Stratasys expands into the Oceania region, Epro Group becomes customer of F850 3D printer
How does PLA Color Influence Mechanical Properties in FDM 3D Printing?
All kinds of research has been conducted regarding the mechanical properties of 3D printing materials, such as how they are effected by things like infill density, build orientation, temperature, and porosity. Researchers Adi Pandžić and Damir Hodzic from the University of Sarajevo and Aleksa Milovanović with the University of Belgrade were curious how much the color of PLA would effect material tensile properties in FDM 3D printing, and published a paper on their work, titled “Influence of Material Colour on Mechanical Properties of PLA Material in FDM Technology.” Different colors need different extrusion temperatures in 3D printing. The additives that make your PLA a different color also have influence on how your part prints and what properties it has. This much was already known, but to which extent do the different color formulations influence your mechanical properties?
The abstract reads, “Topic of this article is to investigate whether colour of PLA material effect on material tensile properties and in what amount. It will be tested more than 10 different colours of PLA material, and for every colour it will be tested 3 specimens. Specimens are prepared according to ISO 527-2, and all printed with same 3D printing parameters and with 100% infill. Also, all used materials are of same company and for every colour specimen will be 3D printed from same filament spool. All this is done to avoid other parameters to effect on material properties. The results of this study will be useful for colour selection of the PLA material without compromising the material tensile properties of 3D printed product.”
Many parameters are taken into account when it comes to the quality of FDM printed products, including things like infill pattern, layer height, nozzle diameter, and material characteristics. Polylactic acid, or the popular PLA we all know and love, is a polymer with a melting point between 150°-160° C, and is still the reigning material on the desktop.
“By reviewing the literature it can be noticed that the greatest accent is given to the influence of parameters on mechanical properties of material. Another characteristic barely evaluated is the influence of different material pigmentations,” the researchers explained. “Today, there are many different colours of PLA material of the same manufacturer, and in most cases it is assumed to have the same mechanical properties regardless of colour. This is one of the reasons why we chose to examine whether and how much the colour of the PLA material influences the mechanical properties of the finished product.”
The team ordered 14 different colors of PLA from 3D Republika, with the same properties and characteristics, in order to investigate their potential influence on the mechanical properties of specimens made with the material. They used SOLIDWORKS to design samples according to ISO 527-2, and printed three different specimens for each color on an Ultimaker 2+, under the same conditions with 100% infill, and the “normal” profile from Cura 4.0.0 slicing software was used to prepare the G-code for the samples.
“Specimens are printed with “flat” printing orientation and 45˚ raster angle,” the researchers wrote. “Also brim around specimen is used for better adhesion with print bed and to reduce wrapping of material, after 3D printing it is removed from specimen.”
A Shimadzu AGS-X tensile machine was then used to perform tensile testing on the 42 3D printed PLA specimens. Properties like elastic modulus, strain, toughness, ultimate tensile strength (UTS), and yield strength were tested.
The team learned some interesting things, such as the fact that the red PLA had the highest elastic modulus, yield strength, and ultimate tensile strength, while pink had the lowest numbers for these. But, pink had the highest toughness and influence on strain, while blue had the lowest.
Once the testing was complete, the researchers determined the following:
• Color of PLA had an influence on elastic modulus, and varies up to 18% (from 2719MPa to 3217MPa) depending on color
• Color of PLA had an influence on yield strength, and varies up to 36% (from 30MPa to 41MPa) depending on color
• Color of PLA had an influence on ultimate tensile strength, and varies up to 31% (from 35MPa to 46MPa) depending on color
• Color of PLA had an influence on toughness, and varies over 300% (from 10J to 48J) depending on color
• Color of PLA had an influence on strain, and varies over 400% (from 7% to 108%) depending on color
“In future research, the influence of material colour on other mechanical properties (bending, hardness, pressure, etc.) should be examined, and also influence of colour on mechanical properties of other materials (ABS, PET, etc.),” they concluded.
Discuss this research and other 3D printing topics at 3DPrintBoard.com or share your thoughts in the Facebook comments below.
The post How does PLA Color Influence Mechanical Properties in FDM 3D Printing? appeared first on 3DPrint.com | The Voice of 3D Printing / Additive Manufacturing.
