The US military has not shied away from implementing modern manufacturing methods such as 3D printing, but has actually embraced the technology. In fact, the US Air Force has used 3D printing for multiple projects, including components for aircraft and fighter jets, such as the F-35. This is what’s known as a next-generation fighter, and the 388th Maintenance Group of the Hill Air Force Base in Utah recently began 3D printing specific replacement parts for the F-35. Base officials are hoping that the technology will help to lower costs and increase availability.
Many branches of the military have turned to 3D printing to make replacement parts for those very same reasons.
“We’re always driving for speed, safety and quality. But cost-effectiveness is also a priority,” said 388th MG commander Col. Michael Miles. “This new tech has great cost-avoidance potential and provides rapid repair capabilities.”
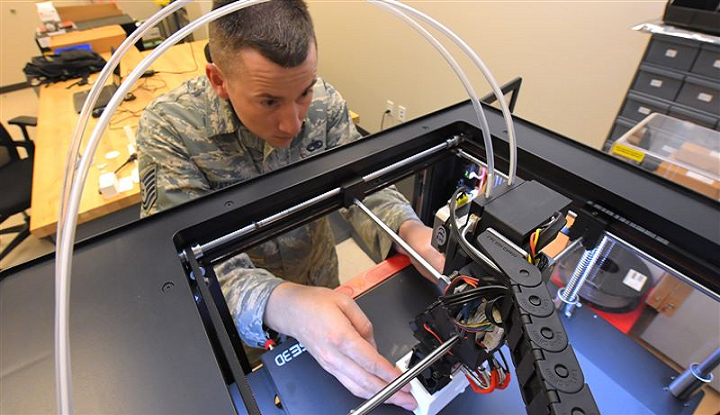
Tech Sgt. Scott Mathews, assistant manager of the 388th Maintenance Group’s Air Force Repair and Enhancement program, makes adjustments to a 3-D printer the unit is experimenting with to create pieces and parts faster and more cost-effectively. [Image: Todd Cromar]
According to Tech. Sgt. Scott Mathews, assistant manager of the 388th MG’s Air Force Repair and Enhancement Program, early returns are showing that when his shop gets in damaged parts that are able to be reproduced through 3D printing, they are then able to be introduced into the supply chain with greater speed and at lower cost.
Tech. Sgt. Mathews explained, “It’s much more cost effective for the Air Force than buying new parts.”
One of the first items the team at the 388th MG created was a small-scale replica of the F-35 fighter jet. But now they’ve moved onto 3D printing simple plastic replacement parts, such as cable splitters, fasteners, grommets, housing boxes, and wiring harnesses. Tech. Sgt. Mathews said that many areas of the shop have figured out how to make the 3D printing easier to work with by “getting away from a lot of fancy metals and getting into composites and plastics.”
However, the technology is still young in the shop at Hill AFB, and the unit’s airmen are using trial and error to refine things, including using computer software to make their own in-house designs. There are even signs that they could manufacture more complex parts out of stronger materials in-house one day.
“There’s one printer (where) you can print with aluminum. That opens up a whole new world of opportunities,” said Tech Sgt. Matthews. “When you look at all of the different parts we could manufacture … it just boggles the mind, the things we could (make) on base. It’s just insane.”
The first two F-35 fighter jets arrived at Hill AFB in September of 2015. But, by the end of 2019, there will be three whole fighter squadrons, made up of a total of 78 jets, on the base. The active duty 388th Fighter Wing and the reserve 419th both fly and maintain the jets, while the Ogden Air Logistics Complex on base performs maintenance on all of the F-35s. Hopefully, 3D printing can soon be used to help with all of this maintenance.
Tech Sgt. Matthews said, “There’s a sense of pride knowing you played at least a minuscule role of getting them airborne.”
Discuss this and other 3D printing topics at 3DPrintBoard.com or share your thoughts in the Facebook comments below.
[Source: Standard Examiner]