Kodak announces Design to Print Service for Portrait 3D printer at RAPID+TCT
Fast Things: Faster Products & Profits Through 3D Printing
Bricks and mortar retail has been going through an extended crisis for many years now. The rise of online retail, shifts in consumer behavior and the fragmenting of collective media have wreaked havoc on their businesses. Many iconic chains, brands, and department stores have gone under. The middle seems to be eroding with either maximum distribution formulas such as Primark offering the absolute lowest prices or rare ultra expensive goods being the most desirable. People still shop, as a fun activity. There are some chains in fast fashion such as Inditex (parent company of Zara, Pull & Bear, Bershka), Fast Retailing (Uniqlo), bestseller (Vero Moda, Only) & H&M that do well.
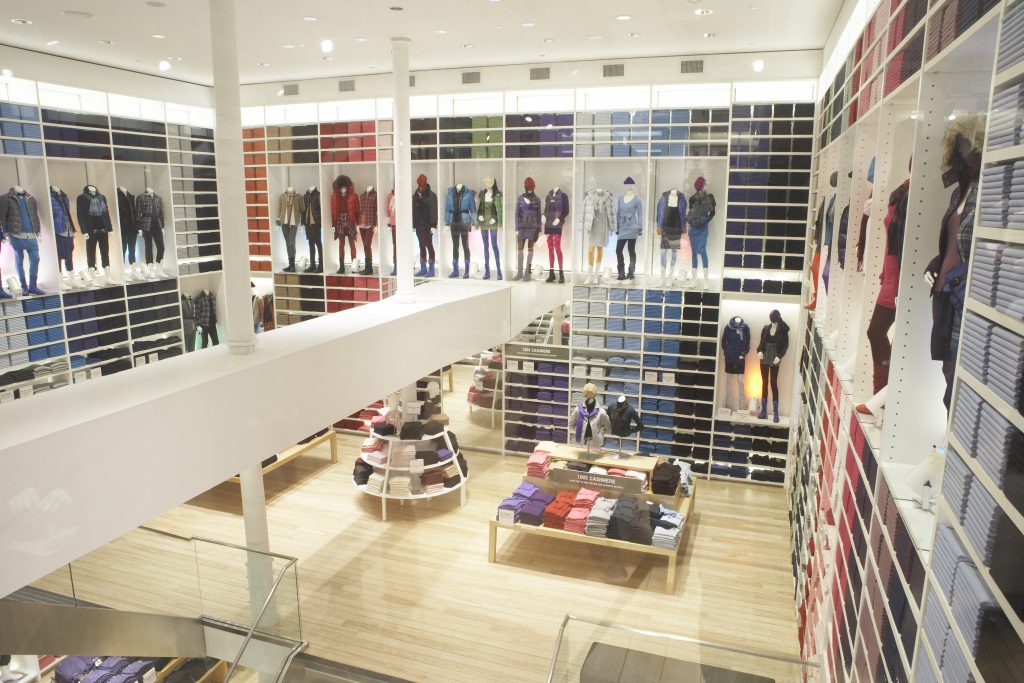
Interior of a Uniqlo store
These stores have their own design, procurement, distribution, and retail operations. They sell their own brands under their own roofs. It seems that you either have to be cheap, hyper-expensive or fast. The fast option seems to be a happy medium between having margins and profits coupled with global reach. There is also some kind of secret sauce to these businesess and how they choose, build and manage brands and lines. At the moment the kings of fast fashion trade blows amongst each other but seem unassailable. It used to be that stores would design collections two years in advance. They would estimate demand for individual articles and order them from suppliers in Asia. Some of the fast retailers do this still but they are all much faster than department stores and other brands are at responding to trends.
The fastest firm is probably Inditex, this very vertically integrated company which near shores most of its current items and sends basics to asia, can go from design to in store item in two weeks. If it takes me two years to plan ahead and you can plan two weeks ahead based on in store data and the very latest in trends then eventually you will win. Better more up to date data coupled with faster more market responsive research will win out every time on a firm trying to predict the future 24 months out.

Uniqlo display in Germany.
So what if we take 3D printing into account and see if we can do this in retail also? What if we can print close to the customer, quickly in response to the latest data and trends? What if we didn’t tie up all our money and operations in stock? What if instead we printed on demand in a retail location? You may think that this has been tried but apart from some small 3D print shops this has actually not been tried in any kind of capital intensive way.
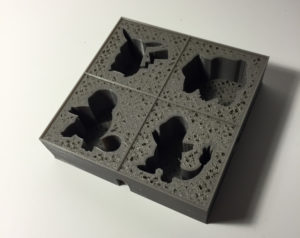
3D Printed Molds
You may think that 3D printed goods are not good enough in terms of color and surface finish.
