According to the United Nations Intergovernmental Panel on Climate Change (IPCC), we have less than ten years to cut greenhouse gas (GHG) emissions by 45 percent to prevent runaway climate change. Some environmentalists argue that even that projection is too optimistic. To prevent the collapse of our ecosystem, some researchers are betting on a technology called carbon capture and storage (CCS). This includes a team at the U.S. Department of Energy’s Oak Ridge National Laboratory (ORNL), which has 3D printed an aluminum device for improving carbon capture at fossil fuel plants and other industrial sites.
While carbon capture can be performed in several different ways, the most common method involves attempting to filter carbon dioxide (CO2) from a smokestack using a solvent, such as monoethanolamine, that separates the GHG from the flue gasses. As the CO2 meets the solvent, heat that is produced can reduce the ability of the solvent to react with the CO2, limiting its efficiency.
ORNL improved the efficiency of this process by creating a device that integrates with a heat exchanger with a mass-exchanging contactor to remove excess heat. The item was tested within a circular device measuring one meter high by eight inches wide and made up of seven stainless-steel packing pieces. Installed in the top half of the column between packing elements, the 3D-printed part allowed for the integration of a heat exchanger. In turn, the group was able to reduce temperatures and, therefore, improve CO2 capture.
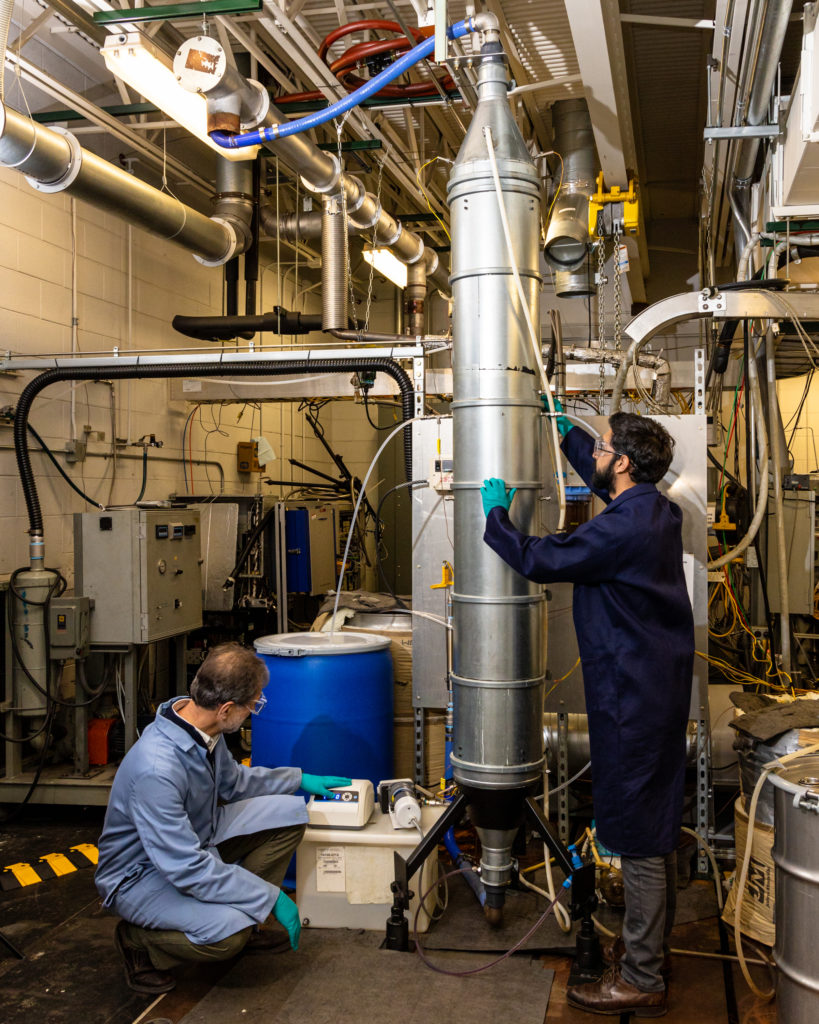
In 2019, ORNL researchers Costas Tsouris and Eduardo Miramontes operated the intensified device inside of the absorption column, which contains commercial stainless-steel packing elements. Credit: Carlos Jones/ORNL, U.S. Dept. of Energy
The project’s Principal Investigator, Xin Sun, explained how such a process was previously unattainable: “Prior to the design of our 3D printed device, it was difficult to implement a heat exchanger concept into the CO2 absorption column because of the complex geometry of the column’s packing elements. With 3D printing, the mass exchanger and heat exchanger can co-exist within a single multifunctional, intensified device.”
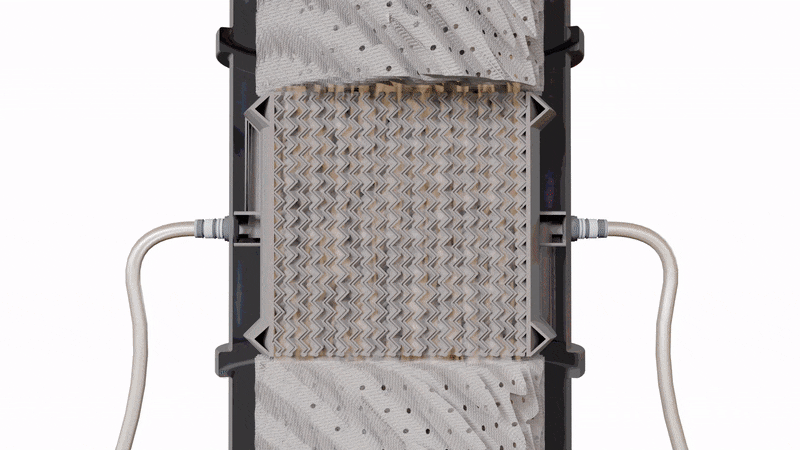
Embedded coolant channels within the intensified device reduce the column temperature due to the heat produced during the forward reaction. Credit: Michelle Lehman/ORNL, U.S. Dept. of Energy.
