Seven years ago, the World Health Organization estimated the total global volume of operations to be 312.9 million. That could probably mean that in our lifetime, a lot of us will go under the surgeon’s knife, and because it’s not as scary anymore as perhaps the early 1900’s (if you saw the Cinemax hit show The Knick, you know what I mean), we should be thankful to live in the 21st. century. Surgery has become safer, and cosmetic surgery, microsurgery and many other elective-type surgeries are quite common and often painless procedures. Still, some of the more complex surgeries still have high death rates. In an attempt to take advantage of the ongoing technological advances, many medical specialists have noticed that 3D printing can improve surgical planning and training, which will directly benefit surgical procedures.
Last year, Nova Scotia surgeons used a 3D printed brain model in surgical planning for the first time, while 60 specialists at the Mayo Clinic dedicated three and a half years and more than 50 Saturdays to practicing a very complex face transplant, thanks to 3D imaging and virtual surgical procedures. In Melbourne, Australia, the Austin Health 3D Printing Laboratory supports 3D printing for clinical applications and runs an active research program exploring how 3D printing can be used for teaching, procedural simulation, patient education, surgical planning, and prosthetic implants. The first facility of its kind in the southernmost city of the country, 3dMedLab came about after discussions for a more coordinated and organised approach to 3D Printing Resources throughout The University of Melbourne and in particular the availability of this technology to Clinician-Researchers at hospitals associated with the Faculty of Medicine, Dentistry and Health Sciences. Since then they have expanded the number of medical specialties and researchers that they work with across multiple Melbourne hospitals as well as developing nationwide and international partnerships.
3DPrint.com spoke to Jasamine Coles-Black, doctor and vascular researcher at the Department of Vascular Surgery at Austin Health, in Melbourne to understand how 3D printing can improve surgical planning in complex endovascular procedures to treat the arteries and veins of the body and training for medical residents.
“3D printing is the exciting next step in personalized medicine. The anatomical models are custom-made using scans that we have acquired as part of a patient’s medical care. From these scans, we can highlight the parts of the patient that we are interested in operating on and use these images to make a 3D model. From there, it can be printed using any 3D printer. The lab frequently prints models of diseased aortas to perform a ‘practice-run’ surgery. We have found that these 3D printed models are of greatest value when we are confronted with challenging cases. In addition to using them for surgical simulation, they can also be used to teach trainee surgeons about the anatomy and approach in difficult cases. These same models can be used to explain to patients their disease, and the procedure we are proposing they undergo. We have found that we are better able to communicate with patients about their disease when they can hold their own anatomy in their hands,” explained Coles-Black, who is Co-Founder of 3DMedLab along with Jason Chuen, the Director of the Lab.
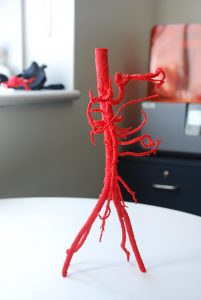
Abdominal Aortic Model 3D printed on MakerBot Replicator 2X FDM printer in ABS, used for anatomical teaching of surgical trainees
At the 3DMedLab experts have also 3D printed internal carotid arteries (the main blood vessel in the neck supplying the brain) to help visualise them before the team performs operations aimed at preventing strokes, or before they operate on tumours in the neck involving these arteries. Tracie Barber, assistant professor and a collaborator for the University of New South Wales, 3D prints fistulas created by vascular surgeons for dialysis access as an educational tool for patients and nurses. Furthermore, the very first anatomical model 3D printed at the lab was to plan a particularly complex abdominal aortic aneurysm that would have been life-threatening to the patient if left untreated. The operation was succesfully performed by Chuen, and according to Coles-Black, the patient has even taken home the 3D printed replica of his aneurysm, where it has been given a name!
Hospital patients will benefit with new research that shows surgery is far superior if doctors do 3D printouts of the relevant body parts, so that people requiring operation will get customized surgery, making procedures quicker, patients wont be under anaesthetics for as long, allowing the production of efficient simulators for endovascular training, improving residents’ surgical performance and self-confidence. Coles-Black claims that 3D-printed models may help in understanding the behaviour of the endovascular material in three dimensions, inside a specific anatomy and can be directly manipulated and inspected, which can help identify some details that might not have been noticed on a CT scan. Furthermore, 3D printing allows a patient-specific simulation, which is more efficient than a generic one. Today, with online 3D printing services, like Shapeways or Materialise, taking care of any bespoke 3D project, it’s easier for doctors who don’t have access to 3D printers to outsource their anatomical printed models.
