3D Printed Cellular Fingers Offer Material Balance Required for Modern Robotics
In ‘Toward a Smart Compliant Robotic Gripper Equipped with 3D-Designed Cellular Fingers,’ authors Manpreet Kaur and Woo Soo Kim delve into the world of combining 3D printing and robotics. Their recently published paper focuses on the design of a robotic structure with deformable cellular structures that are easy to fabricate.
The conventional metal robot or robotic components are increasingly being upstaged by softer materials that offer more versatility for industrial applications. Not only that, many of these new materials are able to morph to their environment, affected by environments such as temperature or moisture. Kaur and Kim remind us that many of these innovations are originally inspired by nature, such as the movement of and the frictional properties of the snake.

Design and fabrication of multi‐material auxetic structure: A) 2D sketch of the re‐entrant honeycomb unit cell with defined parameters. B) Schematic demonstration of filament extrusion–based multi‐material 3D printing. C) Different designs of auxetic unit cells with two important parameters, α (the ratio of length of vertical strut h by re‐entrant strut l) and θ (the re‐entrant angle), defined in the sketch (A). D) The CAD image of the 3D re‐entrant honeycomb structure made by joining two 2D structures at 90°. The single tone gray color indicates the usage of a single material that is a TPU‐based flexible material. E) A dual‐material‐based auxetic unit cell where the re‐entrant struts (red) made of flexible material and the vertical struts (gray) made of rigid material. F) Different designs of dual‐material‐based auxetic unit cell, where the joints (gray) are made of flexible material and the rest of the portion of the struts (blue) are printed with the combination of both flexible and rigid material with equal proportion.
In creating soft robotics, however, there is the challenge of finding a balance between flexibility and structural stiffness and incorporating electronics which usually consist of a variety of different bulky systems. The cellular finger noted in this research can be made with embedded sensors in the fingertips, allowing for a significant gripping force of 16N, and the ability to pick up numerous objects—and acting as an example of more complex architectures for better functionality and performance overall.
“Stretching‐dominated cellular solids, such as octet, octahedral, and so on, show higher initial yield strength compared with bending‐dominated foamed materials, which is due to their different layout of structural components and makes them better alternatives for lightweight structural applications. One such unique spatially arranged structure produces a negative Poisson’s ratio (NPR); these are called auxetics. Like other types of mechanical metamaterials, the NPR of auxetics is generally a direct consequence of the topology, where the joints rotate to move the structure,” state the researchers.

Characterization of 3D printed auxetic structures: A) Compressed samples from the design with α = 1.5 and θ = −20°. Three different material distributions in the unit cell (single, dual 1, and dual 2 designs) are studied. Images were captured for each sample at 0%, 20%, and 40% strains. B) Stress–strain graph of three samples with different combinations of α = 1.5, 2 and θ = −20°, −30 ° for designs (single, dual 1, and dual 2). The legends read as “a” for alpha, “t” for theta, and S, D1, D2 for single, dual 1, and dual 2, respectively. C) Finite element analysis (FEA) simulation analysis of compressed auxetic unit cell to study the different stress distributions in the elastic region for the three different designs. The color code is kept constant and is defined next to each image. The corresponding elastic curves from experiment and simulation are compared for each case. D) The cellular finger is designed using the rigid stretching‐dominated octet structure for the main body and using chosen auxetic structure (α = 1.5 and θ = −20°) with dual 2 designs for the joints.
NPR materials are also able to deform and show ‘compliant-bending behavior.’ In this research project, Kaur and Kim used honeycomb structures—again, inspired by nature—examining their ability to absorb energy and bend. These re-entrant structures are more easily translated to the 3D realm and allowed the authors to experiment regarding parameters and resulting cell properties. The end goal was to achieve deformity, along with suitable durability and energy efficiency.
With the use of porous cellular materials meant to meet the balance of both softness and flexibility and the need for firmness also, the researchers were able to roll their knowledge of materials, manufacturing, and robotics into one—along with 3D printing and the use of triple materials. The robotic gripper finger was made up of the following lightweight parts:
- Three octet segments
- Two auxetic joints (mimicking human bones and joints)
- Integrated pressure sensor on the fingertip
The following materials were used for 3D printing the single, dual 1, and dual 2 designs: SemiFlex, PLA, and carbon fiber reinforced PLA (CFRPLA). The porosity level allowed for the sought-after balance in a lightweight structure as well as offering the proper rigidity for various gripping functions. The overall design was also responsible for the system of fingers able to deform as needed, in tune with objects and their specific shapes—while the fingertip sensors monitoring the environment.
