Researchers use machine learning to develop a stronger 3D printed geopolymer cement
Swinburne robot constructs automotive repair using 3D printing
Interlayer Adhesion Improvements for 3D Construction Printing
Interlayer adhesion is a common problem that users often battle in 3D printing, and Swinburne University of Technology researchers Taylor Marchment, Jay Sanjayan, and Ming Xia address the topic further in ‘Method of enhancing interlayer bond strength in construction scale 3D printing with mortar by effective bond area amplification.’
Since 3D Printing builds up objects layer by layer parts will fail at the weakest point: there where the layers bond. 3D Printed parts under stress will tend to come apart at these points. Any improvement to inter layer bonding will be an improvement to the strength of the part.
The authors point out that 3D printing is still relatively new in terms of development—and especially 3D construction printing (3DCP) with numerous challenges to meet, and especially in extruding with cementitious materials. This type of weakness is attributed to localized voids within the mixture created between the time that layers are deposited by the 3D printer. The goal of the research team was to find a way to strengthen interlayer bonds with a cementitious paste.
Lack of reinforcement for providing tensile strength and weakness due to application of layers are the primary challenges in 3D printing durable structures.
“3DCP brings about many new constraints and factors that can create a weak interfacial bond or often termed “cold joint” due to the lack of intermixing between layers,” state the researchers. “Predominately major influencing factors are the stiffness/dryness of the deposited layer, and the time gap between successive layer depositions.”
Interlayer strength may deteriorate by as much as 50 percent due to drying out during the process:
“As the phase change requirements of the 3D printed concrete are succumbed to shape retention and the sequential loading of fresh layers, the interlayer strength quality becomes a balancing act of the drying rate.”
Adhesion may occur either in mechanical or chemical bonds, either in relation to physical layer attributes or the hydration and bonding of cement particles, respectively. Mechanical factors causing voids are due to surface roughness and stiffness of layers. In the research study, the team used a flatbed scanner to examine layer issues further.
Because drying is such an issue, the research team realized they would have to either decrease the void structure or increase the contact area, with the hope that better moisture levels would encourage improved adhesion. Previous analysis techniques have not only been time intensive but have also proven to damage samples and sometimes cause ‘misleading results’ too. The researchers decided to use flatbed scanners for examining issues in a less invasive but also cheap and fast method.
In attempting to make a glue for stronger adhesion, the research team used four OPC-based paste mixtures, with a water to binder ratio of 0.36, used between the layers.
“The paste mixtures were developed to primarily increase the effective bond area, with a more malleable interface compared to conventional layer by layer construction,” said the researchers. “Three admixtures including retarder, viscosity-modifying agent and slump-retention agent were used in this study.”
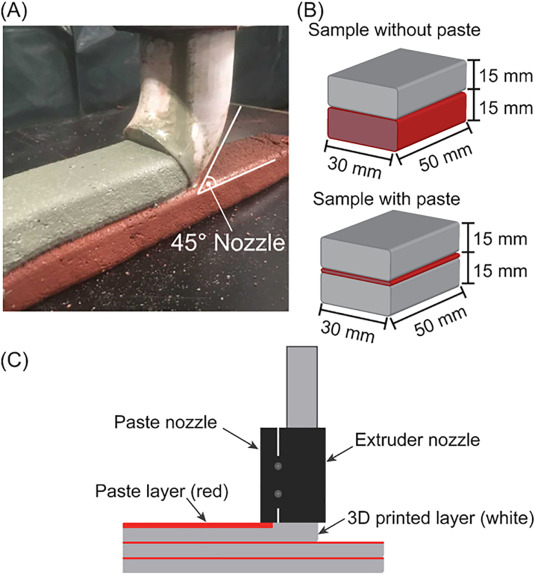
(a) Mortar mix being extruded from 45° angle nozzle without a paste mixture between, (b) 50 mm (L) × 30 mm (W) × 30 mm (H) samples with and without a paste mixture applied between layers. (c) A schematic of the proposed twin nozzle extruder depositing the paste layer and 3D printed layer.
A customized 3D printer, developed with a piston-based extruder, was used in the research, with a time gap interval of 15 minutes in between each layer. Samples were left to cure at ambient temperature for seven days and cut into 50 mm (L) × 30 mm (W) × 30 mm (H) blocks for testing. Adhesion of bonds was tested by using clamps with two centrically loaded pin connections.
The 3D printed paste proved to have the highest resistance to flow, and the lowest average compressive strength, at 34 MPa.
“The analysis is done on the basis that the compressive and tensile strengths are strongly correlated,” state the researchers. “The 3D printed mix will have an inherently lower interlayer bond capacity therefore, samples fabricated with no paste applied at the interlayer, we must factor this difference and contact area.”
The researchers note ‘uniform fracture’ at the interlayer for all samples, along with fractures in between both the overlay and paste layer. They also note that fractures occurred on the areas exposed to the most surface drying. Data also showed that interlayer strength increased with the paste layer:
“The addition of pastes containing additives shows and interlayer strength increase of 26% to a 59%. The highest increase was observed with the addition of superplasticiser. These results replicate similar trends observed in the flowability and compressive strength tests.”
The researchers considered the concept—and the strength—of brick and mortar as they brushed on a variety of cement pastes between the layers with different color schemes for ease in analyzing the images. In the end, they realized the following:
- Using paste with higher, sustained flow characteristics increases strength in layers during 3D printing.
- More reliable and consistent results were available in analysis due to the addition of color in the layers.
- The effective bond area and interlayer strength are closely related.
“The assumption at first was that the higher flowability of the paste mixtures would allow for a greater malleable surface area, in turn creating a greater effective bond area,” concluded the researchers. “However, through this study further evidence is produced to suggest that it is not only the flowability/malleability of the paste which is critical, but the surface moisture retention is also another critical factor. The effects of this may be lack of moisture decreasing the degree of hydration and lowering of strength.”
The study of materials and strength in 3D printing is becoming a priority to researchers seeking better quality and predictability in parts, along with research into other areas like concerns about toxins and emissions. What do you think of this news? Let us know your thoughts; join the discussion of this and other 3D printing topics at 3DPrintBoard.com.
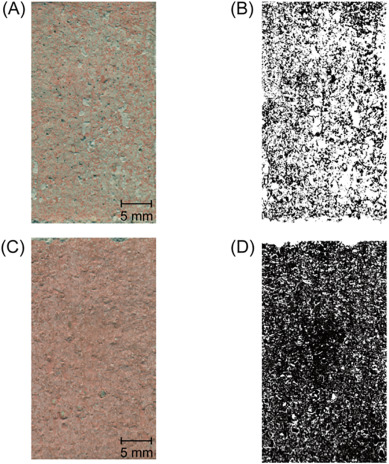
Results of application of colour thresholding. (a) Top Image before thresholding, (b) Top Image after thresholding, (c) Bottom Image before thresholding, (d) Bottom Image after thresholding.
[Source / Images: ‘Method of enhancing interlayer bond strength in construction scale 3D printing with mortar by effective bond area amplification’]