Researchers from Iran and the UK are taking on central topics in digital fabrication, delving deeper into parameters, properties, and composites, with their findings outlined in the recently published ‘The Synergic Effects of FDM 3D Printing Parameters on Mechanical Behaviors of Bronze Poly Lactic Acid Composites.’
The authors use optimization in this study to find out more about the effects of printing on a bronze PLA composite. Popular due to its plant-based origins and biodegradable and biocompatible properties, PLA is a thermoplastic aliphatic polyester often made from corn starch. Fused deposition modeling is a popular method of 3D printing used with PLA and a variety of composites today—from bioinspired materials to graphene oxide, silver nano-wire photopolymers, and more. In this study, the authors investigate the use of bronze polylactic acid (Br‐PLA).
The researchers worked to refine the mechanical properties of FDM-printed parts not only through experimenting with different input parameters but also by employing the design of experiment (DOE) method. Ultimately, the goal was to:
- Print tough Br‐PLA samples
- Reduce part thickness
- Shorten build time
The following parameters were studied:
- Layer thickness
- Infill percentage
- Extruder temperature
- Maximum failure load
- Thickness
- Build time of parts
Samples were designed using Simplify3D, and fabricated using Br‐PLA filament with a Sizan 3D printer. On testing the samples, the researchers noted that 80 percent of the results within the ‘design matrix’ displayed brittle fracture—and not surprisingly, as PLA is known to take on brittle properties during tensile loading.
“The fracture of brittle samples occurred at the elastic limit, while tough specimens showed the ability to undergo a low degree of plastic deformation before fracture,” said the researchers. “Therefore, samples with higher maximum failure load and elongation at the break had a tough fracture. However, a sudden brittle fracture is usually observed in samples at the elastic limit and in a lower failure load.”

(a) Brittle fracture of the specimen (sample #12 Br‐PLA), (b) Brittle fracture of the optimum PLA specimen, (c) fracture of #1 to #6 samples.
Using the DOE method to better the quality of their experiments and cut down on testing, the team measured 20 of the samples for maximum failure load, thickness, and build time.
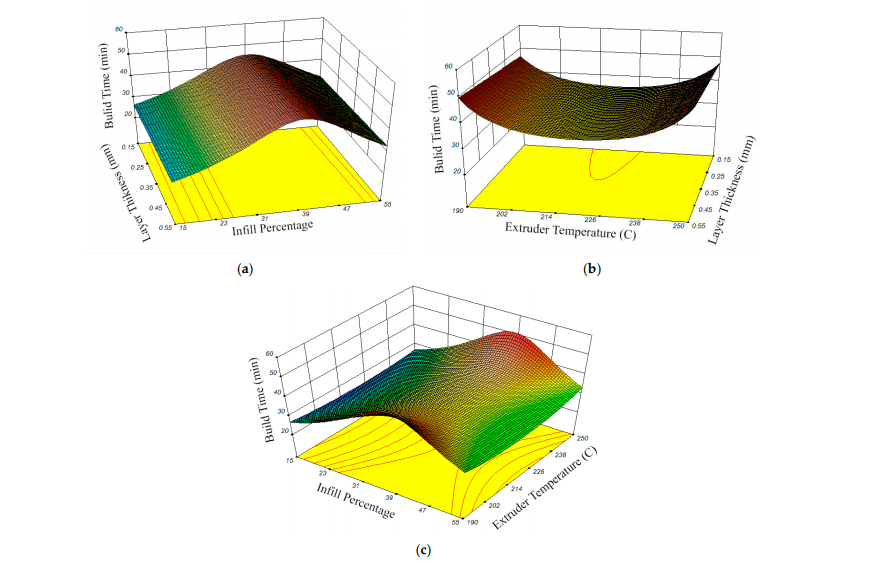
3D surface plot of the build time with (a) infill percentage and layer thickness; (b) extruder temperature and layer thickness; (c) infill percentage and extruder temperature.
Overall, the researchers noted that their optimization technique was successful. ‘Predicted optimum results and experimental validation’ varied little, with few errors. In comparing PLA and Br‐PLA 3D printed samples, PLA clearly showed higher tensile strength. This was attributed to use of greater infill percentage—as well as the fact that PLA is intrinsically stronger because it is a single material—in comparison to the composite made up of two materials.

Overlay plot of 3D printing optimization with (a) infill percentage and extruder
temperature; (b) extruder temperature and layer thickness.
The optimized Br‐PLA samples successfully resisted over 1000 N, with the following parameters:
- Layer thickness of 0.25 mm
- Infill percentage of 15.20
- Extruder temperature of 222.82 °C
“For producing a suitable sample with good mechanical and economical features, middle extruder temperatures and low infill percentages must be considered. Because in the Br‐PLA 3D samples, the heavy and rough samples might not be used very much, and the heavier samples are costly,” concluded the researchers.
“In the PLA 3D printing samples, the maximum failure load was reported more than Br‐PLA samples, and that is because the composite structure has the more particle’s space, and in Br‐PLA, the metal component takes up more space than PLA structure.”
What do you think of this news? Let us know your thoughts! Join the discussion of this and other 3D printing topics at 3DPrintBoard.com.
[Source / Images: ‘The Synergic Effects of FDM 3D Printing Parameters on Mechanical Behaviors of Bronze Poly Lactic Acid Composites’]
The post Optimizing FDM Bronze PLA Composites Prints appeared first on 3DPrint.com | The Voice of 3D Printing / Additive Manufacturing.