Companies, organizations and individuals continue to attempt to lend support to the COVID-19 pandemic supply effort. We will be providing regular updates about these initiatives where necessary in an attempt to ensure that the 3D printing community is aware of what is being done, what can be done and what shouldn’t be done to provide coronavirus aid.
Anesthesiology residents from Massachusetts General Hospital in Boston are now hosting the CoVent-19 Challenge on GrabCAD, where the community can submit designs for rapidly deployable ventilator systems. The challenge will last two months starting April 1, with finalists chosen to work with Stratasys to realize their designs as functional prototypes for testing. After four weeks, 20 finalists will be chosen before another four weeks are dedicated to developing and testing functional prototypes with the help of private and public sector representatives knowledgeable about the regulatory measures and safety testing associated with these medical devices. Three top finalists will win $10,000 in credits Stratasys Direct Manufacturing.
Now that Medtronic has opened up the design files for its PB560 system, there may be a possibility that these designs will be functional and safe. Unfortunately, two months is a long time for people currently in dire need of ventilators, so hopefully alternatives to the CoVent-19 Challenge can be found instead. Perhaps most logically and importantly would be the increase in production of ventilators by manufacturers, possibly in response to government mandate.
In the Czech Republic—the site of a major theft of 680,000 face masks shipping from China to Italy, possibly with state involvement—auto manufacturer ŠKODA is using its Multi Jet Fusion (MJF) systems to 3D print respirators for medical staff. The devices were designed by the Czech Institute of Informatics, Robotics and Cybernetics (CIIRC) at the Czech Technical University and certified according to EN 140:1999 standards for use within a week.
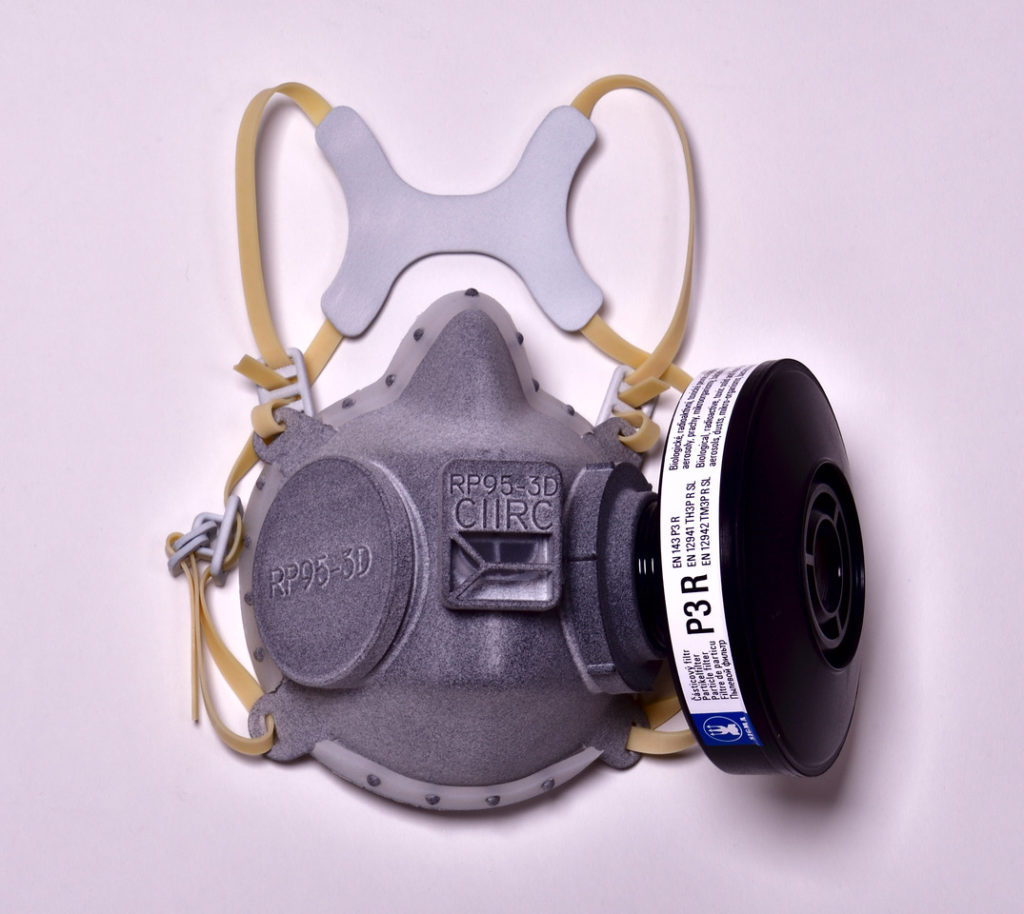
Respirator masks printed by ŠKODA and certified according to EN 140:1999 standards. Image courtesy of ŠKODA.
The CIIRC RP95-3D is made up of a mask, seal caps, an adapter for a P3 filter cartridge attachment and exhalation covers. It is designed to be reused and sterilized in a steam sterilizer, as well as disinfected with a spray solution made of 85 percent ethanol. The filter is meant to last up to a week. MJF was used to ensure minimal porosity and layer lines in order to maximize disinfection.
After first testing the printing of five masks and certifying the production of the device, ŠKODA is now able to produce 60 respirators per day, with 16 hours to print and 16 hours to cool. Once made by the auto company, Czech print shop 3Dees is assembling them and sending them to the Ministry of Health, which will distribute them. Whereas injection molding will ultimately be used for production, 3D printing is a stopgap while molds are developed and made. In the interim, companies with Jet Fusion 4200 and 5200 series systems are invited to access the CIIRC web portal.
The certification of the device is key. The fact that the CIIRC RP95-3D respirator is said to offer the same degree of protection as an FFP3 class respirator or higher, as certified according to specific medical device standards, means that this could be a valid replacement for traditionally made respirators.
The same cannot be said of some well-meaning filter systems being developed by individuals in Hong Kong. Makers in the region have developed 3D printable filter adapters for use on standard 3M half masks. Teacher Carlos Tchiang, for instance, has developed several iterations of an adapter to attach aerosol droplet filters to 3M HF52, 6200 and 7502 masks. Similarly, Neo Chan, the director of a video production team called Mirai Productions, has redesigned his own 3D printable filter adapter shown in the video below.
That isn’t to say that Makers don’t have their role to play in creating items in response to the pandemic, but that there are safer ways of participating. Devices for medical staff should be made in conjunction with medical professionals, possibly through existing initiatives, such as #GetUsPPE in the U.S. Those devices should either be certified by regulatory bodies or of the variety that don’t require as strict safety standards, such as face shields and distancing devices. One example is a face shield that has been approved by the National Institute of Health in the U.S.
Otherwise, Makers and businesses that don’t want to get into risky medical device production can work on items for the general public. Anisoprint, which manufactures fiber reinforcement 3D printing technology, is instead lending its hand to manufacturers impacted by the supply chain disruption resulting from the pandemic. The Russian-Luxembourg company will 3D print composite or plastic parts for businesses facing supply chain issues for free by emailing them at info@anisoprint.com.
The post 3D Printing and COVID-19, April 3, 2020 Update appeared first on 3DPrint.com | The Voice of 3D Printing / Additive Manufacturing.