GSD Global Partners with Sandvik to 3D Print Critical Titanium Part for E-Bike
Electric bikes are known to be pricey, but if you have ever investigated much about quality cycling equipment, that’s not a surprise—whether you are in the market for a conventional bicycle requiring only the energy of your pedaling legs to act as power, or a more complex battery-powered assist. And while there may be a small percentage of bicyclists out there who ride because they have no other choice, for many, cycling is a passion which offers a host of benefits, from improving cardiovascular health to decreasing stress—and cutting down on the environmental footprint.
Coupled with 3D printing, the potential advantages multiply for the bicycle industry—marked by numerous and impressive forays into designs that are stainless and sleek, prize-winning, and even, yes, compostable. Along with bikes and bike parts, we have also seen 3D-printed helmets for cyclists. In the latest modern bicycling news, however, Sandvik Additive Manufacturing has been able to 3D print a critical part for the GSD Global e-bike, in the form of a motor node—one of the most challenging parts to create for these upscale machines.
GSD Global, an engineering and design consultancy company, reached out for help in 3D printing the metal node for their artisan e-bikes.
“Handmade bikes are the type of product that goes straight to your heart – they are pieces of art to begin with. So, if we can provide these high-end bicycle makers with a material that can make their bikes last 10-20 years – that’s a game-changer to them,” says Zach Krapfl, heading up GSD Global.
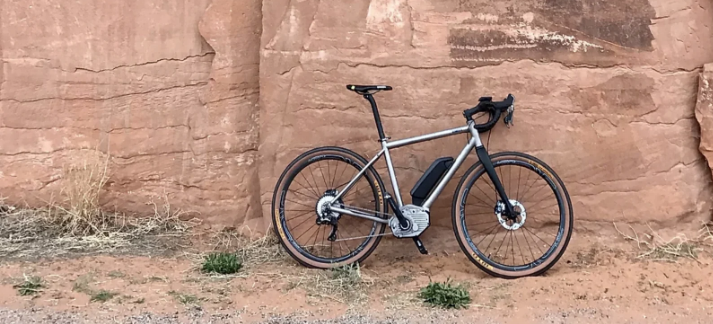
When GSD Global started to investigate the possibility of 3D printing their titanium components, they were thrilled to find that through developing the design of the motor nodes and adapting them to be additively manufactured, they could actually reduce their costs with up to 75%.
With almost ten years behind them in collaborating with Bosch e-bike systems, GSD Global’s main focus in design is centered around e-bikes. Noting that they still see a lack of e-bikes in venues like bike shows, the designers attribute that to difficulty in creating the necessary titanium parts.
In 3D printing the node, they found that they would enjoy some of the greatest benefits that the technology has to offer—from high-performance parts and speed in production to greater affordability; in fact, with Sandvik producing the part, they can now save up to 75 percent in costs.
“This is when we realized that we were on to something that wouldn’t just prove to be financially feasible – but enable substantial improvement in terms of quality and energy efficiency as well,” said Zach.
In perfecting their e-bike, GSD Global will now be able to sell it for less, along with promising lighter weight, greater energy efficiency, and longevity due to durable, high-performance parts.
“We really wanted to add the material advantages of titanium to our high-end electrical propulsion systems for e-bikes,” said Krapfl. “We’re so excited to share this with lots of brands, and to start adding more and more additive parts in the future.”
[Source / Images: Sandvik]
The post GSD Global Partners with Sandvik to 3D Print Critical Titanium Part for E-Bike appeared first on 3DPrint.com | The Voice of 3D Printing / Additive Manufacturing.
3D printing industry news sliced: Sintavia, Sandvik, Xaar, Amaero, 3Diligent, Shining 3D, DP Technology and more
Oil and Gas industry consortium completes two projects to accelerate adoption of AM
The State of 3D Printing in Industrial Goods, Part One
As we have explored some niche industrial sectors, such as agricultural and heavy equipment manufacturers, we’ve learned that, while most of the leading companies in the sector use 3D printing for prototyping and design purposes, they are only now beginning to dip their feet into making parts via additive manufacturing (AM). The same seems to be true of those corporations involved in producing industrial goods.
In this article, we’ll take a look at some of the largest players in the space and explore how they are using AM for industrial goods. Then, we’ll follow this story up with an article on the suppliers in the sector.
Before we get to that, it’ll be necessary to give a bit of definition to “industrial goods”. This blurry concept is a sort of catch-all for manufacturers that don’t fit into clear-cut categories such as aerospace, weapons, oil and gas, automotive, consumer goods, medical and dental and maritime. Broadly speaking, the industrial goods sector sells equipment and parts used to make other goods. Think drill bits, manufacturing equipment, and contract production.
The industrial goods sector may not be as far along in adopting AM for the manufacturing of end parts as the aerospace industry, but it seems to be more mature than the agricultural and heavy machinery fields (which are often lumped under industrial goods, as well).
Emerson Electric is a multinational, Fortune 500 company that makes parts and provides engineering services across a wide number of industries. The corporation is currently using AM primarily for prototyping and design iteration, which Emerson claims has reduced their product design and development time by 85 percent. The company also provides a service for original equipment manufacturers (OEM) to have 3D-printed microfluidic valve assemblies rapidly produced with stereolithography (SLA) for customers to perform form and fit testing.
