3D Hangouts – Episode #196 – Paddle Wheel Rover #3DThursday #3DPrinting
CRICKIT Powered Paddle Wheel Boat
https://learn.adafruit.com/crickit-boat/
Get CRICKIT from DigiKey
https://www.digikey.com/short/jrzr03
3xAA Battery Holder
https://www.adafruit.com/product/3842
2-pin Wire Joints
https://www.adafruit.com/product/3786
3xAA WaterProof Battery Holder
https://www.adafruit.com/product/771
Motion Control Screwdrive
https://www.adafruit.com/product/3856
3D CAD Models of Adafruit Boards and Components
https://github.com/adafruit/Adafruit_CAD_Parts
Saving out projects in Fusion 360 by Chris Young
http://tech.cyborg5.com/2018/07/28/workaround-for-saving-fusion-360-projects-with-linked-components/
Glitter Pink PLA from Proto Pasta
https://www.proto-pasta.com/products/cupids-crush-metallic-pink-htpla
Timelapse Tuesday – Flexy Stego Dual Extruded
https://www.thingiverse.com/thing:3029064
Community Makes
https://www.thingiverse.com/make:518794 facecase pi
https://www.thingiverse.com/make:518589 pi grrl 2
https://www.thingiverse.com/thing:3027514 pigrrl 2 remix
https://www.thingiverse.com/thing:3014112 tesla charger hanger remix
https://www.thingiverse.com/thing:3009560 pigrrl zero remix
Every Thursday is #3dthursday here at Adafruit! The DIY 3D printing community has passion and dedication for making solid objects from digital models. Recently, we have noticed electronics projects integrated with 3D printed enclosures, brackets, and sculptures, so each Thursday we celebrate and highlight these bold pioneers!
Have you considered building a 3D project around an Arduino or other microcontroller? How about printing a bracket to mount your Raspberry Pi to the back of your HD monitor? And don’t forget the countless LED projects that are possible when you are modeling your projects in 3D!
The Adafruit Learning System has dozens of great tools to get you well on your way to creating incredible works of engineering, interactive art, and design with your 3D printer! If you’ve made a cool project that combines 3D printing and electronics, be sure to let us know, and we’ll feature it here!
‘3D Printer Host’ Monitors Your 3D-Prints with Alexa, Arduino, Pi, and OctoPrint | #thingspeak #3Dprinting #3DThursday
High school student and maker Miles Nash built this impressive ‘3D Printer Host‘ for checking in on the status of his 3D-prints with the aid of Alexa as well as a Feather HUZZAH with ESP8266 coupled with a LED ring for visual status indication; a Pi 3 Model B is running OctoPrint and provides the status updates of the printer host.
Check out the description below and the full project here on Hackster!
When I start a 3D print I don’t sit around waiting for it to finish so I can start another one, I get up and do something more productive. This though, can sometimes lead to problems like me forgetting whether or not my printer is currently printing or wondering how much time it will be until I can start another print. The desire to be able to remotely monitor my print led me to OctoPrint, a program which when loaded onto a raspberry pi and connected to a 3D printer lets the printer be controlled and monitored from a website. Though this helped, I wasn’t a fan of having to pull out my phone every time I was curious of my 3D printer’s state. So, I made it even easier for myself to check on my printer by creating what I call 3D Printer Host.
3D Printer Host is a do it yourself electronic device created with a wifi enabled Adafruit Feather, a Neopixel ring, and a 3D printed enclosure. The device connects to OctoPrint via its API and the wonderful OctoPrint API library for Arduino. It displays the print’s progress as well as state on the Neopixel ring. The 3D Printer Host also connects to Alexa via Thingspeak and a custom skill which allows a user to ask Alexa about many aspects of their printer and find details about any current print. Though the way in which this device functions may be confusing, it is all easily explained in the following diagram.
3D Printer Host is a do it yourself electronic device created with a wifi enabled Adafruit Feather, a Neopixel ring, and a 3D printed enclosure. The device connects to OctoPrint via its API and the wonderful OctoPrint API library for Arduino. It displays the prints progress as well as state on the Neopixel ring. The 3D Printer Host also connects to Alexa via Thingspeak and a custom skill which allows a user to ask Alexa about many aspects of their printer and find details about any current print.
