3D Printing Industry News Sliced: Farsoon Technologies, Rize, Titomic, 3D Systems, Formlabs, Protolabs, Dassault Systèmes
Carbon Performance develops 3D printed brake calipers on new SK3L370N platform
Xometry receives ISO 9001:2015 and AS9100D Aerospace Quality Certification
Top 10 3D Printing Aerospace Stories from 2018
3D printing has played an important role in many industries over the past year, such as medical, education, and aerospace. It would take a very long time to list all of the amazing news in aerospace 3D printing in 2018, which is why we’ve chosen our top 10 stories for you about 3D printing in the aerospace industry and put them all in a single article.
Sintavia Received Approval to 3D Print Production Parts for Honeywell Aerospace
Tier One metal 3D printer manufacturer Sintavia LLC, headquartered in Florida, announced in January that it is the first company to receive internal approval to 3D print flightworthy production parts, using a powder bed fusion process, for OEM Honeywell Aerospace. Sintavia’s exciting approval covers all of Honeywell’s programs.
Boeing and Oerlikon Developing Standard Processes
Boeing, the world’s largest aerospace company, signed a five-year collaboration agreement with Swiss technology and engineering group Oerlikon to develop standard processes and materials for metal 3D printing. Together, the two companies will use the data resulting from their agreement to support the creation of standard titanium 3D printing processes, in addition to the qualification of AM suppliers that will produce metallic components through a variety of different materials and machines. Their research will focus first on industrializing titanium powder bed fusion, as well as making sure that any parts made with the process will meet the necessary flight requirements of both the FAA and the Department of Defense.
FITNIK Launched Operations in Russia
In 2017, FIT AG, a German provider of rapid prototyping and additive design and manufacturing (ADM) services, began working with Russian research and engineering company NIK Ltd. to open up the country’s market for aerospace additive manufacturing. FIT and NIK started a new joint venture company, dubbed FITNIK, which combines the best of what both companies offer. In the winter of 2018, FITNIK finally launched its operations in the strategic location of Zhukovsky, which is an important aircraft R&D center.
New Polymer 3D Printing Standards for Aerospace Industry
The National Institute for Aviation Research (NIAR) at Wichita State University (WSU), which is the country’s largest university aviation R&D institution, announced that it would be helping to create new technical standard documents for polymer 3D printing in the aerospace industry, together with the Polymer Additive Manufacturing (AMS AM-P) Subcommittee of global engineering organization SAE International. These new technical standard documents are supporting the industry’s interest in qualifying 3D printed polymer parts, as well as providing quality assurance provisions and technical requirements for the material feedstock characterization and FDM process that will be used to 3D print high-quality aerospace parts with Stratasys ULTEM 9085 and ULTEM 1010.
Premium AEROTEC Acquired APWORKS
Metal 3D printing expert and Airbus subsidiary APWORKS announced in April that it had been acquired as a subsidiary by aerostructures supplier Premium AEROTEC. Premium AEROTEC will be the sole shareholder, with APWORKS maintaining its own market presence as an independent company. Combining the two companies gave clients access to 11 production units and a wide variety of materials.
Gefertec’s Wire-Feed 3D Printing Developed for Aerospace
Gefertec, which uses wire as the feedstock for its patented 3DMP technology, worked with the Bremer Institut für Angewandte Strahltechnik GmbH (BIAS) to qualify its wire-feed 3D printing method to produce large structural aerospace components. The research took place as part of collaborative project REGIS, which includes several different partners from the aerospace industry, other research institutions, and machine manufacturers. Germany’s Federal Ministry for Economic Affairs and Energy funded the project, which investigated the influence of shielding gas content and heat input on the mechanical properties of titanium and aluminium components.
Research Into Embedded QR Codes for Aerospace 3D Printing
It’s been predicted that by 2021, 75% of new commercial and military aircraft will contain 3D printed parts, so it’s vitally important to find a way to ensure that 3D printed components are genuine, and not counterfeit. A group of researchers from the NYU Tandon School of Engineering came up with a way to protect part integrity by converting QR codes, bar codes, and other passive tags into 3D features that are hidden inside 3D printed objects. The researchers explained in a paper how they were able to embed the codes in a way that they would neither compromise the integrity of the 3D printed object or be obvious to any counterfeiters attempting to reverse engineer the part.
Lockheed Martin Received Contract for Developing Aerospace 3D Printing
Aerospace company Lockheed Martin, the world’s largest defense contractor, was granted a $5.8 million contract with the Office of Naval Research to help further develop 3D printing for the aerospace industry. Together, the two will investigate the use of artificial intelligence in training robots to independently oversee the 3D printing of complex aerospace components.
