California-headquartered digital manufacturing company VELO3D, which recently raised $28 million in a Series D funding round, just announced that it has developed a process for 3D printing parts out of foundry-grade Aluminum F357 on its Sapphire metal 3D printers. The commercial release of this capability is significant, because the material is traditionally manufactured with casting technology, but now it can be 3D printed in intricate, complex shapes that casting just can’t achieve.
“Aluminum F357 has already been certified for mission-critical applications—unlike some exotic alloys—so it was a logical addition to our materials portfolio. We will continue to add more compatible materials that enable customers to print parts they couldn’t before, yet with even better material properties than traditional manufacturing,” explained VELO3D Founder and CEO Benny Buller.
This aircraft-grade aluminum alloy, which is well-suited for laser powder bed fusion 3D printing, lets companies in the aerospace, defense, and military sectors 3D print parts that used to be made through casting. Specific components that VELO3D specializes in 3D printing with Aluminum F357 are for thin-walled heat transfer applications.
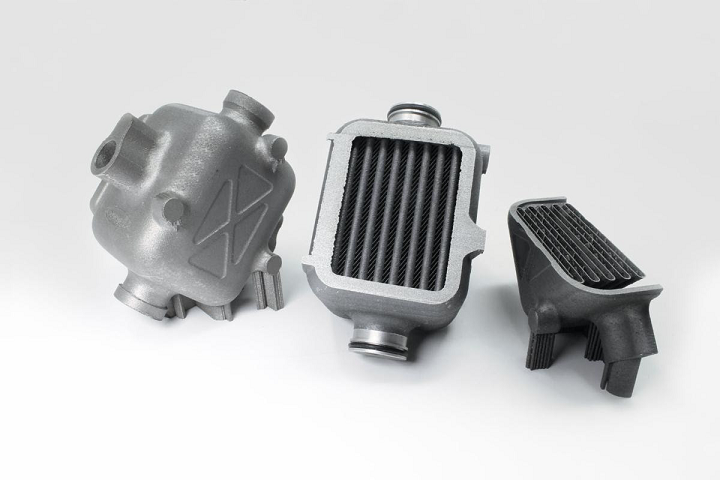
These photos of 3D printed components demonstrate various perspectives of the design freedom that VELO3D’s SupportFree capabilities offer when it comes to heat exchangers.
VELO3D worked with global advanced cooling solutions supplier PWR to develop the Sapphire metal 3D printing process for Aluminum F357. This was a smart partnership, as PWR has provided cooling solutions to several racing series, including Formula 1 and NASCAR, and customers in the aerospace, automotive, and military industries.
Matthew Bryson, General Manager for PWR, said, “We chose Aluminum F357 due to its ideal material properties to suit thermal performance, machining and weldability.
“Our ability to print free-form and lightweight structures for heat transfer applications with our Sapphire system from VELO3D will further enhance performance and packaging optimization opportunities for our product range and provide significant value to our customers.”
VELO3D’s patented SupportFree capability for metal 3D printing means that support structures for steep overhangs, low angles, and complex passageways are not required, allowing users to attain geometric freedom. The Sapphire metal 3D printing system is built with a semiconductor mindset to ensure repeatability in serial manufacturing, and paired with a con-contact recoater, its print process is able to fabricate the high aspect ratios and extremely thin wall structures needed for flight-critical applications.
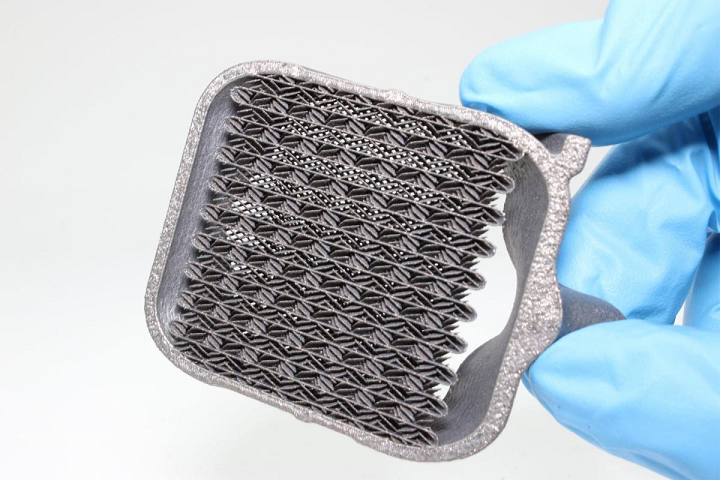
Notice the ultra-thin features in the core (cross-section image). Such complexity is near-impossible to attain with existing AM technologies.
While other aluminum alloys, like AlSi10Mg, are used in metal 3D printing more often, Aluminum F357 is ideal for thin-walled AM applications due to shared characteristics with popular casting alloy A356, and because it can be anodized. SmarTech Analysis reports that aluminum alloys accounted for close to 10% of 3D printed metal content last year, which led to a 43% growth in shipments of aluminum powder. The lightweight material is obviously growing in AM popularity, as VELO3D wasn’t the only company this week to roll out the material – Optomec just announced the use of its LENS DED systems for 3D printing aluminum parts.
VELO3D’s Sapphire metal 3D printer is now compatible with Aluminum F357, INCONEL alloy 718, and Titanium64. If you’re interested in a 3D printed aluminum alloy prototype, contact the company. Last month, VELO3D also announced that a 1-meter tall Sapphire system would be available in Q4 2020 for industrial customers, like Knust-Godwin, interested in using LPBF technology to print tall parts without supports.
Discuss this story and other 3D printing topics at 3DPrintBoard.com or share your thoughts in the Facebook comments below.
The post VELO3D Develops Process for 3D Printing Aluminum F357 on Sapphire Systems appeared first on 3DPrint.com | The Voice of 3D Printing / Additive Manufacturing.