The giants are coming. DSM, SABIC, BASF, DOWDuPont, Eastman, Mitsubishi, Covestro, Evonik, Arkema, Perstorp, Clariant and Solvay have all joined the 3D printing industry. All these companies are making serious investments in creating materials and applications for 3D Printing. Their heft, polymer expertise and existing client base should all help our industry grow. They all have high hopes for our fast-growing industry but these giants range from $2 billion to $65 billion in revenue. Is there enough room in our $12 billion industry for this heard of elephants? Will act like accelerants to our industry, making 3D printing better? Are they here for the long run? What will they do?
3DPrint.com asked Brian Alexander of Solvay what the €12.4 billion Belgian chemicals company is up to in 3D printing. Solvay has not made a brash entrance at all but is slowly but surely making its polymers available to the 3D printing market. Solvay is selling directly via its own e-commerce site and is focussing on high-performance materials such as PPSU and PEEK. Brian leads the Business Incubation Platform Additive Manufacturing at Solvay Specialty Polymers and is in charge of bringing Solvay to the 3D printing market.
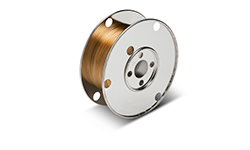
PPSU is a good candidate material for 3D printing, what do you think it will be used for?
PPSU delivers the highest performance of amorphous materials for chemical resistance, toughness and thermal stability. The high heat resistance and excellent hydrolytic stability of Radel PPSU make it an excellent choice for hot water fittings and medical devices requiring repeated steam sterilization such as dental and surgical instruments, but also for aircraft cabin interior parts, that need to withstand cleaning agents and to comply with extremely stringent fire, smoke, and toxicity standards.
Where do you see your Fluoropolymers portfolio being deployed in manufacturing?
With exceptional purity and chemical resistance, our fluoropolymers are typically used in the chemical processing industry, automotive and oil & gas. We already see demands from these sectors for 3D-printable fluoropolymers that will enable more sophisticated shapes and tailor-made, small-series production.
What are your plans for PEKK?
We are working on a PEKK powder for selective laser sintering (SLS) that enables for superior 3D-printed parts. It is currently available for sampling. We are also studying the use of PEKK with other printing technologies.
For PEEK?
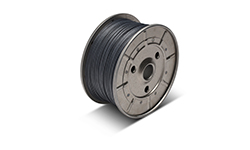
We have recently launched a AM-ready filament based on our KetaSpire PEEK, which has a unique reputation in the market as one of the highest performing polymers out there. We believe that Fused Filament Fabrication is the best technology for such a material, but the industry is evolving quickly, which is why we also work on adapting this material to other printing technologies.
When do I use PEKK and when do I use PEEK?
Both a similar materials, but PEKK has higher thermo-mechanical properties, while PEEK has a higher chemical resistance.
High-performance polyamides would seem to be a future area with significant competition with DSM, BASF and other gearing up in the space. Will you join with your PPA’s?
Solvay Specialty Polymers’ ambition is to leverage its full portfolio of high-performance polymers. At the same time, we work flexibly and pragmatically on new product developments, based on customer demand and technology readiness. PPA’s are currently not in our focus.
Do you believe in Swiss army knife polymers that can be used for a wide array of applications? Or very specific materials?
With over 35 different high-performance polymers in our portfolio, which is the broadest in the market, we firmly believe that there is no “one size fits all” polymer. What you need is a range of AM ready materials able to cover most industry applications. We have that.
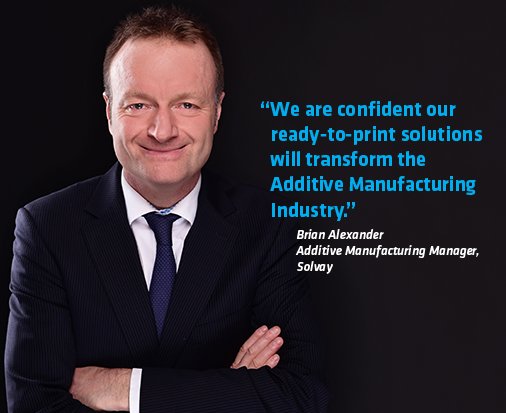
Will you be selling resin for 3D Printing direct, through distributors?
We started selling our polymers directly through our eCommerce platform which offers a new experience to both existing Solvay customers and new customers. The great advantage of this site is that behind, you have access to Solvay’s unique materials expertise and application know-how. But we are also working “offline” with our strategic customers and building a network of partners capable of printing our materials to develop new applications and help our customers find the best solution for their needs.
How about SLS powder?
SLS powder is much more specialised especially for higher performance polymers and requires a higher initial investment for the printer. We are currently working closely with some key customers to enter this market.
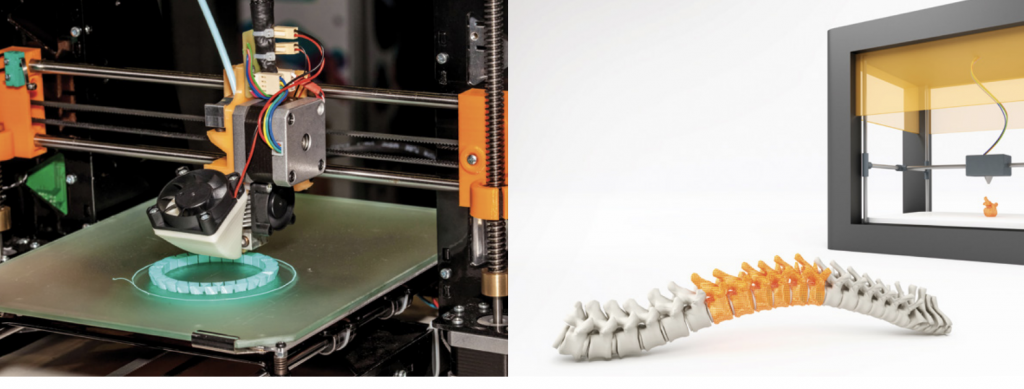
Are you focusing on FDM, SLS, SLA?
We are focussing mainly on FDM and SLS, but we monitor the market constantly for new technologies.
What future applications are you most excited by?
“The most exciting aspect of Additive Manufacturing, is not being limited to current applications and design. The most exciting applications are still in the minds of the designers and engineers, and it is our goal to help them find the right solution to meet the needs for their applications, whatever the industry.”
What does Solvay want to do in 3D printing?
Our objective is to become a globally leading supplier of customized high performance AM solutions.
What are some polymers that you have that we in 3D printing are not familiar with yet?
So far we have focused on a handful of materials from our portfolio, so we still have a wealth of possibilities to explore, both with aromatic polymers and fluoropolymers, including fluoro-elastomers.
We see some companies moving aggressively into 3D printing, Solvay seems comparatively cautious?
There is indeed a lot of communication around the topic, which some even consider to be a hype. We are working on creating the right foundations and expertise, both internally and externally, to grow our 3D printing capabilities for the long run.
Is there a particular industry that you are focussing on?
We started with PEEK and PPSU because they are polymers which are recognised and used extensively in Healthcare and Aerospace. Both industries have ambitious targets for the adoption of 3D printing in customised or small-series production, so they are obvious initial targets for our offering.
What kinds of companies are you interested in partnering with?

