Printrbot closes @printrbot #makerbusiness
Researchers Test 3D Printed Lattice Structures as Implants to Facilitate Bone Growth
The advances being made in bioprinting and tissue engineering mean that even the most severe injuries have a chance at being repaired. Loss of bone due to injury or disease used to be a permanent condition, but that’s not the case anymore – medical technologies including 3D printing are now capable of replacing or even restoring lost bone tissue. New tissue can actually be grown from scaffolds that are implanted inside the body, as long as those scaffolds are made from osteoconductive material, which is a material that is capable of stimulating the growth of bone tissue.
A group of researchers recently conducted a study in which they used selective laser melting (SLM) 3D printing to generate titanium lattice structures as scaffolds for bone regeneration. The research is published in a paper entitled “Osteoconductive Lattice Microarchitecture for Optimized Bone Regeneration,” which you can access here.
“Bone replacement materials need to be accepted by the body and should clinically be infiltrated with bone tissue within a short time, so ideally they are osteoconductive,” the researchers explain. “Bone tissue engineering of osteoconductive biomaterials like other tissue engineering approaches normally relies on the combination of cells, bioactive factors, and biomaterial scaffold to facilitate and accelerate the regeneration of bone tissue.”
The shape of the bone scaffold can be designed to perfectly match the size and shape of the bone defect. In the study, the researchers 3D printed titanium structures to replace bone in rabbits, using SOLIDWORKS software to design the implants.
“The outer macrogeometry of the implants is designed as stepped cylinders of 7.5 mm, respectively, 6 mm diameter and a height of 4.2 mm,” the researchers state. “The inner microarchitecture is constructed by cutting out symmetrically arranged square channels in all three orthogonal directions, see Figure 1. Based on most promising scaffold parameters from the literature, the width of the channels w (distance between the rods) and the wall thickness s (rod caliber) of the remaining trusses have been systematically varied in a way that complete layers of cubic unit cells are formed along the cylindrical main axis (see Fig. 1 for an overview of the designs and Table 1 for the structural values). Finally, a 0.2 mm fine ring completes the outermost margin of the framework to close the last layer and prevent sharp edges during surgery.”
The implants were 3D printed using a Realizer 250HT from SLM Solutions. 18 adult rabbits were used in the study; they were housed in groups of two to four and each had four scaffolds applied to them at random. After four weeks, the implants were removed and studied to see how well they had stimulated bone growth, with distinctions being made between implants with different rod distance and rod caliber in a lattice titanium microarchitecture. The results showed that the best results were achieved at a rod distance of 0.8 mm and a rod caliber of 0.3 to 0.4 mm.
“Since AM and 3DP in many cases yield in a lattice microarchitecture, these results suggest to overcome the former dogma on channels of 0.3 to 0.5 mm and substitute them by channels of 0.8 mm for bone substitutes, where bone ingrowth has to occur fast and efficiently,” the researchers conclude.
Authors of the paper include Michael De Wild, Chafik Ghayor, Simon Zimmerman, Jasmine Rüegg, Flora Nicholls, Felix Schuler, Tse-Hsiang Chen, and Franz Z. Weber.
Discuss this and other 3D printing topics at 3DPrintBoard.com or share your thoughts below.
Oerlikon and RUAG Ink Space Deal while Additive Industries and LPW do the same
Mayday, Farnborough, we’re running out of champagne.
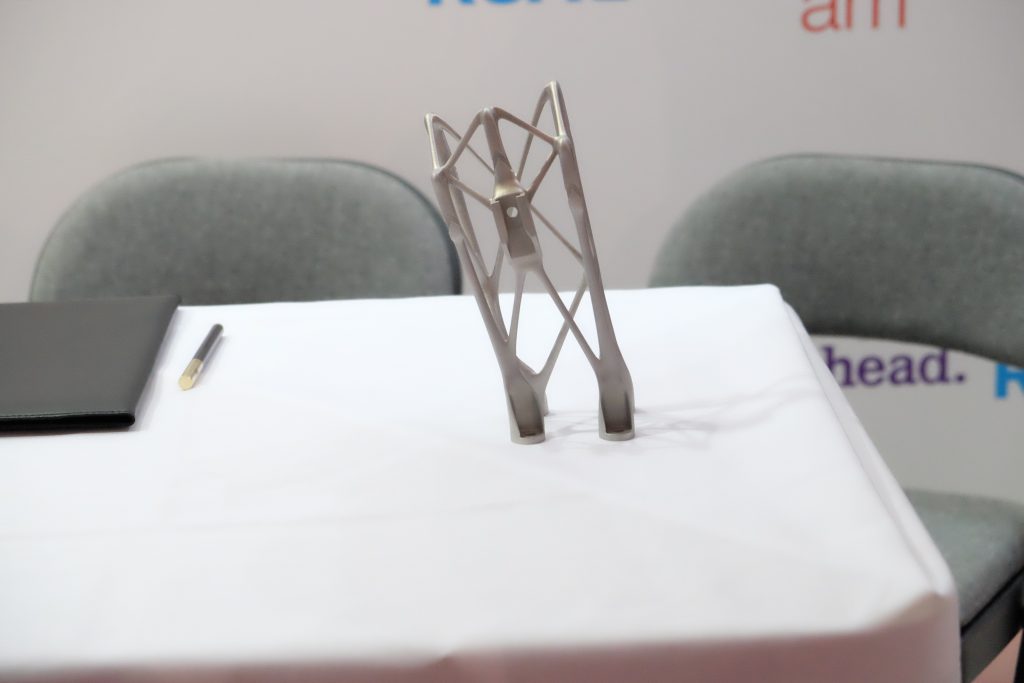
The 3D printed fairing bracket made by RUAG and Oerlikon.
