
Once the glasses are primed, sand the surfaces once more using the 600 grit paper to achieve maximum smoothness and wipe away any resulting dust.
Step 6:

3D printed eyeglass frames, painted (Photo by The Super Maker Bros)
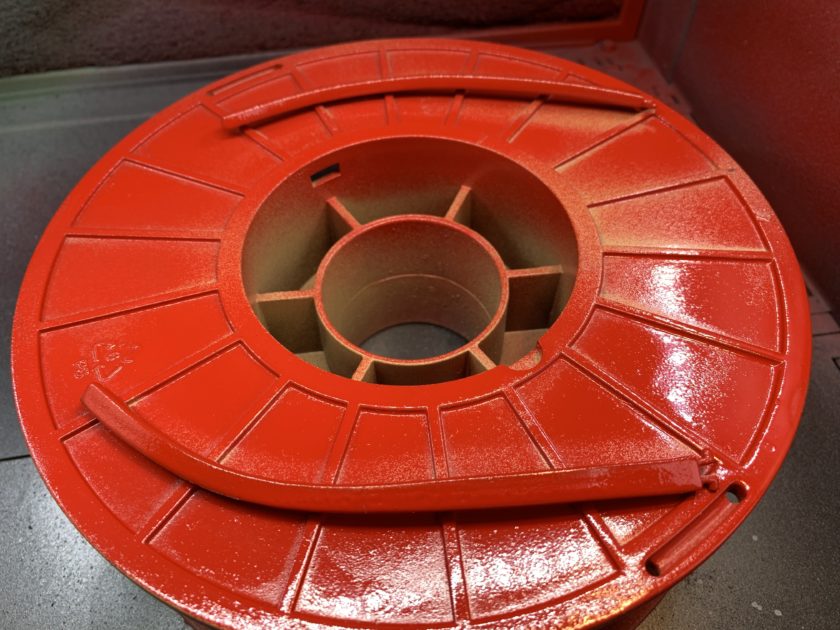
3D printed eyeglass frames, painted (Photo by The Super Maker Bros)
Using the same spray painting method as with the primer, spray each piece in the color of your choice and let fully dry for 24 hours.
Makerbro Tip: Want to use more than one color on the same piece? Use masking tape to cover parts of your project you want in a different color. Once the first color dries, cover that portion and paint the rest.
Step 7:
Once the glasses have had 24 hours to fully dry, it’s time to seal up the paint with a topcoat. Using the same spray painting method, apply two layers of topcoat, leaving 1 to 2 hours of drying time in between. This helps protect the paint and enhances the shine or matte finish desired. It also gives a buffer between paint and skin contact.
Step 8:

3D printed eyeglass frames, painted in blue and brown (Photo by The Super Maker Bros)
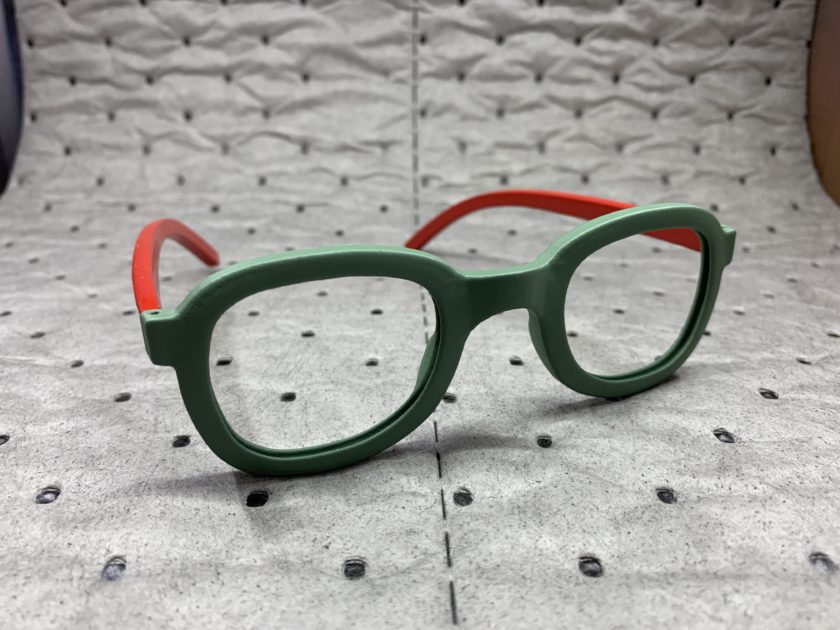
3D printed eyeglass frames, painted in green and red (Photo by The Super Maker Bros)
Now assemble the pieces and you’ve got a brand new pair of glasses! You can have a pair in every color.