- But for many products where 3D printing is a mold the finished product can pass muster as an end use product. Think of cookies, chocolate, slippers, insoles, sports gear handles, glasses and many more items where customization is possible, at a good surface finish, at low cost through direct or intermediate.
- Surface finishing solutions such as DyeMansion are also making consumer-friendly 3D printed goods more affordable.
You may think that 3D printing is too expensive.
- That may be the case for larger items but anything the size of a softball or smaller can be cost effective if you go through the trouble of sourcing your own material.
- This can reduce the cost from $800 per liter to $40 for SLA or $95 to $30 for SLS or $30 to $5 for FDM.
You may think that 3D printing is not fast or reliable enough.
- With an array of cost-effective 3D printers, you can now manufacture at scale, at low item cost at around a 90% success rate which sucks but works if you give yourself the time to start multiple builds.
- Yes an iPhone case could take five hours or an entire day depending on the technology but if the post-processing solution, material sourcing and manufacturing is low cost enough you can still do in day or next day customization.
- This means people have to come back to the store which actually may be advantageous.
You may think that 3D printing is too limited in color, materials, textures etc. You’d be absolutely correct.
- But we don’t have to 3D print the entire backpack we can customize the name tag, clasp or part of the item.
- I call this combinatory manufacturing, using a 3D printed higher performing higher cost small thing to improve a mass manufactured one of a million thing.
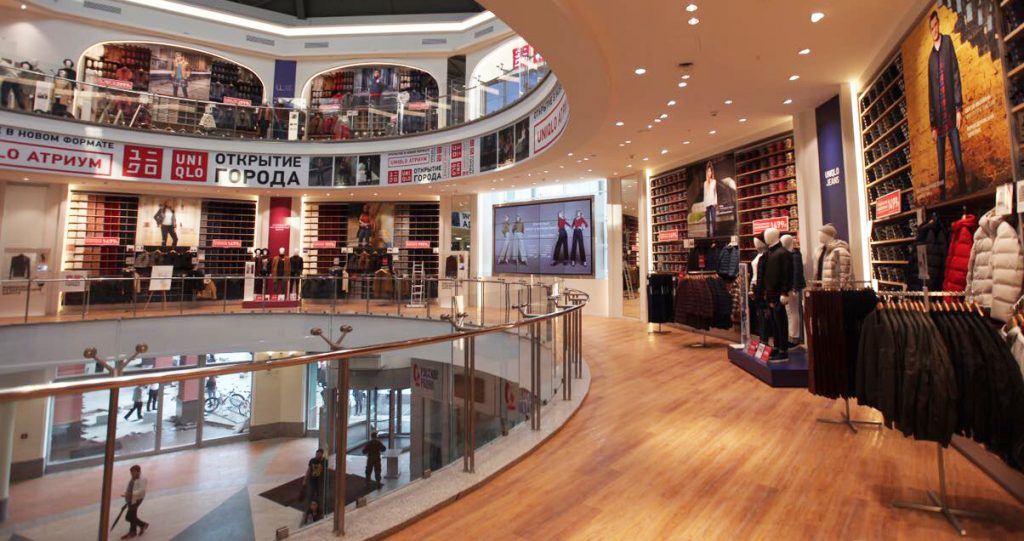
Uniqlo in Russia
You might say that customers may not like customization, or they may not like the effort or they may not pay more for it. And you would in many cases be absolutely right.
- But, for some items customization would be key. I mean for me, I wouldn’t need to customize all the things one Invisalign or hearing aids like product would be fine.
- And its not just about customizing to the individual user. You can customize for local (high school) football teams, events and tastes to 3D print the latest fashion.
To me the future is clear, through fast things some will be able to rapidly outcompete other companies. By using 3D printing in retail a new impulse and a new category of products will be unlocked. The future is fast things. I’ll write a series of articles on this subject including: the desire engine, make it in the store & 3D printing velocity.
Ashley Furniture Uses 3D Printing & Robotics in Manufacturing Processes
Founded in 2005, Wisconsin-headquartered Ashley Furniture is a company known globally, beginning in 1970 with 35 employees, and growing now to over 900 stores. Ashley facilities manufacture over 300,000 pieces of furniture a week—and as operations move at a rapid pace, they not only focus on efficiency but also continued improvement and the ability to think of unique solutions to problems that may be typical.
Factories rely on robots for some jobs, but 3D printing has ‘trickled onto the factory floor and gradually reorganized manufacturing processes from fabrication to assembly, continuing in line with their commitment to staying competitive and embracing progressive technologies, as well as combining them.
“If we don’t have that culture of change, that’s going to start to prohibit our growth. We have to be willing to identify what that change is going to be, and figure out how to best incorporate that into our processes and operations—and teach our employees why we need to make that change, how we can make it, and empower them to help us make it,” said Vaughn Pieters, senior director of casegood operations.