“Our architectured robotic finger is a starting point of cellular design concept. Therefore, there is a lot of room for further research in this topic. Design of other mechanical metamaterials has lots of opportunities, so other lattice structures can be investigated to tune additional mechanical deformation functionality in the robotic finger,” concluded the researchers.
“The optimization of sensor design and addition of other sensors can also be investigated to achieve its ubiquitous performance. This compliant robotic design with metamaterial body can prove to enhance the functionality and durability of robotic bodies for prosthetic or industrial applications, thus developing new generation of robotic systems with better performance and greater adaptability in a variety of tasks.”
Robotics and 3D printing are paired up often these days, in projects ranging from uses in furniture manufacturing to soft robotics, and more. What do you think of this news? Let us know your thoughts! Join the discussion of this and other 3D printing topics at 3DPrintBoard.com.
[Source / Images: ‘Toward a Smart Compliant Robotic Gripper Equipped with 3D-Designed Cellular Fingers’]
The post 3D Printed Cellular Fingers Offer Material Balance Required for Modern Robotics appeared first on 3DPrint.com | The Voice of 3D Printing / Additive Manufacturing.
Purdue Researchers Create Soft Robotics Users Can Customize & Make Using 3D Printing
Researchers have patented promising new robotics technology created through the Purdue Office of Technology Commercialization, and outlined in ‘3D Architected Soft Machines with Topologically Encoded Motion.’ Authors Debkalpa Goswami, Shuai Liu, Aniket Pal, Lucas G. Silva, and Ramses V. Martinez have developed robotic devices that can be 3D printed and customized by users, depending on their needs.
This technology may both surprise and fascinate users, who in the past have expected robots to make things for them—but they may not have expected to be the ones creating the robots from home or the workshop. A 3D printed robot, while not completely able to protect users, can at least communicate with them, ask basic questions, and sense movement such as a fall, acting as a more complex panic button in these cases.
“Unfortunately, the external hard structure of current caregiving robots prevents them from a safe human-robot interaction, limiting their assistance to mere social interaction and not physical interaction,” said Ramses Martinez, assistant professor at the School of Industrial Engineering and in the Weldon School of Biomedical Engineering in Purdue’s College of Engineering. “After all, would you leave babies or physically or cognitively impaired old people in the hands of a robot?”
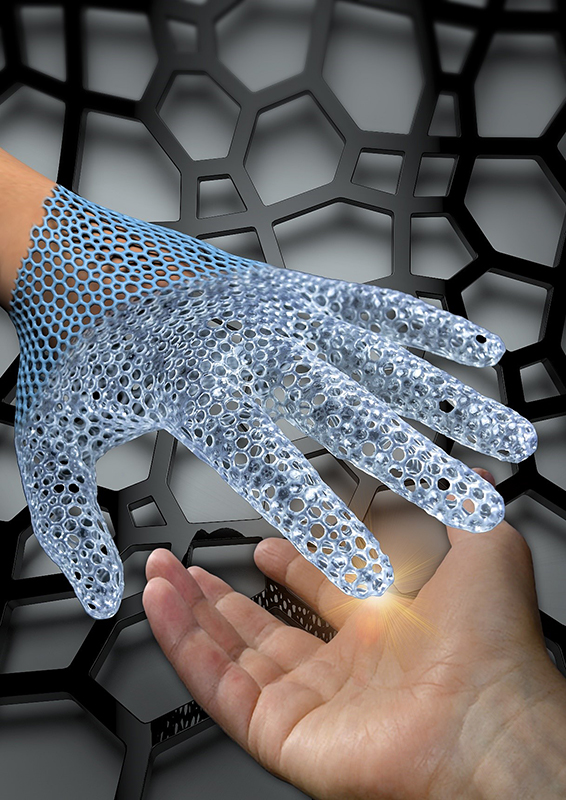
Purdue University researchers have developed a new design method to create soft robots (Artist rendering by Ramses Martinez)
Users can create their own CAD files, shaping the robot, and then designating what types of movements it will make. The researchers have created a customized algorithm that converts the data into a 3D architected soft machine (ASM). And indeed, this opens a brave new world to users everywhere as they can print the robots on virtually any 3D printer.
The fabricated ASMs can mimic human locomotion, operated with tiny motors that rely on nylon to pull the limbs back and forth. The researchers state that these customized robots and their soft materials can be stretched to beyond 900 percent of their initial length.
