The Electronic Presentation Online System, or EPOS, is the European Society of Radiology‘s electronic database for scientific exhibits. A group of researchers published in EPOS about their work using 3D modeling and 3D printing tools to diagnose, classify, and carry out surgical planning for fixing periprosthetic acetabular fractures, which are a difficult, but common, complication of total hip arthroplasty (THA).
“Periprosthetic acetabular fractures are related to traumatic events and pathologic underlining conditions that reduce the structural integrity of supporting bone[1] and often are associated with aseptic loosening, periprosthetic osteolysis and severe bone loss[2],” the researchers wrote.
“Analysis based on standard radiographs alone are not suitable to reliably detect the residual stability of the implant and measure the extent of the fracture and pelvic bone loss [3].”

Fig. 1: (a) Anterior–posterior (AP) pelvis and (b) lateral view of right hip radiographs showed mild signs of periacetabular osteolysis without evidence of implant loosening and acetabular fracture.
They state that when it comes to defining a fracture pattern, CT scanning is “the gold standard,” which is definitely the case when a 3D virtual rendering is needed to help with surgical pre-planning.
3D modeling software based on CT scans allows clinicians to get precise images of “tridimensional reconstructions of the bony surface” by virtually removing metallic implants with segmentation. Other analytic tools include measuring remaining bone stock, evaluating implant stability, and characterizing the fracture, and 3D images can also be used to 3D print anatomical models for surgical planning and simulation purposes.
The researchers said their paper would show that bone quality and fracture morphology assessment can be improved with 3D modeling software, and reveal how useful 3D modeling and 3D printing are for the diagnostic process of periprosthetic acetabular fracture around THA, as well as making life-size models for pre-op implant templating, simulation, and sizing.
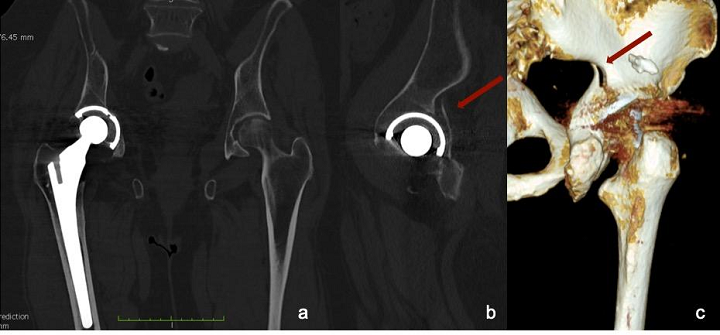
Fig. 2: CT scan of pelvis. (a) Coronal view shows slightly medially protruded acetabular cup; (b) sagittal view of the hip revealed posterior wall fracture of the acetabulum. The tridimensional reconstruction of the fracture is visible (c), but its extension is hidden by image artifacts.
They used the case of a 75-year-old woman who came to an ER after a domestic trauma incident. The patient had a history of severe coxarthrosis in her right hip, which had been treated a decade before using cementless THA. Doctors took AP radiographs of her pelvis, and a cross-leg view of her hip, and saw no signs of fracture or loosening around the acetabulum or the stem. However, a “CT scan of the pelvis with MAR protocol” showed that the posterior wall of the acetabulum did have a fracture, though the acetabular cup wasn’t displaced.
Materialise Mimics software was used to create a 3D digital model of the pelvis based on CT scan data. The bone was differentiated from surrounding soft tissue and the patient’s prosthetic implants through segmentation.
![]()
Fig. 3: Tridimensional images elaborated with 3D modeling software. (a,b) Entire pelvis with acetabular cup retained. Femurs and femoral stem were removed during segmentation. (c,d) Bone quality map shows regions with normal bone quality (green) and regions with low bone quality and thickness (red). (e,f) Measurements of the bone defect area and fracture extension.
“The first phase is thresholding, which includes all voxels whose density is within a specified range of Hounsfield Unit (HU) values. We used a mask with a HU range from 130 to 1750 in order to exclude metallic and ceramic implants and include both cancellous and cortical bone,” the researchers explained.
“The final segmentation, with the removal of soft tissues and artifacts, was manually performed using additional tools of the software (Fig. 3 a,b). Eventually, both femurs and metal implants were digitally removed from the corresponding pelvis and a 3D image of the isolated region of interest (ROI) was created.”
