SNOOZ is known as the world’s best-sounding white noise machine. The device, which houses a real fan, creates white noise to encourage sleep — without either the annoyance of a looping soundtrack or unwanted cold air in cooler months. The best-selling system is seeing success in travel and home use as the sleep fan continues to gain fans around the world.
Working with Shapeways to 3D print dozens (and dozens and dozens) of designs to reach the ideal sound system, the SNOOZ team cut substantial time and costs in their production process by rapidly prototyping. The savings over traditional machining was major enough that this Las Vegas-based startup has now been working with Shapeways for more than five years — and still has more product work with us in the pipeline for the next devices.
We interviewed SNOOZ CTO and Co-Founder Eli Lazar to dig into how SNOOZ utilized Shapeways’ 3D printing technology and services to make a new product possible.
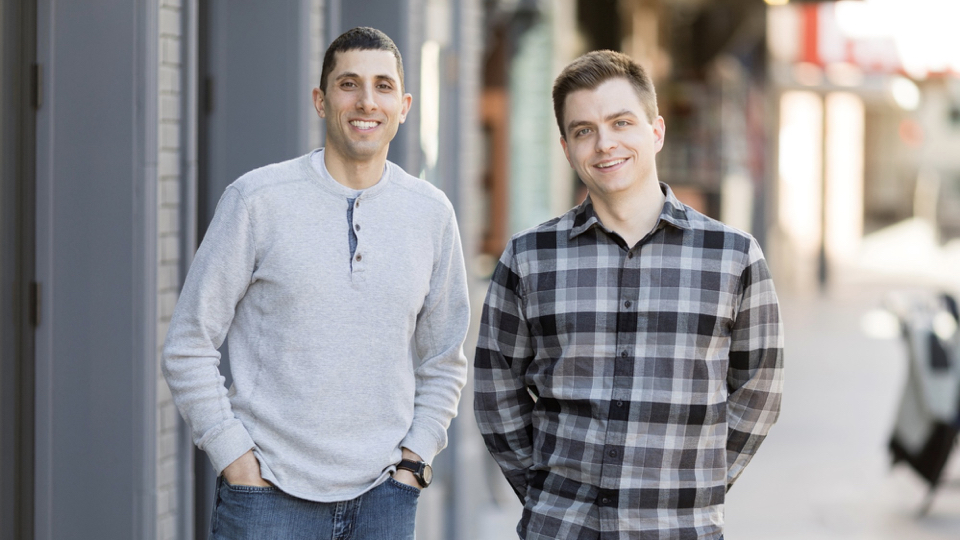
Having parts machined was always an option too, but from our experience, that is 10-25x higher cost [than 3D printing], and perhaps 10x slower, which was just not an option for us.
Eli begins by laying out the big picture:
“The Shapeways printing service has really been instrumental to the success of our product and company. Our product is a specialized fan for sleeping, and in the quiet of a bedroom you can literally hear every frequency, so any unwanted tones people will pick up right away. We used Shapeways to print probably 100+ variations of our product to perfect the acoustics and create our signature sound.
As a result, by the end of this year we will have sold nearly 100k units, and we have a 4.7 star rating on Amazon (without manipulation) with nearly 1,500 reviews. SNOOZ is also used in nearly 2,000 hotel rooms across the country as well.
To be very direct, without having access to the Shapeways printing service our product would not have been nearly as good as it is today, or perhaps, not a success at all. Shapeways gave just two average guys with very limited finances access to world class rapid prototyping at an affordable price. That has really made the difference in our product and the reviews we have received. In fact, we found the precision from Shapeways prints to be so good that when we machined our actual plastic molds for production, we didn’t have to do any changes and were able to go to production much faster and at a lower cost. We also have two new products coming out this year, both of which have been prototyped on Shapeways, and we have started on developing a new product which will be using Shapeways again for.”
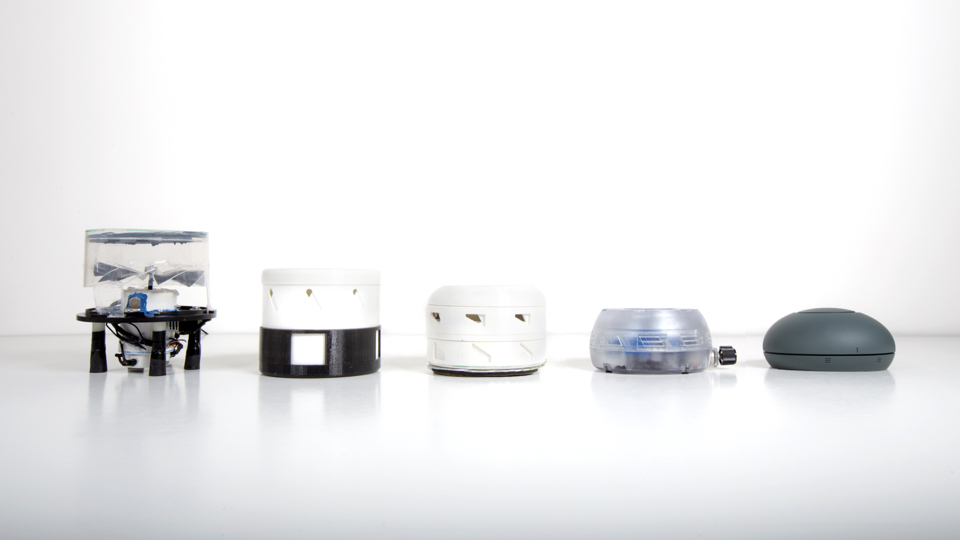
At the beginning, how did you come to the decision to use 3D printing instead of other manufacturing methods?