3D printing is a great example of the furniture leader’s commitment to better and more expedient production processes. The company has always been extremely willing to listen to employees with ideas—and especially those that cut time and costs and allow for more creativity and better productivity.
“We started out just making one simple sample, because we could make that sample in a matter of a few hours versus having to potentially source from an international vendor that would take weeks. We were able to use 3D printing technology to compress some of those timelines and make better more educated decisions with our design staff,” Pieters said.
“Now we’ve continued to grow that with how we use 3D printing technology to make components that help us run our day-to-day business on the manufacturing floor.”
3D printing allows the company to adapt components more easily to ‘end operator suggestions.’ And the more employees learn about 3D printing, the newer ideas they come up with, along with ways to improve productive further.
“The employee actually has the ability to say ‘Hey, I think that this idea will help us to make our process more efficient or effective.’ So that does us several things: it helps the business continue to be more efficient, more effective, and to get more product done in the same amount of time, and the employee gets a bonus for providing that information,” Pieters said.
“If you don’t have that employee buy-in at the ground level, the change is that much more difficult to become successful with. It’s a win-win, and it really helps keep our management and our employee team that much more connected. I think that the way we have such a great relationship all the way from our owners to our manufacturing floor employees and that open communication line does great things for our business.”
Because there have been such shortages of help, however, Ashley Furniture has had to learn more about technology like robotics and 3D printing and integrate it into their business. Their version of working smarter has been to offload heavy, physical work to robots, while employees are able to work and use their minds. 3D printing also allows for enormous savings in time, such as when introducing a new SKU, and company engineers can adapt a design quickly for production.
“We’ve literally replaced fixtures that are three feet by six feet with a simple bin system; it’s a two-minute setup time.” Konkel said. “It frees up jig builders from repetitive task to work on more pressing issues, from busy work to looking at more challenging items.”
“Things like 3D printing and automation are making the job easier for the employee so that it’s not so heavy and not so industrial,” Pieters said.
Processes became much more streamlined when Ashley Furniture brought in the Formlabs Form 2 3D printer. More products could be created in house, and with better performance and surface quality. Both Formlabs 3D printers on-site currently run 40 hours a week.
“Having the Form 2 and the ability to 3D print parts has allowed us to steer away from some of the traditional ways that we develop fixturing and tooling,” Konkel said. “It gives us the ability to quickly adapt to any suggestions or to any needs that we have and create geometries that we’re not traditionally able to manufacture or machine. We’re able to do things that weren’t quite possible several years ago.”
3D printing has been built on people pushing boundaries, and it continues daily. The furniture business has been duly affected also as consumers are given the opportunity to virtual shop, use 3D printed connectors for modular designs, and enjoy futuristic pieces. What do you think of this news? Let us know your thoughts; join the discussion of this and other 3D printing topics at 3DPrintBoard.com.
[Source / Images: Ashley Furniture]
ASTM International’s Advanced Manufacturing Center of Excellence launches second R&D funding round
Titan Robotics debuts dual-extrusion pellet 3D printer in Detroit
3D Printing a Chess Set and Laser Burning a Chess Board
New Layer By layer – PyBadge Case
With the release of the Adafruit PyBadge I thought I’d create a tutorial on making a case. What I thought would be a single video ended up becoming a three part series. This mini series we’ll walk through the process and show case tips along the way. We’ll learn how to design and model a parametric enclosure driven with user parameters in Fusion 360.
Part One – Initial Design
The first six minutes talks about PyBadge, MakeCode Arcade and the case. In this first installment we’ll import the PyBadge PCB and use a joint for placement. Create user parameters and sketch out the initial enclosure. Use construction planes and components to create the top and bottom parts of the enclosure.
Part Two – Cutouts
Picking up right where we left off, in this episode we’re going to create the proper cut outs for the buttons, display, neopixels, and light sensor. We’ll also create a stylish notch to expose the on/off switch and micro USB port. Excellent!
Part Three – Snap Fits
In the last installment of this mini series, we’re creating snap fit features. Instead of drawing them within the document, we’ll import it as an external component and customize user parameters to create snap sets with different lengths.