BeAM And PFW Aerospace Qualified 3D Printed Aerospace Component
BeAM, well-known for its Directed Energy Deposition (DED) technology, announced a new partnership with German company PFW Aerospace, which supplies systems and components for all civilian Airbus models and the Boeing 737 Dreamliner. Together, the two worked to qualify a 3D printed aerospace component, made out of the Ti6Al4V alloy, for a large civil passenger aircraft, in addition to industrializing BeAM’s DED process to manufacture series components and testing the applicability of the method to machined titanium components and complex welding designs.
Researchers Qualified 3D Printed Aerospace Brackets
Speaking of parts qualification, a team of researchers completed a feasibility study of the Thermoelastic Stress Analysis (TSA) on a titanium alloy space bracket made with Electron Beam Melting (EBM) 3D printing, in order to ensure that its mechanical behavior and other qualities were acceptable. The researchers developed a methodology, which was implemented on a titanium based-alloy satellite bracket.
Discuss these stories and other 3D printing topics at 3DPrintBoard.com or share your thoughts below.
3D Printing News Briefs: August 21, 2018
We’ve got plenty of business news for you in today’s 3D Printing News Briefs, and a little scientific research as well. Kelyniam Global has acquired new 3D printing technology, while Rostec makes an investment in technology. One of the earliest SpaceX employees is now an advisor for another aerospace company, the Youngstown Business Incubator has received a federal grant, and SAE International recently hosted a 3D printing webinar. Auburn University has been chosen as the site of a new National Center of Additive Manufacturing Excellence, and a new study discusses 4D printed elastic ceramics.
Kelyniam Global Adds New 3D Printing Capabilities
Using medical models for surgical pre-planning is almost a clinical standard these days. In an effort to increase its current medical modeling skills, custom 3D printed cranial implant manufacturer Kelyniam Global, which works with health systems and surgeons to improve cost-of-care and clinical outcomes, announced that it has expanded its 3D printing capabilities with the acquisition of new technology. This new technology aligns with the company’s reputation as a premium supplier of cranial implants requiring excellence in design and quick turnaround times.
“This state-of-the-art equipment will enable Kelyniam to produce certain medical models on the same 24-hour turnaround schedule we offer for cranial implants. The ability to rapidly print ultrahigh resolution models with high accuracy across our entire platform is a significant differentiator in our industry,” said Kelyniam COO Chris Breault.
Rostec Investing in Industrial 3D Printing Development
Russia’s state technologies corporation Rostec (also Rostek and Rostekh), which develops products for high-tech and communication systems, has invested nearly 3 billion rubles to create a specialized center for industrial 3D printing. The Center for Additive Technologies (CAC), with a goal of reducing the amount of time and money it takes to launch new products, will offer customers a full range of services and advanced 3D printers. The CAC’s main task will be introducing industrial 3D printing to high-tech industries that could really use it.
“Industrial 3D printing is becoming one of the indispensable attributes of modern industry. We see the high potential of this technology and introduce it into our production practice,” said Anatoly Serdyukov, the Industrial Director of the aviation cluster at Rostekh State Corporation. “For example, in the JDC today, about three tons of parts per year are produced by the additive technology method. The holding plans to widely use them in the serial production of promising Russian gas turbine engines, which will be certified in 2025 – 2030. The creation of a specialized center will expand the scope of this technology and produce parts for such industries as aircraft building, space, high technology medicine, automotive industry.”
Project participants calculate that the CAC’s first pilot batch of parts will be manufactured there sometime in 2019.
Former SpaceX Employee Becomes Advisor to Relativity Space
Aerospace company Relativity Space hopes to one day 3D print an entire rocket in an effort to lower the cost of space travel, and has been working hard to achieve this goal over the last few years. The company has fired up its 3D printed engine over 100 times so far, and just a few months ago received $35 million in Series B Funding. Now, Relativity Space has announced that Tim Buzza, one of the very first employees at SpaceX – another company working to 3D print rockets – is one of its official advisors.
Jordan Noone, Relativity Space Co-Founder, said “When I was at SpaceX, Tim’s stellar reputation for breadth and depth of engineering and operations was legendary in the industry.”
Buzza spent 12 years helping to develop SpaceX’s Falcon 9 rocket and Dragon spacecraft and will advise Relativity Space on organizing the company structure, launch site selection and trades, rocket architecture, structures and avionics, and more.