Check out The Super Maker Bros on Instagram (where they’ll be posting more photos and videos) and YouTube for more fun 3D printed projects.
More from the Material of the Month Series: PA12
Part One: Material Overview
Part Two: Material Comparison: Nylon Plastics
Part Three: Business Example: PA12 used in the virtual reality industry
The post How to Paint 3D Printed Eyeglass Frames Your Favorite Color appeared first on Shapeways Magazine.
3D Printing Virtual Reality Products in MJF PA12
Experimenting with virtual reality is an exciting — and somewhat unnerving — process. It often requires much trial and error, which is precisely why the team at Spaces needed to find a final stage prototyping process to aid them. That’s where Shapeways stepped in. Spaces loves Shapeways’ dimensional accuracy and durability and has used 3D printing –primarily the Multi Jet Fusion Plastic PA12 material – ever since first discovering the company.
Why is it beneficial to print with Shapeways over traditional manufacturing methods such as injection molding?
Spaces: We are constantly inventing and iterating, most of the time under very tight time constraints. Using 3D printing allowed us to make parts that broke some rules and to make changes to parts quickly. Shapeways helped us create parts that could not be manufactured through conventional injection molding. Undercuts are a major concern with any tooling for injection molding and create a lot of work to get parts made.
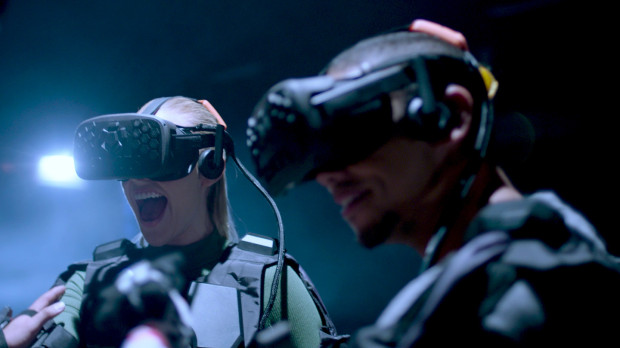
Spaces utilizes 3D printing to build virtual reality experiences. (Photo courtesy of Spaces)
Which is your most used material?
Our most used material is the Multi Jet Fusion Plastic PA12 because it gives us acceptable resolution and is durable.
Why do you print with Shapeways versus desktop 3D printing?
The quality and quantity of the Shapeways parts we print are the main benefit. For the most part, desktop printing does not produce the same quality and resolution. Also, most desktop printers can be unreliable, which is something we cannot take a chance with when printing large quantities of parts for our installations. Most of our parts are conceived using desktop printing methods and then turned over to Shapeways for printing en masse.
What are the added benefits of using Shapeways?
We have been impressed with the customer service. Personal attention is very important when we are working against tight deadlines.
More from the Material of the Month Series: PA12
Part One: Material Overview
Part Two: Material Comparison: Nylon Plastics
Part Three: Business Example: PA12 used in the virtual reality industry
Part Four: Tutorial: Post processing PA12 (coming soon)
The post 3D Printing Virtual Reality Products in MJF PA12 appeared first on Shapeways Magazine.