To enable heat exchange within the column, cooling channels were incorporated into the steel packing elements. The 3D-printed component, referred to as the “intensified device” was printed from aluminum due to its high thermal conductivity, overall structural strength and its printability.
Costas Tsouris, one of ORNL’s lead researchers on the project, said of the item’s name, “We call the device intensified because it enables enhances mass transfer through in-situ cooling. Controlling the temperature of adsorption is critical to capturing CO2.”
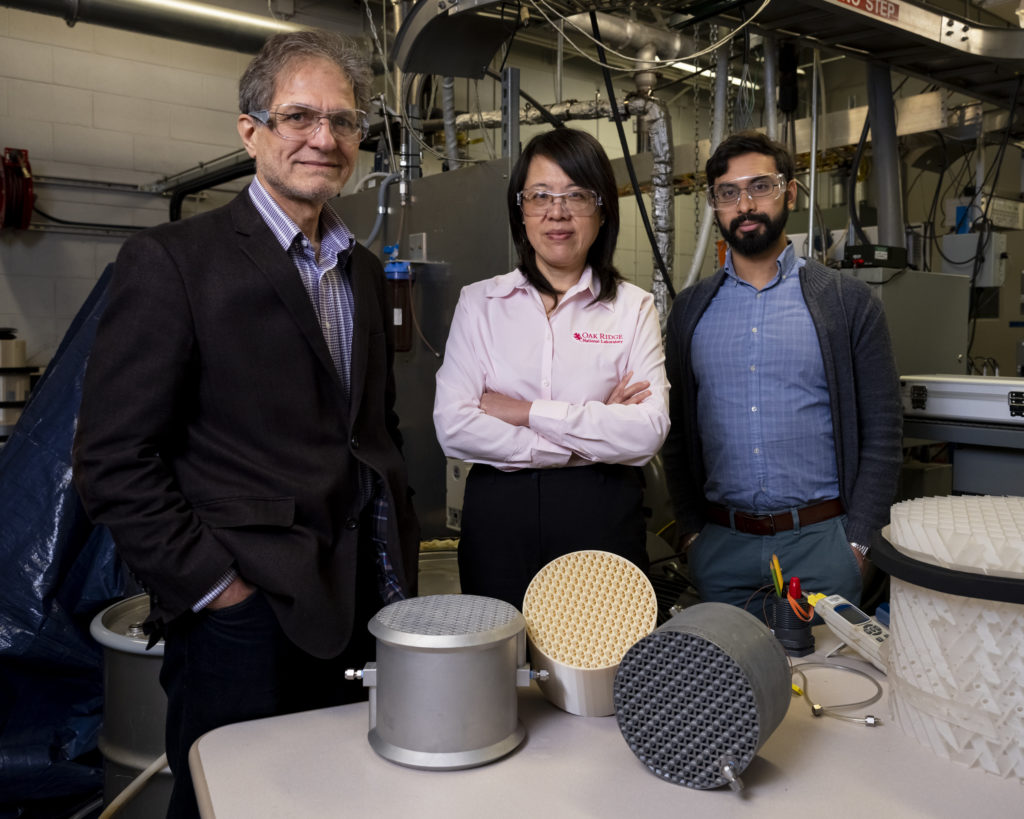
ORNL’s Costas Tsouris, Xin Sun and Eduardo Miramontes, pictured in early March, demonstrated that the 3D-printed intensified device substantially enhanced carbon dioxide capture efficiency. Credit: Carlos Jones/ORNL, U.S. Dept. of Energy.
Lonnie Love, Lead Manufacturing Researcher at ORNL, said that the intensified device was not limited to aluminum:
“The device can also be manufactured using other materials, such as emerging high thermal conductivity polymers and metals. Additive manufacturing methods like 3D printing are often cost-effective over time because it takes less effort and energy to print a part versus traditional manufacturing methods.”
According to some estimates, carbon capture used to reduce emissions from fossil fuel plants could cut CO2 by 55 to 90 percent. However, the bigger issue is not just removing GHGs from the source, but what is done with the material once it’s removed. In the short term, CO2 is already used to extract oil from wells, with the material injected into wells to drive out crude oil. In other words, carbon capture is actively contributing to climate change and the resulting ecological collapse because it is increasing the use of fossil fuels obtained through this enhanced oil recovery.
Long-term storage is another issue. Hypothetically, after CO2 is transported via pipeline as a liquid or gas, it could then be stored underground or underwater in geological formations. Though it may be technically feasible, it has not been tested extensively and we do not know what the side effects of storing excess CO2 underground or underwater. Similar to the short-term problem, this solution disincentivizes fossil fuel dependent civilization from shifting to alternative energy sources because it suggests that fossil fuel use can continue indefinitely if we capture it at the source and store it under the earth with unforeseeable consequences using yet-to-be-developed technologies.
The post ORNL Team 3D Prints Device for Improving Carbon Capture Technology appeared first on 3DPrint.com | The Voice of 3D Printing / Additive Manufacturing.