ExOne’s extensive collaborations yield 20+ qualified 3D printable materials
AFRL and University Partners Used 3D Printed Composite Materials to Make Structural Parts
The Air Force Research Laboratory (AFRL), located at Wright-Patterson Air Force Base (WPAFB) near my hometown of Dayton, Ohio, has long been interested in using 3D printing and composite materials for the purposes of aerospace applications. Last year, AFRL’s Composites Branch at the Materials and Manufacturing Directorate partnered up with researchers from the University of Arkansas, the University of Miami in Florida, Louisiana Tech University, and the University of Texas at El Paso (UTEP) to work on advancing 3D printable composite materials.
The Composites Branch works on the research and development of organic and ceramic matrix composite technologies for legacy, developmental, and future Air Force system components. Together with its university partners, the AFRL branch demonstrated 3D printed composite materials, made from a combination of carbon fiber and epoxy, which had been successfully fabricated and used to make structural parts on both air and space craft. The results of this 3D printed composite material effort will soon be published in a special issue of the Journal of Experimental Mechanics that’s dedicated to the mechanics of 3D printed materials.
Dr. Jeffery Baur, leader of the Composite Performance Research Team, said, “The potential to quickly print high-strength composite parts and fixtures for the warfighter could be a tremendous asset both in the field and for accelerating weapon system development.”
Composite materials are made up of two, or sometimes more, constituent materials that have very different chemical or physical properties. When combined, these components produce a new material that has characteristics which are different from the originals. The individual components that make up the composite will remain distinctly separated within the final material structure.
When compared to the more low-quality polymers that are typically used in 3D printers, the composite materials demonstrated by AFRL and its partners are the same type that are already being used to make Air Force system components. These materials are very strong, while also lightweight, and have higher thermal and environmental durability than most.
Most traditional epoxy and carbon fiber composites are made by layering carbon fiber sheets, coated with epoxy resin, on top of each other. Then, the whole thing is cooked for hours in a costly pressure cooker to finish. The major downside to this method is that it’s more difficult to create parts that have complex shapes when sheets are being used.
This is where additive manufacturing comes in. Composite materials that are 3D printed are able to create parts with those complex shapes, and additionally don’t require the use of long heating cycles or expensive pressure cookers. On a materials level, there aren’t a whole lot of downsides to using composites for the purposes of producing, assembling, or repairing parts for the Air Force, whether at the depot or out in the field.
Military branches in other countries are also seeing the benefit of 3D printable composite materials. For example, engineers in India are manufacturing complex core structures using the composite 3D printing process; when combined with top and bottom face sheets, these structures will create lightweight sandwich structures that have properties tailored specifically to, as AFRL put it, “the physical forces that need to be carried.”
Conventionally fabricated sandwich structures use the same core geometries over the entire area of an aircraft skin, but a 3D printed version would be able to stand up under heavier forces when necessary, while also remaining lightweight in other parts of the skin.
Discuss this story and other 3D printing topics at 3DPrintBoard.com or share your thoughts in the Facebook comments below.
[Source: Dayton Daily News]
AFRL and U.S. universities create 3D printable epoxy/carbon fiber composites for aircraft parts
3D Printing Industry News Sliced: Carbon, BigRep, Protolabs and more
3D Printing News Sliced: Linde Gases, Techniplas, Autodesk, America Makes
World’s First 3D Printed Volumetric Circuit Emerges from University of Texas El Paso Lab
A great many discoveries have been made in the lab of Raymond C. Rumpf, PhD, the Schellenger Professor in Electrical Research in The University of Texas at El Paso’s College of Engineering. Dr. Rumpf leads the EM Lab, which is dedicated to the research and development of advanced concepts in electromagnetics and photonics technologies enabled by 3D printing. The latest advancement made by the lab is an exciting one – earlier this year, the researchers completed the first true three-dimensional volumetric circuit using a fully automated process. According to Dr. Rumpf, the breakthrough may change the way that electrical products are designed and manufactured.
“This is a very significant step and potentially disruptive achievement,” Dr. Rumpf said. “There are many other large research groups that have been chasing this. It’s what everybody in this field is working toward and talking about, yet nobody has yet achieved it. It’s sort of the holy grail for 3-D printed circuits, and it was accomplished here at UTEP.”
