3D Printed Cellular Fingers Offer Material Balance Required for Modern Robotics
In ‘Toward a Smart Compliant Robotic Gripper Equipped with 3D-Designed Cellular Fingers,’ authors Manpreet Kaur and Woo Soo Kim delve into the world of combining 3D printing and robotics. Their recently published paper focuses on the design of a robotic structure with deformable cellular structures that are easy to fabricate.
The conventional metal robot or robotic components are increasingly being upstaged by softer materials that offer more versatility for industrial applications. Not only that, many of these new materials are able to morph to their environment, affected by environments such as temperature or moisture. Kaur and Kim remind us that many of these innovations are originally inspired by nature, such as the movement of and the frictional properties of the snake.

Design and fabrication of multi‐material auxetic structure: A) 2D sketch of the re‐entrant honeycomb unit cell with defined parameters. B) Schematic demonstration of filament extrusion–based multi‐material 3D printing. C) Different designs of auxetic unit cells with two important parameters, α (the ratio of length of vertical strut h by re‐entrant strut l) and θ (the re‐entrant angle), defined in the sketch (A). D) The CAD image of the 3D re‐entrant honeycomb structure made by joining two 2D structures at 90°. The single tone gray color indicates the usage of a single material that is a TPU‐based flexible material. E) A dual‐material‐based auxetic unit cell where the re‐entrant struts (red) made of flexible material and the vertical struts (gray) made of rigid material. F) Different designs of dual‐material‐based auxetic unit cell, where the joints (gray) are made of flexible material and the rest of the portion of the struts (blue) are printed with the combination of both flexible and rigid material with equal proportion.
In creating soft robotics, however, there is the challenge of finding a balance between flexibility and structural stiffness and incorporating electronics which usually consist of a variety of different bulky systems. The cellular finger noted in this research can be made with embedded sensors in the fingertips, allowing for a significant gripping force of 16N, and the ability to pick up numerous objects—and acting as an example of more complex architectures for better functionality and performance overall.
“Stretching‐dominated cellular solids, such as octet, octahedral, and so on, show higher initial yield strength compared with bending‐dominated foamed materials, which is due to their different layout of structural components and makes them better alternatives for lightweight structural applications. One such unique spatially arranged structure produces a negative Poisson’s ratio (NPR); these are called auxetics. Like other types of mechanical metamaterials, the NPR of auxetics is generally a direct consequence of the topology, where the joints rotate to move the structure,” state the researchers.

Characterization of 3D printed auxetic structures: A) Compressed samples from the design with α = 1.5 and θ = −20°. Three different material distributions in the unit cell (single, dual 1, and dual 2 designs) are studied. Images were captured for each sample at 0%, 20%, and 40% strains. B) Stress–strain graph of three samples with different combinations of α = 1.5, 2 and θ = −20°, −30 ° for designs (single, dual 1, and dual 2). The legends read as “a” for alpha, “t” for theta, and S, D1, D2 for single, dual 1, and dual 2, respectively. C) Finite element analysis (FEA) simulation analysis of compressed auxetic unit cell to study the different stress distributions in the elastic region for the three different designs. The color code is kept constant and is defined next to each image. The corresponding elastic curves from experiment and simulation are compared for each case. D) The cellular finger is designed using the rigid stretching‐dominated octet structure for the main body and using chosen auxetic structure (α = 1.5 and θ = −20°) with dual 2 designs for the joints.
NPR materials are also able to deform and show ‘compliant-bending behavior.’ In this research project, Kaur and Kim used honeycomb structures—again, inspired by nature—examining their ability to absorb energy and bend. These re-entrant structures are more easily translated to the 3D realm and allowed the authors to experiment regarding parameters and resulting cell properties. The end goal was to achieve deformity, along with suitable durability and energy efficiency.