If you’re slowly but surely getting the impression that a lot of deals are being signed at the Farnborough Airshow, you would be right. Amidst the clash of Airbus and Boeing to land big orders and make an impression it is now de rigeur to sign a deal of some kind at Farnborough.
The show is one of the yearly game of one-upmanship of Boeing and Airbus. It also sees a lot of demonstrations and novelties in aviation, including this incredible display with a C130. There’s always far out stuff such as talk of balloons with 46 meter long cabins taking people on tours around the world and tiny robots that would crawl across engines to repair them (which I believe is much more likely to happen). There are always surprisingly large orders from surprisingly unknown airlines. This year Vietjet inked a deal for $12 billion to purchase a 100 737 Max Jets. That’s one deal, that is approximately the size of our total industry revenue. Everything in 3D Printing, all of the materials used, all of the machines sold, all of the software, everything. Smaller than one deal inked at Farnborough by a Vietnamese Airline. Puts things into perspective, doesn’t it?
A big portion of our future lies at Farnborough though. Don’t expect us to make the BBC headlines any time soon there but an important shift is happening. Quietly, we’re moving into production. Serial production and manufacturing in metals has been with us for a number of years with millions of parts being produced for dental and tens of thousands for prosthetics. The renderings of 3D printed metal aviation components have been flying around more than the components, but a fundamental shift is occurring towards actual manufacturing in aircraft. So far test brackets, unique parts, retrofits and the like saw metal 3D printed parts. EBM and DMLS have been used extensively in rockets and on satellites. Now companies are taking the necessary steps into manufacturing tens of thousands of aviation components. For aviation, this means a lot of qualification and certification which is a significant investment for people wanting to serve the aviation and space industries. We saw two important 3D printing tie-ups recently, along with all the matchmaking GE was doing as well. The first tie-up is “the Swiss space program” while the other is “anglo dutch powder.”
Oerlikon
Oerlikon is a Swiss company that makes fibres, drive systems and surface solutions. It is a multibillion-dollar company and makes over $20 million a year in 3D printing chiefly through metal fabrication. The company will be investing over $100 million in 3D printing in the coming years.
RUAG Space
RUAG is also swiss; partially government owned the company was recently split into a Swiss-based government controlled MRO (Maintenance Repair and Operations, a sum total of aviation repair services)unit and a company that focuses its attention outside of Switzerland. RUAG space is one of the largest Europe based space firms. RUAG Space makes satellite components, launchers and electronics components for onboard spacecraft. Far away from the profligate spending on American satellites by the NRO (National Reconnaissance Office, $10 billion budget us agency in charge of the US’s spy satellites) and a bit separate from its more European counterparts RUAG simply needed to get good.

Oerlikon and RUAG partner to make products like the serially produced space bracket.
RUAG Space and Oerlikon signed a Memorandum of Understanding to facilitate the series production of space components. The companies are working together on a bracket for a payload fairing. Payload fairing might sound cute but below you can see a picture of a payload fairing, pay close attention to the desk with the men in the red shirts. Its essentially a nose cone part for a rocket, and they’re working on a bracket for this.
