Metal materials with remarkable properties. This has been the focus of Swedish company VBN Components since the very start. In the middle of the financial crisis in 2008, VBN saw the opportunity to turn the steel business upside down by using additive manufacturing of high strength, carbide-rich materials. Today they present a range of patented alloys with unique performance.
The Vibenite® materials
VBN Components nurtures the Swedish heritage within the metal industry by continuously developing new and improved materials branded Vibenite®. Sweden was one of the first countries in the world to produce industrial steel with purity as a key factor. VBN takes this to the next level by 3D printing materials unique in their composition, offering exceptional wear resistance. Their properties are achieved by a patented additive manufacturing process through which metal materials with 100% density can be produced. Small sized uniformly distributed carbides in a specific matrix are the reason for the materials’ performance. They are all produced from a base of gas atomized metal powder and are therefore classified as powder metallurgy materials.
Vibenite® technology allows the user to switch to a more wear resistant material than what can be produced with traditional manufacturing. When 3D printing, most production and transportation steps are eliminated, material usage optimized, and environmental impact significantly reduced. Both performance and life-time of components increase with Vibenite®. These properties are easily tested by simply printing a full-quality prototype and running it! Better material properties are normally not heard of in the 3D printing business today, where typically difficult geometries are promoted.
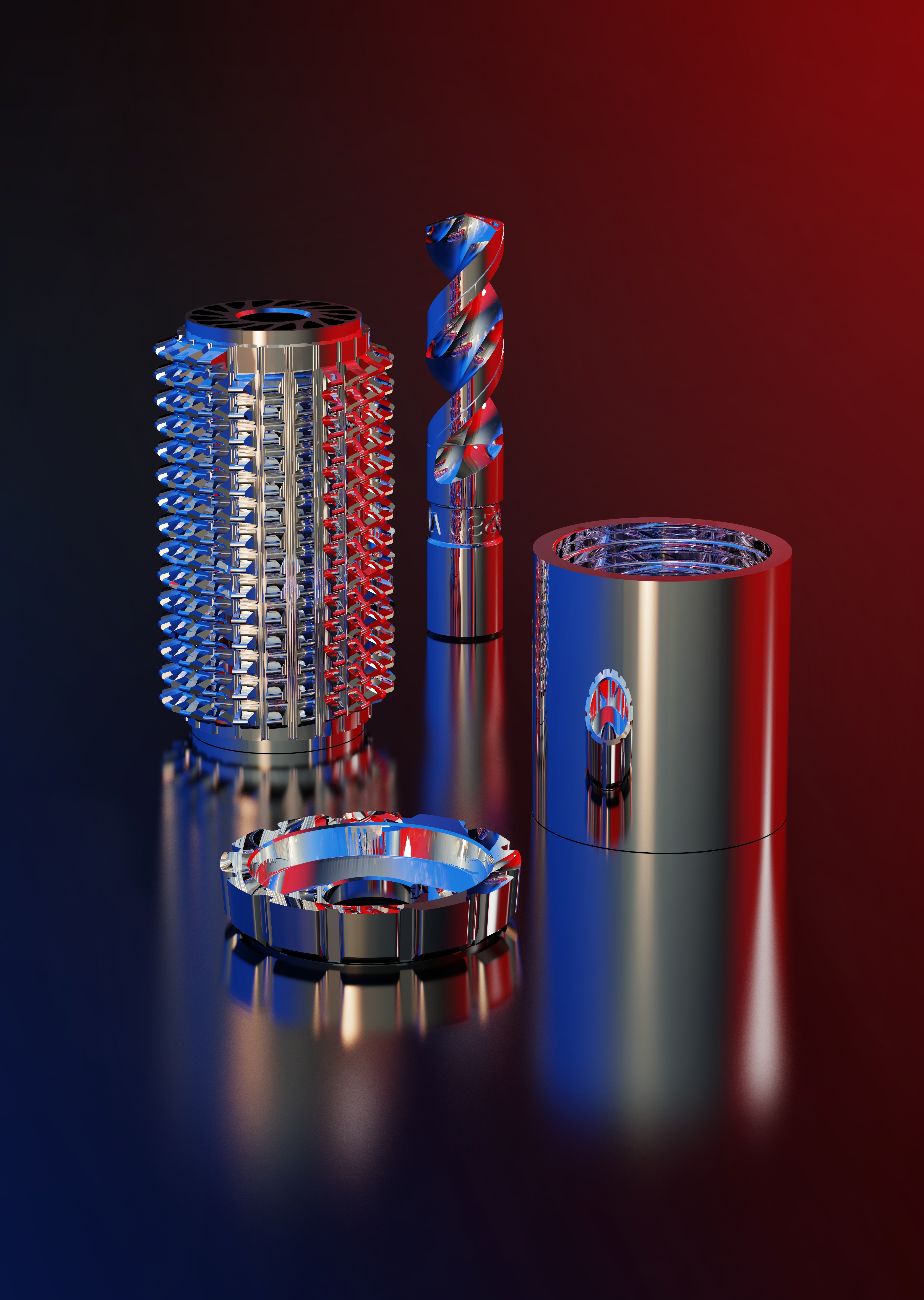
Your application of choice can be printed with Vibenite® materials.