With the use of porous cellular materials meant to meet the balance of both softness and flexibility and the need for firmness also, the researchers were able to roll their knowledge of materials, manufacturing, and robotics into one—along with 3D printing and the use of triple materials. The robotic gripper finger was made up of the following lightweight parts:
- Three octet segments
- Two auxetic joints (mimicking human bones and joints)
- Integrated pressure sensor on the fingertip
The following materials were used for 3D printing the single, dual 1, and dual 2 designs: SemiFlex, PLA, and carbon fiber reinforced PLA (CFRPLA). The porosity level allowed for the sought-after balance in a lightweight structure as well as offering the proper rigidity for various gripping functions. The overall design was also responsible for the system of fingers able to deform as needed, in tune with objects and their specific shapes—while the fingertip sensors monitoring the environment.
“Our architectured robotic finger is a starting point of cellular design concept. Therefore, there is a lot of room for further research in this topic. Design of other mechanical metamaterials has lots of opportunities, so other lattice structures can be investigated to tune additional mechanical deformation functionality in the robotic finger,” concluded the researchers.
“The optimization of sensor design and addition of other sensors can also be investigated to achieve its ubiquitous performance. This compliant robotic design with metamaterial body can prove to enhance the functionality and durability of robotic bodies for prosthetic or industrial applications, thus developing new generation of robotic systems with better performance and greater adaptability in a variety of tasks.”
Robotics and 3D printing are paired up often these days, in projects ranging from uses in furniture manufacturing to soft robotics, and more. What do you think of this news? Let us know your thoughts! Join the discussion of this and other 3D printing topics at 3DPrintBoard.com.
[Source / Images: ‘Toward a Smart Compliant Robotic Gripper Equipped with 3D-Designed Cellular Fingers’]
The post 3D Printed Cellular Fingers Offer Material Balance Required for Modern Robotics appeared first on 3DPrint.com | The Voice of 3D Printing / Additive Manufacturing.
Purdue Researchers Create Soft Robotics Users Can Customize & Make Using 3D Printing
Researchers have patented promising new robotics technology created through the Purdue Office of Technology Commercialization, and outlined in ‘3D Architected Soft Machines with Topologically Encoded Motion.’ Authors Debkalpa Goswami, Shuai Liu, Aniket Pal, Lucas G. Silva, and Ramses V. Martinez have developed robotic devices that can be 3D printed and customized by users, depending on their needs.
This technology may both surprise and fascinate users, who in the past have expected robots to make things for them—but they may not have expected to be the ones creating the robots from home or the workshop. A 3D printed robot, while not completely able to protect users, can at least communicate with them, ask basic questions, and sense movement such as a fall, acting as a more complex panic button in these cases.
“Unfortunately, the external hard structure of current caregiving robots prevents them from a safe human-robot interaction, limiting their assistance to mere social interaction and not physical interaction,” said Ramses Martinez, assistant professor at the School of Industrial Engineering and in the Weldon School of Biomedical Engineering in Purdue’s College of Engineering. “After all, would you leave babies or physically or cognitively impaired old people in the hands of a robot?”
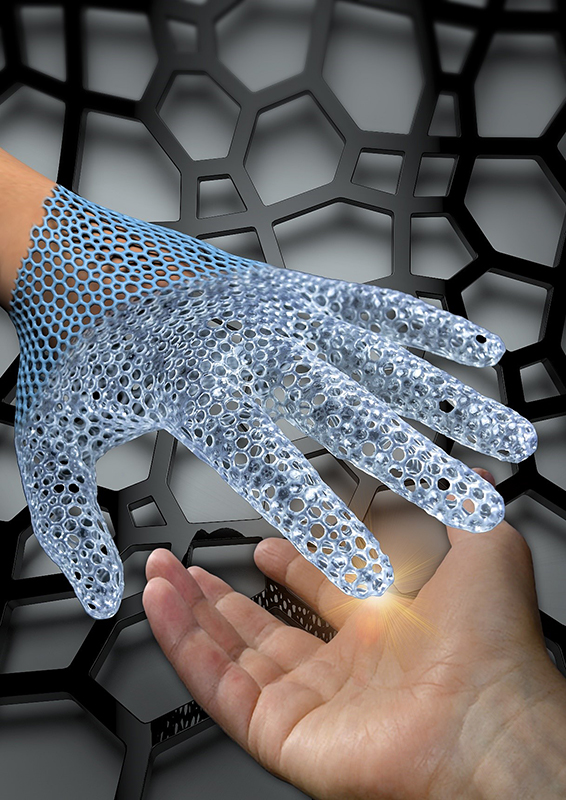
Purdue University researchers have developed a new design method to create soft robots (Artist rendering by Ramses Martinez)
Users can create their own CAD files, shaping the robot, and then designating what types of movements it will make. The researchers have created a customized algorithm that converts the data into a 3D architected soft machine (ASM). And indeed, this opens a brave new world to users everywhere as they can print the robots on virtually any 3D printer.
