There was much to enjoy and learn at the recent Additive Manufacturing Strategies event, held in Boston and co-hosted by 3DPrint.com and SmarTech Analysis, especially with the addition of a new metals track. There was the ever popular Startup Competition, time to network with colleagues, interesting keynotes, an exhibition hall, industry forecasts by SmarTech, and many different panels and presentations.
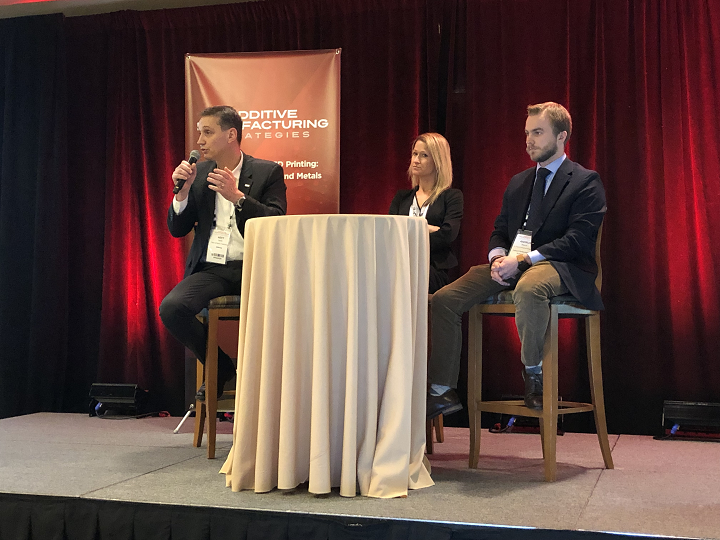
On the first day, I sat in on a panel on the event’s medical track about the use of 3D printing in implants and orthopedics. Martin Neff, the Head of Plastic Freeforming for German machine manufacturing company Arburg, spoke first, and provided attendees with a detailed explanation of its patented ARBURG Plastic Freeforming (APF), the process principle behind it, and what the Freeformer can offer.
“Our process can use standard resin, is already on the market and cleared by the FDA for medical devices, and it’s similar to injection molding,” he explained.
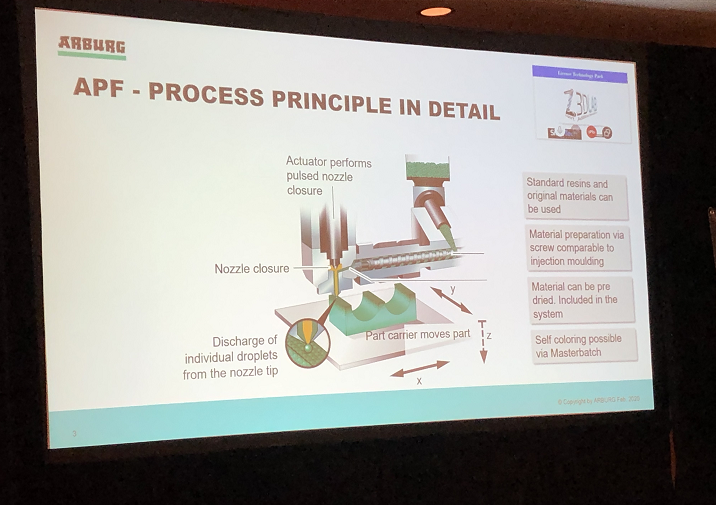
Moving on, Neff said the biggest thing to keep in mind for this application of 3D printed implants and orthopedics is how to achieve repeatability, traceability, and position. Additionally, he mentioned that the selection and freedom of materials in this sector is also a “very important area.”
Carissa Kennison, the Director of Marketing for New Jersey-based Additive Orthopaedics, explained that the company, which was founded in 2016, designs, markets, and manufactures medical implants.
“We’re inspired by the outcomes these 3D printed implants are having in our patients’ lives,” she said. “The patient testimonials are truly inspiring – often, patients go to multiple surgeons and are told to get a fusion, which limits joint motion, or an amputation. So we’re giving them an alternative solution, and challenging the solutions of standard of care. It’s pretty exciting to be a part of that.”
Jean-Jacques Fouchet on Skype
While he was unable to be at AMS 2020 in person, Jean-Jacques Fouchet, the VP Business Development and co-founder of 3D printing company Z3DLAB – Parc Technologique, was able to join the panel via Skype, and explained to attendees that “Z3DLAB is an expert in materials science,” and that it has developed a 3D printed implant for the dental field. The company’s mission is to deliver a new generation of advanced, titanium-based material for the AM market.
“We do two titanium materials, one based on Ti-64 that’s enhanced and one based in Ti-CP,” he explained. “Our 3D printed implant has an interior porous structure.”
Fouchet went on to say that Z3DLAB had completed a study with EnvA, LNE, and BAM, and that after just two months of implementation, “we got high-resolution scanner results that showed 84% bone inside the implant. Not bone tissue, but bone.”

