VELO3D Releases Assure for 3D Metal Printing: Stratasys Direct Manufacturing as First Customer
With the release of the VELO3D Assure Quality Assurance and Control System for its Sapphire® 3D metal printers, VELO3D also brings on board a heavy hitter in their first customer as Stratasys Direct Manufacturing, a subsidiary of Stratasys, Ltd., will be the first to integrate Assure into their manufacturing processes.
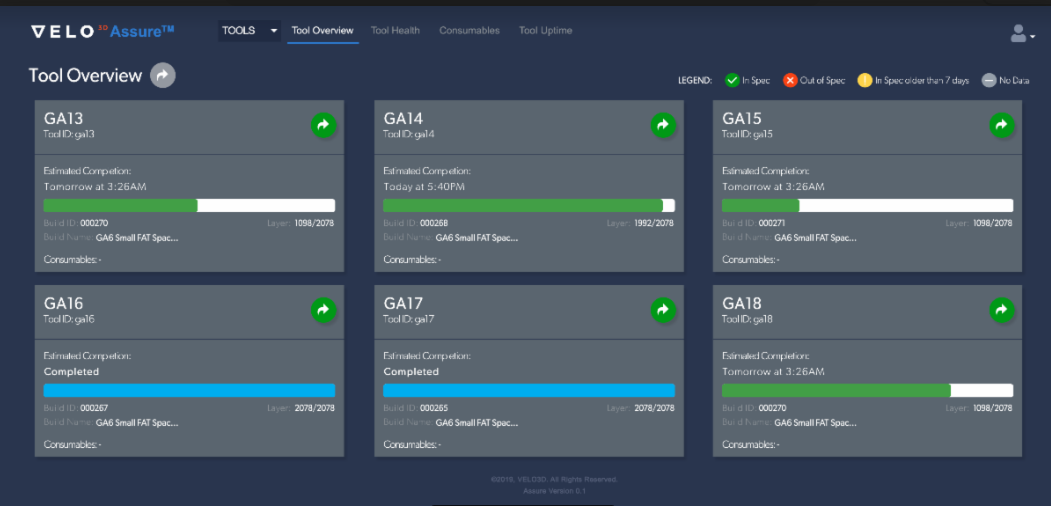
VELO3D’s Assure quality control dashboard enables engineers to track the quality and progress of Sapphire® machines in real-time.
Assure offers unprecedented monitoring and substantiation of part quality, offering the following features:
- Detects process anomalies
- Flags issues
- Highlights necessary corrective actions
- Offers traceability
“Assure is a revolutionary quality-control system, an inherent part of the VELO3D end-to-end manufacturing solution for serial production,” says Benny Buller, founder and CEO of VELO3D. “Assure is part of our vision to provide an integrated solution to produce parts by additive manufacturing with successful outcomes.”
Upon receipt of their own Sapphire 3D printer earlier this year, Stratasys Direct not only began using Assure, but they produced an entire study from their evaluation, which included:
- Monitoring integrity of builds
- Validating bulk material density
- Observing ongoing process metrics
- Verifying calibration of the system
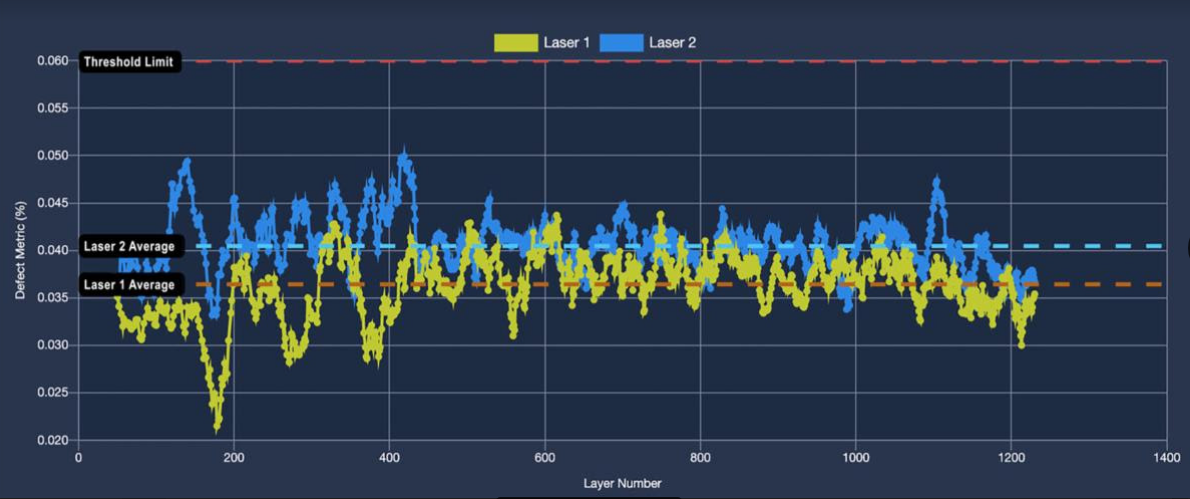
Assure predicts defectivity as a function of layer number. An increase in the defectivity metric is correlated with increasing defectivity in the bulk core of the part.
