DiManEx is Dutch company that wants to bring 3D printing to the supply chain. They’re focussing on one of the most promising and challenging areas in 3D printing, how to identify parts that are suitable for 3D printing so they can be used for spares. DiManEx hopes to help firms identify good parts and then successfully print them as well. The regulatory, performance and print challenges there are considerable. Tibor van Melsem Kocsis is DiManEx’s CEO and he hopes that his firm will be the one to solve these challenges. If they can then they’ll have a very valuable capability on their hands. What’s more, companies would be very likely to deepen and broaden a long term relationship with a key partner that could guide them from a 3D printing standstill into spare part production. Furthermore, if they can prove that they can do this and maintain part performance and certification then people would not be very likely to shop around for less trusted firms. It will take a lot of convincing, knowledge and long sales cycles to get firms to the point where they’re printing spares though. We interviewed Tibor to find out more about the firm and what it hopes to achieve.
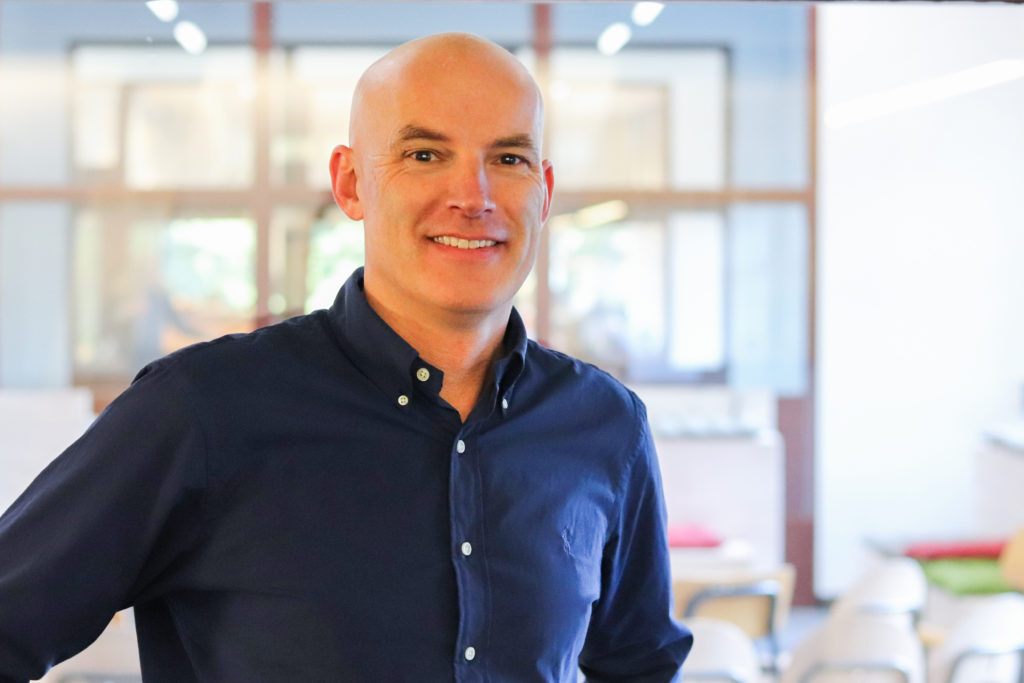
What is DiManEx?
DiManEx is an end-to-end platform that makes 3D printing easy for supply chain teams. We help you identify the right parts for Additive Manufacturing, digitize your inventory and print parts on demand through a network of industrial-quality facilities.
How is it different from Shapeways. Xometry, 3DHubs?
Supply Chain Optimization is the core element of our offering. For us 3D printing is an exciting technology, and a means to an end, not a goal in itself.We don’t just offer access to a manufacturing network, we provide a comprehensive service that helps companies find out what they can print, what they can’t print, and what’s beneficial to print from a supply chain stance. We start from the data, as well as immediate supply chain problems our customers need to address. We are also not a marketplace and assume end-to-end responsibility, from part identification to delivery to the end use location.
Where do you hope to be in five years?
We know that by then, even more than today, supply chains will operate in a highly networked environment, enabled by data and analytics, as well as end-to-end automation. Our big idea is to transform industrial supply chains in the same way e-commerce has disrupted retail. In the next five years, we want to become the preferred platform for companies that want to transition to digital inventory and optimize their global supply chain with digital manufacturing technologies like 3D printing.
What markets do you focus on?
We work mainly with companies in discrete manufacturing, in a wide range of industries, and companies with parts-intensive supply chains in Europe and the U.S. They are all focused on improving fundamental aspects of their business by solving specific supply chain issues. For instance, they want to improve the availability of service parts, ensure uptime to meet service levels, speed up lead times, optimize their inventory, and reduce their environmental footprint by preventing waste and unnecessary logistics.In addition, we see a growing demand for first series. Using AM for the first series helps companies speed up time to market, make changes on the fly and prevent unnecessary tooling costs.
Lightyear, for example, worked with us to secure more than 60 first series parts for the LightyearOne, a long-range solar car prototype. Being a prototype, some changes were required in several parts. The use of Additive Manufacturing made it possible to incorporate these changes quickly at a much lower cost than through traditional production. The first series was secured much faster without minimum order quantities. There was no investment in tooling or tied up working capital required.
Electrolux also works with us to secure like-for-like replacements of parts. The OEM is required by law to keep parts in stock for its appliances, but often incurs high set up costs, large minimum order quantities and eventual scrapping costs in order to meet this requirement. 3D printing offers a better way, by enabling them to supply the part as needed, on-demand. They work with us to 3D print, test and deploy several parts on the field.