SmarTech Patent Reports Provide New Insights into Corporate Strengths and Strategies
SmarTech Analysis’ range of reports on patents in the Additive Manufacturing (AM) sector provides unique tools for better understanding the strengths and weaknesses of individual firms and going well beyond the usual techniques employed by industry analysts. To add power to traditional approaches, used by market analysts SmarTech’s patent reports now use a special kind of patent analysis, called p-scores. Individual patents are also given individual letter grades indicating their strength.
Specifically, SmarTech is utilizing Wisdomain’s ActionablePatents automated Patent Grading and Scoring System for quantitatively evaluating patent quality. This approach provides insights into not just patent environments but also enables the purchasers of SmarTech’s patent reports to build competitive advantage based on a deeper understanding of the patent environment. For example, SmarTech claims that readers of its patent reports will be able to secure IP in the 3D printed metals areas that are less populated, and also avoid patent disputes.
The Power of p-Scores
The technique embodied in SmarTech’s patent reports – generically referred to as p-Scores — uses a set of assessment criteria well known and practiced by patent economics. The system compares a patent with hundreds, if not thousands, of patents that share the same IPC sub-classification and evaluates specific quality attributes. Each attribute is evaluated individually to measure its unique contribution to patent quality. Each evaluation result is then applied to a weighted scale to compute a sum weight. The sum weight then used to arrive at the patent’s final p-score.
These patent scores are based on quantitative measures of inventors’ expertise, technological significance and endurance (number of patent citations and their duration); market scope (the number of families to which the patent belongs. Rejected claims reduce scope); and novelty (A patent fewer backward citations suggests there is less relevant prior art) Also taken into consideration is technological focus, which is measured by continuing patent groups that cover new aspects or improvements to the subject inventions.
Using this system, the SmarTech report scores the patents for 3D printing metals, from the strongest and most valuable to the weakest. In addition, the report identifies the top assignee companies of patents and pending applications for 3D printing metals, trends in such patents and applications, patents for 3D printing metals involved in litigation, most-cited patents, top assignees and inventors based on patent scores and inventor scores, and most prolific inventors.
Based on the p-score analysis, companies can see which patents are strong and provide a competitive or litigation edge, and which patents are likely to be invalidated if they are challenged or enforced. Such scores can also be an invaluable resource for companies enforcing or defending their patents. For example, a company may elect not to try to enforce a patent with a quantitatively derived low score. Conversely, a high patent score may help a company fend off a validity challenge. Companies challenging patents may use their low scores, which are independently generated and objectively based, to help invalidate them.
3D-Printed Metals: A Patent Landscape
It turns out that such apparently technical considerations can also provide some very powerful analytic tools, not just for pure play patent analysis, but also for better understanding how a company’s patent activities impact its overall strategy.
For example SmarTech’s recent report, 3D Printed Metals: A Patent Landscape Analysis 2019 identifies the leading inventors in the 3D-printed metals field, who they work for, and the value of their patented inventions. SmarTech’s patent analysis also reveals the degree to which the public corporate strategy of major firms in the 3D printing metals space is backed up (or not) by patent strategy.
One of the surprising conclusions of this report is that some of the most impressive patent portfolios are held by smaller firms. Velo3D, for example, is currently the top assignee of patents for 3D printing metals. SmarTech’s analysis of p-Scores also shows that Desktop Metal has many quality patents. By contrast, the more established firms are more of a mixed bag GE’s Arcam and EOS both get high p-Scores for its U.S. patents. 3D Systems does not stand out from a patents perspective, especially when considered in terms of assignee applications.
While all of these firms are “famous” players in the AM space, SmarTech’s patent analysis also reveals important “under the radar” contributors to Metal AM. For example, Boeing and United Technologies (UTI) are both forces to be reckoned with in the 3D printing metals space. Boeing’s 3D printing metals patents are widely cited, suggesting that the usefulness of these patents goes beyond Boeing’s internal needs. The SmarTech’s patent work in the metals AM space also reveals some truths about Chinese metals AM. For now, there are relatively few Chinese AM metals patents — Chengdu New Keli Chemical Science is the current leader. Also, Major players in the West are not investing in patent protection in China, since they may believe it affords them little protection.