“ASMs can perform complex motions such as gripping or crawling with ease, and this work constitutes a step forward toward the development of autonomous and lightweight soft robots,” Martinez said. “The capability of ASMs to change their body configuration and gait to adapt to a wide variety of environments has the potential to not only improve caregiving but also disaster-response robotics.”
While users can 3D print customized robotics, the actual forms created move in the realm of the 4D, responding and morphing with their own environment. The researchers state that they can perform a wide range of motion, depending on need.
“The topological architecture of these low‐density soft robots confers them with the stiffness necessary to recover their original shape even after ultrahigh compression (400%) and extension (500%),” state the researchers in their paper. “ASMs expand the range of mechanical properties currently achievable by 3D printed or molded materials to enable the fabrication of soft machines with auxetic mechanical metamaterial properties.”
You don’t have to be an engineer or a techno-geek to understand that today (which used to be that distant, faraway future) has not yielded the type of progress we expected from robotics. And while we are not being served and accompanied 24/7 by charismatic androids, significant and interesting developments have certainly been achieved—from 3D printed robots that pick up trash for us, to construction robots—and even swarms of robots doing the 3D printing work for us. The picture may be different from what we imagined, but in the end—far more spectacular. Find out more about the recent research in soft robotics here, serving as part of the university’s Giant Leaps celebration in connection with their 150th anniversary.

Purdue researchers have developed a new design method that will enable anyone to quickly design and fabricate soft robots using a 3D printer (Photo credit: Purdue University)
What do you think of this news? Let us know your thoughts! Join the discussion of this and other 3D printing topics at 3DPrintBoard.com.
[Source / Images: Purdue University]
Soft Robotic Sheets Can Make Inanimate Objects Move
Among 3D printing’s many applications, the technology often crosses over into the field of robotics, including soft robotics. Soft robotics is a field that has been changing the way people look at robots, taking them from rigid metal creations to something much more fluid and flexible. Applications include synthetic muscle, prosthetics, search and rescue tools, and more. Now researchers at Yale University are creating soft robots from everyday objects.
The researchers created “skins” by embedding sensors and remotely operated actuators into elastic sheets. When those skins were wrapped around objects, the objects could move, grasp, and even walk. A stuffed horse was able to move its legs when wrapped with the sheets, and a foam tube was able to squirm. The research is described in a paper entitled “OmniSkins: Robotic skins that turn inanimate objects into multifunctional robots.“
Rebecca Kramer-Bottiglio, Assistant Professor of Mechanical Engineering and Materials Science and leader of the research, said that the sheets could be used to create improvised robots that could be used in disaster situations, for example.
“A designer could quickly construct a robot using the robotic skins wrapped around whatever deformable materials they have access to and stick a camera on it, and then deploy the robot for exploration of small or dangerous spaces,” she said. “Robotic skins can be applied to, removed from, and transferred between different objects, and used in combination to create many different configurations to perform many different tasks.”
Kramer-Bottiglio and her colleagues plan to use 3D printing to build additional components for testing the robotic sheets, as well as creating clay structures that can morph into different shapes.
“I’m really excited to see what other people will do with robotic skins,” Kramer-Bottiglio said. “The possibilities are endless.”
The field of soft robotics encompasses a wide variety of production techniques, although 3D printing has been one of the most common methods of fabricating them. Soft robotics has the potential to eliminate many components from traditional robots, doing away with circuits and other clunky parts in favor of actuation by light or chemical reaction. With this new way of looking at robots, they can be made and activated more easily, and used in situations that involve small or unknown spaces.
“This is a very exciting study that demonstrates the versatility and adaptability of soft robotics,” said Conor Walsh, an Associate Professor of Engineering and Applied Sciences at Harvard University. “The idea that we can have a soft and flexible sheet, wrap it around any surface, have it learn what it is attached to and then move it in some desired way has lot of potential.”
Soft robots can be made out any number of flexible materials, but the researchers’ idea is novel in that it can transform ordinary objects into robots just by wrapping them in fabric. As Kramer-Bottiglio pointed out, this means that in an emergency situation, any flexible item that happened to be at hand could be quickly turned into a search and rescue bot – or, in a less urgent situation, kids could turn their favorite stuffed animals into companions that could move around the house. Whether that’s fun or creepy is a matter of opinion, but it’s hard to argue against this new method of robot creation as being potentially very useful in the future.
Authors of the paper include Joran W. Booth, Dylan Shah, Jennifer C. Case, Edward L. White, Michelle C. Yuen, Olivier C. Choiniere and Rebecca Kramer-Bottiglio.
Discuss this and other 3D printing topics at 3DPrintBoard.com or share your thoughts below.