BASF and Reebok to Release Additional 3D Printed Liquid Speed Shoes, More Projects in Development
Multiple major shoe manufacturing corporations have been turning to 3D printing over the last couple of years. While 3D printed shoes aren’t filling shoe stores just yet, companies are being attracted to the technology for its design potential and customization possibilities. Now we’re in the age of the small series of exclusive 3D printing shoe. Earlier this year, Nike introduced the first shoe with a 3D printed upper, while New Balance has led the way with the first partially 3D printed shoe to be made commercially available. And in 2016, Reebok introduced the Liquid Speed shoe, which uses liquid developed by BASF to draw a frame directly onto the shoe. This allows for a tighter fit, and it’s pretty cool-looking, too.
The technique also does away with the traditional mold-driven process, which is expensive and time-consuming, and allows for localized production. Currently, nearly all athletic footwear is made in Asian factories due to the labor-intensive nature of the mold process, but thanks to Reebok’s 3D printing technology, the Liquid Speed shoe can be made anywhere, including in the company’s Liquid Factory, which is located in Rhode Island.
“The point of automation is to shorten the production cost and enable that automation,” said Chau Nguyen, Market Segment Manager for Footwear, PM North America, BASF. “So instead of a person sitting there and putting a sole on, they were able to dispense it in 3D on the part itself— that saved a lot of time.”
Reebok approached BASF, which it had worked with before, about creating a polyurethane material that it could use to create a unique outsole. BASF formulated a urethane-based liquid that could be drawn on to create an outsole that melds with the lacing on the shoe.
“We provide the material to Reebok that has the required rheology and reactivity to produce a part with no molds,” said Nguyen. “Look at it as if drawing with ketchup. When you draw with this material, it’s already curing, it’s already started to solidify.”
Comfort is key in any shoe (except some formal wear), but especially running shoes, where performance depends largely on how comfortably the shoe fits. The design of the Liquid Speed shoe allows for an especially secure and comfortable fit, according to Nguyen.
“In this case the outsole has wings on it and it wraps around to the sides of the shoe. You have tension at the top of your foot, and usually all of the materials are combined together,” he explained. “Well, in this case you have material attached to the sides, the medial and the lateral parts of your foot, so you get a more custom fit.”
Nguyen also calls the shoe the first high-rebound outsole. Until now, most outsoles have been made from rubber, but the polyurethane allows for better rebound.
“When you’re running, a certain amount of energy is going to the ground,” he said. “So, when you hit the ground, in this case, it absorbs the energy and then it returns it, that’s why it’s called high rebound.”
When the Liquid Speed shoe was first released in November, only 300 pairs were made, and they sold out within hours for $189.50 each. The first batch was so limited because Reebok was borrowing lab time, but now that it has opened its own Liquid Factory, there will be more extensive releases in the future. Reebok is working on additional footwear products with help from BASF, as well.
“The various chemistries provided by BASF—we have separate chemistries for cushioning, durability and support— are central to these creations,” said Bill McInnis, Head of Future at Reebok.
So keep an eye out for Liquid Speed to reemerge on the market before long, as well as some new developments from Reebok. As 3D printed shoes become more easily and frequently made, costs will likely go down as well, making them more accessible – Liquid Speed shoes are already relatively inexpensive compared to some of the other 3D printed shoes that have been released. Many of these other shoes have been made specifically for professional athletes, but Reebok seems to have the average consumer in mind.
Discuss this and other 3D printing topics at 3DPrintBoard.com or share your thoughts below.
[Source: BASF/Images: Reebok]
How did Formlabs get to become a unicorn and what are the implications of this for our Industry?
Yesterday we learned that Formlabs obtained an additional $15 million in funding from New Enterprise Associates making it estimated to be worth a billion dollars. We told you about that story and the immediate implications here, and now we have some analysis. This gives it coveted unicorn status amongst startups since so few privately held start-up companies are worth over a billion dollars. At first blush this unicorn status is meaningless. If I sold you a one billionth share of my shoe for two bucks then my shoe would be a unicorn too. The valuation and the resulting unicorn status are decided and conveyed by the same people hoping to profit from selling the business for more later on. Please also note that the people doing this selling and telling are VCs, who make their money allocating risk but almost all live near earthquake fault lines. These people are in the manufacturing inevitability business. So the Tl;dr is, nothing. It is not important that some of the people who invested in Formlabs would now like us to believe it is now worth a billion dollars as opposed to $10. What is important, however?
What are the implications for our industry?
$100 million is the new $3 million. VC’s are now willing to sink over a $100 million in a third 3D printing company after Desktop metal and Carbon. This tells us a number of things. VCs really do believe in 3D printing which is nice. It also tells us that VCs believe that there will be one or two winners in the Additive Manufacturing market. Meanwhile, we see a chaotic open-source FDM 3D printer ecosystem with over 500 entrants. This implies that investors are expecting a mass die-off there of companies. Everyone I speak to expects the great majority of 3D printer companies to die off soon. It’s a near universally held truth, and you know when predicting the future these are almost never correct. What if we see more granular approaches to market and more companies filling more niches? What if specialization and systems integration into custom manufacturing solutions provides an alternative?