In addition to the patent analysis itself, the report also comes with an Excel database containing 1,381 worldwide patent references for 3D printing metals and processes used to make them. This database is a valuable resource to anyone researching the worldwide patent landscape for 3D printing metals. It enables them to determine the top cited patents in their field, how many patents are being filed each year, what patent families are already claimed and where new patent rights may be available. SmarTech’s research covers both granted patents and published applications. The information is drawn from U.S., EP, WIPO PCT, Chinese, and Japanese sources.
Some of the organizations covered in this report include 3D Systems, AHMR GmbH, Airbus Defence, Arcam, Arconic, Battelle Memorial Institute, Boeing, California Institute of Technology, Daido Steel, Desktop Metal, DuPuy Synthes, EOS, ExOne, GE, GM Global Technology, HC Starck, Halliburton, Hamilton Sundstrand, HP, Honeywell, Illinois Tool Works, Jiangsu Boqian New Materials, Johnson Matthey, Kennametal, MIT, Norsk Titanium, Raytheon, Ricoh, Sciaky, Siemens Energy, South China University, Texas A&M, United Technologies, University of Texas, Velo3D, Xerox, and others. Learn more here.
The post SmarTech Patent Reports Provide New Insights into Corporate Strengths and Strategies appeared first on 3DPrint.com | The Voice of 3D Printing / Additive Manufacturing.
UrbanAlps and Fieldmade to 3D print Stealth Keys on-demand for the military
Blooming Time: A Mechanical Flower
Beautiful project-in-progress from Samantha Song up on Hackster.io.
When I was young, I loved to play with plants, and one of my favourites is the mimosa plant, which will close when touched. However, in fantasy tales, flowers would open when they are touched, and I wanted to recreate this magical effect in my project.
With the 1 year anniversary of my boyfriend and I nearing, I wanted to dedicate to him a special present that I made myself, hence the birth of this flower. As both of us are forgetful people, I wanted the flower to remind us of special days, with the flower lighting up in a colour for each important day. On each day of the week, one of the petals will light up, reminding you of the day of the week in a unique and fun way. Not only is it a beautiful timepiece, when the flower is touched and “open”, it will also tell you the temperature, humidity, date etc., giving it a useful daily function.
British Airways posts top ten predictions for the use of 3D printing in planes
ETH Zürich researchers develop novel glass 3D printing method
Middle East Architecture Network creates 3D printed pavilion made from 30,000 water bottles
2019 Year in Review: Industrial 3D Printing
We continue to see industrial 3D printing increase in speed, size and capability, while dropping in cost as signs point to its integration into the larger manufacturing industry. This year, there were a number of announcements that reinforce this trend, including mergers, acquisitions, partnerships and product releases.
Service Bureaus
This was one of the more important stories of the year, in this author’s opinion, in that it solidified BASF as more than a periphery agent in the AM space. The largest chemical company in the world had slowly been spready its tendrils into the space, developing materials for companies like HP and then acquiring Innofil3D, Advanc3D Materials, Setup Performance, Forward AM. It also continues to develop materials to new 3D printing processes. In addition to Multi Jet Fusion (MJF), BASF has teamed with Paxis, Impossible Objects and Origin for material development.
With the acquisition of San Francisco- and Paris-based service bureau Sculpteo, BASF has established itself as a major player. The fact that it has also invested $25 million in 3D printing software and service company Materialise indicates that it is making significant bets on the service bureau space, with its materials fueling those efforts.
BASF may be the largest chemical company in the world but it’s not the only materials giant in the 3D printing industry. DuPont, Mitsubishi Chemicals, Covestro (Bayer spin-off), Arkema (spin-out of French oil giant Total), Henkel, DSM, Evonik and others were also very active in the space this year (though of course that is to be expected).
Meanwhile, another service bureau marketplace, Xometry, has continued to grow. After closing a $50 million Series D investment earlier in the year, the startup acquired Europe’s largest on-demand manufacturing marketplace, Shift. This will allow it to expand into 12 new countries and access a network of over 4,000 manufacturers.
GKN has also continued to grow its AM activities, acquiring more metal powder makers and California-based 3D printing bureau FORECAST3D, which complements the group’s existing HP Metal Jet technology with a large fleet of Multi Jet Fusion 3D printers. Additionally, GKN Powder Metallurgy opened a third customer center in Germany and one in Michigan, which also serves as its North American headquarters.
