On its first launch, NASA‘s uncrewed Space Launch System (SLS) mega-rocket will go on a trip around the Moon as part of the initial test flight for the Artemis 1 mission. It will mark the beginning of one of the most talked-about space programs this year, Artemis, an ongoing government-funded crewed spaceflight initiative with the goal of landing the first woman and the next man on the Moon by 2024, particularly, on the lunar south pole region. The most powerful rockets ever built, the SLS is in turn powered by four super engines that are designed to handle some of the most extreme temperatures as they move massive amounts of propellants to generate enough energy for the rocket to escape Earth’s gravity.
As part of a years-long working relationship with NASA, Aerojet Rocketdyne of Sacramento, California, will be building a total of 24 RS-25 rocket engines to support as many as six SLS flights for a total contract value of almost $3.5 billion. Originally slated to produce six new RS-25 engines, the company has recently been awarded a $1.79 billion contract modification to build 18 additional RS-25 rocket engines to support future deep space exploration missions.
“This contract allows NASA to work with Aerojet Rocketdyne to build the rocket engines needed for future missions,” said John Honeycutt, the SLS program manager at NASA’s Marshall Space Flight Center in Huntsville, Alabama. “The same reliable engines that launched more than 100 space shuttle missions have been modified to be even more powerful to launch the next astronauts who will set foot on the lunar surface during the Artemis missions.”
Although the Space Shuttle Endeavour is now at a museum exhibit at the California Science Center in Los Angeles, its engines—along with those that used to power space shuttles Discovery and Atlantis—have been maintained for SLS. However, unlike the shuttles, SLS will not reuse its engines. Once the core stage falls away at around eight minutes after launch, the engines will disintegrate during reentry. There are currently 16 RS-25 engines remaining from NASA’s Space Shuttle Program that Aerojet Rocketdyne has upgraded, tested, and that are ready to support the first four SLS missions. Yet, with more SLS missions expected to launch well into the end of the decade, Aerojet Rocketdyne has been asked to build more engines; actually, six new expendable RS-25 engines are already being assembled using advanced manufacturing techniques, including 3D printing, that reduces both the cost and time for manufacturing each engine.
The additional 18 engines will continue to leverage supply chain optimization and the incorporation of additive manufacturing (AM) techniques that were already introduced in the initial SLS engine production.
Employing AM technology to reduce costs and improve the efficiency of its engines is among the top priorities of the aerospace and defense company. Aerojet Rocketdyne’s senior engineer on the Additive Manufacturing team, Alan Fung, told 3DPrint.com that hundreds of people have been working on the design, development, and manufacture of the engines which relies mainly on laser powder bed fusion technology to additively manufacture at least 35 parts on each engine.
“Our primary focus is to make reliable, robust printed parts, that will work 100 percent of the time. We started designing some of these pieces a couple of years ago to make sure they were tested and certified for NASA’s space program, which is crucial to the safety of the upcoming crewed missions,” said Fung.
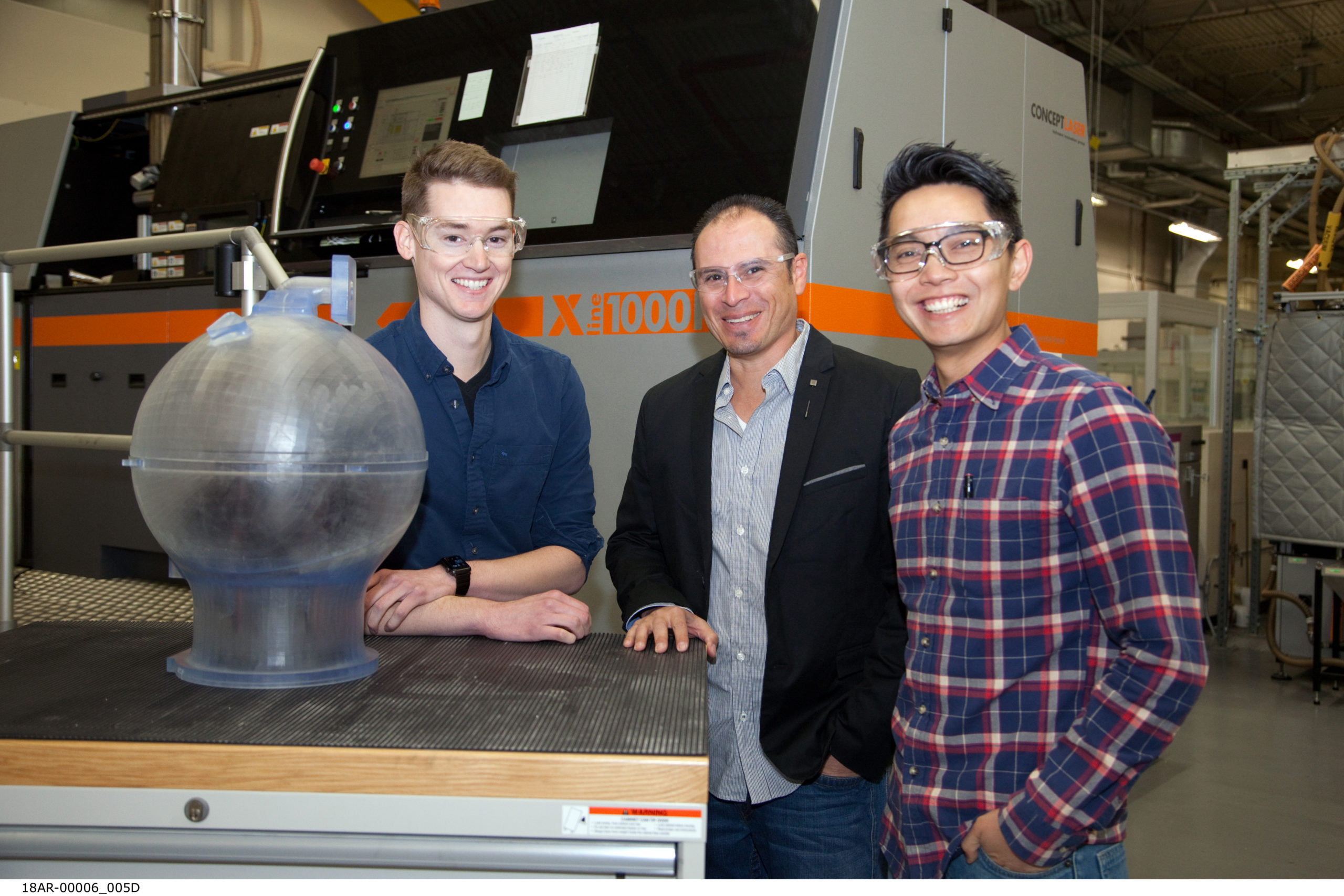
AM Team at Aerojet Rocketdyne, from left to right: Bryan Webb, Ivan Cazares, and Alan Fung (Credit: Aerojet Rocketdyne)
With the delivery of these new engines scheduled to begin in 2023, the team is not wasting any time. Fung said that “part of the big quest in the first round was to work with NASA closely on developing the certification processes.” Revealing that “we now have a process to make parts using AM that we know is safe and it is exactly what we need to make sure that our parts will work on the engines that will power future SLS missions.”