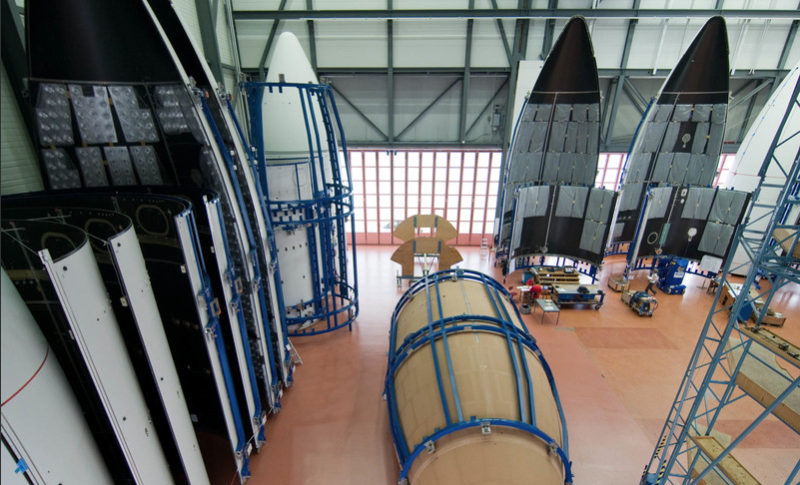
A room with fairings in EMMEN at RUAG
The companies are seeing that the bracket “25 percent and decrease weight by more than 50 percent while doubling the stiffness of the bracket.” The fact that we can create higher performance 3D printed parts than conventional ones is of course interesting. In rocketry and satellites each kilo saved may save them $20,000 or more with additional gains in performance. Dr. Roland Fischer, CEO of Oerlikon Group stated,
“Through our ongoing collaboration with RUAG Space, we have identified opportunities to fine-tune the qualification and certification processes, which are crucial in ensuring consistent quality in production. We are confident, that our materials and additive manufacturing expertise will further grow this important partnership.”The consistent quality will certainly be important for space. Certification may seem boring but in this case, means that many millions have gone into reducing the errors in 3D printing.
In another article, the CEO stated that, “
“It is not good enough that everyone does something a little different,” Fischer said. “We are talking about aerospace, where failure is not an option.” 3D printing today is like driving a car in 1905, he said. There were different automakers, but no certification processes, no standards, and not even established road signs.”
This candor and humility will surely complement their lofty ambitions well.
Additive Industries and LPW
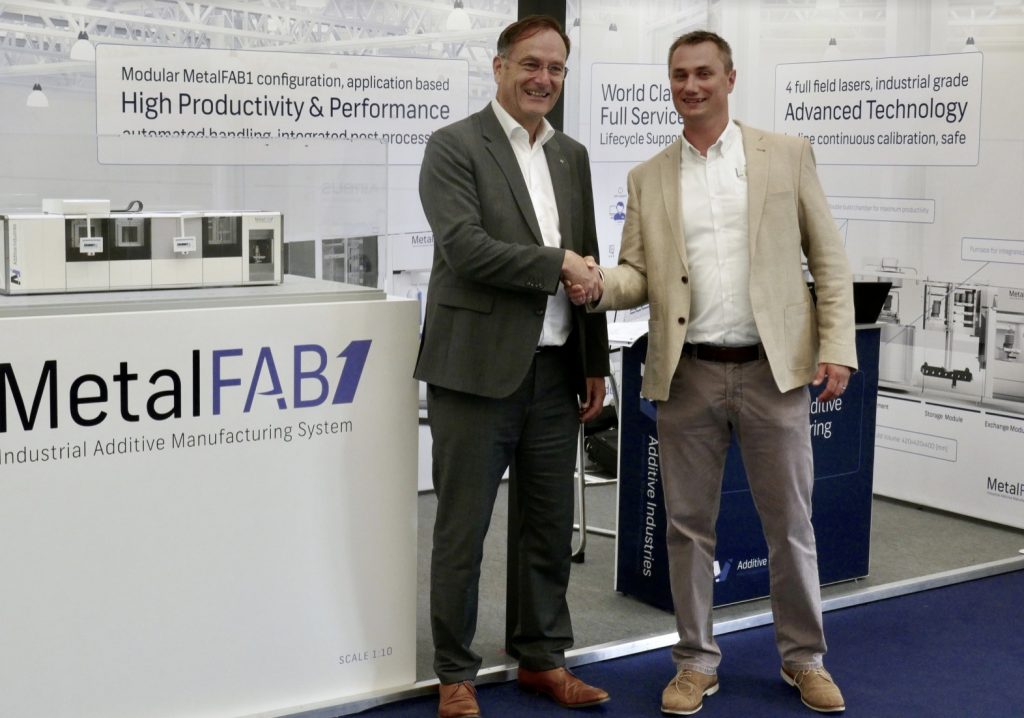
At Farnborough with Phil Carroll and Jan-Cees Santema
Another pair with lofty ambitions is Dutch-based Additive Industries and UK company LPW Technology. Additive Industries has from the ground up designed a metal 3D printer for manufacturing. The company minimized handling through automation and designed a system meant for high reproducibility and series production that could simultaneously reduce the cost of parts. Essentially their modular system means that rather than an operator turning on and off the machine and carrying build platforms to various steps, the machine handles this; significantly reducing handling and cost.