Have’s and Have Nots. There are a few companies with oodles of cash, namely Carbon, Desktop metal and Formlabs. This once again illustrates the power the US has in capital allocation. Shapeways moved to the states and the other high funding companies all hail from there. In a globalized world, it is still a great advantage to be a US startup. Other companies such as Ultimaker have tens of millions of funding and seem to be running a marathon rather than running for the exits. Does this mean we are about to see a bifurcation in our industry with the European companies opting to stay private and the Americans going public? EOS is a huge firm that has grown incredibly quickly and yet it all in the hands of its founder Dr. Langer. What are the implications of this?
Will we also see a war of attrition on the desktop? In metal 3D printing people at Formnext, last year seemed to be building dreams and wars of attrition, not parts. Huge investments in stands made us believe that this sky castle was a better long-term bet than the next. Will we seem similar wars of attrition on the desktop? Will the happy few simply outspend those others who took little or no investment?
Kickstarter went from being a universe on and of itself to a byword for optimism induced consumer fraud. Formlabs success is a huge validation of the Kickstarter model and Kickstarters ability to build actual businesses. Far from dream coolers or once omnipresent Pebble watches some smart kids built an amazing business out of a Kickstarter. Will this mean that Kickstarter will once again become a mechanism for funding businesses or will it be novelties?
Jeff Immelt is probably as connected as one could get in manufacturing. His Rolodex could get Formlabs a strategic seat at the table right at a time when the boards of polymer companies, industrial firms, and large car companies are considering making end-use parts with 3D printing. Whereas Formlabs did enter into production with dental, casting and other applications, Immelt armed with Formlabs new sintering system could open some very exciting doors for Formlabs at the precise moment that they need it.
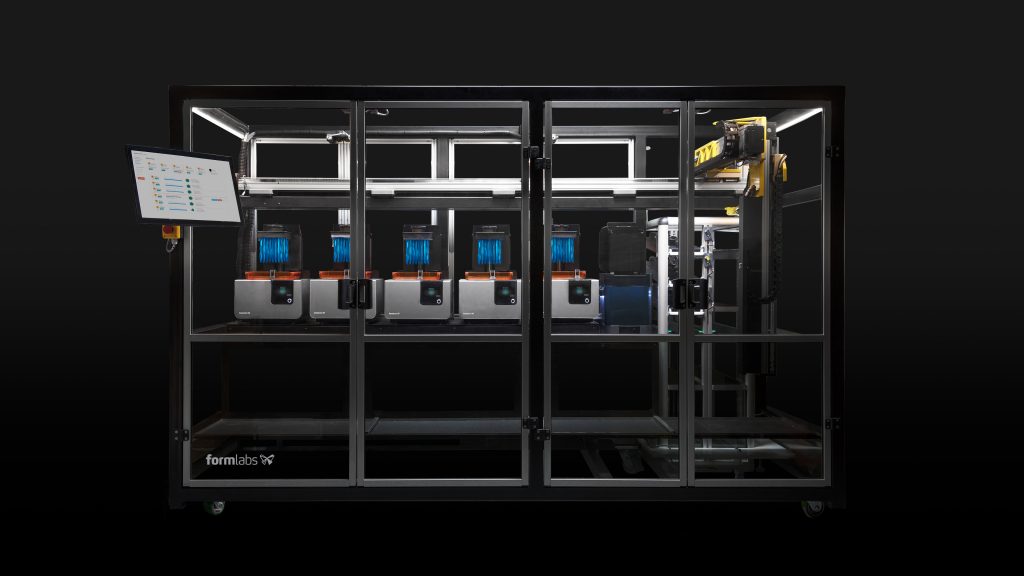
The Formlabs Form Cell Automated manufacturing setup.
Leaping into manufacturing. So far it seemed to me that industrial laser sintering fas in the driving seat in “protected things” such as regulated things and medical while FDM would naturally win in manufacturing because of the price and diversity in materials. A more shop floor focus by Formlabs could see the company lead into competition for the manufacturing crown and this would mean a real challenge for FDM and EOS. Meanwhile, it could also decide to continue to dominate a mid-level manufacturing no man’s land where it would be the system in the room at the lab or at the design department. I think that the latter would be a much better bet in growth and margins long term. The wrong choice here could sink them.
