Researchers from Germany are exploring democratizing bioprinting with their findings outlined in ‘Nydus One Syringe Extruder (NOSE): A Prusa i3 3D printer conversion for bioprinting applications.’ Recognizing the promise of this new technology and all that surrounds it, the authors focus on the potential for eliminating animal testing in the pharmaceutical industry, along with the ability to offer patient-specific treatment in nearly every area of medicine. But, applications could extend far beyond these.
In this study, the research team studies the performance of a Prusa i3 converted with a Nydus One Syringe Extruder (NOSE), allowing for hydrogel extrusion and ‘tunable deposition precision’ with a syringe holder. Projects like these are possible because of open-source technology, and here, the team was able to alter their low-cost 3D printing hardware to experiment in bioprinting. The combination of NOSE and the Prusa i3 platform in an open source bioprinting package is a potentially powerful one that could democratize bioprinting worldwide. Building on CMU’s FRESH research that has already lead to tissues being made on low-cost printers this is really a potentially groundbreaking moment in bioprinting.
So far bioprinters have been niche and cost 100,000’s or tens of thousands. With FRESH CMU already has demonstrated for three years that low-cost bioprinting for $500 to a $1000 is possible. But, this GPL licensed research combined wit the popular Prusa i3 open source 3D printer could be the thing that makes bioprinting accessible. What this paper does is give you a step by step guide on how to bioprint using a modified Prusa printer and some extra parts. In one fell swoop, hundreds of thousands of Prusa operators could potentially now experiment with bioprinting.
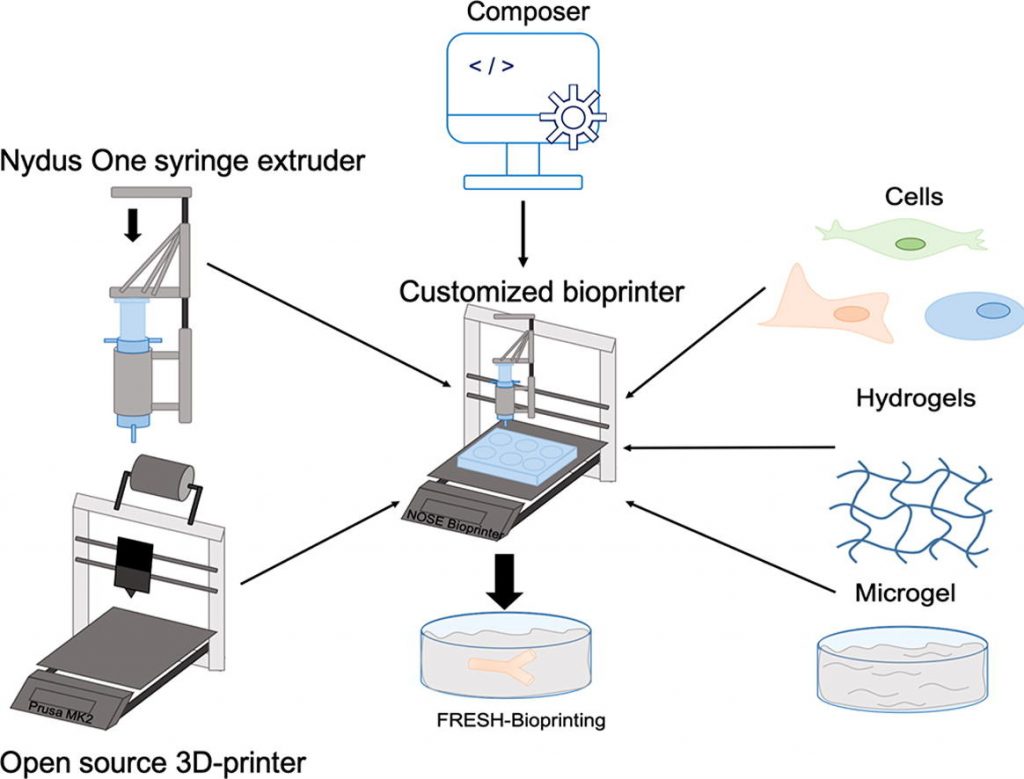
No matter what type of hardware, software, or materials are used though, challenges still abound in bioprinting as researchers must work hard to keep cells alive in the lab. Open sourcing allows for smaller labs to forge ahead in bioprinting also as they can bypass the cost of commercial hardware which could cost hundreds of thousands of dollars. Modifications to the Prusa i3 with the NOSE offer many benefits, to include:
- A RepRap basis and GPL license allowing modifications and opening the door to support in a large 3D printing community.
