German chemical giant BASF has steadily been saturating the 3D printing industry with its presence. The latest partnership established by the world’s largest chemical company is with machine tool manufacturer Cincinnati Incorporated (CI). The two inked a distribution deal in which CI will supply ABS, carbon fiber PET and recycled PET materials from BASF 3D Printing Solutions (B3DPS) for use with its Small Area Additive Manufacturing (SAAM HT) 3D printer.
The SAAM HT is the high temperature version of CI’s desktop-sized 3D printer, originally developed by Boston startup NVBots in 2016 before CI bought the smaller firm outright in 2017. The machine complements CI’s range of massive pellet-based extrusion 3D printers with a comparably petite prototyping device which is capable of automatically ejecting parts upon completion. The HT version of the SAAM is capable of 3D printing at temperatures of up to 500°C, including ULTEM, PEEK and polycarbonate. Material profiles for each filament the system uses can be downloaded, allowing the printer to process them more quickly and easily.
Now, with the BASF partnership, the SAAM HT will be sold alongside Ultrafuse ABS, PET CF15, and rPET. While ABS is nearly ubiquitous in the world of filament extrusion for its strength, flexibility and heat-resistant properties, PET CF15 offers additional strength and thermal resistance. BASF describes the material as being easy to process with low moisture uptake.
rPET is BASF’s gesture towards sustainability. Made up of 100 percent recycled PET, rPET “looks and prints just like virgin material,” according to the company. While BASF maintains a veneer of sustainability through the numerous admirable projects is has established related to renewable energy and biomaterials, it is one of the world’s leading petrochemical manufacturers, explores for and produces oil and gas, has been responsible for dangerous environmental disasters, and develops pesticides and other agricultural chemicals that have potentially toxic effects.
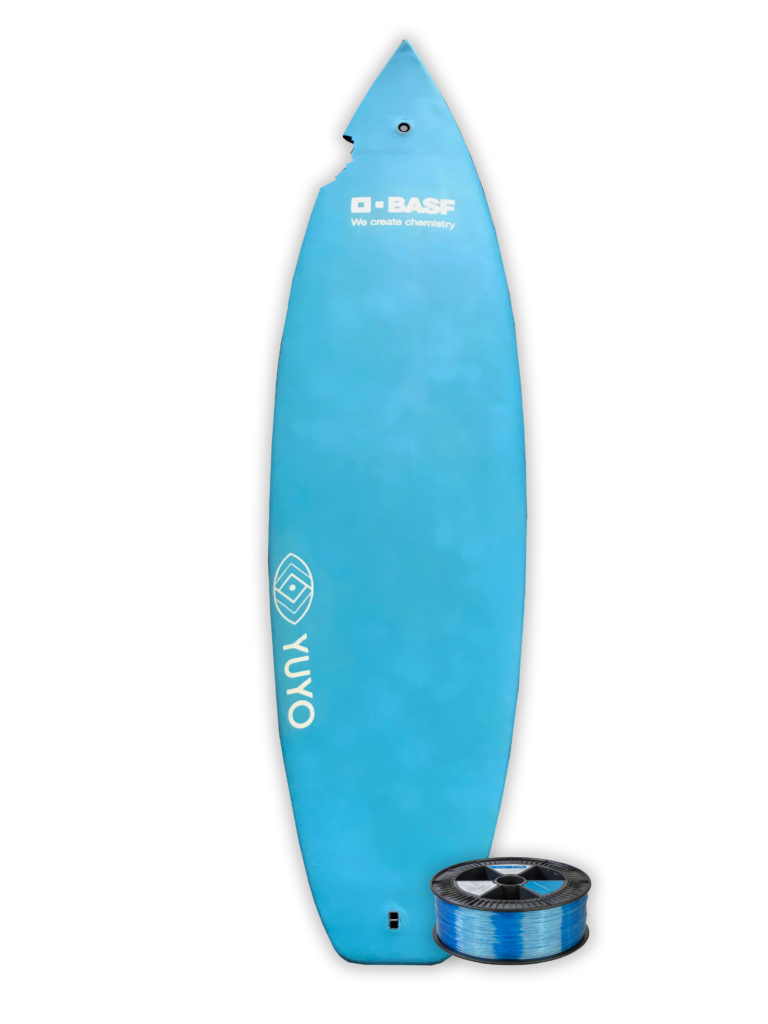
A surfboard from YUYO 3D printed from rPET. Image courtesy of BASF.
While any attempt to introduce sustainability to the world is worthy, it might be difficult to overlook the conglomerate’s larger role in the climate and biodiversity crises we’re currently facing. Of course, any large chemical company in the 3D printing industry will be involved in many of these same ecologically harmful practices, which is why a larger discussion about the role of plastics and 3D printing in a sustainable society needs to be had.
Meanwhile, BASF continues to expand its footprint in the additive space. It has partnered with countless firms in the industry while growing its portfolio of additive materials, including an interesting metal filament for desktop metal 3D printing. Its backing of Materialise and Essentium and acquisition of Sculpteo means that it is only becoming more and more important in additive manufacturing.
The post BASF Supplies Materials for Cincinnati Inc’s SAAM HT 3D Printer appeared first on 3DPrint.com | The Voice of 3D Printing / Additive Manufacturing.