What processes and materials?
We offer all available direct and indirect Additive Manufacturing techniques and post processing technologies. We provide access to 2000+ materials, both plastic and metal. We have global coverage with additive manufacturing production facilities and contracts with 60 partners we work with on an ongoing basis.
What is the Supply Chain Inspector?
Supply Chain Inspector is the analytics engine in the DiManEx platform. It uses semantic search, powered by machine learning algorithms, to help you identify the right parts for additive manufacturing. The solution draws on supply chain and technical data to assess parts’ printability and pinpoint those that are ideal candidates for digital inventory. We developed Supply Chain Inspector because we see that a lot of companies struggle with missing insights from available data. It’s not always straightforward to identify when 3D printing makes sense from a technical and supply chain optimization perspective. Through Supply Chain Inspector, you get this visibility and insights expressed in relevant metrics, like lead time reduction, inventory value reduction, future demand (uncertainty) and how to act upon this. The insights we provide make it easier for our customers to make the right decisions within our platform, with the ultimate goal to optimize their supply chain.
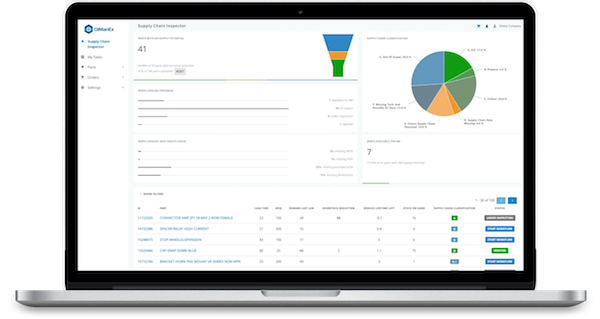
How does it work?
Our platform makes 3D printing easy for supply chain teams. A lot of complex processes happen behind our user-friendly interface. We facilitate a complete flow, from data to parts delivered. Looking at data, customers can get a bigger picture of what’s happening in their business and can more easily identify the right parts for AM. When a part is selected, they can trigger our end-to-end workflow, which includes scanning, digitization, production, and quality control.
Once a part design is approved, the part is added to the company’s digital inventory and users can place orders as often as they need to. Our platform matches the order with the additive manufacturing facility in our network that best matches the customer’s needs. Proximity to the end use location is also considered so we can minimize miles traveled. After the part is produced, it gets delivered through our network of partners.
A 1000 orders doesn’t seem like a lot?
This would be true and was the case when we first launched the platform. Right now this is not an accurate number anymore. We are now shipping orders on a daily basis, resulting in a new partnership with Logistyx which will help us optimize multi-carrier parcel deliveries. This partnership is very important for us. Logistyx simplifies the complexity of cross-border, multi-carrier parcel shipping. Their platform will help us quickly scale and ship high volumes of parts profitably, to customers worldwide. Their global carrier network counts more than 8,500 carrier services and helps us determine the ideal combination of carriers in real-time, based on factors such as price, capacity, service requirements, and performance.
How will you grow?
We will grow thanks to our customer-focused approach. Our goal is two-fold. Scaling up business with existing customers, and increasing the number of customers we serve across the globe. Further growth will be achieved by delivering the next generation of tools and services we have in our roadmap, and continuing to provide immediate value to our customers. This means having a positive impact on their total cost of ownership, service to their end customers and environmental footprint.

Is it realistic to add 3D printing to the supply chain?
Absolutely, 3D printing is an enabler, especially for discrete manufacturing companies and service organizations. It creates immediate and tangible value during the various stages of the manufacturing life cycle.
The key is to have a solid change management strategy and to work with partners that will make the transformation go smoothly. It helps to work with a managed service, so you don’t have to invest in machines yourself and can tap into a partner’s expertise without committing too many internal resources.
How do I redesign old parts for 3D Printing?
In daily practice, customers provide us with an old drawing, a physical part, and sometimes even a damaged part to be reverse engineered. This is especially true for older components.
We’ve done this for a range of companies that produce household appliances, elevators and escalators, and heavy equipment, as well as service organizations.
The Dutch Railways (NS), for instance, worked with us to reverse engineer and 3D print a frame for its train radios. The frame was not available through NS’ original supplier anymore. Without it, trains couldn’t run. Other suppliers had a large minimum order quantity. In most cases, NS would have to order a minimum of 100 parts, when in fact they only needed 10. They also faced very long lead times. We were able to reverse engineer the part and reduce lead times significantly. This helped them guarantee that their coaches would keep running. The weight for the part itself was also optimized.
A radio frame part for the Dutch railways, the NS
And these 3D printed parts will they be as safe, perform as well?
Pretty much all the parts we supply are functional parts, which means they must meet the technical specifications. Several of them have been tested by our customers. In many cases, we provide a material certificate and/or a test report which is provided by a qualified third party, as part of our quality assurance program. All of this is available in our end-to-end workflow.
What advice do you have for companies who wish to manufacture with 3D Printing?
First and foremost try to understand how 3D printing as a production technique can contribute to optimize your supply chain. Second, once you have an understanding of the potential during the various stages of the manufacturing lifecycle, bring a team together with the key stakeholders.Next, define a concrete plan with clear deliverables; start small, learn quickly and scale fast.
The post Interview with Tibor van Melsem Kocsis of DiManEx on 3D Printing in the Supply Chain appeared first on 3DPrint.com | The Voice of 3D Printing / Additive Manufacturing.