3D printing is often used in education these days, whether it’s being taught as a subject or used to enhance another one. As we’re moving ever closer to the start of a new year, we decided to save you some time and gather the ten best education stories from 2018 in one article.
Siemens STEM DAY

The Siemens Foundation focuses on philanthropic efforts in order to continue the advancement of STEM-related education and workforce development, and has invested millions of dollars for this cause in the US. In early 2018, the Siemens Foundation worked with Discovery Education to re-brand its annual Siemens Science Day into a program for more modern educational opportunities: Siemens STEM Day, which is an opportunity for US schools to promote STEM activities for both students and teachers. The program, which doesn’t actually happen on one specific day but is a promotion of STEM lessons and hands-on activities, is meant to be used by students in grades K-12, and offers multiple tools and resources to help reboot STEM curriculum.
New 3D Printing Educational Initiatives
[Image: 3D PARS]
In February, we provided a round-up of some of the many educational initiatives that were looking to provide adults with a deeper understanding of 3D printing. Included in this round-up was a new online course for professionals by MIT, new 3D printing courses from the Sharebot Academy program, and a joint two-day training course in additive manufacturing from German consulting firm Ampower and full service prototyping and 3D printing provider H & H. Additional educational initiatives shared in the round-up were 3DPrint.com’s own Additive Manufacturing with Metals Course.
learnbylayers Partnered with Kodak
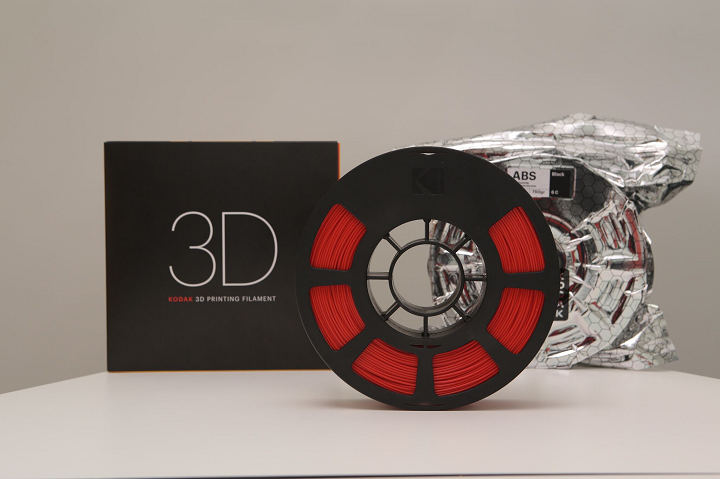
In 2017, educator Philip Cotton launched an online 3D printing resource for teachers called learnbylayers that offers lesson plans, project ideas, assessments and more that were designed by teachers for teachers. The site grew quickly, and in February Cotton announced that it had reached a distribution agreement with Kodak. The learnbylayers educational curriculum was added to the Kodak 3D Printing Ecosystem, as the company began offering the internationally-taught curriculum along with its Portrait 3D printer’s launch.
Renishaw Deepened Its Commitment to 3D Printing Education
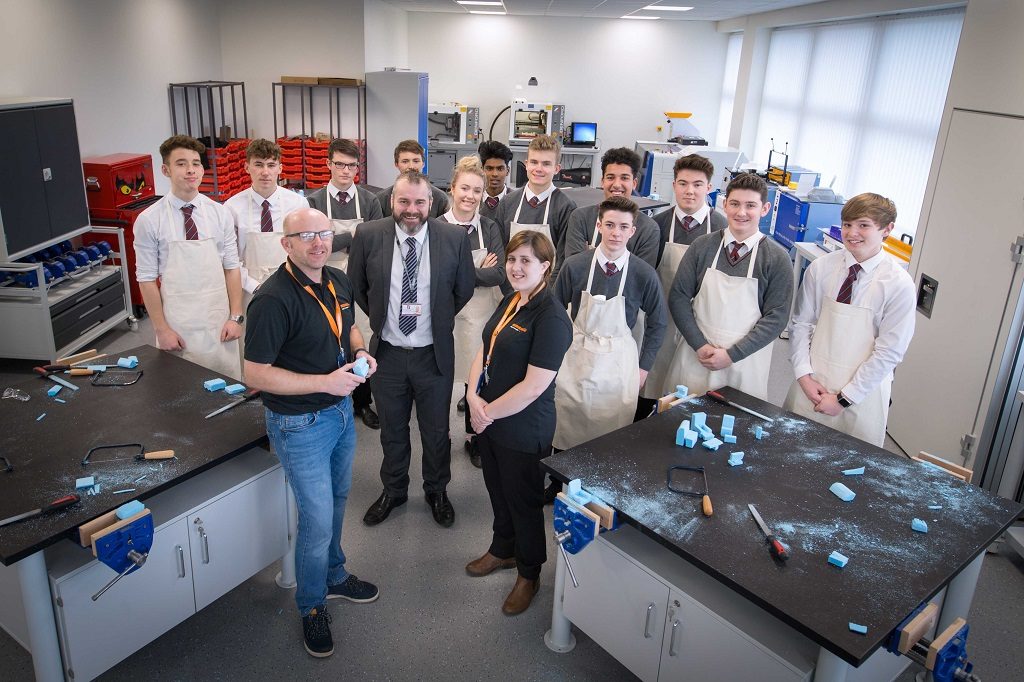
This spring, Renishaw announced that it would be deepening its commitment to 3D printing education. The company established a new Fabrication Development Centre (FDC) at its Miskin facility in South Wales, with the goal of inspiring young people to pursue STEM careers. The FDC has two classrooms, staffed by qualified teachers and Renishaw’s STEM ambassadors, that can be used for free by schools or groups of young people for lessons or workshops. The FDC was actually in use by Radyr Comprehensive School students long before it was officially launched by Andy Green, a driver for Bloodhound SSC, a 3D printing user and Renishaw partner which also devotes many resources to education about the technology.
