Electric bikes are known to be pricey, but if you have ever investigated much about quality cycling equipment, that’s not a surprise—whether you are in the market for a conventional bicycle requiring only the energy of your pedaling legs to act as power, or a more complex battery-powered assist. And while there may be a small percentage of bicyclists out there who ride because they have no other choice, for many, cycling is a passion which offers a host of benefits, from improving cardiovascular health to decreasing stress—and cutting down on the environmental footprint.
Coupled with 3D printing, the potential advantages multiply for the bicycle industry—marked by numerous and impressive forays into designs that are stainless and sleek, prize-winning, and even, yes, compostable. Along with bikes and bike parts, we have also seen 3D-printed helmets for cyclists. In the latest modern bicycling news, however, Sandvik Additive Manufacturing has been able to 3D print a critical part for the GSD Global e-bike, in the form of a motor node—one of the most challenging parts to create for these upscale machines.
GSD Global, an engineering and design consultancy company, reached out for help in 3D printing the metal node for their artisan e-bikes.
“Handmade bikes are the type of product that goes straight to your heart – they are pieces of art to begin with. So, if we can provide these high-end bicycle makers with a material that can make their bikes last 10-20 years – that’s a game-changer to them,” says Zach Krapfl, heading up GSD Global.
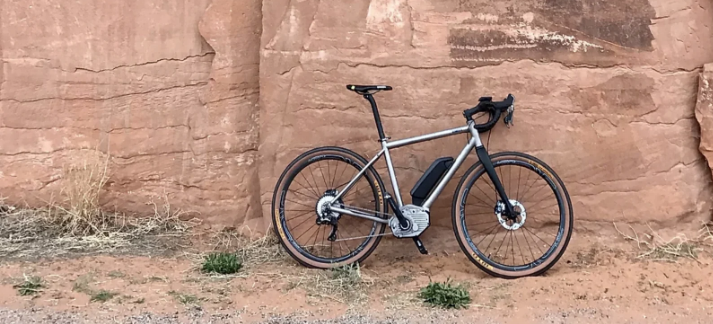
When GSD Global started to investigate the possibility of 3D printing their titanium components, they were thrilled to find that through developing the design of the motor nodes and adapting them to be additively manufactured, they could actually reduce their costs with up to 75%.
With almost ten years behind them in collaborating with Bosch e-bike systems, GSD Global’s main focus in design is centered around e-bikes. Noting that they still see a lack of e-bikes in venues like bike shows, the designers attribute that to difficulty in creating the necessary titanium parts.
In 3D printing the node, they found that they would enjoy some of the greatest benefits that the technology has to offer—from high-performance parts and speed in production to greater affordability; in fact, with Sandvik producing the part, they can now save up to 75 percent in costs.
“This is when we realized that we were on to something that wouldn’t just prove to be financially feasible – but enable substantial improvement in terms of quality and energy efficiency as well,” said Zach.
In perfecting their e-bike, GSD Global will now be able to sell it for less, along with promising lighter weight, greater energy efficiency, and longevity due to durable, high-performance parts.
“We really wanted to add the material advantages of titanium to our high-end electrical propulsion systems for e-bikes,” said Krapfl. “We’re so excited to share this with lots of brands, and to start adding more and more additive parts in the future.”
[Source / Images: Sandvik]
The post GSD Global Partners with Sandvik to 3D Print Critical Titanium Part for E-Bike appeared first on 3DPrint.com | The Voice of 3D Printing / Additive Manufacturing.