The last panelist was Andrus Maandi, Sr. Product Development Engineer for Oxford Performance Materials (OPM). He explained that OPM was originally founded as a materials science company, working exclusively with PEKK (polyetherketoneketone), and began adopting 3D printing all the way back in 2008.
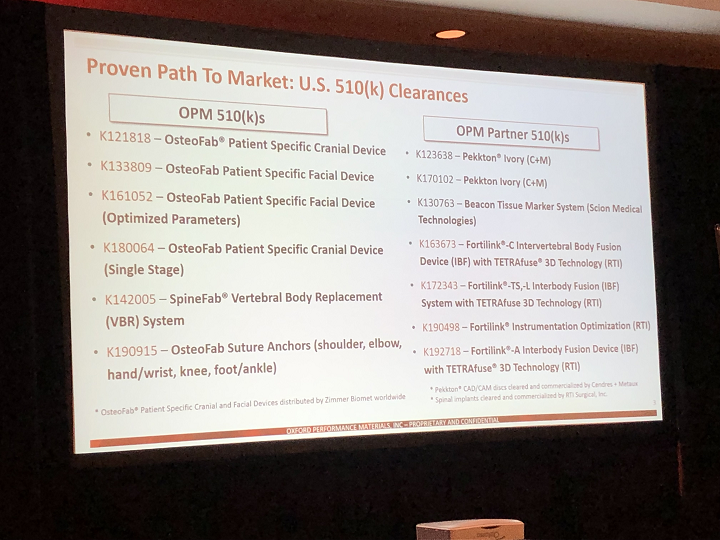
Discussing some of the company’s orthopedic applications, Maandi brought up OPM’s OsteoFab 3D printing process, which involves laser sintering with its high-performance OXPEKK material.
“We’ll get a CT scan, and in-house can deliver implants within 24-48 hours to healthcare facilities,” he stated.

OPM started with CMF and spinal implants, and its latest 3D printed device is a suture anchor, which will have its first case performed this month.
“One of the main benefits is the impact we can have on patient care and improving their lives,” Maandi explained. “We see the additive manufacturing industry moving, at least in the orthopedic market, and slowly going down the body…moving down to long bone defects and ankle reconstruction.”
The floor was then opened for questions, and someone asked if OPM had a roundabout price for its 3D printed implants; as we all know, custom medical devices can be pricey. But Maandi responded that it is “overall cheaper than something you could machine.”
John Hornick, the Chairman for the Medical and Dental track at AMS 2020, asked a question next, telling the panelists that two of his friends had recently received knee replacements. One friend had a 3D printed implant, while the other had a conventionally manufactured one, “because his doctor didn’t know anything” about AM technology. Hornick wanted to know how the panelists got the word out about what their companies could offer.
Kennison said that it really depends on the application – surgeons are more likely to engage in word of mouth, and do their own marketing and PR, for some of the more complex cases that use 3D printing.
“It can be challenging to market some of these cases,” she said. “You can’t promote custom devices, so there are some restrictions here.”

Maandi acknowledged that it can be tough, because many of the people they deal with in the healthcare field just aren’t aware of all of the available 3D printed options.
Later that same day, I sat in on a panel called “Regulation of Additive Manufacturing of Medical Devices and Its Impact on Products Liability,’” which I had not originally planned on attending; however, after sitting at the same lunch table as panelist Sean Burke, a partner with the Duane Morris law firm in Washington D.C., I was intrigued.
Panelist Bob Zollo, the President of Avante Technology, was unable to make it, so Burke had the floor all to himself. Acknowledging with good humor that he was the only thing standing in the way of happy hour, he moved through his topic efficiently.
According to his bio, “Mr. Burke’s practice focuses on representation of manufacturers of medical devices in products liability cases across the country, including in consolidated multi-plaintiff matters in both federal court and state courts in California, Illinois, and Tennessee.” In terms of defense experience, he has worked with many things, including surgical instruments and fusion plates, and recently became interested in the use of AM, advising and consulting his clients on best practices in the early product development stages in order to help them lower their risk of liability exposure.

But, as Burke told the room, “Basically, at the end of the day, there are always risks.”
He explained that while many people look at it as more of a barrier, FDA regulation and compliance is “really the best shield that medical device companies have.”
“You’re on a bit of an island if you don’t have the same regulations.”

Burke explained that the FDA is trying to “play catch-up” in determining how exactly to regulate this kind of technology. The agency has issued guidance on design, testing, and manufacturing controls for AM, but this doesn’t mean that it’s offering a solution.

From a products liability standpoint, if a company has standards to fall back on when telling a jury about the testing that’s been completed on a 3D printed medical device, the chances are more likely that the jury will be able to understand.
“But when there aren’t standards or testing, but the FDA wants to look at it, that’s a recipe for exposure,” Burke said.
As an example, Stryker’s 3D printed tritanium spinal cage was recalled last year for updates; after conducting a Google search, Burke found four different attorneys who were looking to take these cases to court…bad news for the AM industry.
Burke moved on to current trends about litigation involving 3D printed medical devices. While there haven’t been too many class action suits because the cause for each patient’s failure is usually different, the number of cases is rising.