“Without 3D printing, I am not sure we could have ever developed a viable product, or at least one that people actually liked. Our fan blade is entirely custom, and small details make a huge difference. A 1-degree extra twist in the blades or 1mm extra length or width of the blades, and it generates a whole different set of tones. You can use software to simulate the acoustics for a fan blade design, and we did do quite a bit of this. However, these simulations can take up to a few weeks to run, and they are really not accurate enough to predict the subtleties that we were interested in. The best way I can explain this is that a stringed piano is always acoustically superior to a digital keyboard, because the timbre (perceived sound quality) of real sound is just better than any digital replica. With that said, we had to make actual parts. Having parts machined was always an option too, but from our experience, that is 10-25x higher cost, and perhaps 10x slower, which was just not an option for us.”
Did you already have technical knowledge in 3D printing? If not, was there a learning curve to getting into this technology?
“We didn’t have any prior experience with 3D printing before SNOOZ. It was actually for this reason that I was drawn to the Shapeways website. A lot of other 3D printing services seemed to put the burden of getting the print right more on the user. When we first started using Shapeways in 2015, I think you were the only online platform where you could instantly get your 3D CAD analyzed for printing with a quoted price. Even still, I think Shapeways has the most user friendly website for 3D printing. The only learning curve was figuring out what tolerances to use so parts could snap together well. However, since I found Shapeways prints to be repeatable and accurate to the CAD, every time, it became pretty easy. I actually use the same tolerances we figured out worked in 2015 to this day, and that is nearly a five year span.”

What material(s) do you print in and why?
“We have printed in SLA, Versatile Plastic (Nylon), and PLA (which you guys offered shortly). However, Versatile Plastic is our preferred choice for prototyping. The main reason is the strength of the parts. We actually produce some parts out of Nylon and the strength and flexibility of a 3D printed part is definitely on par with a Nylon molded part that comes out of an industrial factory.”
Are you able to share any quantifiable metrics on the time and/or cost you’ve saved by prototyping with Shapeways?
“I found an early quote to machine a single part for $381 that we eventually ended up just 3D printing with Shapeways for about $30. Since then, we have printed over 100 parts, so the savings has literally made the difference in us being able to afford to start SNOOZ. Also, in terms of timing, it is absolutely incredible to be able to design a part on Monday and have it in your hand within a week or so. If the legendary inventors of the past had access to this technology, the world would be a vastly different place today.”
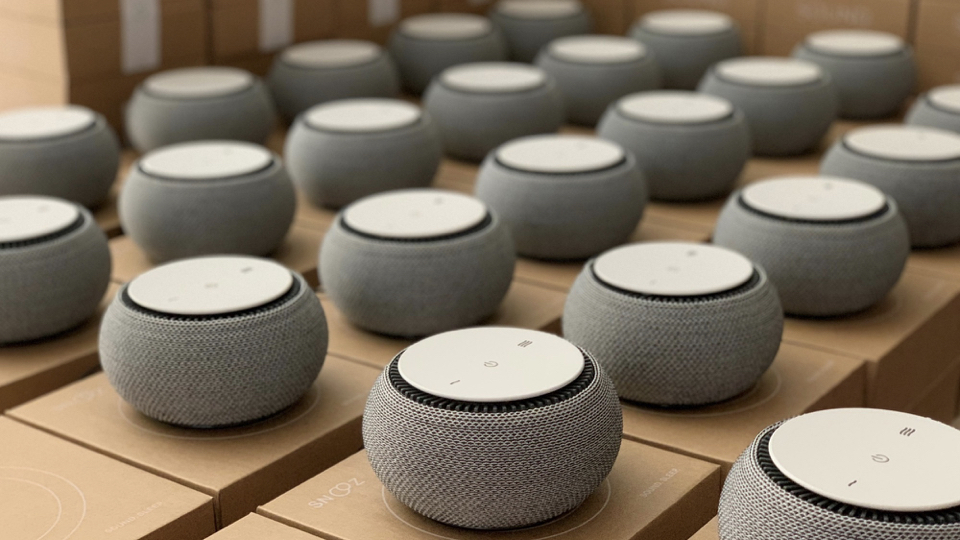
By rapid prototyping with 3D printing, the
SNOOZ team was able to test out more than 100 designs to find their perfect
acoustic fit — and then translate the final prototype directly into scale
production. The ease with which SNOOZ put the pieces together, at a literal
fraction of the cost of traditional machining, highlights the effectiveness of
3D printing throughout the product development cycle. And today? We’re SNOOZ’s
biggest fans!
Find out how Shapeways can help with your rapid prototyping needs today.
The post The World’s Best Sleep Fan Is A Fan Of 3D Printing: Rapid Prototyping With SNOOZ appeared first on Shapeways Blog.