Usually when we’re talking about 3D printing in terms of acoustics, it has to do with making a good set of speakers. But, recent research has determined that acoustic signal processing could be used to monitor the build quality of a 3D printed part while in progress. There are 3D printable sound-shaping super-materials, and 3D printed objects have even been implanted with sound data for tagging purposes. New research out of Nanyang Technological University (NTU) in Singapore looks at using acoustics to manipulate microparticles inside the actual 3D printing ink itself to improve the final object’s performance and functionality.
Properly orienting and aligning the fibers in a polymer matrix could help transfer loads from critical areas for better performance, and creating 3D scaffolds with a controlled hierarchical structure at the nano- and micro-scale levels could increase their mechanical strength, which is good for cell and tissue regeneration and load-bearing bone defect repair. In addition, using surface acoustic waves to focus microparticles inside the microchannel could delay accumulation on the wall, which can improve extrusion-based 3D printing.
Researchers from NTU recently published a paper on their 3D printing work with acoustics, titled “Cells alignment and accumulation using acoustic nozzle for 3D printing.”
The abstract reads, “Arrangement or patterning of microparticles/cells would enhance the efficiency, performance, and function of the printed construct. This could be utilized in various applications such as fibers reinforced polymer matrix, hydrogel scaffold, and 3D printed biological samples. Magnetic manipulation and dielectrophoresis have some drawbacks, such as time-consuming and only valid for samples with specific physical properties. Here, acoustic manipulation of microparticles in the cylindrical glass nozzle is proposed to produce a structural vibration at the specific resonant frequency. With the acoustic excitation, microparticles were accumulated at the center of the nozzle and consequently printed construct at the fundamental frequency of 871 kHz. The distribution of microparticles fits well with a Gaussian distribution. In addition, C2C12 cells were also patterned by the acoustic waves inside the cylindrical glass tube and in the printed hydrogel construct. Overall, the proposed acoustic approach is able to accumulate the microparticles and biological cells in the printed construct at a low cost, easy configuration, low power, and high biocompatibility.”
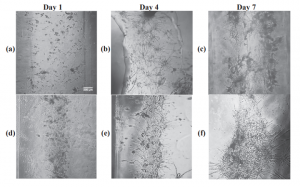
Morphology and distribution of the cells in 5% GelMA without the acoustic excitation on (a) day 1, (b) day 4, (c) day 7, and with the acoustic excitation on (d) day 1,(e) day 4, (f) day 7.
The team numerically and experimentally studied the structural vibration of a cylindrical tube, as well as the patterning of the microparticles and cells inside of it.
“Firstly, the resonant frequency was numerically predicted and validated with experiment,” the researchers wrote. “Subsequently, the distribution of microparticles and biological cells inside the cylindrical tube and printed construct was investigated. Lastly, the growth of biological cells undergone the acoustic excitation was monitored for up to 7 days.”
During an acoustic excitation, a mixture of C2C12 cells embedded in 2 ml of 5% GelMA was printed on a 4″ petri dish, with the nozzle perpendicular to the print bed. The researchers discovered that during the excitation, most of the microparticles that were initially suspended in fluid ended up accumulating at the center of the glass tube. There seemed to be a good overall agreement between the experimental results and numerical simulation of the excitation frequency, along with the location of pressure nodes in the glass tube.
The researchers further evaluated their acoustic nozzle’s performance using C2C12 muscle cells, and determined that without the excitation during printing, the distribution of the cells in the tube was very random.

Microparticle distribution in the cylindrical tube (a) without and (b) with the acoustic excitation at 877 kHz.
“Results of simulation and experiment are agreeable with a slight difference in the resonant frequency (< 2%). In the experiment, microparticles were accumulated at the center of the nozzle and consequently printed construct. The distribution of microparticles fits well in a Gaussian curve with a standard deviation of (V = 0.16 mm). Furthermore, the acoustic excitation could also be used for patterning biological cells in the 3D printed construct of GelMA,” the researchers concluded. “Subsequently, the distribution of cells was quite dense at the center of the printed structure, and accumulated C2C12 cells had greater growth and differentiation in comparison to the suspended ones in the control group.”
Co-authors of the paper are Yannapol Sriphutkiat, Surasak Kasetsirikul, Dettachai Ketpun, and Yufeng Zhou.
Discuss this research and other 3D printing topics at 3DPrintBoard.com or share your thoughts below.