Companies, organizations and individuals continue to attempt to lend support to the COVID-19 pandemic supply effort. We will be providing regular updates about these initiatives where necessary in an attempt to ensure that the 3D printing community is aware of what is being done, what can be done and what shouldn’t be done to provide coronavirus aid.
At 12 pm on Monday, May 11th, 2020 America Makes, the U.S. Food and Drug Administration, the National Institute of Health, and the Veterans Affairs administration will be hosting a COVID-19 Response panel discussion, followed by a virtual networking reception. You can register for the event here.
Quant-U, a midsole printing project from Danish shoemaker ECCO and chemical giant Dow, has created 100 pairs of shoes with 3D-printed midsoles for medical workers at intensive care units at OLVG hospitals in Amsterdam. After 3D scanning the wearer’s feet and then capturing their walking data via wearable sensors, ECCO’s experimental shoe division 3D printed custom midsoles from Dow-produced silicon for staff who need to be on their feet for numerous throughout the day.
Siemens Mobility began using Stratasys 3D printers for printing spare parts for Russian Railways’ high-speed rail this February. The division is now testing 36 attachments for toilet and driver cab doors that make it possible to open train doors with an elbow or lower arm in order to reduce the spread of germs and the SARS-CoV-2 virus. Prototype parts are installed multiple Desire trains in the Moscow region.
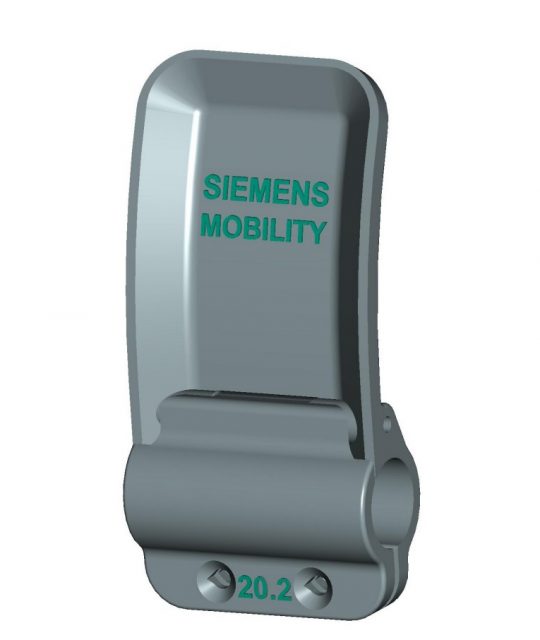
A hands-free door opener reportedly being used by Siemens Mobility. Image courtesy of Siemens Mobility.
An emergency working group dubbed the Sustainable Hub for Innovation, Execution, Launch and Distribution (SHIELD) is joining together experts in healthcare, 3D printing, engineering and construction to use additive manufacturing, injection molding and textiles manufacturing to get personal protection equipment to staff in the U.K. Makerversity in London has made over 30,000 face shields so far.
3D Systems posted its financial information for the quarter, reporting a 11.4 percent decline in revenue compared to last year at $134.7 million. This was pinned on the overall decline in manufacturing activity and industrial production, which reduced demand for its industrial products, while delays or cancellations of elective surgeries, such as dental, slowed consumption. Supply chain disruptions also led to issues with its facilities in China and Europe. Outgoing CEO Vyomesh Joshi said:
“COVID-19 has presented unprecedented challenges globally, so we asked our customers and partners to help address these challenges with 3D printing. Over the last several weeks we have seen applications of our technology and software being used to assist COVID-19 efforts, from ventilator parts to personal protection equipment to nasal swabs, which are all able to go from prototype to production in mere days, compared to what would normally take months using traditional supply chain and showcasing our true value proposition. Amid this uncertain environment we have managed the company by continuing to reduce expenses and preserving cash, and we believe we will be well-positioned when the market comes back.”
SLM Solutions has reported its earnings for Q1 2020, with revenues unaffected by the virus due to a backlog of orders from the end of 2019, causing a 143 percent increase in total revenue from €7.3 million Q1 2019 to €17.8 million in Q1 2020. However, the company has said that order intake for this most recent quarter was negatively impacted in that it sold the same number of machines Q1 2020 as it had in Q1 2019, with CEO Meddah Hadjar saying:
“While our first quarter was strong in terms of revenue generation, we started to feel the implications of the COVID19 pandemic in markedly lower order intake. The resulting economic slowdown hits some of SLM’s key end markets like the aircraft, the aero-engines, and the oil & gas industries.”
As the pandemic continues to grip the world, we will continue to provide regular updates about what the 3D printing community is doing in response. As always, it is important to keep safety in mind, remain critical about the potential marketing and financial interests behind seemingly good humanitarian efforts from businesses, and to do no harm.
The post 3D Printing and COVID-19, May 9, 2020 Update: NIH, Siemens, 3D Systems, SLM Solutions appeared first on 3DPrint.com | The Voice of 3D Printing / Additive Manufacturing.