The fabricated ASMs can mimic human locomotion, operated with tiny motors that rely on nylon to pull the limbs back and forth. The researchers state that these customized robots and their soft materials can be stretched to beyond 900 percent of their initial length.
“ASMs can perform complex motions such as gripping or crawling with ease, and this work constitutes a step forward toward the development of autonomous and lightweight soft robots,” Martinez said. “The capability of ASMs to change their body configuration and gait to adapt to a wide variety of environments has the potential to not only improve caregiving but also disaster-response robotics.”
While users can 3D print customized robotics, the actual forms created move in the realm of the 4D, responding and morphing with their own environment. The researchers state that they can perform a wide range of motion, depending on need.
“The topological architecture of these low‐density soft robots confers them with the stiffness necessary to recover their original shape even after ultrahigh compression (400%) and extension (500%),” state the researchers in their paper. “ASMs expand the range of mechanical properties currently achievable by 3D printed or molded materials to enable the fabrication of soft machines with auxetic mechanical metamaterial properties.”
You don’t have to be an engineer or a techno-geek to understand that today (which used to be that distant, faraway future) has not yielded the type of progress we expected from robotics. And while we are not being served and accompanied 24/7 by charismatic androids, significant and interesting developments have certainly been achieved—from 3D printed robots that pick up trash for us, to construction robots—and even swarms of robots doing the 3D printing work for us. The picture may be different from what we imagined, but in the end—far more spectacular. Find out more about the recent research in soft robotics here, serving as part of the university’s Giant Leaps celebration in connection with their 150th anniversary.

Purdue researchers have developed a new design method that will enable anyone to quickly design and fabricate soft robots using a 3D printer (Photo credit: Purdue University)
What do you think of this news? Let us know your thoughts! Join the discussion of this and other 3D printing topics at 3DPrintBoard.com.
[Source / Images: Purdue University]
WATCH: the 3D printed soft robots working their way into medicine
Researchers Use Shape Memory Polymers to Increase Stiffness of 3D Printed Soft Actuators
While soft robots are very flexible, and adaptive to more complex environments, they aren’t great at completing tasks with a high load capacity due to the low stiffness of constituent materials. Attempts have been made to use variable stiffness materials and structures in order to develop stiffness‐tunable soft actuators, but these are limited by factors such as small deformations, slow responses, and difficulty fabricating microfeatures.
A team of researchers from the Singapore University of Technology and Design (SUTD) and Shanghai Jiao Tong University (STJU) recently published a paper, titled “Fast-Response, Stiffness-Tunable Soft Actuator by Hybrid Multimaterial 3D Printing,” detailing their efforts to fix this issue.
The abstract reads, “This work presents a paradigm to design and manufacture fast‐response, stiffness‐tunable (FRST) soft actuators via hybrid multimaterial 3D printing. The integration of a shape memory polymer layer into the fully printed actuator body enhances its stiffness by up to 120 times without sacrificing flexibility and adaptivity. The printed Joule‐heating circuit and fluidic cooling microchannel enable fast heating and cooling rates and allow the FRST actuator to complete a softening–stiffening cycle within 32 s. Numerical simulations are used to optimize the load capacity and thermal rates. The high load capacity and shape adaptivity of the FRST actuator are finally demonstrated by a robotic gripper with three FRST actuators that can grasp and lift objects with arbitrary shapes and various weights spanning from less than 10 g to up to 1.5 kg.”
The researchers used a Stratasys J750 PolyJet 3D printer to manufacture the four components for the actuator, using VeroClear and VeroBlack material.