Ultimaker Launched New 3D Printing Core Lessons for STEAM Education
Lesson 1: Coin Traps
In April, Ultimaker launched its new Ultimaker Core Lessons: STEAM Set for educators. Eight free lessons, published under a Creative Commons Attribution-ShareAlike 4.0 International License, are included in the set, which can help teachers in informal, K12, or Higher Ed classrooms incorporate 3D printing into their educational practices and STEAM curriculum. Some of the beginner lessons include 3D printing a coin trap, flashlight, and penny whistle, and can teach young students important skills like how to align objects, using symbols to communicate ideas, and how to effectively work together on creative projects.
PrintLab Teamed Up with CREATE Education Team

UK-based global 3D printing distributor and curriculum provider PrintLab partnered with UK 3D printing company CREATE Education, a collaborative platform that provides educators with free resources and support, in order to support schools all across the UK with 3D printing. Each company’s educational 3D printing offerings will be combined in this partnership so that UK schools can enjoy unlimited access to full 3D printing solutions for the classroom, which will be locally supported for life by CREATE. Multiple initiatives came out of this partnership to support teachers, like 3D printer loan schemes, funding advice and resources, special training and curriculum workshops, and new educational 3D printing bundles.
3Doodler Introduced New Educational Kits
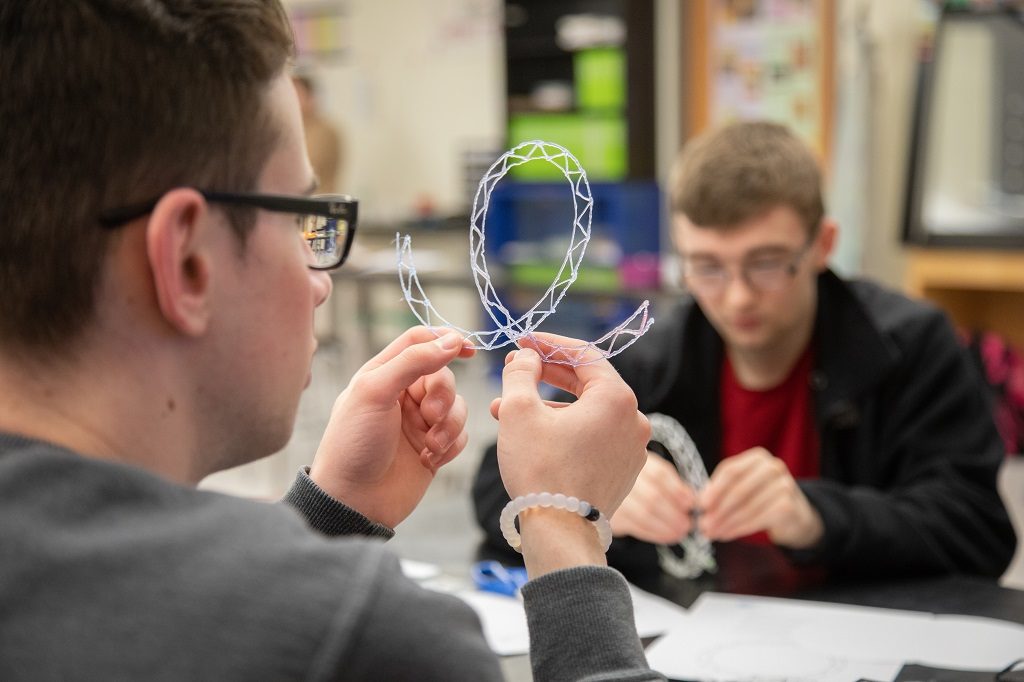
3Doodler has long supported education, and often releases new STEM-centered educational packages, including its latest classroom product line: the 3Doodler Create+ EDU Learning Pack and 3Doodler Start EDU Learning Pack. Each pack, designed for and with teachers, was designed specially for classrooms from kindergarten to 12th grade and includes 6 or 12 3Doodler pens (Create or Start, depending on the package) and 600 or 1,200 strands of plastic, as well as other tech accessories, lesson plans, and classroom materials. Additionally, the company released its 3Doodler Create+ EDU Teacher Experience Kit and 3Doodler EDU Start Teacher Experience Kit, which are designed to be trial packs for teachers who are thinking about introducing the 3Doodler into their classrooms.
