3D Printing Industry News SLICED: Rize, 3D Systems, Essentium, Protect3d, Xioneer Systems
Rochester Institute of Technology: Creating Reactive Metal Inks for 3D Printing
In the recently published ‘Three Dimensional Digital Alloying with Reactive Metal Inks,’ author Chaitanya G. Mahajan submitted a dissertation for a PhD at the Kate Gleason College of Engineering at the Rochester Institute of Technology, exploring new ways to 3D print multifunctional components with multiple materials.
Mahajan extensively explores the theory of nanoalloys, including details on core-shell nanoalloys, subcluster nanoalloys, mixed nanoalloys, multishell nanoalloys, along with the factors influencing their structure from strength of atomic bonding to surface energies of bulk elements, atomic size, and more.
The author discusses the variety of nanoalloys, created via a chemical, bottom-up method, as well as a physical top-down method. With bulk metal broken into nanosized particles for the top-down technique, for bottom-up, both atoms and molecules are brought together to construct nanoparticles.
“The main advantage of the top-down approaches is that bulk quantities of nanoparticles can be produced within a short span of time. However, the bottom-up approaches have the advantage of a more homogenous structure with more ordered crystallography within the nanoparticle,” states Mahajan.
The author explains that many applications use alloy nanoparticles; for example, they are employed in biomedical applications for in vivo and in vitro studies. Such materials exhibiting shape-memory effect will be even more useful.
Metal inks are used either with nanoparticles (top-down) or metal-organic decomposition (bottom-up approach) precursor inks, with the active material comprised of a nanoparticle suspension.
“Additives such as surfactants are added to modify the surface tension of the ink, whereas dispersants are added to avoid agglomeration of the nanoparticles in the carrier solvent. To get rid of the carrier solvent, the printed pattern is thermally sintered to form a metallic layer,” stated the author.
Here, Mahajan presents a binary copper-nickel system to form an alloy with metal precursor inks, avoiding the typical clogging issues found with nanoparticle suspensions.
For this study, both copper and nickel inks were created for the purpose of inkjet printing, with reduction examined under a range of conditions. Both metal and alloy were then characterized using:
- Thermal analysis
- Infrared spectroscopy
- Energy dispersive X-ray spectroscopy (EDS)
- X-ray diffraction
“To achieve a homogeneous alloy formation, the copper phase and the nickel rich phase were diffused together at high temperatures,” stated the author. “Copper nickel alloy inks with ratios Cu30Ni70, Cu50Ni50, and Cu70Ni30 were formulated and reduced at 230 °C and later high-temperature diffusion was achieved at 800 °C.
“The lattice parameter of the alloy phase for the inks with ratio Cu30Ni70 was 3.5533Å, Cu50Ni50 was 3.5658 Å, and Cu70Ni30 was 3.5921 Å. Using Vegard’s law, the composition of the alloy phases for the three samples was estimated to be Cu32Ni68, Cu46Ni54, and Cu75Ni25. This formation of the desired alloy composition can open the door to numerous applications in the biomedical and electronics sectors, among others.
No segregations were seen for the samples that were sintered in vacuum and in the inert atmosphere; however, XRD analysis of the sintered alloy demonstrated both copper and bimetallic copper-nickel phases.
“To print a part with desired alloy composition, each layer can be printed and reduced over and over to build up a 3D structure. The final printed 3D part can be placed in a high-temperature furnace to achieve diffusion and form a homogenous alloy structure,” concluded the author.
“As the weight percentage of copper and nickel in the precursor inks presented were 6.5% and 4.5 % respectively, the number of printing and reducing steps increases to print a 3D part. The printing time can be reduced by increasing the drop volume of the ink or by increasing the solid content of the ink.”
3D printing has not only sparked innovation around the world, but also the study of materials—and especially inks—from direct ink writing to fiber ink, and even chocolate ink.
What do you think of this news? Let us know your thoughts! Join the discussion of this and other 3D printing topics at 3DPrintBoard.com.
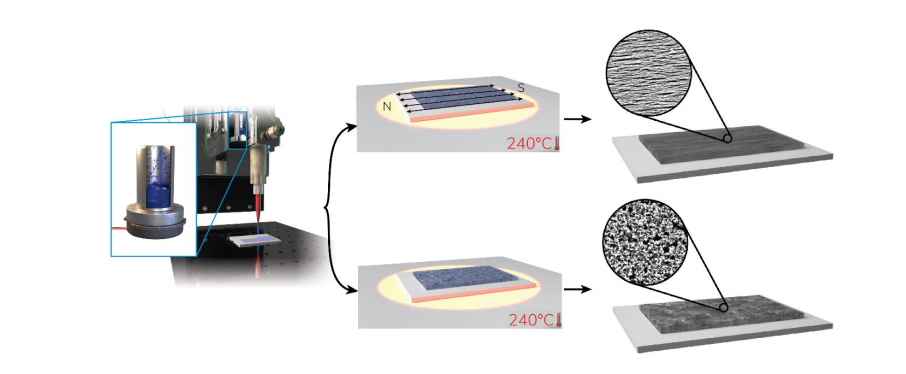
Schematic illustration of printing a Ni precursor ink and sintering it in presence of homogeneous magnetic field to reduce the nickel complex to aligned nanowires. Reproduced from [23] licensed under CC by 4.0
[Source / Images: ‘Three Dimensional Digital Alloying with Reactive Metal Inks’]
The post Rochester Institute of Technology: Creating Reactive Metal Inks for 3D Printing appeared first on 3DPrint.com | The Voice of 3D Printing / Additive Manufacturing.