Companies, organizations and individuals continue to attempt to lend support to the COVID-19 pandemic supply effort. We will be providing regular updates about these initiatives where necessary in an attempt to ensure that the 3D printing community is aware of what is being done, what can be done and what shouldn’t be done to provide coronavirus aid.
3D printing is a great tool for short, fast production runs, but, as Dr. Beth Ripley from the Veterans Affairs department pointed out, it is a stop gap measure while mass manufacturers retool for larger, less expensive batches. Steve Cox, a 3D technologies consultant, posted an open design for an injection mold meant for producing face shield headbands. The tool was designed in Autodesk Fusion 360, while Inventor was used to analyze the flow of polypropylene flow and filling within the mold. Those interested can contact him for the file.
After the Chief of Milwaukee Police Department (MPD) put out a request for personal protection equipment donations, a local 3D printing company called GSC stepped in to produce new filters for the police force. MPD required 600 new filters, including the actual filter material. While Milwaukee Tool donated 600 HEPA filters from their vacuum line, Bradley Corp donated 600 O-rings for sealing them (as well as 600 extra from Viking Masek).

A face mask with 3D-printed filter attachment supplied to the Milwaukee Police Department. Image courtesy of GSC.
With the safety supplies in place, GSC prototyped an adapter for the filters to attach to MPD’s existing masks. In just five-and-a-half days, the 3D printing firm was able to get the device in the field, 3D printing the adapters on its HP 5200 3D printer printing at a rate of 125 to 250 parts daily. While the design files are available online, they are specific to MPD’s masks; however, talented designers and engineers should be able to modify them for their own use.
The Portland 3D Printing Lab is now 3D printing face and eye shields for local hospitals in Portland, Oreg. So far, 220 makers with 380 printers has produced 5,000 pieces of PPE for hospitals and partners, establishing what the group refers to as a “pop-up supply chain.”
Through MakerForce.org, local hospitals can request PPE, at which point community members can connect with them and begin making items from a catalog of parts. The group can either perform small 100-unit runs or production jobs of 200 to 5,000 units using its Rapid Assistance Database, a method for maker members to “select verified units of work, 3D print them, and drop off in bins outside three local businesses.” Using this complex method, which you can learn more about here, the group has been able to perform 9,000 hours of work in less than three weeks, delivering 1,000 pieces of individually wrapped face shields in less than a week.

Physicians at Providence Willamette Falls Medical Center’s ER with their new face shields with parts 3D printed by MakerForce.org. Image courtesy of Sean Stone.
A Massachusetts team—made up of AFFOA, MIT, MIT Lincoln Laboratory, University of Massachusetts Lowell and the US Army Combat Capabilities Development Command-Soldier Center— is establishing a method for characterizing and analyzing materials and supplies used during the COVID-19 pandemic. The goals of the coalition include the following:
- coordinating testing efforts for medical supplies
- evaluating internationally sourced products based on their regulatory designations
- testing and analyzing research work dedicated to product resterilization and re-use
- Analyzing raw materials and product prototypes for PPE to establish a method for regulatory certification via NIOSH and the FDA
- Analyzing new filter media
The group, led by AFFOA, is testing N95 respirators and masks, surgical masks, face shields, isolation gowns using the tests below. While the tests do not provide certification or pre-certification, the organization can provide connections to resources at NIOSH and the FDA. More about the effort can be found here. These tests are currently being offered for free with the organization prioritizing the tests based on need dictated by the pandemic:
A group of four medical device companies in Ohio, the Theken Group, developed a resuable, autoclavable, titanium 3D-printed N95-style face mask in a span of less than 10 days. Based off of 3D scans of human faces, 20 iterations of the mask design were first 3D printed using an FDM printer before an Arcam electron beam system was used to create the final part. The goal of the device was the ability to replace disposable cloth masks with a reusable counterpart, potentially addressing supply shortages.
The mask is now with the FDA for approval, but it does raise some questions about the viability of such a device. It weighs 60 grams, which is nearly six times the weight of a traditional, 12-gram N95 face mask, which could potentially be burdensome on the wearer. Moreover, the cost of the metal powders used with a metal powder bed fusion machines are notoriously expensive and, one would assume, cost prohibitive for these types of masks.
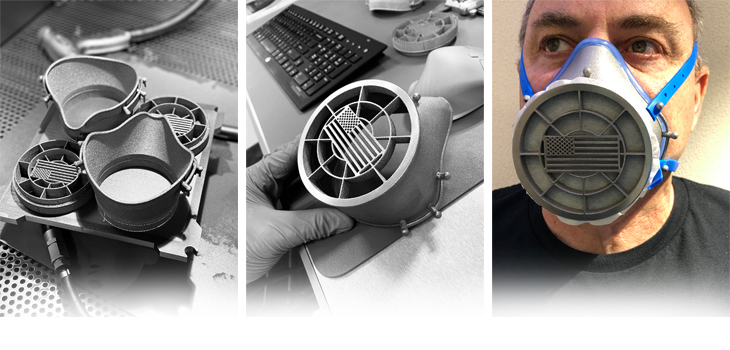
(L to R): 3D-printed N95 Respirator Straight Out of Printer; Finalized N95 Respirator; Cowan Moore, CTO of Theken Group wearing the Titanium 3D-printed N95 Respirator. Image courtesy of Theken Group.
As the pandemic continues to grip the world, we will continue to provide regular updates about what the 3D printing community is doing in response. As always, it is important to keep safety in mind, remain critical about the potential marketing and financial interests behind seemingly good humanitarian efforts from businesses, and to do no harm.
The post 3D Printing and COVID-19, April 19, 2020 Update appeared first on 3DPrint.com | The Voice of 3D Printing / Additive Manufacturing.