LPW Technology is a powder company that develops custom powders independently of machine manufacturers. It also is big on managing and tracking the powder throughout its use. This is precisely the kind of thing that has to be done if one were to make aerospace components.
Their agreement lets LPW offer its powder management products to MetalFAB1 customers through Additive Industries Additive World Platform.
“This allows Additive Industries customers to automatically load powder into the MetalFAB1 systems in
inert conditions and record the main characteristics of the metal powders during their lifecycle from
metal powder manufacturing to part production. Especially in series production of qualified parts,
this closed-loop system is key in reducing the risk of contamination and potential variations in the
powder performance as a result of exposure to oxygen and humidity.”
More control and fewer variables mean that mistakes can be found and tracked while quality is more likely to occur.
Daan Kersten CEO of Additive Industries said,
“We have been working with LPW for years and share the vision on full automation and integration. Integrating the
LPW Powder Hopper solution and PowderSolve software in our MetalFAB1 systems and software allow our customers to accelerate the manufacturing of industrial quality parts and store all data in one place. The integrated supply of powder combined with full traceability closes the loop to produce certified parts in regulated environments like aerospace and healthcare. Moreover, the automated and closed powder loading system cuts manual labour significantly and reduces operator exposure to powder providing a safe and healthy work environment. The long-term relationship between LPW Technology and Additive Industries has resulted into this innovative powder handling
System”.
Additive Industries tends to collaborate also working with 3DSim simulation software and also working with GKN Powder an LPW competitor. If Additive Industries, LPW, RUAG and OERLIKON four just got together with a software company, they would have most of the supply chain for making space parts. In order to impress the huge space industry we’ll have quite a ways to go, but perhaps one or two Airbus or Boeing people wiggled their noses post champagne bubble long enough to squint at the future of their industry.
Researchers Develop 4D Printed Load-Bearing Polymer Structures
Researchers at ETH Zurich have just developed a new memory-material based design that evolves with environmental stimuli. These 4D printer structures contain programmable actuators that deploy autonomously and change shape using temperature alterations as the catalyst. They are also load-bearing before and after actuation, and thus can serve as great construction materials. Professor Kristina Shea and […]
The post Researchers Develop 4D Printed Load-Bearing Polymer Structures appeared first on 3D Printing.
3D printing news Sliced Siemens, ExOne, Stratasys, Massivit, CELLINK, Formlabs, Star Rapid
Turkish Man Helps Injured Eagle Return to the Skies with 3D Printed Prosthetic Foot
Some of the most heartwarming stories we get to write are the ones where an animal gets a new lease on life thanks to a 3D printed prosthetic. The veterinary field has definitely been increasing its use of the technology over the last few years, and all sorts of animals, from dogs, cats, and goats to turtles, lizards and birds, have been the lucky recipients of various 3D printed prosthetic limbs, beaks, and other medical devices.
However, based on the evidence at hand (all of the stories we publish), it seems to me that our feathered friends have been receiving the most 3D printed assistance. In just the last six months, Gumpy the seagull, a baby chick and an adult chicken, a beautiful peacock, and a lucky duck named Peg each received new 3D printed feet or legs. Over the years, multiple other birds, from a macaw, a crane, and a duck to a cockatoo, a toucan and an eagle, have an increased quality of life due to 3D printed bills and beaks, which birds require to drink, eat, preen, build nests, feed their young, and complete other necessary tasks to survive.
While it’s true that most of these 3D printed animal prosthetics come from veterinarians and animal hospitals, sometimes people without a medical degree are the ones who spend their time and energy helping injured animals. Two years ago, 16-year-old Nikita Krishnan learned 3D printing and CAD skills and set up her own nonprofit, all so she could design and fit 3D printed prostheses and splints to injured animals at no cost. 23-year-old Hasan Kızıl, a resident of Derik village in the Mardin province of southeastern Turkey is also one of these amazing animal saviours.
Kızıl is known by the locals around town as “the life repairer,” as he creates his own makeshift prosthetic limbs and walkers for injured animals for free. He said that he’s treated close to 300 disabled animals so far, and his most recent patient was an eagle, a species of bird that has received 3D printed medical assistance in the past. A child brought the eagle to Kızıl after finding it in, as the Daily Sabah Turkey put it, “an exhausted state.”
