In today’s 3D Printing News Briefs, DOMO Chemicals and RPD have announced a partnership related to a Sinterline initiative. The 2021 AMPM event is calling for technical papers related to metal additive manufacturing. Finally, Alloyed has won a prestigious award.
DOMO Chemicals and RPD Partnering
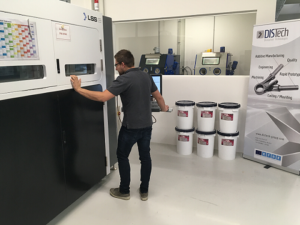
DOMO’s Sinterline PA6 powders combined with RPD’s SLS printer, modified and upgraded by LSS, enable OEMs to step up their 3D printed parts performance. (Photo courtesy of RPD)
Polyamide solutions provider DOMO Chemicals and Rapid Product Development GmbH (RPD), a specialist in prototyping and serial production of complex parts and assemblies, have formed a strategic partnership for the purposes of speeding up the growth of plastic materials for selective laser sintering (SLS) 3D printing. The collaboration will merge the continuing development of DOMO’s Sinterline Technyl PA6 SLS powder materials with a package of support services for SLS technology, benefiting from RPD’s expertise in application development and the SLS process. Sinterline PA6 powders are an oft-used nylon in the industry, especially by demanding markets like automotive.
“Sinterline® has pioneered the use of high-performance PA6 in 3D printing, and allows us to leverage the same polymer base that has proven so successful in many existing injection molding applications. Backed by the joint application development services of our companies, even highly stressed automotive components can now be successfully 3D printed in PA6 to near-series and fully functional quality standards,” stated Wolfgang Kraschitzer, General Manager and Plastics Processing Leader at RPD.
AMPM Conference Seeking Papers and Posters
The Additive Manufacturing with Powder Metallurgy Conference (AMPM2021) will be held in Orlando, Florida from June 20-23, 2021. While this may seem far in the future, the event’s program committee is looking ahead, and has issued a call for technical papers and posters that are focused on new developments in the metal additive manufacturing market. Stuart Jackson, Renishaw, Inc., and Sunder Atre, University of Louisville, the technical program co-chairman, are asking for abstracts that cover any aspect of metal AM, such as sintering, materials, applications, particulate production, post-build operations, and more.
“As the only annual additive manufacturing/3D printing conference focused on metal, the AMPM conferences provide the latest R&D in this thriving technology. The continued growth of the metal AM industry relies on technology transfer of the latest research and development, a pivotal function of AMPM2021,” said James P. Adams, Executive Director and CEO of the Metal Powder Industries Federation.
The submission deadline for abstracts is November 13, 2020, and must be submitted to the co-located PowderMet2021: International Conference on Powder Metallurgy & Particulate Materials.
Alloyed Wins IOP Business Award
UK company Alloyed, formerly OxMet Technologies, has won a prestigious award from the Institute of Physics (IOP), the learned society and professional body for physics. The IOP is committed to working with business based in physics, and its Business Awards recognize the contributions made by physicists in industry. Alloyed has won the IOP Business Start-up Award, which OxMet submitted for consideration before merging with Betatype to form Alloyed, and recognizes the team’s hard work in developing its digital platform Alloys By Design (ABD). This platform is helping to set new metal material development standards, including the commercialization of Alloyed’s ABD-850AM and ABD-900AM alloys for additive manufacturing.
“Everything we do in every bit of our business rests on the foundations provided by physics, and we’re delighted that the judges believe we have made a contribution to the field,” Alloyed CEO Michael Holmes said about winning the IOP Business award.
The post 3D Printing News Briefs, July 18, 2020: DOMO & RPD, AMPM2021, Alloyed appeared first on 3DPrint.com | The Voice of 3D Printing / Additive Manufacturing.