In just two years a robotic device that prints a patient’s own skin cells directly onto a burn or wound could have its first-in-human clinical trials. The 3D bioprinting system for intraoperative skin regeneration developed by Australian biotech start-up Inventia Life Science has gained new momentum thanks to major investments from the Australian government and two powerful new partners, world-renowned burns expert Fiona Wood and leading bioprinting researcher Gordon Wallace.
Codenamed Ligō from the Latin “to bind”, the system is expected to revolutionize wound repairs by delivering multiple cell types and biomaterials rapidly and precisely, creating a new layer of skin where it has been damaged. The novel system is slated to replace current wound healing methods that simply attempt to repair the skin, and is being developed by Inventia Skin, a subsidiary of Inventia Life Science.
“When we started Inventia Life Science, our vision was to create a technology platform with the potential to bring enormous benefit to human health. We are pleased to see how fast that vision is progressing alongside our fantastic collaborators. This Federal Government support will definitely help us accelerate even faster,” said Dr. Julio Ribeiro, CEO, and co-founder of Inventia.
Seeking to support Australia’s biomedical and medical technology sector, the Australian government announced it will invest AU$1 million (US$723,085) to supercharge the Ligõ 3D bioprinting system for regenerating skin. The project is one of 21 initiatives to receive support from the Federal Government’s BioMedTech Horizons (BMTH) program, operated by MTPConnect, a non-profit organization aiming to accelerate the rate of growth of the medical technologies, biotechnologies, and pharmaceuticals sector in Australia.
Late in July 2020, Australia’s Federal Health Minister, Greg Hunt announced that the program’s funding is expected to move the device faster into first-in-human clinical trials. Separately, the team also received funding from the Medical Research Future Fund Stem Cell Therapies Mission to collaborate with stem cell expert Pritinder Kaur from Curtin University, in Perth, to use the Ligō device to deliver stem cell-based products that could improve skin regeneration.
According to Inventia, the skin is the first point of injury in accidents and some diseases and, when significantly damaged, it heals slowly, usually leaving a scar. Moreover, throughout the regeneration process, it is open to infection, a major problem in the body’s first protective barrier, and a good enough reason to find new ways to speed up the healing process.
Focusing energies on creating a robot capable of printing tiny droplets containing the patient’s skin cells and biomaterials directly on the wound gave Inventia the potential to recreate functional and aesthetically normal skin. Moreover, the researchers behind the Ligõ technology suggest this can be achieved in a single procedure in the operating theatre, reducing treatment cost and hospital stays, and minimizing the risk of infection.
The device uses Inventia’s patented technology, which was already successfully featured in its RASTRUM platform for lab-based medical research and drug discovery. By taking this core technology into the clinic through the Ligō robot, the company expects to break new ground with some of Australia’s leaders in skin regeneration.