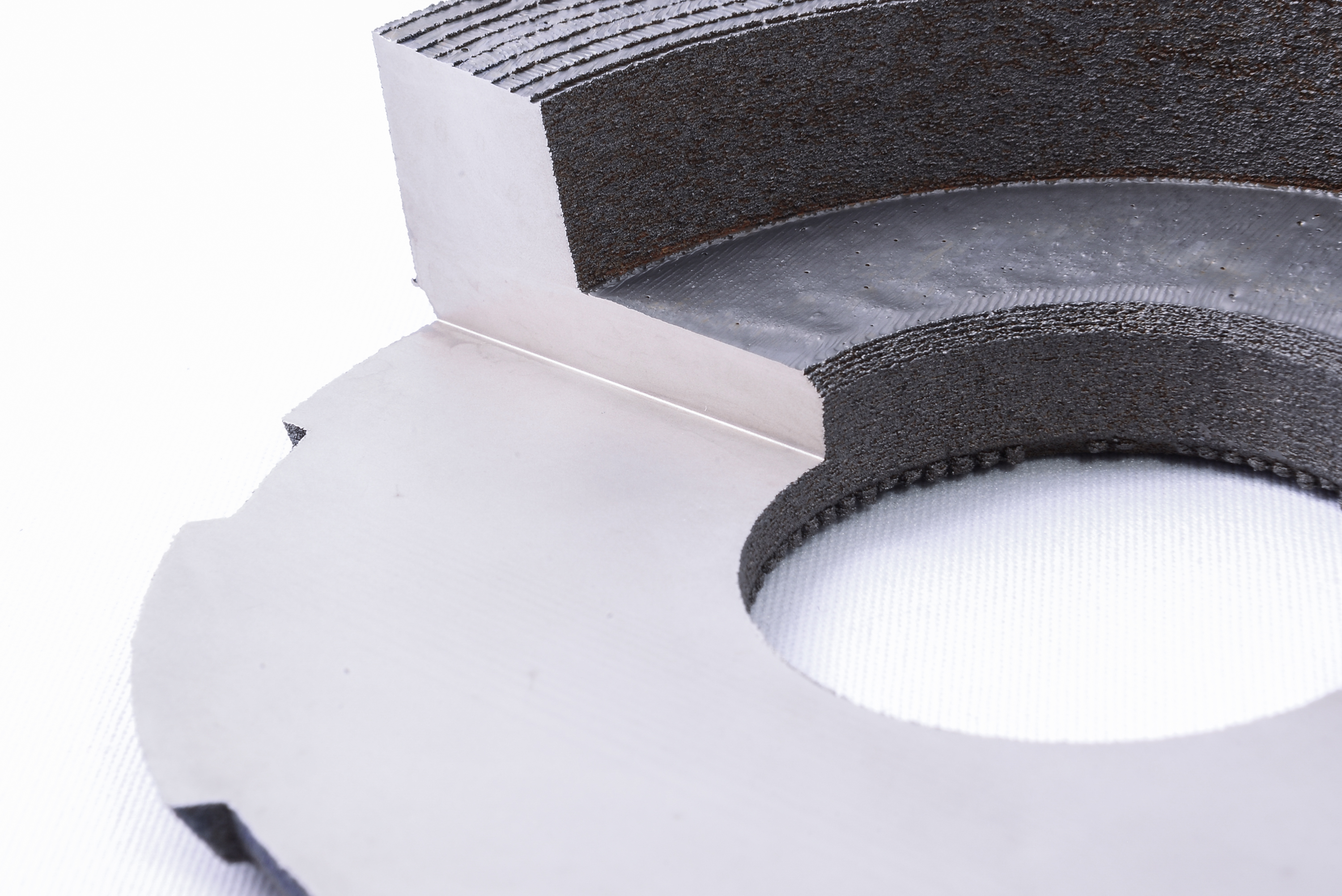
Cross section of shaper cutter showing a 100% dense material.
Caption: Hardness of Vibenite® materials compared to H13, a common tool steel.
Vibenite® 290, the world’s hardest steel
Today there are five different types of Vibenite® materials, with a hardness range from 58-72 HRC (600-1100 HV). Among them we find the world’s hardest steel, Vibenite® 290 with 25% carbide content. Its hardness of 72 HRC means it could never be processed traditionally. It was recently put through two abrasion tests to measure wear against rock, in collaboration with Robit Plc. The results spoke for themselves; Vibenite® 290 showed only 50% of the wear rate compared to reference material H500 (51 HRC) in the first test, and 25% of the wear rate in the second. H500 is commonly used in these types of abrasion lab-tests.
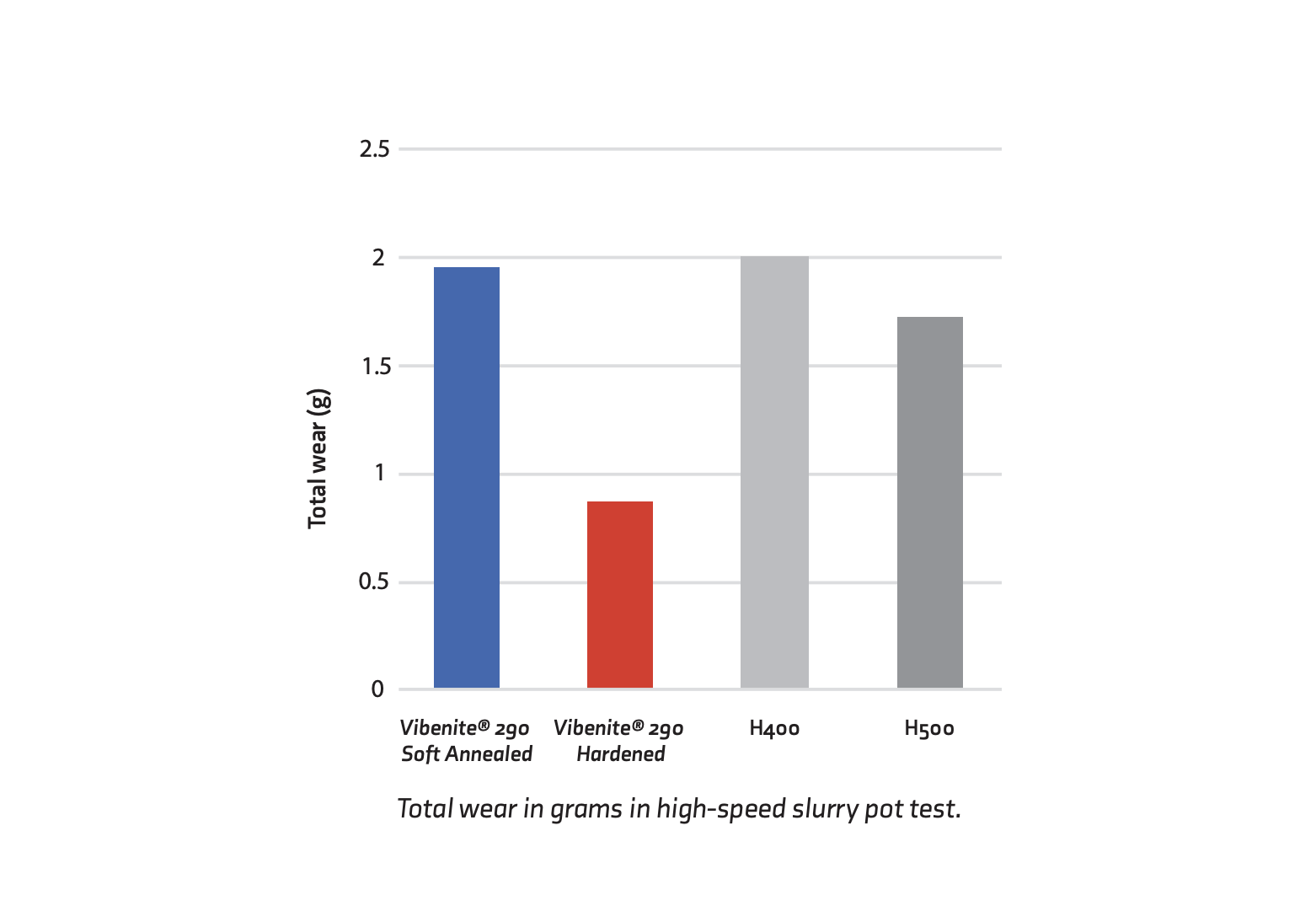
Total wear in grams in high-speed slurry pot test.
Vibenite® 480 – a new type of cemented carbide
Recently, VBN Components announced that they can print cemented carbide. This type of material has previously been considered “impossible” to print, due to high carbide content. Vibenite® 480 contains an astonishing ~65% of carbides, which really beats al the odds. There is no mixing, drying, pressing or sintering needed, as in the traditional process. It has a long-term heat resistance of 750°C, is corrosion resistant and magnetic. Vibenite® 480 is niched both towards applications where steel is normally used, but where replacing it with hard metal would increase production efficiency, and also towards hard metal applications with complex geometry. Since it combines the best of two material worlds – powder metallurgy high-speed steel and cemented carbide, it is referred to as “hybrid carbide”.