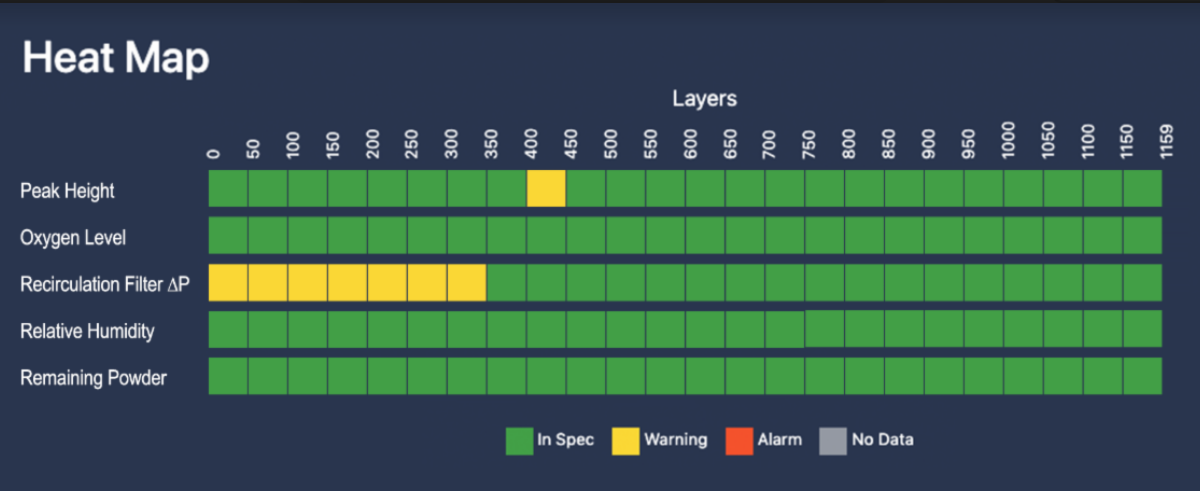
Before and during a build, Assure validates that critical parameters stay within control limits ensuring high quality parts. Clicking on individual squares reveals details on the underlying event.
These results were published in ‘Stratasys Direct Manufacturing Performs Field Validation of VELO3D Assure,’ after the Stratasys Direct team used Assure for 12 weeks, verifying findings produced by VELO3D. They are now using the system in ongoing production efforts.
“AM can print parts and meet requirements for single units but scaling from a single part into serial production has been challenging. OEMs lack confidence in AM process control, and AM users struggle to demonstrate it. Without visibility into each part’s deposition lifetime AM becomes a risk,” states author Andrew Carter, Sr. Manufacturing Engineer at Stratasys Direct Manufacturing.
Assure boosts manufacturing techniques for the user as they can understand tool health better, calculate part quality, and perform field validation. Engineers 3D printed test structures during their study, producing wedges measuring 20mm x 41mm in width and length respectively. The wedges could be stacked into a tower shape, making a structure to match the build z-height. For each test run, they created two towers.

Test structure added to production builds to enable destructive testing. Image from ‘Stratasys Direct Manufacturing Performs Field Validation of VELO3D Assure.’
Ultimately, 75 test structures were created and then analyzed via X-rays. Bulk porosity measured at 0.02 percent, and the researchers pointed out that there was no ‘single part exhibiting porosity higher than 0.1 percent. There were no deviations in print quality for the test builds.