Robo Acquired MyStemKits

3D printer manufacturer Robo announced this summer that it had acquired Atlanta company MyStemKits, which provides the largest online library of STEM curriculum in the world. Thanks to this acquisition, Robo is now offering educational bundles that include its classroom-friendly 3D printers, a supply of filament, one-year subscriptions to MyStemKits, and additional professional development and online learning.
GE Additive’s Education Program Provided Five Universities with Metal 3D Printers
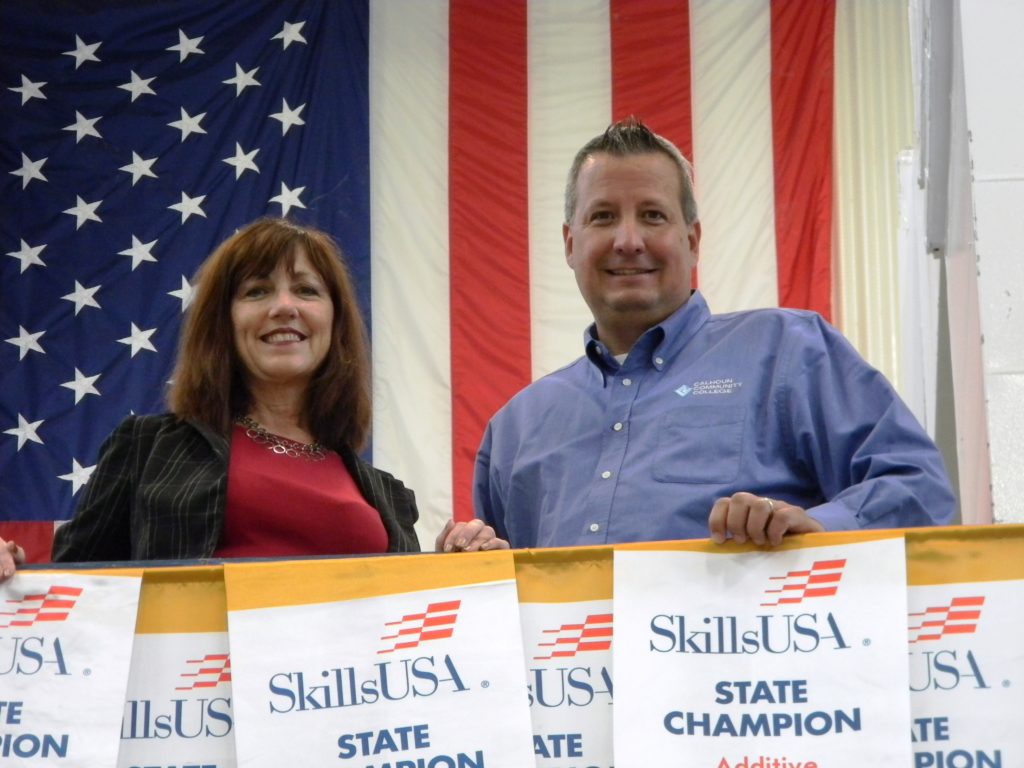
GE’s Additive Education Program (AEP) – a five-year, $10 million, two-part initiative to provide 3D printers to as many schools as possible – chose five universities this summer to receive an Mlab 200R from the program. 500 proposals were submitted for this round of the program, and GE Additive chose German’s Coburg University of Applied Sciences and Arts, Ireland’s University of Limerick, the Calhoun Community College in Alabama, the University of Illinois at Urbana-Champaign, and West Virginia University as the lucky winners.
3D Printing In Fashion Education

In a recently published paper, titled “Integration of 3 Dimensional Modeling and Printing into Fashion Design Curriculum: Opportunities and Challenges,” Nicole Eckerson and Li Zhao from the University of Missouri discussed whether 3D printing should be integrated into fashion design curriculum. The researchers noted that while 3D printing has been recognized as a major influence in the work of designers and engineers, educators in the fashion industry are facing a lack of time, resources, and knowledge to teach the technology to students. The two conducted semi-structured interviews with eight 3D printing industry experts and academic professionals for their research, and came up with three distinct themes from their data about why 3D printing should be adopted, and taught, in fashion.
Discuss this and other 3D printing topics at 3DPrintBoard.com or share your thoughts below.