However, in 2016, Emerson also launched a new additive manufacturing center in Singapore, through a partnership with the Singapore Economic Development Board and Nanyang Technological University, that aims to make AM a production-worthy technology for the company. The center will work on 3D printing valve and automation components with greater speed and flexibility than possible with traditional manufacturing techniques. This comes three years after launching an AM program in Iowa.
Xylem is a water technology provider for commercial and industrial customers, among other industries. In 2019, the company announced its end part made with 3D printing, the Flygt N3069 stainless steel submersible pump. To produce the Flygt N3069 pump customized for each client, Xylem’s facility in Emmaboda, Sweden, 3D prints one-off sand molds with which to cast the final steel part, which, according to the company, reduces lead times by up to 75 percent.
Parker Hannifin Corporation is a U.S. company focused on manufacturing motion and control technologies. In 2017, Parker opened an AM facility at Corporate Technology Ventures facility in Macedonia, Ohio to study how the technology can be used for design purposes.
KOMET GROUP, out of Germany, is a precision cutting tool supplier that began working with Renishaw in 2017 to 3D print Poly-Crystalline Diamond screw-in milling cutters that feature four more blades that previously possible, a greater axis angle and shortened grooves that increase the feed rate by 50 percent. The paths for coolant channels have also been optimized.
Alaska General Seafoods is using ExOne’s binder jetting process provided by 3DX Industries to 3D print metal replacement parts for its seafood canning line. Karry Lattig of Alaska General reported that the printed parts worked as well as traditionally made parts despite the harsh environment in which they operated under high use for two full seasons. And because they were 3D printed on-demand, the company did not have to shut down operations in order to remove and replace worn parts.
Seco Tools is a large Swedish manufacturer of metal cutting tools which has begun 3D printing end parts. Specifically, its Jetstream Integrated coolant clamps have been 3D printed so to include internal coolant channels optimized for turning applications. The clamp is attached to the cutting edge of a turning head, allowing coolant to flow through it and cool the edge. It is also easier to handle, making making it easier to apply and remove, thus reducing downtime.
The part was produced by Sandvik, Swedish machine tool manufacturer Sandvik. While the company could fit into the next part of our series on 3D printing suppliers, given its role as a 3D printing service bureau (and metal powder producer), it also uses AM to make its own parts. Its CoroMill 390 milling cutter was optimized with AM, resulting in an 80 percent reduction in weight and a 50 to 200 percent increase in productivity, as well as less part vibration.
In the next installment in our series, we’ll take a look at suppliers of 3D printing for the industrial sector, including service providers and 3D printer manufacturers.
The post The State of 3D Printing in Industrial Goods, Part One appeared first on 3DPrint.com | The Voice of 3D Printing / Additive Manufacturing.
Beam IT Commits to Buy 15 Metal 3D Printers from SLM Solutions
After Sandvik acquired a substantial stake in June 2019, Beam IT has made a massive purchase of metal 3D printers from SLM Solutions. Italy’s largest 3D printing service bureau has signed a letter of intent to buy 15 selective laser melting (SLM) machines over the next three years.
The exact systems Beam IT intends to buy fall across SLM’s entire product range, including the SLM280, SLM500 and SLM800. In particular, the company is investing in the multi-laser and closed-loop powder handling technology featured on the machines. This, the Beam IT team believes, results in higher productivity and a more reliable, safe and efficient method for 3D printing parts. The purchase is a part of Beam IT’s expansion of its manufacturing plant, which is more than twice as large as the previous space.
Mauro Antolotti, Chairman and Founder of Beam IT, said of the agreement, “Through the replacement of single laser products with SLM Solutions` multi-laser technology we are able to increase our productivity and provide competitive pricing to our customers. By partnering with SLM Solutions, we can meet our customer’s requirements to build high quality parts at increased productivity and expand our facilities.”
The 15 machines will augment Beam IT’s existing array of 20 metal powder bed fusion machines already installed. The company’s AS 9100 certifications for aerospace, and NADCAP approval, make it a substantial firm in the service bureau sector.
The purchase also signals Sandvik’s increased strength in the AM space, which already consists of metal powders manufacturing and engineering services. As a leading engineering multinational, the company has implemented 3D printing to improve both its own products and those of its customers. This includes the CoroMill 390 milling cutter, steel sliding cases for LKAB Wassara, Varel’s nozzles for hard-rock drilling, and a coolant clamp for Seco Tools.
All of this is a part of Sandvik’s larger strategy of maintaining growth and the top position in the world of the $17 billion metal cutting tools market, of which it represents roughly one fifth. In turn, Sandvik, Beam IT and SLM Solutions stand to become increasingly important players in the 3D printing industry. This will obviously be beneficial to SLM Solutions, in particular. Not just because of the revenue generated from the sale of each machine, but also due to the revamp in its image after failing to secure an acquisition by GE in 2016.
Based on the types of projects and deals that the company has been involved in over the past several years, it seems as though SLM Solutions has recovered from the snafu. In addition to the significant partnership with Beam IT, SLM has been working with Honeywell for metal 3D printing qualification, selling machines to Rolls Royce, and involved in the 3D printing of parts for Bugatti, among other things.
The post Beam IT Commits to Buy 15 Metal 3D Printers from SLM Solutions appeared first on 3DPrint.com | The Voice of 3D Printing / Additive Manufacturing.