Nanodiamonds are diamond particles produced by explosions, and are very thermally conductive. Nanodiamond powder is made up of non-toxic diamond nanoparticles, with a large surface, that are about 5 nm in size, and feature some interesting properties.
Researchers Krzysztof Królewski, Aleksandra Wieloszyńska, Aleksandra Kamińska, and Katarzyna Kardacz from Poland’s Gdańsk University of Technology (GUT), wanted to investigate a particular property, and published a paper on their work, titled “Optical properties of daylight curable resin doped with nanodiamond powder.”
The abstract reads, “In this paper a new material for 3D printing was elaborated on. Since diamond has very good optical properties, an idea occurred to us to apply it in a 3D printing process. A mixture of nanodiamond powder and standard 3D printing resin was created and several printouts have been completed. They have been tested for their abilities to transmit and absorb light in a wide spectrum of wavelengths. It turned out that nanopowder doped resin in comparison to standard one has worse optical properties. However, it shows that a mixture of resin and nanopowder can control optical properties of printouts.”
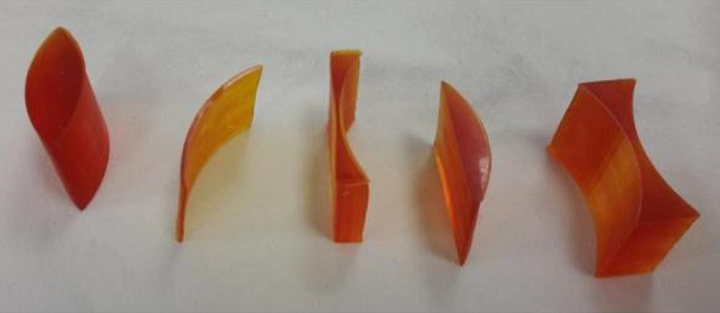
Fig. 1. Prototypes of 3D printed cylindrical lenses. L-R: convexo-convex lens, convexo-concave lens, plano-concave lens, plano-convex lens, and concavo-concave lens.
The team prepared and analyzed a new 3D printing material made out of diamond nanoparticles and amber 3D Daylight Hard resin from Photocentric, which caused unique optical properties. They fabricated a few examples of their material on the Liquid Crystal 10′ 3D printer, and then tested the optical properties, along with the optical properties of the Photocentric polymer resin for comparison.
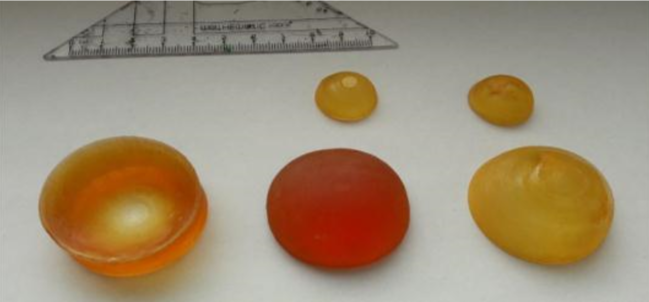
Fig. 2. Prototypes of 3D printed spherical lenses. Bottom L-R: plano-concave lens, plano-convex lens, and convex-concave lens. The top row shows two convex-concave lenses.
“The 20 mm × 20 mm plates were printed as test samples which were prepared with different thickness (0.2 mm, 0.5 mm, 0.8 mm, 1 mm, 1.5 mm, 2 mm and 5 mm),” the researchers explained.
A spectrometer was used to obtain transmission characteristics of the 3D printed sample plates, in the 200-1100 nm wavelength range at room temperature. These characteristics are defined by, as the researchers wrote, “increasing transmission with decreasing the thickness of plates.”
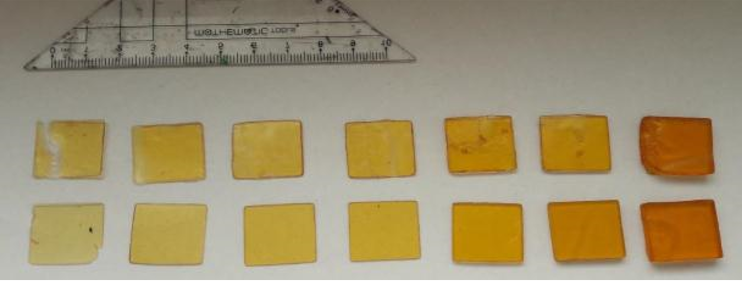
Fig. 3. Two series of flat plates (first series at top and second at the bottom). The thinnest plate is on the left.