But although 3D printing improves surgical outcomes, as a cutting-edge field, there are still gaps in the literature that need to be filled in order to validate the benefits of these anatomical models in surgery. Scientific articles published to date have shown that surgeons find 3D printed models a beneficial advancement in surgical planning, and quite useful to train junior surgeons. Also, studies have shown that 3D printed anatomical models enhance patient safety by reducing a patient’s time under anesthesia, reducing operation times, recovery times, and even blood loss. The applications of producing life-size 3D models can have great benefits as well to a patient’s understanding of their disease and lessens their anxiety about the upcoming procedure. Personalised 3D printed models have been associated with increased patient understanding of basic anatomy, physiology, and the planned surgical procedure. This in turn helps the patient be more satisfied with their care resulting in a better engagement with the treating doctor.
The 3DMedLab is fully equipped with many 3D printers which are used depending on the function required of the 3D printed anatomical model. Including printers from FormLabs, the Form2 which Coles-Black claims was very useful in the creation of transparent, flexible, and autoclavable models which can be sterilised and applied in the operative field, and the Form Cure and Form Wash. While for inexpensive initial prototypes and to print bony models such as for orthopaedic or maxillofacial surgery, they use an Ultimaker S5, for intricate structures such as the delicate bones of the face, Coles-Black and her team uses Ultimaker PVA (polyvinyl alcohol) a water-soluble support material for multi-extrusion 3D printing. To produce Orthopaedic models to size prostheses and simulate the reaming of bone, they rely on an Objet Scholar. And also have access to a Connex 3, Makerbots, and a metal SLS printer through the University of Melbourne.
So how much time does pre-surgical simulation take? As Coles-Black told 3DPrint.com, it depends very much on the procedure that is being planned:
“The process can be as quick as bending a metal plate for facial reconstructive surgery against a 3D printed replica of a patient’s jaw in order to save time during surgery, to doing an entire “practice-run” of a procedure, such as introducing a needle and wire into a life-sized 3D printed aorta, navigating its anatomy, and deploying a stent into it as you would in a real patient. In essence, the strength of 3D printed anatomical models is that it allows us to create a life-sized replica of a patient’s anatomy. Doing a ”practice-run” before performing surgery on a real patient allows us to better plan for and anticipate challenging scenarios. Every individual’s anatomy is unique, and having the opportunity to practice the procedure beforehand allows us to make a plan to deal with potential problems before we operate on a patient. This improves the speed and the safety of our operations. Sometimes doing a “practice-run” on an exact replica of a patient’s anatomy also changes the techniques and equipment used.”
With research involving 3D printing hollow, diseased patient-specific abdominal aortic aneurysms, dilatation of the abdominal part of the main artery in the body which has a 70 to 80% mortality rate when ruptured, Coles-Black is very interested in introducing 3D printing technology to her work. Using 3D printed models help visualise and physically hold the patient’s individual anatomy in their hands, as well as practice minimally invasive repairs before performing them on the actual patient.
“These replicas of patient’s aortas also help to guide our selection of technique and equipment,” she stressed.
In order to improve the realism of her models, the expert is searching for a material that “most closely mimics a real aorta.” Every month, doctors at the 3DMedLab print dozens of anatomical models to help with the pre-surgical planning of Cardiothoracic Surgery, Orthopaedic Surgery, Plastic Surgery, Maxillofacial Surgery, Ear Nose and Throat Surgery, Urology, General Surgery, Neurosurgery, and of course Vascular Surgery. They even produce 3D printed anatomical models to help Vets with their surgical planning too; something many veterinarians have been attempting to do.
“In addition to this, we 3D print training models used by medical professionals to teach and upkeep their procedural skills,” Coles-Black said. “For example, we have just 3D printed a large batch of airway training models requested by a paramedic at a base hospital in the Middle East. We also receive requests from research labs hoping to quickly and cheaply replace equipment parts. 3D printing technology has been around for a while, but a few years ago, doctors and other health professionals began to make use of it as part of patient care. Five years ago, when Jason and I founded 3D Med Lab I was still a medical student, so I have always envisioned 3D printing as part of my practice. In the past few years we have noticed an increase in the uptake of this technology amongst medical professionals. Certainly, the number of requests our lab receives seems to reflect this. 3D Med Lab is open to the medical space and offers clinicians everywhere a chance to get started in 3D printing.”
The 3D Med Lab supports doctors and scientists interested in this technology by providing a central hub for the exchange of knowledge and ideas. Thanks to their workshops they teach other interested clinicians in using 3D printing as part of their practice. Their next annual Australian 3D printing in medicine conference (#3dMed19) will take place November 14 through 16, in Melbourne.
As Coles-Black says, it is a small but growing field, getting a lot of interest from enthusiastic research students. Nonetheless, to really disrupt the medical industry, some of these models will require even more human-like properties, so it might be a few more years before advances in 3D printing technology allow printing of multi-material products to achieve the mechanical properties required, using cost-effective methods. But this is a great start for many research centers, universities and hospitals around the world that are getting a noticeable advantage through the use of additive manufacturing, and certainly, more patients would benefit with its widespread use.
[Images: 3dMedLab, Austin Health]