“Once clean, the SMP slice I was taken to our self-built DIW device for the fabrication of the Joule-heating circuit,” the researchers wrote. “A syringe was held vertically on the DIW device, and its translations in the printing plane were enabled by linear stages…which were precisely controlled by stepper motors.”
The 3D printed SMP slice with the Joule-heating circuit was placed in a universal oven in order to sinter the Ag NP circuit before being bonded with the body of the actuator. In each spacer between neighboring air chambers in the actuator body, a slot was created in order to receive an insert for the SMP slice.
“The slot-and-insert design would enhance the bonding strength at the interface to better limit the cover layer’s strain under inflation and inhibit the air from travelling outside the central channel,” the researchers explained.
Once the bonding interfaces were cured, the team tested how airtight everything was, then inserted conductive wires through the actuator base’s channels, which were connected to the Joule-heating circuit and then sintered. The SMP slice II was bonded with the elastomeric sheet using VeroClear, and the processed parts were bonded together, again using VeroClear.
The researchers performed all kinds of tests on their 3D printed soft actuator, including a DMA test, tensile tests at 25 °C and 70 °C, a stiffness-tunable strip test, and others. A characterization test on a single FRST actuator’s load capacity was completed, and the team also conducted finite-element simulations in an effort to learn more about the stiffness variation mechanism.
The researchers wrote, “To gain insight on potential ways to improve the load capacity, we simulated the bending stiffness tests by varying two parameters, namely the SMP layer thickness and material modulus at room temperature.”
Finite-element simulations were also completed for heating and cooling tests, and the researchers also characterized the printing parameters.

Thermistor glued to innermost surface of SMP component with leads extending out from side edges of the actuator.
The field of soft robotics is helping people change their perception of robots as hard, metal creations to something that is more fluid and flexible. Through their experiments, the joint SUTD/STJU research team found that by adding shape memory polymers to the mix, their 3D printed soft actuator’s body became up to 120 times stiffer, but without sacrificing adaptivity or flexibility – making it far more effective at carrying high loads.
Co-authors of the paper are Yuan‐Fang Zhang, Ningbin Zhang, Hardik Hingorani, Ningyuan Ding, Dong Wang, Chao Yuan, Biao Zhang, Guoying Gu, and Qi Ge.
Discuss this research and other 3D printing topics at 3DPrintBoard.com or share your thoughts in the Facebook comments below.
Soft Robotic Sheets Can Make Inanimate Objects Move
Among 3D printing’s many applications, the technology often crosses over into the field of robotics, including soft robotics. Soft robotics is a field that has been changing the way people look at robots, taking them from rigid metal creations to something much more fluid and flexible. Applications include synthetic muscle, prosthetics, search and rescue tools, and more. Now researchers at Yale University are creating soft robots from everyday objects.
The researchers created “skins” by embedding sensors and remotely operated actuators into elastic sheets. When those skins were wrapped around objects, the objects could move, grasp, and even walk. A stuffed horse was able to move its legs when wrapped with the sheets, and a foam tube was able to squirm. The research is described in a paper entitled “OmniSkins: Robotic skins that turn inanimate objects into multifunctional robots.“
Rebecca Kramer-Bottiglio, Assistant Professor of Mechanical Engineering and Materials Science and leader of the research, said that the sheets could be used to create improvised robots that could be used in disaster situations, for example.
“A designer could quickly construct a robot using the robotic skins wrapped around whatever deformable materials they have access to and stick a camera on it, and then deploy the robot for exploration of small or dangerous spaces,” she said. “Robotic skins can be applied to, removed from, and transferred between different objects, and used in combination to create many different configurations to perform many different tasks.”
Kramer-Bottiglio and her colleagues plan to use 3D printing to build additional components for testing the robotic sheets, as well as creating clay structures that can morph into different shapes.
“I’m really excited to see what other people will do with robotic skins,” Kramer-Bottiglio said. “The possibilities are endless.”