Federal Grant Awarded to Youngstown Business Incubator
The Youngstown Business Incubator (YBI) is about to receive some new 3D printing software and hardware, thanks to a federal grant. Recently, the Appalachian Regional Commission awarded $185,000 in federal funding to YBI. The new 3D printers and 3D printing software that the grant will fund, in addition to being a boon for YBI, will also help to strengthen its frequent area partners Youngstown State University (YSU) and America Makes.
“Each additional piece of equipment further strengthen us as a national and international leader in additive manufacturing technology and this is a key part of that process,” said Michael Hripko, YSU’s Associative Vice President for Research.
SAE International Recently Held Additive Manufacturing Webinar
Last week, global engineering organization SAE International hosted an hour-long additive manufacturing webinar, called “Considerations When Integrating Additive Manufacturing into Aerospace and Ground Vehicle Development and Production Environment,” for members of the mobility engineering community. The discussion, moderated by the organization’s Senior Global Product Manager Audra Ziegenfuss, was led by four guest speakers: Dr. John Hart, the Director of MIT’s Center for Additive and Digital Advanced Production Technologies (ADAPT); Bill Harris, a Technical Fellow with Lockheed Martin; and Adam Rivard, the Additive Manufacturing Director for LAI International, Inc.
Topics covered during SAE International’s webinar last week included novel AM methods that translate to automotive and aerospace applications, the risks involved in introducing 3D printed, flight-critical parts, and the anticipated timeline for general acceptance of 3D printed parts by aerospace customers.
Auburn University Site of New National Center of AM Excellence
Recently, Auburn University in Alabama, ASTM International, and NASA launched two new centers of excellence in additive manufacturing with the shared goal of speeding up research and development, standardization and innovation in 3D printing. Researchers at Auburn’s National Center for Additive Manufacturing Excellence (NCAME), will conduct interdisciplinary research, while also striving to grow effective collaboration between industry, government, academia, and not-for-profit.
“The Center of Excellence is going to facilitate us bringing together the best technical experts in industry, government, and academia, and that’s going to help us develop the very best standards for this emerging technology,” said Katharine Morgan, the President of ASTM International.
New Study On 4D Printed Elastic Ceramics
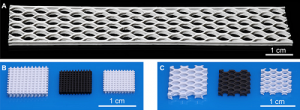
3D printing EDCs. (A) 3D printed large-scale elastomeric honeycomb. (B) 3D printed microlattices and (C) honeycombs of PDMS NCs and first EDCs and second EDCs.
Shape-morphing assembly is a great technology for applications in 4D printing, biomaterials, life sciences, and robotics, and multiple materials like ceramics, silicone, and polymers are used. But, we’ve not yet seen much in the way of ceramic structures derived from soft precursors that allow for elastic deformation. Polymer-derived ceramics (PDCs) have some excellent properties, such as high thermal stability and chemical resistance to oxidation and corrosion, and their microstructures can be fine-tuned through tailored polymer systems.
While we’re seeing a lot in the way of 3D printing soft materials, current ceramic precursors are not flexible and stretchable. Guo Liu, Yan Zhao, Ge Wu, and Jian Lu with the City University of Hong Kong published a paper, titled “Origami and 4D printing of elastomer-derived ceramic structures,” that explains how they developed silicone rubber matrix nanocomposites (NCs) that can be 3D printed and deformed into elastomer structures with complex shapes and transformed into mechanically strong EDCs.
The abstract reads, “Four-dimensional (4D) printing involves conventional 3D printing followed by a shape-morphing step. It enables more complex shapes to be created than is possible with conventional 3D printing. However, 3D-printed ceramic precursors are usually difficult to be deformed, hindering the development of 4D printing for ceramics. To overcome this limitation, we developed elastomeric poly(dimethylsiloxane) matrix nanocomposites (NCs) that can be printed, deformed, and then transformed into silicon oxycarbide matrix NCs, making the growth of complex ceramic origami and 4D-printed ceramic structures possible. In addition, the printed ceramic precursors are soft and can be stretched beyond three times their initial length. Hierarchical elastomer-derived ceramics (EDCs) could be achieved with programmable architectures spanning three orders of magnitude, from 200 μm to 10 cm. A compressive strength of 547 MPa is achieved on the microlattice at 1.6 g cm−3. This work starts a new chapter of printing high-resolution complex and mechanically robust ceramics, and this origami and 4D printing of ceramics is cost-efficient in terms of time due to geometrical flexibility of precursors. With the versatile shape-morphing capability of elastomers, this work on origami and 4D printing of EDCs could lead to structural applications of autonomous morphing structures, aerospace propulsion components, space exploration, electronic devices, and high-temperature microelectromechanical systems.”
Discuss these stories and other 3D printing topics at 3DPrintBoard.com or share your thoughts in the Facebook comments below.