Innovator’s Dilemma. If they go the manufacturing route it would mean a big challenge for EOS in the long run as well as a continued challenge for 3D Systems. How will they respond with pressure from below? The latter firm made a patent litigation settlement with Formlabs in 2014 which meant that Formlabs pays them 8% of sales in order to be able to use SLA. This was a win for 3D at the time but I think that the stability and lack of worry it brought the company meanwhile was important. Also, it must have terrified the 3D systems guys each installment to learn what they were getting paid.
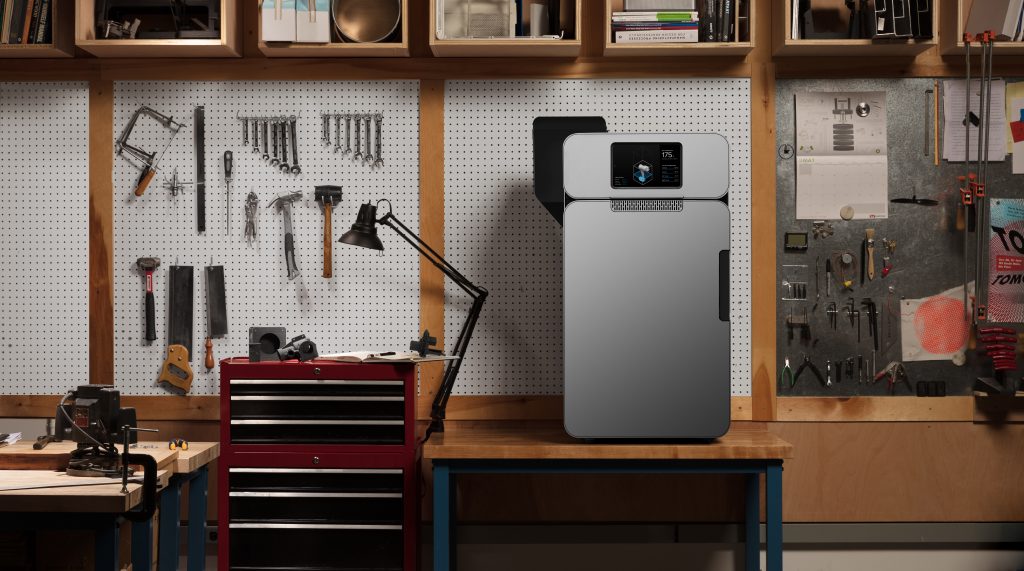
The Fuse Powder Bed Fusion System
$100m. Tucked away in the press release Formlabs mentioned that its run rate was a $100 million a year, which by the by was 70% lower than my estimates. There are dozens of successful desktop startups that have a few million in revenues. Only a few have 30 million or more. To as an organization make it through several transitions, lose people, find people, find structures and replace them successfully is a challenge. It is a great achievement that a 7-year-old startup in hardware is doing at least sixth of 3D Systems’ revenue. Having the escape velocity to do that makes them well poised for further growth. Also, a billion dollar valuation with over 100m in revenue is less of a stretch of some more fanciful startups recently.
Scale and scope. Additionally, the company has expanded globally with multiple offices and now will extend its technologies to powder bed fusion as well. This will be an additional hurdle to follow. What will be the model of the successful 3D printing OEMs of the future? Service businesses that sell machines and have several technologies as Stratasys is; a jack of all trades as 3D Systems is; highly specialized but complete offering firms such as Ultimaker; a command and control company like EOS; or will it be a scrappy Prusa i3 clone maker that will only do that? We still can not know, but I think that Formlabs unique path has given us many implications for our industry. How exactly did they get this far?
Why was Formlabs able to out-execute and get this far?
Closed works too. The riotous open FDM ecosystem is making leaps, bounds, sidesteps, tumbles generally forward. They are open, mostly pretend open source companies that through scrappy competition have made an open landscape that is increasingly being used for manufacturing. Recently I said that Stratasys should go open as well to become more competitive against this ecosystem. But, here is Formlabs and they’re closed. Their software, their printer, their materials. They decide, Apple-like, what is right for you.
Ease of Use. The closed Formlabs approach actually as a user gives you the best UX in 3D printing. The Formlabs printers are still the easiest to use from buttons to software in the industry. UX is not only for conferences and press releases, it matters. I’m not a fan of SLA but damn the thing just works.
Outexecute. Formlabs took what looked to be a rather simple challenge and outexecuted in all regards. Obsessive about quality and experience they went it alone in popularizing SLA and Pro. By holistically looking at the entire experience they performed better for one particular group of people: designers and engineers that needed smooth, highly detailed parts in semi-office settings. Too often companies want to be all things to all men and end up being nothing to no one.