The field of soft robotics encompasses a wide variety of production techniques, although 3D printing has been one of the most common methods of fabricating them. Soft robotics has the potential to eliminate many components from traditional robots, doing away with circuits and other clunky parts in favor of actuation by light or chemical reaction. With this new way of looking at robots, they can be made and activated more easily, and used in situations that involve small or unknown spaces.
“This is a very exciting study that demonstrates the versatility and adaptability of soft robotics,” said Conor Walsh, an Associate Professor of Engineering and Applied Sciences at Harvard University. “The idea that we can have a soft and flexible sheet, wrap it around any surface, have it learn what it is attached to and then move it in some desired way has lot of potential.”
Soft robots can be made out any number of flexible materials, but the researchers’ idea is novel in that it can transform ordinary objects into robots just by wrapping them in fabric. As Kramer-Bottiglio pointed out, this means that in an emergency situation, any flexible item that happened to be at hand could be quickly turned into a search and rescue bot – or, in a less urgent situation, kids could turn their favorite stuffed animals into companions that could move around the house. Whether that’s fun or creepy is a matter of opinion, but it’s hard to argue against this new method of robot creation as being potentially very useful in the future.
Authors of the paper include Joran W. Booth, Dylan Shah, Jennifer C. Case, Edward L. White, Michelle C. Yuen, Olivier C. Choiniere and Rebecca Kramer-Bottiglio.
Discuss this and other 3D printing topics at 3DPrintBoard.com or share your thoughts below.
Aether and UCLA Partner to Develop 3D Printed Artificial Muscles
Robots have come a long way, moving past their traditional image of stiff metal machines and becoming something much more varied and sophisticated. Soft robotics is an expanding field, leading to everything from virtual reality applications to artificial muscle. Artificial muscles are a promising development, with applications that include prosthetics, implants, drug delivery systems, and other medical devices, and they are the focus of a new collaboration between UCLA and bioprinting company Aether.
Aether and UCLA’s Henry Samueli School of Engineering will work together to develop technologies for faster, easier fabrication of soft artificial muscles and other multi-material structures. Aether will work on optimizing the Aether 1 bioprinter and its computer vision capabilities to automate the process of 3D printing soft robotic devices, improve print quality and ease of use.
Aether recently upgraded its automatic offset calibration system to make embedding conductive materials easier than ever before, using computer vision to automatically calculate precise offsets for multiple tools and tool types. This allows users to extrude multiple materials side by side without overlapping or gaps and enables conductive materials like graphene or silver nanoparticles to be printed directly into robotic devices, eliminating the need for wires.
Partnering with UCLA is personal for Aether CEO Ryan Franks, who caught pneumonia 10 years ago and was hospitalized at UCLA Hospital. He was healed thanks to a lifesaving procedure performed by Dr. Abbas Ardehali. The procedure was called VATS, or video-assisted thoracoscopic surgery, and it sparked Franks’ interest in medical technology, leading directly to the founding of Aether.
“Working on technology with UCLA is something I’ve dreamed of for a long time,” said Franks. “There’s no one better when it comes to robotics, and the fact that UCLA faculty saved my life makes this collaboration incredibly special.”

Aether Director of Engineering Marissa Buell (a fellow UCLA Engineering alumni), CEO Ryan Franks, and students at UCLA with Aether 1 beta unit [Image: Aether]
UCLA researchers will also join a collaboration between Aether and Harvard Medical School and will receive pre-release access to Aether’s upcoming advanced visualization AI software, featuring ASAR (Automatic Segmentation and Reconstruction) technology. ASAR allows users to view medical images like CT scans or X-rays. They can select a desired organ or tissue type and quickly obtain a segmented organ 3D file. The system simplifies medical analysis and saves time, allowing surrounding anatomy to be quickly removed for a clearer focus.
In 2019, Aether will launch software that will allow users to create 3D printable organs from medical images with the push of a button, and according to the company, it will be priced lower than competing software. Aether also states that the software is faster than that of competitors, taking only seconds to do what previously has taken hours or even days.