Siemens
After completing what it claims was a successful pilot program, Siemens officially launched its Siemens Additive Manufacturing Network, which allows customers and suppliers to connect for their production needs. It will also integrate HP’s Digital Manufacturing Network and include large manufacturers, including the world’s biggest sporting goods retailer, Decathalon. The tech giant is also working on an end-to-end AM workflow that includes digital inventory, part and cost analysis, production tracking, RFQ processing and scheduling.
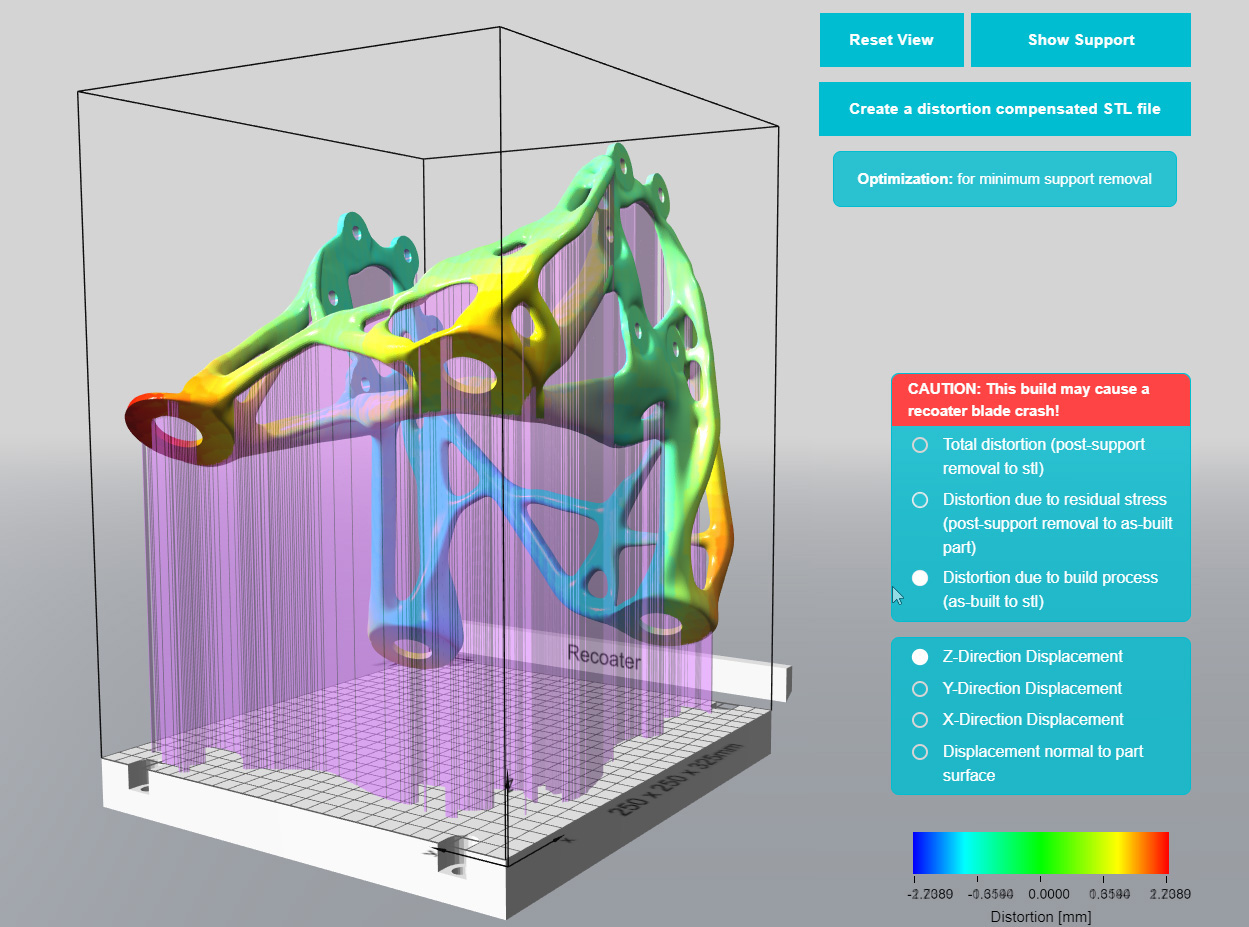
Atlas3D is capable of quickly orienting parts and adding support structures to minimize distortion in DMLS.