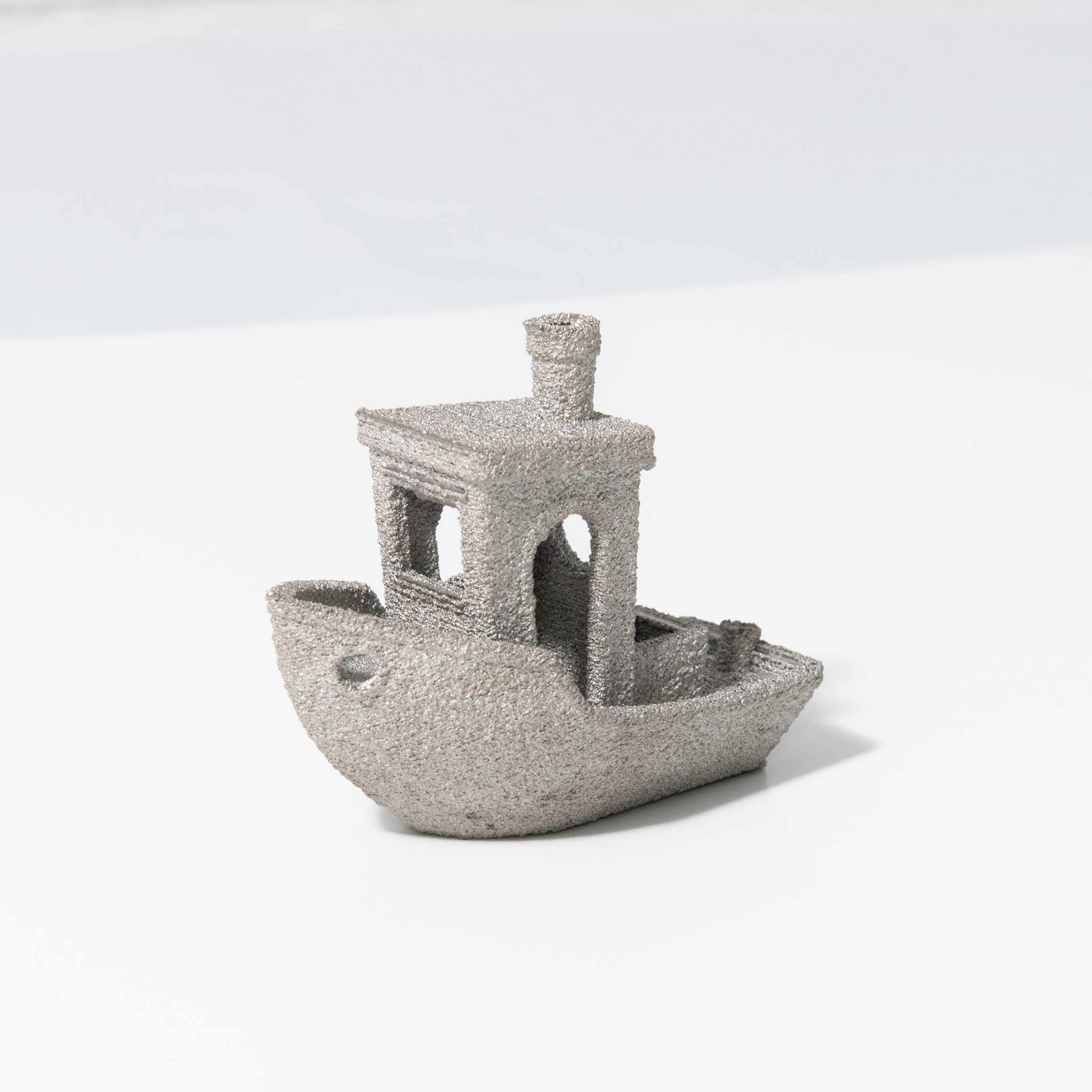
3D Benchy printed with Vibenite® 480.
Milestones and future projects
These material innovations have raised quite a lot of attention. Already in 2013, VBN Components was awarded with Sweden’s largest and most important innovation prize, SKAPA, established in honor of Alfred Nobel. In that same year, Swedish steel giant Uddeholms AB contested VBN’s first patent regarding high purity in high carbon content materials. It took five years before the battle was finally settled, in favor of VBN Components, at the European Patent Office (EPO) in Munich. Not long thereafter, just before Christmas of 2018, a multi-million license agreement was signed with a global engineering group. It implies an exclusive license within a specific niche of high-strength components, which is kept confidential for now.
VBN Components is the only company 3D printing alloys with high carbon content, resulting in hard and wear resistant unique materials. The extremely high cleanliness of Vibenite® alloys gives very high fatigue resistance. Following this path, VBN will continue developing new metal alloys and novel ways to print these. The possibilities are vast, from “Vibenite® Combo” which implies printing Vibenite® upon other existing components, to “Vibenite® Grado” which would give different properties in different parts of the component.