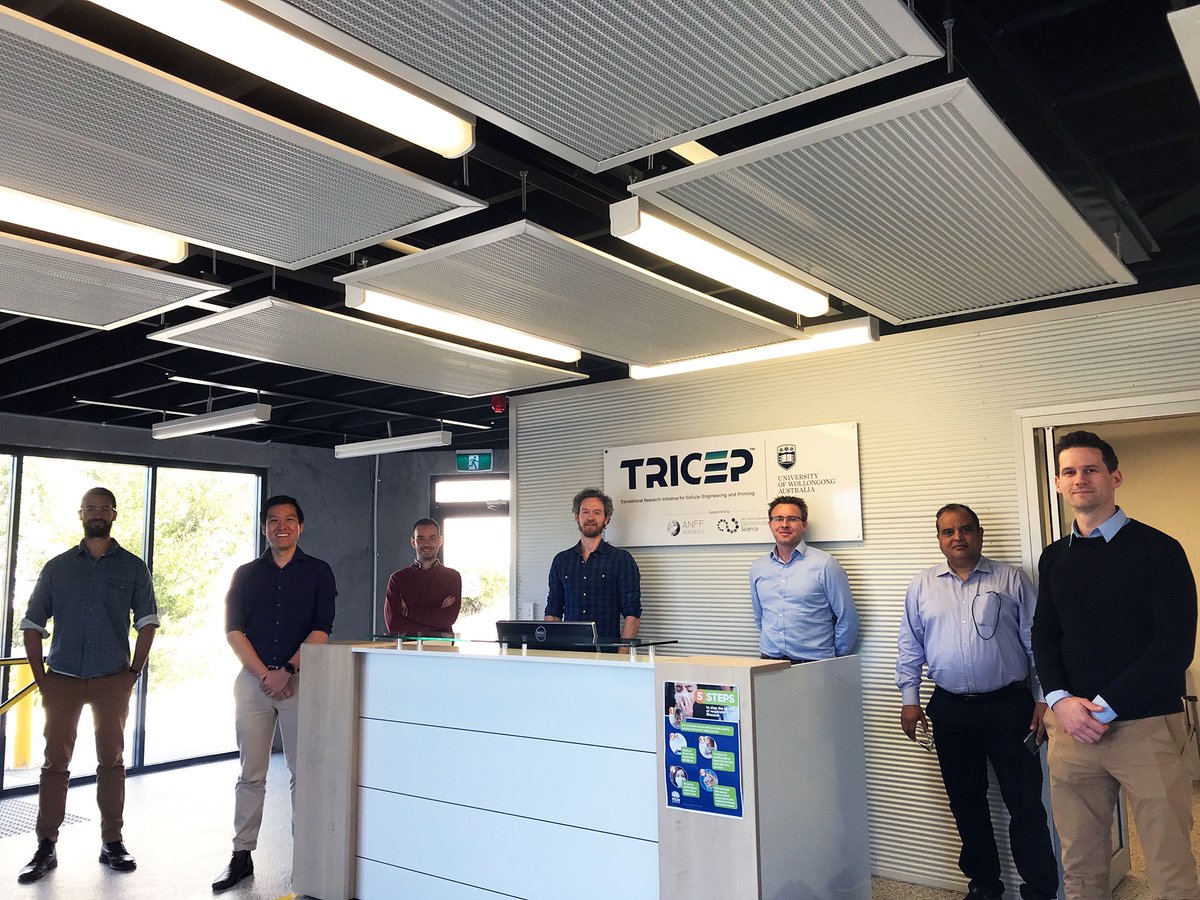
Researchers from Inventia Life Science at the Translational Research Initiative for Cell Engineering and Printing (TRICEP) at Wollongong. (Image courtesy of TRICEP)
Researchers from the ARC Centre of Excellence for Electromaterials Science (ACES) at the University of Wollongong, in Australia, will also lend their internationally renowned expertise in bioinks to develop the new 3D bioprinting system to treat burns during surgery. Led by ACES Director Gordon Wallace, the researchers will provide critical input in the bioprinter and bioink development process. This news comes as no surprise as the ACES team already had a strong working relationship with Inventia.
“ACES is at the forefront of building new approaches to 3D printing, and this project will draw on this significant success we have had in this space in recent years,” Wallace said. “3D printing has emerged as the most exciting advance in fabrication in decades, and I’m excited to continue to build our local capabilities in this area to establish a new, innovative and sustainable industry for the Illawarra [a region in the Australian state of New South Wales]. Being part of this skin regeneration project will help to put Wollongong on the map for the commercial manufacture of bioprinting technologies.”

Leading bioprinting researcher Gordon Wallace. (Image courtesy of the ARC Center for Excellence for Electromaterials Science)
For project partner Fiona Wood, a world-leading burns specialist and surgeon, and Director of the Burns Service of Western Australia, this is not the first time that she has looked towards bioengineering to help her patients. In the early 90s, the expert pioneered the innovative “spray-on skin” technique, which greatly reduces permanent scarring in burns victims, and came to notice in 2002, when the largest proportion of survivors from the Bali bombings arrived at Royal Perth Hospital.
“The combination of these grants is an excellent example of the way the Medical Research Future Fund is being applied across the continuum of translational research to commercialization, leading to better patient outcomes,” commented Wood.
Burns are the fourth most common type of trauma worldwide, with an estimated 11 million burned patients treated every year worldwide, and over 300,000 deaths resulting from serious wounds. In Australia alone Wood’s foundation reported that 200,000 people suffer burns annually, costing the Australian community over AU$150 million per year. Burn injuries are horrific and they present complex problems for both the patient and clinicians to deal with, with a road to recovery beyond easy to tackle. Inventia Skin expects bioprinting technology will be a game-changer in wound medicine. Moreover, the combined expertise of leading specialists in bioprinting and burn wounds, along with funding and support from the local government could lead to one of the most innovative 3D bioprinting systems to treat burns during surgery, and best of all, it could be available in 2022.
The post Robot Skin 3D Printer Close to First-in-Human Clinical Trials appeared first on 3DPrint.com | The Voice of 3D Printing / Additive Manufacturing.