Aether also released a new video today that shows the Aether 1 printing an analog of a microfluidic device, using eight tools in one print. First, two FDM extruders print a substrate in two colors of PLA. Then, two colors of silicone are printed on the substrate as aboveground wells, which are then cured by the UV LED. A laser engraves two thin grooves in the PLA substrate to serve as belowground liquid channels. Two microvalves, each filled with a different color of water, then jet liquid into the two aboveground wells and belowground channels. You can see the video below:
Discuss this and other 3D printing topics at 3DPrintBoard.com or share your thoughts below.
3D Printing News Briefs: June 29, 2018
In today’s 3D Printing News Briefs (the last one this month, how is the summer going by so quickly?!), a few companies are announcing special honors and recognitions, and then we’re sharing stories stories about some interesting new 3D printing projects, and finally wrapping things up before the weekend with some business news. Renishaw’s Director of R&D has been honored by the Royal Academy of Engineering, while MakerBot earned an important designation for its 3D printing certification program for educators and Renovis Surgical Technologies received FDA approval for its new 3D printed implant. Festo is introducing three new bionic robots, one of which is partially 3D printed, and CINTEC is using 3D printing for its restoration of a famous government house. GE wants to use blockchains for 3D printing protection, and ExOne announced a global cost realignment.
Royal Academy of Engineering Honors Renishaw’s Chris Sutcliffe
Earlier this week, the Royal Academy of Engineering (RAE) awarded a Silver Medal to Professor Chris Sutcliffe, the Director of Research and Development of the Additive Manufacturing Products Division (AMPD) for global metrology company Renishaw. This award is given to recognize outstanding personal contributions to British engineering, and is given to no more than four people a year. The Silver Medal Sutcliffe received was in recognition of his part in driving the development of metal 3D printed implants in both human and veterinary surgery, and also celebrates his successful commercialization of 3D printed products with several companies, including Renishaw, and the University of Liverpool.
“Throughout my career I’ve worked hard to commercialise additive manufacturing technology. As well as AM’s benefit to the aerospace and automotive sectors, commercialisation of AM and associated technologies has been lifechanging for those with musculoskeletal diseases,” said Sutcliffe. “The award celebrates the successes of the engineers I have worked with to achieve this and I am grateful to receive the award to recognise our work.”
MakerBot’s Certification Program for Educators Gets Important Designation
One of the leaders in 3D printing for education is definitely MakerBot, which has sent its 3D printers to classrooms all over the world. Just a few months ago, the company launched a comprehensive, first of its kind 3D printing certification program, which trains educators to become 3D printing experts and create custom curriculum for STEAM classrooms. An independent review of the program showed that it meets the International Society for Technology in Education (ISTE) standards, and it has earned the prestigious ISTE Seal of Alignment from the accreditation body. In addition, a survey conducted over the last three years of over 2,000 MakerBot educators shows that the percentage of teachers reporting that MakerBot’s 3D printers met their classroom needs has doubled in just two years.
“This data shows that MakerBot isn’t just growing its user base in schools. We’re measurably improving teachers’ experiences using 3D printing,” said MakerBot CEO Nadav Goshen. “Much of this impressive teacher satisfaction is thanks to the effort we’ve put into solving real classroom problems—like the availability of 3D printing curriculum with Thingiverse Education, clear best practices with the MakerBot Educators Guidebook, and now training with the new MakerBot Certification program.”
Earlier this week, MakerBot exhibited its educator solutions at the ISTE Conference in Chicago.
FDA Grants Clearance for 3D Printed Interbody Spinal Fusion System
California-headquartered Renovis Surgical Technologies, Inc. announced that it has received 510(k) clearance from the FDA for its Tesera SA Hyperlordotic ALIF Interbody Spinal Fusion System. All Tesera implants are 3D printed, and use a proprietary, patent-pending design to create a porous, roughened surface structure, which maximizes biologic fixation, strength, and stability to allow for bone attachment and in-growth to the implant.
The SA implant, made with Renovis’s trabecular technology and featuring a four-screw design and locking cover plate, is a titanium stand-alone anterior lumbar interbody fusion system. They are available in 7˚, 12˚, 17˚, 22˚ and 28˚ lordotic angles, with various heights and footprints for proper lordosis and intervertebral height restoration, and come with advanced instrumentation that’s designed to decrease operative steps during surgery.
