Researchers from both Mexico and Costa Rica have joined efforts to further research into bone regeneration via bioprinting, allowing doctors and surgeons to create patient-specific scaffolds for improved treatment. 3D printing and tissue engineering show great promise for scientists because of the opportunity to build complex geometries, with precision. All the classic benefits of 3D printing are enjoyed during these experiments too, like affordability, speed in production, and best of all—the ability to create on-demand in the lab, manufacturing and making changes to structures in a completely self-sustained fashion.
The team of researchers detail their findings further in ‘Biocompatibility of Developing 3D Printed Tubular Scaffold Coated with Nanofibers for Bone Applications’ explaining how bone scaffolds can be improved further with an added composite layer that creates a layer more conducive to cell attachment and uniform seeding. To create these scaffolds, the team used a unique air jet spinning (AJS) technique, featuring a specialized spinning system nozzle and a surface for collecting polymer fibers and compressed gas—and they also 3D printed tubular scaffolds with PLA, featuring ‘submicrometric fiber surface coating in the biological response of human fetal osteoblast cells (hFOB).’
This new method uses both the inner core of the PLA 3D printing material and the outer layer of its nanofibers, with the researchers using Cura software for internal geometries and a MakerMex 3D printer to manufacture the tubular structures. The dual technique allowed the team to create a fiber layer dispersion resulting in a surface with ‘homogeneous thickness distribution’ and nanofibers adapting well to merging with the 3D printed scaffold. Adhesion was noted as ‘very strong,’ with the composites showing an increase in thermal stability, and the coating imbuing the tubular scaffold with properties critical to tissue engineering for bone regeneration.
“The 3D surface of the printed tubular scaffold exhibited distinctive morphologies and structures analyzed by SEM, and the surface roughness of the tubular scaffolds increased with the incorporation of the coating functionalization by the fiber membrane,” concluded the authors.
“Moreover, scaffolds coated with submicrometric fibers allow hFOB cells to adhere and proliferate better than uncoated 3D tubular scaffolds showing that the fibers work as a platform to improve cell biocompatibility (being not toxic to cells) and provide support to colonization and cell growth by the osteoblast cells. Moreover, the 3D tubular scaffold coated with fibers needs more studies as a biomineralization process for it to have a potential future use in bone tissue engineering or for it to have an application in the vascularization process.”
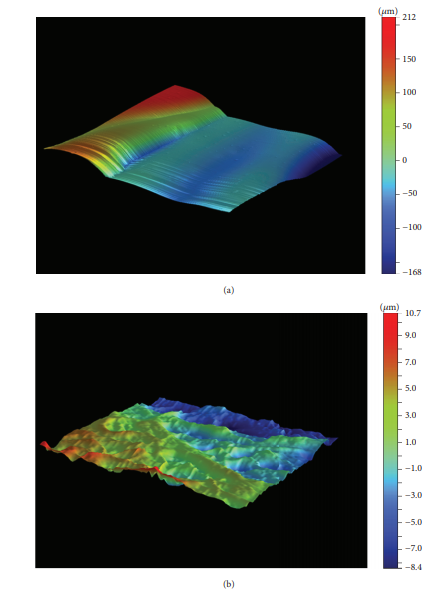
Optical profiler data showing the topography of a 3D-printed tubular scaffold. (a) Images show the uncoated smooth surface and
(b) the coated surface where roughness is strongly enhanced by the presence of nanofibers.
The field of bone regeneration is fraught with challenge, but doctors and surgeons press on to make improvements in both surgical techniques and devices such as implants so that they can improve the quality of life for patients who may be debilitated or in great pain. Researchers have engaged in many different studies over the years regarding 3D printing, producing devices such as implants made just for patients in China, bone scaffolds created at low temperatures, and other different types of bone scaffolding platforms. What do you think of this news? Let us know your thoughts! Join the discussion of this and other 3D printing topics at 3DPrintBoard.com.
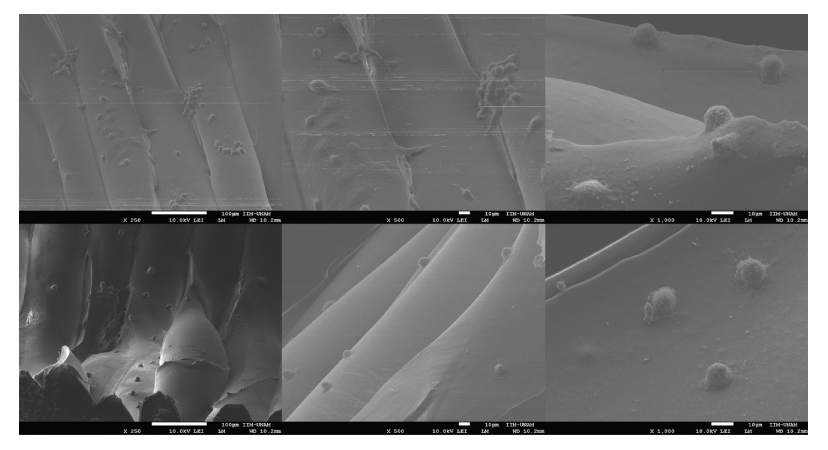
SEM micrographs of the 3D tubular scaffold surface seeded with hFOB cells showing some cells with an oval to spindle-shaped morphology typical of osteoblasts cells.
[Source / Images: ‘Biocompatibility of Developing 3D Printed Tubular Scaffold Coated with Nanofibers for Bone Applications’]