He listed some of the factors that drive litigation, including the media, company field actions, FDA safety communications and labeling changes, pending litigation, and scientific and medical literature. Burke also provided an explanation on the different types of product liability claims – strict liability, negligence, and fraud/misrepresentation.

In terms of manufacturing defect claims, evidence must be presented that shows there has been a “deviation from the original design.” This can be difficult to validate, but there are many variables involved with AM, such as powder use. To protect against Failure to Warn claims, medical device companies that use 3D printing need to broadcast if there are any developments, and provide up to date information as well.
Burke gave attendees some pretty solid advice at the end:
“I know you all consider this, but think about why you’re 3D printing, and make a concise statement about why you’re doing it, and not just because you’re trying to “keep up with the Joneses” in terms of cool new technology.”
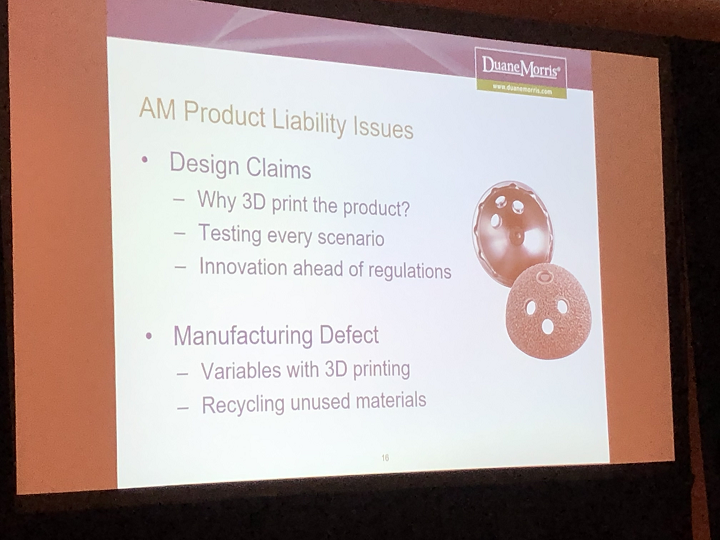
Then it was time for some questions. One attendee said that patient-specific products are not always treated as customized, and wanted to know why this makes a difference in terms of regulation. Burke explained that if a 3D printed patient-specific device is deemed a custom product, then it does not have to go through the same regulatory channels.
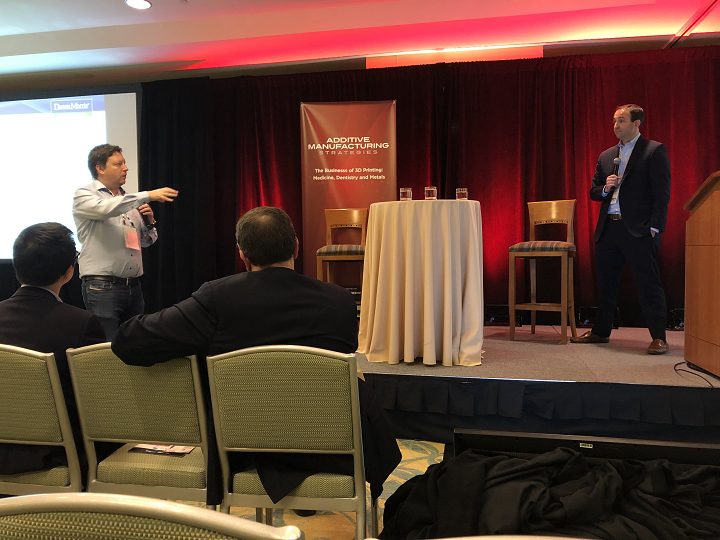
Joris Peels, 3DPrint.com’s Editor-in-Chief, was chairing this panel, and asked about the use of 3D printing in courtroom settings, and if regulatory bodies consider it. Burke said that his firm’s experts are definitely on board with this, especially in terms of patient anatomy models. He mentioned a big case centered around hip dysplasia, and how a 3D printed exhibit – I’m guessing it was an acetabular cup – was used to show how things were not fitting correctly in the patient’s body.
Another attendee asked Burke for best practices that startups not yet looking to liabilities could use.
“I think it depends on what they want to do,” he answered. “I work with startups and large companies, but there are some things to do up front to advise them.”
He suggested setting up a meeting with the FDA to hear their thoughts and concerns, and document the meeting.
“It’s an exhibit – the FDA knew we were doing this and that test, and still cleared it,” Burke explained.
Stay tuned to 3DPrint.com as we continue to bring you the news from our third annual AMS Summit.
Discuss this and other 3D printing topics at 3DPrintBoard.com or share your thoughts below.
[Photos: Sarah Saunders]
The post AMS 2020: Panels on 3D Printing in Implants and Orthopedics, Regulation in Additive Medical Devices appeared first on 3DPrint.com | The Voice of 3D Printing / Additive Manufacturing.