Festo Introduces Partially 3D Printed Bionic Robot
German company Festo, the robotics research of which we’ve covered before, has introduced its Bionic Learning Network’s latest project – three bionic robots inspired by a flic-flac spider, a flying fox, and a cuttlefish. The latter of these biomimetic robots, the BionicFinWave, is a partially 3D printed robotic fish that can autonomously maneuver its way through acrylic water-filled tubing. The project has applications in soft robotics, and could one day be developed for tasks like underwater data acquisition, inspection, and measurement.
The 15 oz robot propels itself forward and backward through the tubing using undulation forces from its longitudinal fins, while also communicating with and transmitting data to the outside world with a radio. The BionicFinWave’s lateral fins, molded from silicone, can move independently of each other and generate different wave patterns, and water-resistant pressure and ultrasound sensors help the robot register its depth and distance to the tube walls. Due to its ability to realize complex geometry, 3D printing was used to create the robot’s piston rod, joints, and crankshafts out of plastic, along with its other body elements.
Cintec Using 3D Printing on Restoration Work of the Red House
Cintec North America, a leader in the field of structural masonry retrofit strengthening, preservation, and repair, completes structural analysis and design services for projects all around the world, including the Egyptian Pyramids, Buckingham Palace, Canada’s Library of Parliament, and the White House. Now, the company is using 3D printing in its $1 million restoration project on the historic Red House, which is also known as the seat of Parliament for the Republic of Trinidad and Tobago and was built between 1844 and 1892.
After sustaining damage from a fire, the Red House, featuring signature red paint and Beaux-Arts style architecture, was refurbished in 1904. In 2007, Cintec North America was asked to advise on the required repairs to the Red House, and was given permission to install its Reinforcing Anchor System. This landmark restoration project – the first where Cintec used 3D printing for sacrificial parts – denotes an historic moment in structural engineering, because one of the reinforcement anchors inserted into the structure, measuring 120 ft, is thought to be the longest in the world.
GE Files Patent to Use Blockchains For 3D Printing Protection
According to a patent filing recently released by the US Patent and Trademark Office (USPTO), industry giant GE wants to use a blockchain to verify the 3D printed parts in its supply chain and protect itself from fakes. If a replacement part for an industrial asset is 3D printed, anyone can reproduce it, so end users can’t verify its authenticity, and if it was made with the right manufacturing media, device, and build file. In its filing, GE, which joined the Blockchain in Transport Alliance (BiTA) consortium in March, outlined a method for setting up a database that can validate, verify, and track the manufacturing process, by integrating blockchains into 3D printing.
“It would therefore be desirable to provide systems and methods for implementing a historical data record of an additive manufacturing process with verification and validation capabilities that may be integrated into additive manufacturing devices,” GE stated in the patent filing.
ExOne to Undergo Global Cost Realignment
3D printer and printed products provider ExOne has announced a global cost realignment program, in order to achieve positive earnings and cash flow in 2019. In addition to maximizing efficiency through aligning its capital resources, ExOne’s new program will be immediately reducing the company’s consulting projects and headcount – any initial employee reductions will take place principally in consulting and select personnel. The program, which has already begun, will focus first on global operations, with an emphasis on working capital initiatives, production overhead, and general and administrative spending. This program will continue over the next several quarters.
“With the essential goal of significantly improving our cash flows in 2019, we have conducted a review of our cost structure and working capital practices. We are evaluating each position and expense within our organization, with the desire to improve productivity. As a result, we made the difficult decision to eliminate certain positions within ExOne, reduce our spending on outside consultants and further rely on some of our recently instituted and more efficient processes,” explained S. Kent Rockwell, ExOne’s Chairman and CEO. “Additional cost analyses and changes to business practices to improve working capital utilization will be ongoing over the next several quarters and are expected to result in additional cost reductions and improved cash positions. All the while, we remain focused on our research and development goals and long-term revenue growth goals, which will not be impacted by these changes, as we continue to lead the market adoption of our binder jetting technology.”
Discuss these stories, and other 3D printing topics, at 3DPrintBoard.com or share your thoughts in the Facebook comments below.