3DTrust is a five-year-old startup that began in Munich. In the beginning, the team was one of a crop of startups that wanted to secure the digital supply chain. Through encryption and software, companies could assure themselves that they were printing the right parts, according to the firm. Through product development and contact with the market, the startup has since evolved.
Now, 3DTrust has ten staff, offices in Toulouse and Munich, and a new focus on repeatability. The company saw that the real challenges in 3D printing were in “printing any part anywhere and making sure that quality is right every time” according to cofounder Antoine Jeol. Jeol has a venture capital (VC) background at 3M and learned an immense amount from 3DTrust being a part of Airbus’s startup accelerator. This knowledge led 3DTrust to pivot away from security and toward a more manufacturing-focused offering.
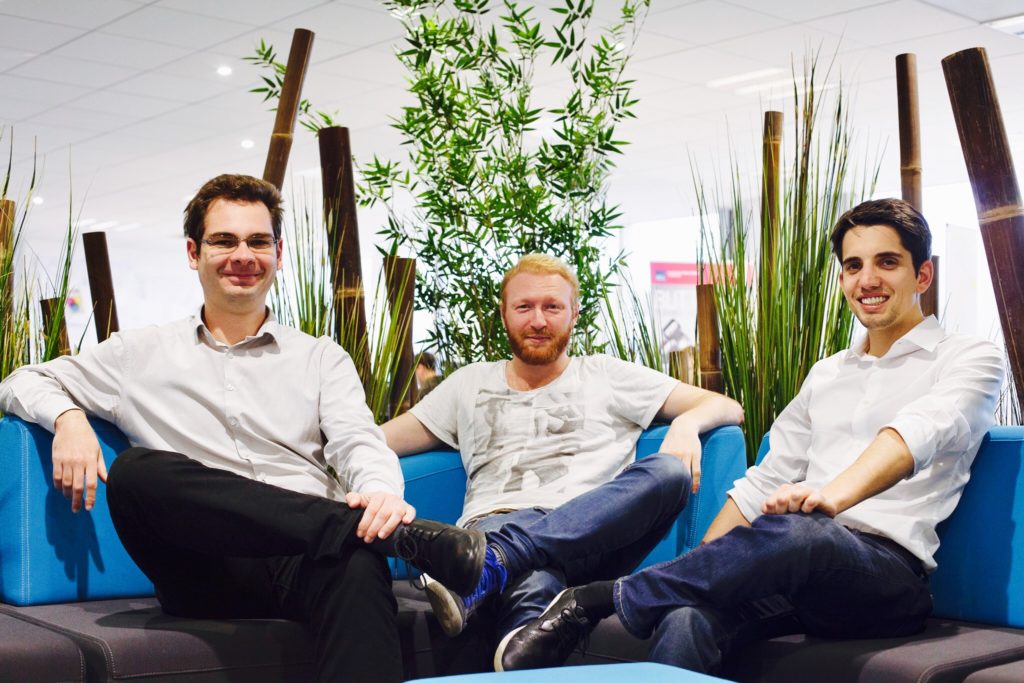
The 3DTrust team cofounders: (L-R) Andrei Mituca, Alexandre Guérin and Antoine Jeol.
When the team partially located to Toulouse for the accelerator program, they were confronted with the challenges that Airbus and its suppliers have. Of course, security is important in commercial aviation, but, other factors, such as traceability, are also of extreme concern. Aviation firms always need to know where parts come from, when they are made, by whom, in what orientation, with which batch of material, on which machine, etc. The team also saw just how many production steps 3D printing for manufacturing required.
Another 3DTrust cofounder I spoke to is Alexandre Guérin, who came from Siemens where he worked at that company’s VC arm. Guérin said that, at many manufacturing companies, the 3DTrust team saw challenges in the “scheduling of production, especially since scheduling and tracking was a manual step, often done with post-its or in Excel.”
The team had to first understand what it took to conduct day-to-day manufacturing with 3D printing. By working with manufacturers, they gained a more in-depth understanding that let them develop their software to work on and with the shop floor. They had to get their software to work with the most popular brands of industrial AM equipment to read and collate data from each of them.