A three-dimensional circuit can be made smaller, lighter and more efficient than other circuits, and 3D printing allows them to be manufactured into arbitrary form factors that can be integrated into any object or surface. Years of research went into the idea, according to Dr. Rumpf.
“The last three years were spent developing futuristic CAD (computer-aided design) tools, to produce 3-D/volumetric circuits,” he said. “These tools do not exist anywhere else.”
Rumpf worked with fellow EM Lab researchers Gilbert Carranza, Ubaldo Robles, and Cesar Valle. Carranza, a doctoral student, used an open source CAD software to integrate his custom functions that allowed the lab to design true 3D circuits.
“I built a custom tool that allows us to place electric components in any position and in any orientation,” Carranza said. “We can route the electrical interconnects throughout all three dimensions following smooth paths.”
He worked on the first version of the software for a year.
“We couldn’t go anywhere beyond that,” he said. “We didn’t have the necessary tool to actually translate my design into something that could be read by our 3-D printer.”
Robles and Valle, also doctoral students, were able to help. Earlier in the summer, Robles completed an interface that could convert the circuit design into code that the 3D printer could use to print the circuit in one step. Valle and Carranza then fine-tuned the process and used it to build the first 3D volumetric circuit.
“Getting the CAD, code generator, and 3-D printer to play along well together proved the most difficult step,” Valle said. “Typically, when you make a circuit, it’s two steps. You start with a thin sheet of plastic. On top of that, you form metal traces, then put electrical components onto that. What our tool does that is unique is it combines these processes, and it does it in three dimensions with complete design freedom. We are now able to load 3-D files, hit ‘run’ and out comes the part. Literally ‘File,’ ‘Print.’”
The applications for the technology are many. Because circuits can now be built into any surface or shape, electronics can be built into anything without any added weight or bulk.
“We can make circuits in any form or fashion,” Rumpf said. “You could put circuits in munitions, in eyeglasses, in shoes, and even in coffee mugs. You can be at a restaurant drinking coffee and, when the liquid gets down to a certain level the server gets notified before you have to say anything. It’s about making electronics ubiquitous in many different things.”
He believes that this will open the door for small businesses to become electronics manufacturers, just by purchasing a 3D printer.
“In the future, I don’t think you will see places, such as major electronics manufacturing companies, churning out billions of things and dominating the market nearly as often,” Rumpf said. “Instead, you may have thousands of small businesses in the U.S. churning out thousands of products, both mass-produced and customized. Our 3-D circuit technology may be the first step to change the paradigm of circuit manufacturing. And it may enable us to exploit and incorporate new physics in traditional planar (2-D) circuitry.”
Discuss this and other 3D printing topics at 3DPrintBoard.com or share your thoughts below.
[Source: Phys.org/Images: UTEP]
Aconity3D to Set Up North American Base of Operations for 3D Printing at UTEP
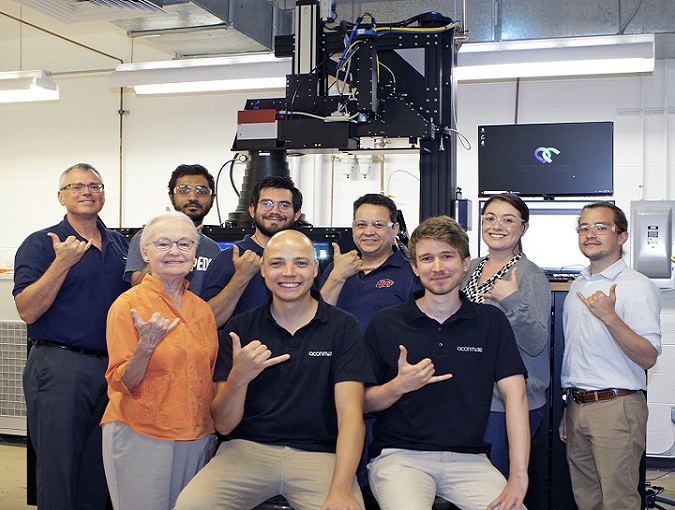
Bottom, L-R: Diana Natalicio, UTEP President; Yves Hagedorn, Aconity3D, managing director; Florian Sondermann, AconityUS, managing director. Top, L-R: Ryan Wicker, PhD, Keck Center director; Zia Uddin, student researcher; Alfonso Fernandez, powder bed manager; Francisco Medina, director of technology and engagement; Mireya Flores, Keck Center manager; Philip Morton, applications manager. [Image: UTEP Communications]
The University of Texas at El Paso (UTEP) has long been a 3D printing advocate, and a lot of this important work takes place at the university’s W.M. Keck Center for 3D Innovation, which is also the first satellite center for America Makes. Now, UTEP has made an agreement with Germany-based Aconity3D GmbH, which develops laser powder bed fusion 3D printers, to be its base of operations in North America.