Bulk defectivity measured on test parts by x-ray imagery. Image from ‘Stratasys Direct Manufacturing Performs Field Validation of VELO3D Assure
“Stratasys Direct has built a culture of continuous improvement that means we are continually setting new standards for our industry on quality,” said Kent Firestone, CEO of Stratasys Direct Manufacturing. “We integrated Assure into our quality control workflow because it produces highly actionable insights. The user interface features intuitive graphs and charts that enable us to see and interpret the vast amount of data collected during builds. This information helps our engineers verify the quality of the build each step of the way and enables them to make quick decisions in the event of an issue. Assure helps us reduce production variation, improve yields, and circumvent anomalies to ensure consistent additive manufacturing.”
If you are interested in finding out more about Assure, check out the webinar on November 14th at 10 am PST, offered by Stratasys Direct. Click here to register. Also, if you are attending formnext in Frankfurt, Germany, don’t miss the joint press conference at the VELO3D booth (Hall 11, E79) on November 19 at 10 a.m.
VELO3D continues to be a dynamic presence in the 3D printing realm, from fabrication of a supersonic flight demonstrator to their efforts to expand on design and build limitations. What do you think of this news? Let us know your thoughts! Join the discussion of this and other 3D printing topics at 3DPrintBoard.com.
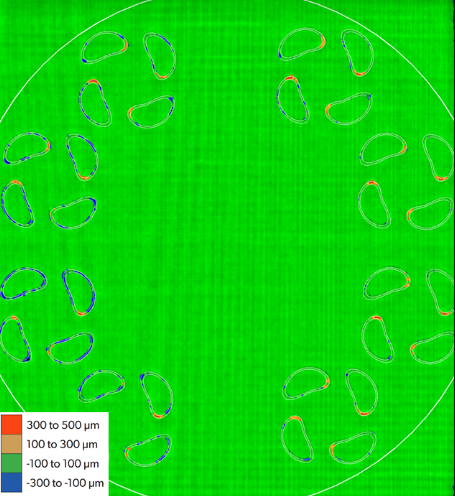
Assure provides true z-height quantitative powder bed and part metrology. Note the sections of parts with red lobes indicating metal protruding >300um above the powder bed but still below control limits.
[Source / Images: VELO3D]
The post VELO3D Releases Assure for 3D Metal Printing: Stratasys Direct Manufacturing as First Customer appeared first on 3DPrint.com | The Voice of 3D Printing / Additive Manufacturing.
3D Printing News Briefs: October 6, 2019
We’ve got lots of material news for you in today’s 3D Printing News Briefs, starting with a Material Development Kit from RPS. Polymaker and Covestro are releasing three new materials and EOS has introduced a new TPU material for industrial 3D printing. Moving on, CASTOR and Stanley Black & Decker used EOS 3D printing to reduce costs and lead time, and Velo3D is partnering with PWR to make high performance heat exchangers.
RPS Introduces Material Development Kit for NEO800
UK 3D printer manufacturer RPS just launched its NEO Material Development Kit, which was designed by company engineers to be used as a polymer research and development tool for its NEO800 SLA 3D printer. The MDK comes in multiple platform and vat sizes, and allows developers to work with different resin formulations, so that R&D companies can work to develop a range of polymers that are not available in today’s industry. Users can print single layer exposure panes with Titanium software and the 1 liter vat in order to find the photo-speed of the formulation they’re developing; then, tensile testing of different material formulations can commence. Once this initial testing is finished, developers can scale up to the 13 liter vat – perfect for 3D printing prototype parts for use in optimizing final configuration settings.
“This NEO Material Development Kit now opens the door for large industrial chemical companies such as BASF, DSM and Heinkel to push the boundaries of UV photopolymers,” said David Storey, the Director of RPS. “The industry is looking for a quantum jump in materials to print end-user production parts from the stereolithography process.”
New Polycarbonate-Based Materials by Polymaker and Covestro
Advanced 3D printing materials leader Polymaker and polymer company Covestro are teaming up to launch three polycarbonate-based materials. These versatile new materials coming to the market each have unique properties that are used often in a variety of different industries.