Siemens also acquired Atlas3D, which has developed a cloud-based software for automatically orienting parts for metal 3D printing and generating support structures through the use of thermal distortion analysis.
HP and GE Additive Continue to Grow
Having already released its flagship series, metal 3D printers and color 3D printers, HP launched its Jet Fusion 5200 Series, meant to be the company’s new production line. The 5200 series is marketed as more productive, accurate, consistent and efficient than the preceding 4200 line. This was followed up with the opening of a new 150,000-square-foot R&D center in Barcelona. HP also announced a partnership with Rösler AM Solutions to develop automated post-processing technology.
GE Additive opened a new 40,000-square-meter campus in Lichtenfels, Germany, which will serve as the new headquarters for Concept Laser. Investing in itself further, GE Aerospace purchased 27 new Arcam electron beam melting systems for GE9X blade production.
Mass Production Technologies
Upon receiving yet another round of massive funding in 2019, Carbon, which boasts its digital light synthesis as capable of mass production, secured new partnerships for the large batch manufacturing of bicycle parts for Specialized and fizik, eyeglasses for JINS, nightguards and splints for Keystone Industries, and car parts for Lamborghini.
Additive Industries also suggests that its modular MetalFAB1 3D printer is suited for mass production and, in addition to selling six of its expensive metal 3D printers to a US aerospace company (and later on a seventh!), it partnered with Airbus and Premium AEROTEC subsidiary APWORKS to further certify its technology for serial production of aerospace parts.
HP’s MJF is also designed for mass manufacturing, which was further demonstrated when Smile Direct Club announced the use of the technology to 3D print over 50,000 dental aligner molds per day.
Niche Sectors
Sectors ripe for additive disruption are starting to gain more attention. In particular, the railway sector has seen more activity related to 3D printing. Stratasys, for instance, partnered with Angel Trains in the U.K. in a pilot program that has 3D printed four passenger armrests and seven grab handles for Chiltern Railways. Europe’s “Mobility goes Additive” network made the first 3D-printed safety-relevant component for rail: a metro brake unit that is already being used in Hamburg, Germany.
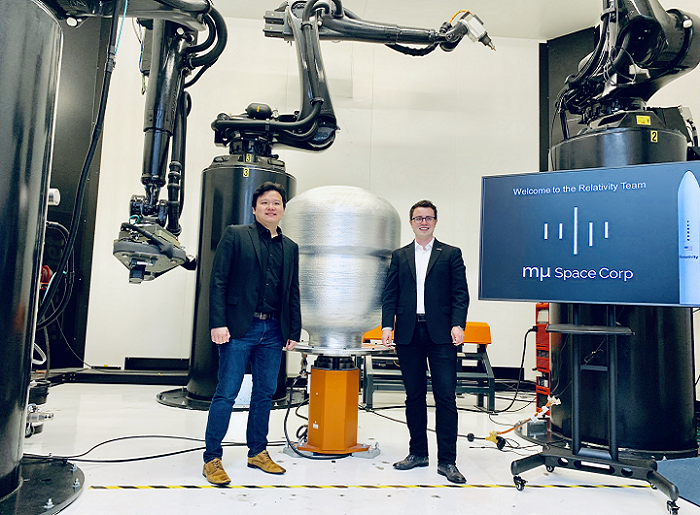
mu Space CEO & Founder James Yenbamroong and Relativity Space CEO & Founder Tim Ellis stand in front of Relativity’s Stargate, the world’s largest metal 3D printer.
In addition to rail, the marine and space industries have been impacted by AM. Companies like Relativity Space, Launcher and Rocket Lab (if you count news from last year) are all working on 3D-printed rockets for use in the launch of small payloads. And this is beyond the existing work with mainstream launch companies like United Launch Alliance and Space X. German steel giant thyssenkrupp has also made continuous headway into the maritime field, certifying a facility for 3D printing marine parts and partnering with a large shipping firm for the 3D printing of spare parts.
All of this paints a picture in which 3D printing for end part production is no longer experimental, nor is the entry of large and unique businesses into the space. AM is still far from saturating the much, much, much larger manufacturing industry, but it now has a significant foothold.
The post 2019 Year in Review: Industrial 3D Printing appeared first on 3DPrint.com | The Voice of 3D Printing / Additive Manufacturing.