Part One
https://youtu.be/C-31tlBQtuc
Part Two
https://youtu.be/NVSQzi-dQMk
Part Three
https://youtu.be/pfBXfgCTmAU
PayBadge
https://www.adafruit.com/product/4200
PyBadge LE
https://www.adafruit.com/product/3939
MakeCode Arcade
https://arcade.makecode.com/
PyBadge PCB on Github
https://github.com/adafruit/Adafruit_CAD_Parts/tree/master/4200%20PyBadge
PyBadge Case Learn Guide
https://learn.adafruit.com/pybadge-case/overview
PyBadge Case Project Video
https://www.youtube.com/watch?v=rTxf4x6bQPc
3D Printing Projects Playlist:
https://www.youtube.com/playlist?list=PLjF7R1fz_OOWD2dJNRIN46uhMCWvNOlbG
3D Hangout Show Playlist:
https://www.youtube.com/playlist?list=PLjF7R1fz_OOVgpmWevin2slopw_A3-A8Y
Layer by Layer CAD Tutorials Playlist:
https://www.youtube.com/playlist?list=PLjF7R1fz_OOVsMp6nKnpjsXSQ45nxfORb
Timelapse Tuesday Playlist:
https://www.youtube.com/playlist?list=PLjF7R1fz_OOVagy3CktXsAAs4b153xpp_
Custom Stencil Frame for TinyPICO PSRAM
3D Printing News Briefs: May 19, 2019
We’ve got business news and materials news for your weekend, just ahead of next week’s massive RAPID + TCT show. 3D Hubs and AM Ventures are both opening new offices, but in vastly different countries. BASF 3D Printing Solutions is launching a new TPU material for use with HP’s latest 3D printer series, and Freeman Technology will be hosting a seminar about AM powders next month.
3D Hubs Opening US Headquarters in Chicago
Two months ago, automated manufacturing platform 3D Hubs announced that it had received $18 million in Series C funding, some of which was earmarked for opening a dedicated US office to best serve the over 10,000 clients it serves here. Now, the company has announced that its new North American headquarters will be located in Chicago, Illinois, with the added bonus of an endorsement from the city’s Mayor Rahm Emanuel. This decision allows 3D Hubs to centralize its US workforce, and it plans to double the team at headquarters by the end of 2019. The offices will be located at the mHUB technology innovation center in the city’s West Town neighborhood, and are scheduled to open next month.
“3D Hubs joins the long list of international companies choosing Chicago for their future. With our growing tech economy and strong digital manufacturing community, Chicago is the perfect home for this innovative company,” said Mayor Emanuel. “I look forward to seeing 3D Hubs success in Chicago in the years to come.”
AM Ventures Opens Office in Korea
Germany-based AM Ventures Holding GmbH (AMV) is a top independent strategic investor in the AM industry, and over the last four years has been busily setting up an ecosystem of sustainable strategic investments, in addition to a partner network for using advanced manufacturing technologies in serial production. Now in an effort to further grow its technology venturing activities, it is expanding to the Asia Pacific region with a new office in Busan, Korea.
AMV’s Chief Venturing Officer Arno Held said, “AMV is pleased to announce the opening of its new office in Korea serving the Asia-Pacific region, a market which is already demonstrating active AM adoption for serial production and a large growth potential. AMV commits to this dynamic region and the investment opportunities available there.”
Having already moved to its new Korean home , AMV’s liaison office AM Ventures Asia has appointed Simon (Sangmin) Lee, a previous sales manager at the Korea office of EOS GmbH, as the Regional Director of Asia.
BASF 3D Printing Solutions Launches Ultrasint TPU Powder
Rüdiger Theobald, the Senior Manager for Sales & Marketing in Powder Bed Fusion at BASF 3D Printing Solutions GmbH, discusses the company’s new Ultrasint TPU powder in a recent YouTube video. The highly flexible yet accurate material, which is perfect for automotive applications and coating and simulation solutions, was launched specifically for HP’s new Jet Fusion 5200 series.
“Two great brands, two great companies merge together, both with innovative technologies on hand and a great new ecosystem to support the industry with a very innovative material,” Theobald said in the video.
“We have found out a good way to operate with different wall thicknesses, that makes it very reasonably usable for any kind of pressurized applications in regards of liquids or gas.”
Freeman Technology to Host Seminar on AM Powders
Next month, powder flow specialist Freeman Technology will be hosting a free seminar in the UK entitled “Understanding Powders for Additive Manufacturing.” The one-day event, which will take place on June 11th at the Hilton Birmingham Metropole, will introduce attendees to the principles of powder rheology, and explain how associated methodologies can also be applied in order to gain a better understanding of how to optimize powder for AM applications.
During the seminar, there will be a presentation from Freeman Technology’s Operations Director Jamie Clayton about understanding and measuring powder flow and behavior. Industry experts, such as Ricoh Material Specialist Enrico Gallino and Product Manager Cathryn Langley with Malvern Panalytical, will present about some of the major challenges when it comes to powder handling, including how to quantify the size and shape of metal powders for AM. Delegates will also have the chance to see a demonstration of the company’s FT4 Powder Rheometer. You can register for the seminar here.
Discuss these stories and other 3D printing topics at 3DPrintBoard.com or share your thoughts in the Facebook comments below.