“It could be much more efficient if this tracking was done in software and future job planning was done algorithmically…with reduced human error…resulting in more parts being delivered on time,” Guérin said. “[We had to connect] with EOS, Renishaw, SLM Systems, Stratasys, AddUp and 3D Systems machines… to monitor every machine. If a machine stops, the error notification will get tracked in the software, which can analyze historical trends, detect mistakes, monitor gas levels, get real-time temperatures, receive notifications for specific events, get utilization data and performance data as well.”
With 3DTrust, a user can subscribe to a single machine or multiple machines to only receive the data relevant to them.
Making accessible all of that manufacturing data, scheduling, optimizing, and ensuring traceability is really what the company does now. Jeol believes that every AM machine should be connected and that, while there is a lot of data, in order to achieve true Industry 4.0 process control, that data has to be extracted from all of the connected systems and well managed. Once this happens, 3DTrust can perform traceability, productivity optimization, and analyze entire fleets of additive systems producing parts on time, as well as the post-production steps, to decide what should be done.
In response to client needs, they developed two entirely different architectures. In one, all of their software can be deployed locally, through ethernet cables and customer servers. In the other, Hybrid system, all of the file data is stored locally, but information—such as sensor values—is shared in the company’s cloud. The former version would be especially useful for defense and aviation companies, a group that has traditionally been wi-fi adverse. 3DTrust offers these tools in the form of software-as-a-service, with the company charging $650 per month per machine, although university and large installation pricing are also available. The setup consists of one to three days, typically with 3DTrust often conducting an on-site training for staff of two days.
Users can view individual machine data, aggregate data or dive into individual build plates. They can upload STL or CAD files and queue jobs; files can also be downloaded and re-uploaded from Magics and Netfabb so it is possible to continue to use a preferred file-checking solution in tandem with the software. The output is a specific job file for a user’s particular machine. One could store files in the cloud and schedule or assign files or build platforms to machines or series of post-processing steps. Adjustments in print quality, results, machine utilization, status updates, and part traceability all happen in the software. Users can see delivery dates, materials, and add notes to files and jobs. It can be used in a service environment, in manufacturing or as an internal shared service for large firms.
Through drilling down into each process, machine, and job users can get very granular data, but they can also see performance across time series or analyze all of the alerts and events that delayed builds. One can interface with onboard cameras in printers to check errors and look at individual layers as they are being built, as well.
Jeol said that initially, “We focused on a few key customers in medical, automotive and aerospace to make those customers happy. Making [the software] in conjunction with the guys on the shop floor every day helped us bring value to customers.”
Guérin believes that their customers are using data to get parts made right the first time in AM.
Guérin said, “Optimizing planning saves costs, makes the machines and processes more efficient, faster and cheaper, letting customers industrialize their technology for true serial production.”
In addition to its flagship product, the 3DTrust team has just released a powder management solution. I was very excited about this since, for metals, powder management is key to getting good outcomes in prints, especially for manufacturing. Powder management is essential, but very tedious and time-consuming, especially in highly regulated environments. With the company’s new tool, users can track powder, do inventory management, and use a system that makes tracking easier and more robust as a process.
Meant mainly for large manufacturing companies, but also for universities, the software has some convenient tricks such as a QR print-and-read functionality that lets users stick their own labels on everything. I know from acquaintances that the profusion or lack of labels is often an annoyance. Now, handheld or phone-based scanners can read a production line or lab’s own QR barcodes to quickly tell them about a box, jar or pellet. The system lets users see quantities, dates, materials, storage conditions and availability.
Jeol mentioned that It also enables you to run a “genealogy, a family tree, to see, based on a part, where it came from, with which powder, where it was stored, where it was made, and in which boxes.” It can also be used to track samples or batch tests, with users then able to go back to identify parts or powders that failed tests. Users can also rely on scheduling tools to monitor how often a powder is recycled and combine it with job scheduling, so that a planned job is not able to use a powder recycled more than four times, for example. I’m very bullish on 3DTrust’s powder management tool and would recommend looking at it if you work in a production metal printing environment. It seems to be an intuitive, time-saving piece of technology.
The post 3DTrust Releases Intelligent Powder Management Solution for Quality Control appeared first on 3DPrint.com | The Voice of 3D Printing / Additive Manufacturing.