Timing. That Formlabs was the first to tout Pro is largely understood and their focus on not the shop floor and not the desktop but the in-between was in retrospect brilliant. They anticipated what everyone else found out later, that the majority of desktop 3D printer buyers were companies. Also, they waited to bring out the Form Cell to do manufacturing, they didn’t try to sell manufacturing solutions off the bat. Being too early can suck too. The company had the only completely finished the prettiest product when it mattered, not to everyone but to enough.
Contrarian. Being contrarian is good on paper, rarely fun in real life. In 2009 I was at a meeting with around 10 or so industry experts discussing the challenges in 3D printing and every single one of us concluded that stereolithography was dead. We were unanimous in declaring that in the coming revolution of real-world end-use parts, SLA was toast. Ooops.
Lucky. At a time when there were dozens of FDM startups pouring into 3D printing most didn’t even give SLA a second glance. Exotic expensive photopolymers, lasers, it seemed so finicky. To the open source rough and tumble grease and solder folks the whole SLA thing just seemed a tad effete compared to what they were doing. And its not open source? Lets completely ignore them. This ended up being a godsend to the company and to this day they’ve had spectacularly little competition in desktop SLA.
Right place. Being close to MIT matters, its easier for some of the best people to join you and for you to get advice from some amazing people as well. Location still matters a lot in today’s world.
Max is very smart. 3D Printing has a lot of bright people in it, among those bright people Max is an exceptionally bright one. He’s also relentless in pursuing a vision. For most people and most firms such an approach leads to failure but if someone like Max surrounds himself with the brightest of people then sometimes, just sometimes the future happens.
Essentially there was a firm that sought out excellence at the right time in a contrarian way. By developing a system with good usability they, VC fueled were able to find and keep customers while being left to their own devices. Can’t wait to see what they’ll do next.
AMFG Unveils Holistic Build Analysis Tool
London-based AMFG has just unveiled their new holistic build analysis tool software for 3D printed parts. The tool serves as the latest addition to their overall AI powered AMFG program, adding in the ability to digitally analyse cost-effectiveness in an instant. The holistic build analysis tool acts as a quicker, more efficient alternative to nesting […]
The post AMFG Unveils Holistic Build Analysis Tool appeared first on 3D Printing.
Shining 3D partners with AGE Solutions to create new 3D digital dental software
Altair expands access to digital manufacturing through global startup program
Dremel 90 degree drill press adapter #3DThursday #3DPrinting
endel99 shares:
This adapter is used for mounting a Dremel mini-grinder horizontally into a vertical drill press that uses 43mm collar. When used with a cutoff wheel, it allows precise movement in the plane of the disk, effectively turning the drill press into a cutoff saw.
download the fils on: https://www.thingiverse.com/thing:2990118
Every Thursday is #3dthursday here at Adafruit! The DIY 3D printing community has passion and dedication for making solid objects from digital models. Recently, we have noticed electronics projects integrated with 3D printed enclosures, brackets, and sculptures, so each Thursday we celebrate and highlight these bold pioneers!
Have you considered building a 3D project around an Arduino or other microcontroller? How about printing a bracket to mount your Raspberry Pi to the back of your HD monitor? And don’t forget the countless LED projects that are possible when you are modeling your projects in 3D!
The Adafruit Learning System has dozens of great tools to get you well on your way to creating incredible works of engineering, interactive art, and design with your 3D printer! If you’ve made a cool project that combines 3D printing and electronics, be sure to let us know, and we’ll feature it here!
Exporting from Fusion 360 Tips by Chris Young
Chris Young has a tip on saving projects out of Autodesk Fusion 360. Although that sounds like an obvious thing to do, it’s actually a bit of workaround when projects don’t quite export easily.
when it comes time to share my open source designs with the world, it’s very difficult to save these Fusion 360 designs to my hard drive to later be uploaded to GitHub or Thingiverse. Fusion 360 stores its files in the cloud under your account most of the time. It does have the ability to save a design to your hard drive but not if that design contains linked components. If you try breaking the links it can create reference errors especially if the linked components themselves contain linked subcomponents.
I’ve myself have ran into issues when trying to save out my projects locally for sharing on github, learn, thingiverse, etc. I thought it was easy enough share public links via the project window but seeing the process of downloading broken out in Chris’ blog made me realize how it is a bit of a process.
Common Autodesk, ya’ll can do better
Read full post on Chris Young’s Blog