- Specialized P.I.N.D.A. calibration routine for user-friendliness, and ease in reproducing prints
- Open-source software
- Accessibility and affordability for users
- Validated conversion for use with cell lines, stem cells, and FRESH printing for complex structures
Once parameters are set, the researchers promise an algorithm delivering a ‘collision-free path.’ They must be set carefully and correctly, however, and the team suggests that users practice first by fabricating and experimenting with basic samples. If desired, the printer mainframe can also be replaced with a RebelliX frame.
The research paper also includes information regarding:
- Operation instructions
- One-time setup
- Software requirements and downloads
- Slic3r setup
- Bioprinting routine
- Ink preparation
- Support removal
A selection of the most commonly used bioprinting techniques: a) Inkjet bioprinting describes the deposition of biomaterials (and cells) in a low viscosity range by production and depositioning of drops in the 1-100 pL range. b) Extrusion Bioprinting: a continuous thread of biomaterial containing cells is extruded through a needle and deposited on a print surface. A broad range of viscosities is possible. c) Laser-induced forward transfer: the biomaterial is deposited on a gel ribbon. Laser impulses then initialize the release of small drops onto a receiver plate. The choice of the printing technique depends on the desired resolution, the type of biomaterials and the cell-type and -density.
Costs for converting the Prusa i3 into a comprehensive bioprinter are minimal, and the FRESH method means that users can print complex geometries, using concentrated hydrogels for bioprinting purposes. The researchers did note, however, that the NOSE system was lacking in some areas:
“A completely screw-based extruder assembly would enhance the modifiability for following iterations,” stated the researchers. “Rapid infill motions caused by the high center of mass might increase the material fatigue. One potential solution here could be the placement of the servo closer to the y-carriage. Extra mechanical-endstops would improve the user-friendliness, by automatizing the repositioning of the mechanical press. Additionally, thermal extrusion control or UV-emitting diodes could increase the cross-linking capabilities and thus the range of hydrogels in future.”
The NOSE bioprinting setup exhibited an 81 percent survival rate of HEK293 cells during experimentation and promising 85 percent rate for embryonic stem cells (mESC). Again, however, some major issues did arise as the FRESH microgel proved to be ‘non-ideal’ for cells exposed over 30 minutes.
The NOSE modification consists of four 3D-printed parts: (1) the mounting part of the y-carriage and adapter for the modular syringe holder (“main adapter”), (2) a syringe holder with a diameter suitable for common 10 mL disposable syringes (“syringe holder”), (3) part to mount a NEMA17 servo engine (“servo mounter”), (4) the press part to move the syringe-piston (“mechanical press”). All parts have been printed using 0,01 mm layer height using support structures. Any support structure leftovers or unfitting hinges were gently polished using fine sandpaper.
“Overall these findings open up further optimization of the embedded bioprinting method by creating a physiological environment,” concluded the researchers. “Our bioprinting approach is protected with the GPLv3 license, hence we invite you to reproduce our data and modify our approach.”
Bioprinting may be much more common in research labs around the world today, from microfluidic platforms to scaffolds for bone regeneration and more, but for most scientists, the ultimate goal is that of 3D printing human organs. Impressive strides have already been made, however, with cellularized hearts, human brain tissue, animal brains, and many other spectacular models.
Given that the Prusa i3 is an inexpensive 3D printer capable of high-quality 3D prints this development could potentially democratize bioprinting. If the NOSE nozzle works well then this could make the i3 an affordable bioprinting platform, for some bioprinting applications, for use in the lab and classroom. The Prusa i3 is the predominant FDM system architecture and hundreds of thousands of Prusa and Prusa clones are scattered across the earth. Hundreds of vendors sell and manufacture them. With the NOSE nozzle and the i3 bioprinting could now become affordable for many people worldwide. Sometimes a moment changes everything, sometimes that moment is this one.
A selection of the most commonly used bioprinting techniques: a) Inkjet bioprinting describes the deposition of biomaterials (and cells) in a low viscosity range by production and depositioning of drops in the 1-100 pL range. b) Extrusion Bioprinting: a continuous thread of biomaterial containing cells is extruded through a needle and deposited on a print surface. A broad range of viscosities is possible. c) Laser-induced forward transfer: the biomaterial is deposited on a gel ribbon. Laser impulses then initialize the release of small drops onto a receiver plate. The choice of the printing technique depends on the desired resolution, the type of biomaterials and the cell-type and -density.
[Source / Images: ‘Nydus One Syringe Extruder (NOSE): A Prusa i3 3D printer conversion for bioprinting applications’]