The first is PC-ABS, a polycarbonate and ABS blend which uses Covestro’s Bayblend family as its base material. Due to its high impact and heat resistance, this material is specialized for surface finishings such as metallization and electroplating, so it’s good for post-processing work. Polymaker PC-PBT, which blends the toughness and strength of polycarbonate with PBT’s high chemical resistance, is created from Covestro’s Makroblend family and performs well under extreme circumstances, whether it’s subzero temperatures or coming into contact with hydrocarbon-based chemicals. Finally, PolyMax PC-FR is a flame retardant material that’s based in Covestro’s Makrolon family and has a good balance between safety and mechanical performance – perfect for applications in aerospace motor mounts and battery housings.
EOS Offers New Flexible TPU Material
In another materials news, EOS has launched TPU 1301, a new flexible polymer for industrial, serial 3D printing. Available immediately, this thermoplastic polyurethane has high UV-stability, great resilience, and good hydrolysis resistance as well. TPU materials are often used in applications that require easy process capabilities and elastomeric properties, so this is a great step to take towards 3D printing mass production.
“The EOS TPU 1301 offers a great resilience after deformation, very good shock absorption, and very high process stability, at the same time providing a smooth surface of the 3D printed part,” said Tim Rüttermann, the Senior Vice President for Polymer Systems & Materials at EOS. “As such the material is particularly suited for applications in footwear, lifestyle and automotive – such as cushioning elements, protective gears, and shoe soles.”
You can see application examples for TPU 1301 at the EOS booth D31, hall 11.1, at formnext in Frankfurt next month, and the material will also be featured by the company at K Fair in Dusseldorf next week.
CASTOR, Stanley Black & Decker, and EOS Reduce Costs and Lead Time
Speaking of EOS, Stanley Black & Decker recently worked with Tel Aviv startup CASTOR to majorly reduce the lead time, and cost, for an end-use metal production part that was 3D printed on EOS machinery. This was the first time that 3D printing has been incorporated into the production line of Stanley Engineered Fastening. In a CASTOR video, EOS North America’s Business Development Manager Jon Walker explained that for most companies, the issue isn’t deciding if they want to use AM, but rather how and where to use it…which is where CASTOR enters.
“They have a very cool software in which we can just upload the part of the assembly CAD file, and within a matter of minutes, it can automatically analyze the part, and give us the feasibility of whether the part is suitable for additive manufacturing or not. And in case it is not suitable, it can also let us know why it is not suitable, and what needs to be changed. It can also tell us what is the approximate cost, which material and printer we can use,” said Moses Pezarkar, a Manufacturing Engineer at Stanley’s Smart Factory, in the video.
To learn more, check out the case study, or watch the video below:
PWR and Velo3D Collaborating on 3D Printed Heat Exchangers
Cooling solutions supplier PWR and Velo3D have entered into a collaborative materials development partnership for serial manufacturing of next-generation heat exchangers, and for the Sapphire metal 3D printer. PWR will be the first in the APAC region to have a production Sapphire machine, which it will use to explore high-performance thermal management strategies through 3D printing for multiple heat exchange applications. Together, the two companies will work on developing aluminum alloy designs with more complex, thinner heat exchange features.
“PWR chose Velo3D after extensive testing. The Velo3D Sapphire printer demonstrated the ability to produce class-leading thin-wall capabilities and high-quality surfaces with zero porosity. Velo3D and PWR share a passion for pushing the limits of technology to deliver truly disruptive, class-leading, products. We are a natural fit and look forward to building a strong partnership going forward,” said Matthew Bryson, the General Manager of Engineering for PWR.
“Heat exchanger weight and pressure-drop characteristics have a huge impact on performance and are significant factors in all motorsport categories. Using additive manufacturing to print lightweight structures, enhancing performance with freedom-of-design, we have the ability to further optimize these characteristics to the customer’s requirements whilst providing the necessary cooling. The broad design capabilities and extremely high print accuracy of the Velo3D Sapphire 3D metal printer will help us optimize these various performance attributes.”
Discuss these stories and other 3D printing topics at 3DPrintBoard.com or share your thoughts in the comments below.
The post 3D Printing News Briefs: October 6, 2019 appeared first on 3DPrint.com | The Voice of 3D Printing / Additive Manufacturing.