“We are pleased to establish a relationship with UTEP. This is an excellent example of how research universities can partner with private industry to advance the educational opportunities afforded to students and also attract economic development to the region,” said Yves Hagedorn, PhD, the Managing Director of Aconity3D. “We are confident that the combined expertise of the Keck Center and Aconity3D will yield innovative approaches to 3D printing and offer world-class research opportunities for students.”
Aconity3D was founded in 2014 as a small startup, though it now boasts over 50 employees, and makes 3D printers capable of manufacturing complex metal parts for medical implants, airplanes, and cars, among others. It was eager to set up camp at UTEP due to the Keck Center’s expertise and prominence in the industry, as well as its commitment to increase economic development.
“This exciting collaboration is very well aligned with UTEP’s access and excellence mission. UTEP is committed to providing our students with exceptional educational opportunities, many of which are advanced through the ground-breaking research underway on our campus,” said UTEP President Diana Natalicio. “This agreement with Aconity3D will enhance UTEP’s research environment, broaden the range of experiences available to our students in the Keck Center for 3D Innovation, and attract new business development that will enable UTEP graduates to remain in this region to pursue their career goals.”
This agreement will not only give Aconity3D a home in the US, but it will also attract high-end jobs for the community’s engineering students, increase UTEP’s production and service operations, and advance 3D printing through important research investigations with government agencies and industry.
“The Keck Center is a natural fit for Aconity3D as it is a recognized leader in additive manufacturing. This collaboration will enhance our technical knowledge base and expand our expertise,” said Theresa A. Maldonado, PhD, the dean of UTEP’s College of Engineering. “We can also work collaboratively toward our model to incubate startups and provide them a pool of highly qualified graduates.”
The company’s 3D printers have an open architecture system, which is different from most commercial approaches in that users can modify the parameters themselves in order to find the optimal way to 3D print a customer’s specified material. The equipment is great for research, as one needs plenty of knowledge about the technology in order to operate the 3D printers. This helps feed Aconity3D’s corporate philosophy of locating near high-tech research organizations – for instance, its German headquarters are near the Fraunhofer Institute for Laser Technology (Fraunhofer ILT). Aconity3D’s model of supporting the institute’s interns and students will continue at UTEP.
Aconity3D will begin its North American operations with only a CEO, but plans to hire up to three employees within a year. The hiring process will focus first on Keck Center graduates who have experience working with the company’s technology, as one of Aconity3D’s laser powder bed machines is already housed there.
“We have long worked on leveraging our expertise in 3D printing to build a new economy in El Paso around additive manufacturing. Our partnership with Aconity3D is a major milestone in that direction and is validation of all of our combined efforts,” said Ryan Wicker, PhD, the founder of the Keck Center. “The only way a company like Aconity3D would decide to come here is because of our technical strength in additive manufacturing, access to our graduating talent to meet their workforce needs, and the tremendous opportunities available for commercial success through collaborations with UTEP. We can apply this economic development model to build other businesses around their technologies, recruit other 3D printing businesses to our region and create new businesses from our own 3D printing technologies coming out of UTEP. As a research university, UTEP must be – and is excited to be – fully engaged in stimulating economic development for the benefit of our region.”
The long-term goal of this agreement is to set up a technical center and research space in the Keck Center, which will work with Aconity3D’s German headquarters to sell and service its 3D printers in North America. Its US base of operations will be located at UTEP’s University Towers Building.
Discuss this story and other 3D printing topics at 3DPrintBoard.com or share your thoughts in the Facebook comments below.