3D printing simplifies the production of several RS-25 parts and components, making the engine more affordable to produce while increasing reliability. With fewer part welds, the structural integrity of the engine increases. This is a very manual, complex manufacturing process. In fact, rocket engines are so complicated to build, that only a handful of countries have been able to manufacture them.
“That’s where AM really shined for us. We were able to get rid of many welding joints and just incorporate the processes automatically, getting down the part count and reducing the load across the engine,” said Fung.
One of the largest 3D-printed components of the engine was the critical “Pogo” accumulator assembly. Roughly the size of a beach ball, the complex piece of hardware acts as a shock absorber to reduce oscillations caused by propellants as they flow between the vehicle and the engine. Fung described the 3D-printed component as a critical part of the engine because it helps smooth the ride for astronauts and the vehicle ensuring a safe flight. Moreover, he explained that the Pogo used to demand more than 100 weld joints that had to be done manually and took almost four years to make, while the 3D-printed Pogo developed at Aerojet Rocketdyne’s factory in Los Angeles, brought the welds down to just three, and was finished in less than a year.
Some of these modified components have already been tested during engine tests that replicate the conditions of flight. For example, during a 400-second test at NASA’s Stennis Space Center, Aerojet Rocketdyne was able to successfully evaluate the performance of the 3D printed Pogo accumulator assembly.
“We expect that more and more engines will be additively manufactured in the future, leaving behind a lot of traditional rocket engine manufacturing processes that are very difficult, and allowing us to print more engines. Eventually, the time to build is going to go down even more, especially as the industry gears towards incorporating more lasers and bigger machines; which is good for us, because our engines keep getting a little bit bigger than the last ones. So, when those machines get to be bigger, use more lasers, and print parts faster, then that’s when we will see a really big shift in the way we make rocket engines,” went on Fung.
Working with NASA, Aerojet has implemented a plan to reduce the cost of the engines by more than 30% on future production when compared to the versions that flew on the Space Shuttle, all thanks to more advanced manufacturing techniques, like AM, that help the engineers modify some of the rocket components.
During the flight, the four engines will provide the SLS with around two million pounds of thrust to send the heavy-lift rocket to space. The rocket engines are mounted at the base of a 212-foot-tall core stage, which holds more than 700,000 gallons of propellant and provides the flight computers that control the rocket’s flight.
The AM team at Aerojet is using GE Concept Laser and EOS machines for its selective laser melting requirements. Fung said they were using superalloys, mostly nickel-based for the engine parts being 3D printed, due to its outstanding corrosion resistance, high strength, and ability to resist hydrogen embrittlement due to the hydrogen fuels found in most of Aerojet Rocketdyne’s liquid propellant rocket engines.
“These new RS-25 engines are an upgrade from the Space Shuttle engines, which were already some of the most reliable engines made in history. Engineers spent 40 years making the shuttle engines as reliable, safe and high performance as possible; but with additive manufacturing we thought we could also try to get the cost down. This technology will revolutionize the way we build engines”
With so many challenges ahead, having certified rocket engines to take the next lunar explorers to orbit feels like a stepping stone for the journey that lies ahead. After all, the SLS rocket is part of NASA’s backbone for deep space exploration and will prepare humans for long-duration space travel and the eventual journey to Mars.
The post NASA Wants Aerojet Rocketdyne to Make More Rocket Engines with 3D-Printed Parts appeared first on 3DPrint.com | The Voice of 3D Printing / Additive Manufacturing.