VELO3D ships largest order of Sapphire metal 3D printers to aerospace customer
Boom Supersonic Working with VELO3D to Make Metal 3D Printed Hardware for Supersonic Flight Demonstrator
Metal 3D printing startup VELO3D came out of stealth mode last year with its innovative, support-free laser powder bed fusion process that offers a lot more design freedom than most metal systems. Since the company commercialized in 2018, it’s made known that aerospace manufacturing is one of its largest target markets, and since that time at least two OEMs in that industry are using its Sapphire 3D printing systems to make parts. Now, it has just announced a partnership with Colorado-based Boom Supersonic – the company working to build the fastest supersonic airliner in history.
“Boom is reimagining the entire commercial aircraft experience, from the design, build, and materials used. Our technology is designed to help innovators like Boom rethink what’s possible, empower advanced designs with little or no post-processing, and enable an entirely new approach to production,” said VELO3D’s CEO Benny Buller. “Boom needed more than just prototypes and we’re thrilled to help them create the first 3D-printed metal parts for an aircraft that will move faster than the speed of sound.”
Boom, founded in 2014 and backed by several investors, employs over 130 people to help realize its vision: use supersonic travel to make the world significantly more accessible to the people who live in it. The company wants to bring businesses, families, and cultures closer together, and has recognized that 3D printing will help speed up the process. Recently, Boom renewed its existing partnership with Stratasys in order to create 3D printed parts for its XB-1 supersonic demonstrator aircraft, which is exactly what VELO3D will be doing as well.
“High-speed air travel relies on technology that is proven to be safe, reliable, and efficient, and by partnering with VELO3D we’re aligning ourselves with a leader in additive manufacturing that will print the flight hardware for XB-1. VELO3D helped us understand the capabilities and limitations of metal additive manufacturing and the positive impact it would potentially have on our supersonic aircraft,” said Mike Jagemann, the Head of XB-1 Production for Boom Supersonic. “We look forward to sharing details about the aircraft development and improved system performance once XB-1 takes flight.”
The 55-seat, Mach-2.2 (1,687 mph) aircraft is the first supersonic jet to be independently developed, and is made up of over 3,700 parts, combined with multiple advanced technologies, such as a refined delta wing platform, an efficient variable-geometry propulsion system, and advanced carbon fiber composites. Because the demonstrator aircraft – a validation platform called the “Baby Boom” – has such demanding precision, performance, and functional requirements in order to reliably provide safe and efficient travel, Boom is using VELO3D’s Intelligent Fusion technology to make the metal flight hardware for the jet, as it offers more design freedom, process control, and quality assurance; these qualities are essential in challenging design environments.
Boom is also working with VELO3D in order to leverage its customer support partnership, market expertise, and ability to guarantee consistent production quality. The supersonic flight company hopes that by utilizing metal 3D printing, it will be able to improve system performance and speed up the development of its XB-1 – which should eventually fly at twice the speed of sound – and any future aircraft as well.
The two companies have already conducted validation trials together, which were successful in their accurate performance and achieving the desired results. VELO3D developed two 3D printed titanium flight hardware parts, which will be part of the ECS system and make sure that the supersonic aircraft is able to conduct safe flights in any conditions; these parts will be installed on the prototype aircraft early next year.
In addition, the company also 3D printed some engine “mice” for Boom, which were used to validate the additive process.
“The mice allow for high engine operating line testing, ensuring we can achieve safe flight at all conditions,” Ryan Bocook, a manufacturing engineer at Boom Supersonic, said in a VELO3D blog post.
“The 3D printed mice helped Boom execute the test plan and validate predictions, and furthers the success of the program.”
These mice helped to facilitate testing, which included flow distortion simulation at the inlet, by decreasing the nozzle area in order to help simulate stall conditions while the engine is running from part power to mil power.
Not only did Boom Supersonic receive 3D printed flight hardware out of its partnership with VELO3D, but the company’s engineers also had the chance to familiarize themselves with the limitations and capabilities of 3D printing in terms of supersonic aircraft.
Discuss this story, and other 3D printing topics, at 3DPrintBoard.com, or share your thoughts in the Facebook comments below.
[Source/Images: VELO3D]