A bone quality map with a color gradient was used for the acetabulum, according to cortical and overall bone thickness of the various regions. Measures of the fracture’s area, shape, and spatial location were analyzed later, along with “the acetabular bone loss and the center of rotation, compared to the contralateral acetabulum.”
Finally, a life-size model of the patient’s entire pelvis was 3D printed on a Form 3L system.

Fig. 4: (a) 3D printed life-size plastic model of the entire pelvis. (b,c) Particular of the medial wall and posterior column fracture.
After analyzing the 3D images and the 3D printed model, they re-classified the posterior wall fracture as an incomplete posterior column and medial wall acetabular fracture. Additionally, the fracture was found to be “spontaneous,” with less than 50% loss of bone stock. Finally, the bone quality map determined global bone loss, showing poor quality in both the posterior and medial walls. The 3D printed model was also used to perform pre-op templating.
“The treatment strategy was chosen according to the algorithm proposed by Simon et al. [14, 15, 16], which suggest the acetabular revision surgery bridging or distracting the fracture, without fracture fixation,” the researchers explained.
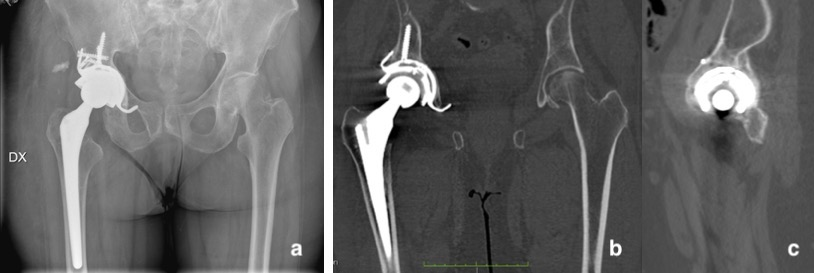
Fig. 5: (a) Postoperative AP radiograph of the pelvis and (b,c) CT scan of the pelvis at 3 months post-op shows good implant positioning and complete fracture healing.
AP radiographs taken of the pelvis and right hip post-op showed that the implant was “well-positioned and fixed.” Three months later, a CT scan was taken of the patient’s pelvis, which showed “bone integration of the trabecular cup” and complete fracture healing “with callus formation.” A 3D digital model built using DICOM images confirmed this.
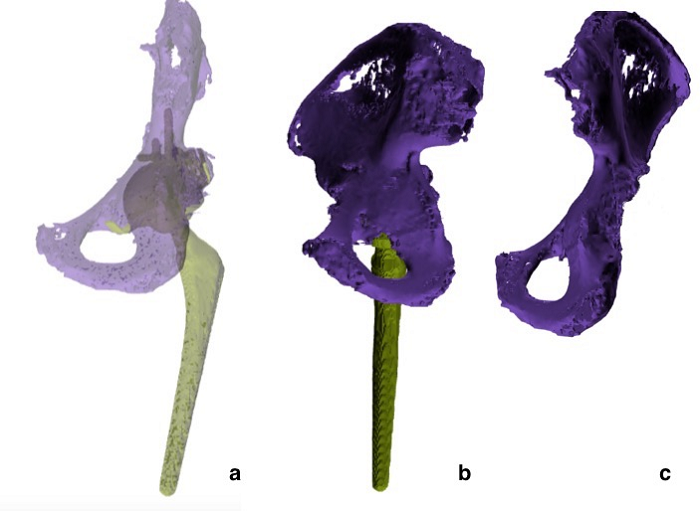
Fig. 6: 3D modeling digital reconstruction. The posterior column and medial wall of the acetabulum have been restored.
“The use of 3D modeling software showed that periprosthetic acetabular fractures can be better addressed, compared to plain radiograph and CT scans,” the researchers concluded.
“3D modeling software provide additional measurement tools which allow the volumetric analysis of bone defects and bone quality assessment.”
Discuss this and other 3D printing topics at 3DPrintBoard.com or share your thoughts below.
The post 3D Modeling & 3D Printing Can Improve THA Diagnosis, Classification, & Surgical Planning appeared first on 3DPrint.com | The Voice of 3D Printing / Additive Manufacturing.