For the first series of 3D printed plates, the transmission was almost zero for light waves in the 200-400 nm range, while the greatest transmission was for those in the 800-1100 nm range. The transmission for series #2 was even higher, which was easy to see with thicker plates. These characteristics are comparable with those of other optical materials, such as fused silica, and are definitely appropriate for a number of optical applications.
“In the first series, the maximal transmission is 60% and 44% for 2 mm and 5 mm thick plate, respectively. In turn, in the second series, this value is 75% and 65%, respectively,” the researchers noted.
The team then determined the absorption characteristics for the plates, and found that the greatest absorption is for light waves in the 200-400 nm, due to their orange color; the lowest absorption was for waves in the 600-1100 nm range.
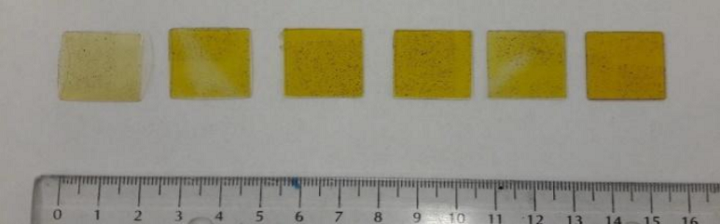
Fig. 8. One series of flat plates, printed from the mixture of resin and nanodiamond powder which was obtained by evaporating DMSO from the suspension with nanodiamond.
More plates were then 3D printed out of the team’s novel material of nanodiamond powder and resin. The researchers then went into a little more detail as to how they obtained, and created, the material.
“The nanodiamond powder was obtained by evaporating DMSO (dimethyl sulfoxide) from the suspension with nanodiamond,” they wrote. “Then the 66.835 g liquid resin was mixed with 0.069 g powder. First, the magnetic stirring was carried out for an hour and after that, the sonication was done for 45 minutes. The sonicator worked in pulse mode with power set at 10%.”
The team used a series of OCT measurements to evaluate the material properties of the 3D printed plates, and got single B-scans from three plates with diamond nanoparticles, and one without, for reference. The images show that because of nanoparticles being present, and “the lack of tendency to agglomeration,” the prepared material was in fact homogeneous.

Fig. 9. OCT image of the plate with nanopowder. There are scattering centers in the sample (bright spots in the image), which indicates the occurrence of diamond nanoparticles.
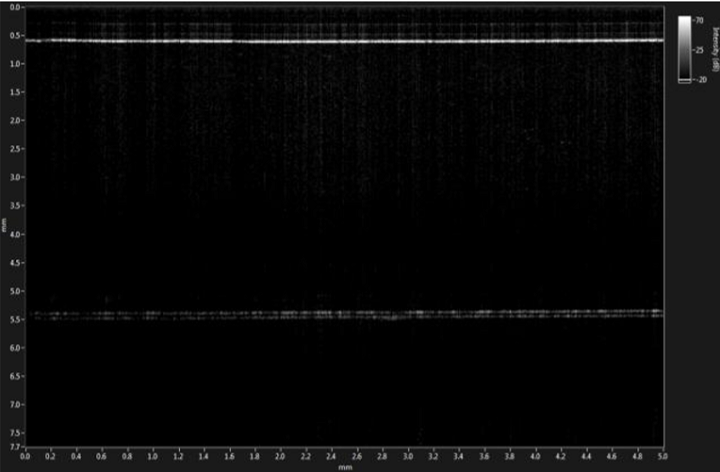
Fig. 10. OCT image of polymer used for printing. Lack of the scattering centers indicates no occurrence of the diamond nanoparticles.
“In this research we have shown that the presence of nanodiamond affects the optical characteristics of the mixture,” the researchers concluded. “It gives premises that other nanoparticles can modify the optical properties, especially absorption characteristics. Therefore, it may lead to new opportunities for a low-cost, quick and easy method for rapid prototyping of optical filters.”
Discuss this story and other 3D printing topics at 3DPrintBoard.com or share your thoughts in the Facebook comments below.
The post New 3D Printing Resin Made with Nanodiamond Powder appeared first on 3DPrint.com | The Voice of 3D Printing / Additive Manufacturing.