After an examination, he realized that the eagle was missing the claws on one of its feet, which meant that it would not be able to fly.
Kızıl explained, “Eagles take off with support from their feet and the eagle was not able to fly as it couldn’t take off without a foot.”
Kızıl said that an electric fence was the culprit behind its missing claws. So he set out to help the eagle and decided to use 3D printing to create a prosthetic limb. After plenty of calculations and modelling work, Kızıl was successful in his efforts…for which it seems the great bird was very grateful. Not long after the eagle received its 3D printed prosthetic, it started trying to take off into flight; after several tries, it succeeded and flew off.
While eagles don’t generally stick around to say thank you, Kızıl said he was happy to help it get back to the skies again. But there are others who appreciate his efforts – this March, he was the proud recipient of a Benevolence Award by Turkey’s Presidency of Religious Affairs for his continued efforts and hard work helping to treat and save the lives of disabled animals. President Recep Tayyip Erdoğan presented him with the award.
Do you know of any other 3D printed animal prosthetic stories? Let us know! Discuss this and other 3D printing topics at 3DPrintBoard.com or share your thoughts in the comments below.
EnvisionTEC Reduces Cost of Aria 3D Printer, Available Directly from Website Only
This year, EnvisionTEC has already launched several new 3D printers, and it has notably increased its offerings for dental and orthodontic 3D printing recently. As a pioneer in SLA/DLP 3D printers, EnvisionTEC is a trusted supplier to a wide range of customers, and although its printers aren’t the cheapest, they also don’t skimp on quality, which is what has kept the company so successful even as SLA and DLP 3D printers drop in price elsewhere.
In November of last year, EnvisionTEC announced that it was releasing a new affordable desktop 3D printer called the Aria. At just under $7,000, the 3D printer still isn’t cheap, but it’s certainly more affordable and accessible for small businesses. Now EnvisionTEC has lowered the price of the Aria to $5,999 for North American customers.
“EnvisionTEC has been known for its unwavering commitment to delivering professional-grade 3D printers for more than 15 years, which is why we consistently remain a 3D printing leader,” said EnvisionTEC CEO Al Siblani. “The Aria remains faithful to our mission of delivering a premium product, but at a more accessible price that gives users a taste of EnvisionTEC’s outstanding quality and reliability.”
The Aria boasts an industrial-grade UV LED light engine, a dual-axis Z slide and a material tray made from optical glass rather than plastic. Z layer resolution can be set at 25, 35 or 50 microns, depending on the material used. The 3D printer comes with a choice of four materials from among EnvisionTEC’s most popular resins:
- EC500, a high-resolution lost wax casting material ideal for heavier jewelry pieces
- PIC100, a castable resin designed for intricate, delicate pieces
- QView, one of EnvisionTEC’s fastest materials, ideal for quick design verification
- RC90, a high heat-resistant, ceramic-containing material well-suited for tough, stiff parts
These aren’t the only materials the Aria can use, however; the 3D printer features an open materials system, though all materials must be certified for use by EnvisionTEC.
Currently, the Aria is only available online directly from the EnvisionTEC website. This is a change for the company, which typically employs a large network of resellers to sell its products. It’s interesting to think about what may have prompted the decision to sell this particular 3D printer directly from the website, and whether this signals a larger move toward direct selling for the company. Also notably, the Aria is only available currently to ship to North America and Europe. As this 3D printer is designed to be a more accessible printer that some of EnvisionTEC’s other machines, it’s odd that its availability is currently so limited. With such a wide range of resellers across the world, why not make the Aria available through them as well?
Resellers depend on the companies whose products they sell, and one wonders if any of EnvisionTEC’s resellers are at all uneasy with the decision to go with direct sales for this 3D printer, whose very affordability suggests that it will be a strong seller. Only time will tell if EnvisionTEC ends up selling any of its other 3D printers direct from its website only, but the choice to make the availability of the Aria so limited is an interesting one. Essentially we’re seeing a company come to grips with competitive pressure from lower cost systems. Turning to open materials would seem to reduce part costs. It would also let polymer companies and other partners introduce newer materials for innovative applications. Envisiontec may forgo some materials revenue here but puts itself on a solid footing for tackling the competition. Resellers, on the other hand, may not be terribly enthusiastic about this.
Discuss this and other 3D printing topics at 3DPrintBoard.com or share your thoughts below.
[Images: EnvisionTEC]