We believe in an open ecosystem approach that allows to combine the best solutions for a given customer or application. Those solutions will not always be the same. This is why we are ready to partner with a large range of players, from leading printer manufacturers – large and small – to specialist software companies such as e-Xstream, we want to work with the best companies to take 3D printing together to the next level. We have even launched an AM Cup, an open innovation competition to tap into the ideas and creativity of some of the brightest students in AM and accelerate our product development cycle – and we were stunned the results, which were excellent.

Why should I as an end user work with Solvay PEEK rather than someone else’s PEEK?
We have worked hard to develop a PEEK filament with superior performance and are already working on NexGen materials. We are also combining our strength with those of our partners in the printer, processing, and design space to allow our end users to print the best possible 3D parts.
PEEK is very difficult to print. Are you doing things to correct this? Or do you think that the industry will solve this with printers?

Materials, hardware & software all need to be optimised to get the best 3D printed part performance. We are working to take PEEK to the next level for demanding AM applications.
Just generally why should people work with you rather than another firm?
Solvay is an innovation powerhouse since 1863. We believe in the power of science and what science can deliver for society. We demonstrate this every day by pushing the limits of high performance polymers to solve some of the planet’s trickiest material challenges, and we do so striving for sustainable solutions. More specifically, we also have the broadest range of high performance materials and work with over 3,000 customers across all industries. This gives us unique capabilities to develop the best possible AM-ready material solutions.
What kinds of end-use customers are you looking for?
Obviously, we want to serve our over 3,000 existing customers with our AM offering. But we also believe in the democratisation of manufacturing thanks to AM. Tomorrow, anyone among the 10s of millions of designers, engineers, or makers across the planet could need a spool of Solvay filament for his or her project. Our eCommerce platform is there to also reach out to all these potential end users.
Melt processable fluoro TPE’s are very interesting materials – could these become 3D printing materials?
“We have our entire portfolio to play with, and we will develop it flexibly and pragmatically. too soon to say.”